Специфика изготвления и контроля приспосблений. Исполнитель
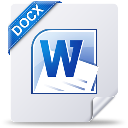
- Скачано: 21
- Размер: 107 Kb
Специфика изготвления и контроля приспосблений.
План
- Спецификаизготовления приспособлений.
- Приемка и периодический контроль приспособлений в процессе их эксплуатации.
{spoiler=Подробнее}
Приспособления изготовляют различными методами. Универсальные приспособления выпускаются в значительном количестве для укомплектования новых станков и действующего станочного оборудования; значительная часть их стандартизована (трех- и четырехкулачковые патроны, плиты и другие устройства). Изготовление этих приспособлений сосредоточено на специализированных заводах или в специальных цехах станко-инструментальних заводов и осуществляется по принципам поточно -массового или крупносерийного производства. Аналогичным образом изготовляют нормализованные приспособления, а также узлы и отдельные детали к ним. Специальные приспособлении изготовляют индивидуально или малыми партиями в инструментальных цехах машиностроительных заводов (для собственных нужд) и станко-строительными, заводами (для оснащения выпускаемых специальных станков). При широком использовании стандартных элементов их изготовление может быть организовано по принципу серийного производства на специализированных заводах. При широкой номенклатуре изделий и большом объеме выпуска эти заводы могут обслуживать группы прикрепленных предприятий.
Специализация производства и возможность эффективного использования специального оборудования обеспечивают изготовление приспособлений в сжатые сроки и меньшей себестоимости.
Заготовки дли деталей специальных приспособлений выполняют методами единичного производства (литьем, ковкой, мелкие детали обрабатывают из сортового материала). Заготовки средних и крупных размеров сложной конфигурации (корпусы приспособлений, стойки, кронштейны и т.п.) часто изготовляют сварными. Литые заготовки ответственных деталей (корпусы приспособлений) перед окончательной механической обработкой целесообразно подвергать обдирке и естественному или искусственному старению для снятия остаточных напряжений. Сварные заготовки получают из предварительно заготовленных элементов (плит, планок, угольников, косынок, шайб, втулок). Их очищают от ржавчины и масла, собирают на струбцинах, выверяют правильность взаимного положения и «прихватывают» в отдельных точках.
При обработке (или контроле) наклонных площадок, положение которых на детали задано определенными углами, применяют синусные плиты, установленные на три сферические опоры. Зная расстояние между опорами, можно рассчитать высоту подставок, чтобы обрабатываемая (контролируемая) деталь занимала то или иное наклонное положение. Применяют также синусные плиты в комбинации с делительным устройством. На них можно размечать и шлифовать детали, используя съемные магнитные плиты. Плиту устанавливают под требуемым углом к горизонтальной плоскости с помощью мерных плиток с высокой точностью.
Для достижения заданной точности при изготовлении приспособлений применяют спаренную обработку (совместное растачивание сопряженных деталей, развертывание, шлифование), а также перенос размеров с одной детали на другую. Механическую обработку ведут на универсальных станках, используя инструменты и приспособления общего назначения.
Большие возможности в части сокращения сроков и себестоимости изготовления приспособлений для серийного производства дает применение пластмасс. В станочных приспособлениях обычно используют эпоксидные компаунды как наиболее прочные пластические массы. Литейная композиция из них содержит 100 массовых долей эпоксидной смолы ЭД-5 или ЭД-6, 200 м. д. наполнителя (железный порошок, железный сурик, маршаллит, цемент и др.), 15-20 м. д. пластификатора (дибутилфталат) и 8-9 м. д. отвердителя (полиэтилепполиамин). При изготовлении основных и вспомогательных деталей специальных приспособлений эту композицию заливают в разовые формы. После отверждения компаунд имеет следующие механические свойства: твердость НВ 20, предел прочности при растяжении 60 МПа, предел прочности при сжатии до 130 МПа, удельную ударную вязкость до 120 МПа. Плотность компаунда в зависимости от наполнителя 1,2-2,0; усадка компаунда при отверждении около 0,1 %; его износостойкость близка к износостойкости алюминиевых сплавов. Прочность компаунда можно повысить введением стальной арматуры.
Разовые формы для отливок можно изготовлять из гипса (по выплавляемой восковой модели отливаемой детали), картона (путем вычерчивания, вырезки и последующего склеивания развертки для простых конфигураций деталей), а также из пластилина. Изготовление таких форм не требует много времени (около 1-1,5 ч).
Рис. 65. Приспособление с использованием пластмассы:
а— с ложементом; б — пример отливки кондукторной плиты из пластмассы
Из эпоксидного компаунда можно отливать ложементы (негативные отпечатки) для установки обрабатываемых заготовок по внешней поверхности. Основанием ложемента служит сварная коробка (кассета) 1, заливаемая компаундом 2 (рис. 65, а). На ее верхней плоскости литьем по эталонной детали получается негативный отпечаток 3 для обрабатываемой заготовки 4.
На рис. 65, б показан способ изготовления кондукторных плит с точно координированными отверстиями. Кондукторные втулки 5 устанавливают на основание 6 по мерным плиткам. Фиксация их производится струбцинами или клеем. Затем устанавливают рамку 7, определяющую внешние контуры кондукторной плиты, и пространство между втулками и рамкой заливают компаундом 2. При малой усадке компаунда обеспечивается точное межосевое расстояние.
Сборку специальных приспособлений производят с выполнением ряда пригоночных работ и обработкой «по месту». Для получения сопряжений повышенной точности применяют припиливание, пришабривание и притирку. Сборку следует расчленять на узловую и общую, что сокращает длительность цикла изготовления приспособлений.
В процессе сборки производят регулировку и точную выверку взаимного положения деталей и узлов приспособления. Найденное положение фиксируют контрольными штифтами. Для неподвижных соединений деталей и приспособлений, работающих на сжатие и сдвиг, можно применять склеивание. При использовании эпоксидных клеев получают прочность на сдвиг 30-35 МПа. Для точной фиксации сопряженных деталей необходимо применять контрольные штифты. Разборка клеевых соединений производится нагревом их до температуры 150 °С.
Для повышения точности сборки часто практикуют совместную обработку нескольких деталей после их сборки. Так, для получения строгой соосности отверстий в нескольких деталях их окончательное растачивание ведут с одной установки. Рабочие поверхности установочных элементов часто шлифуют за один проход после окончательной фиксации на корпусе приспособления.
При сборке приспособления обращается внимание на качественную пригонку элементов фиксации корпуса приспособления со станком.
Вновь изготовленное приспособление тщательно проверяют перед сдачей в эксплуатацию. Проверка предусматривает: внешний осмотр, контроль комплектности в соответствии с чертежом, правильность изготовления приспособления по основным элементам и сопряжениям (плавность и легкость перемещений, плотность посадок), опробование приспособления в работе с выполнением необходимых регулировок и доводочных работ (проверка действия установочных и зажимных механизмов, поворотных устройств, фиксаторов, выталкивателей) и контроль приспособления на точность выполняемой им работы.
Контроль точности изготовления станочных и сборочных приспособлений осуществляют тремя способами: непосредственным измерением тех размеров приспособления, от которых зависит точность его работы; пробной обработкой нескольких заготовок (сборкой нескольких узлов) с последующим контролем их качества универсальными измерительными средствами, калибрами или контрольными приспособлениями; использованием для контроля эталонных деталей.
Первый способ, осуществляемый с помощью универсальных измерительных инструментов, трудоемок и выполняется высококвалифицированными контролерами. Второй способ является чисто функциональным, он удобен для производственных условий, но связан с потерей пробных заготовок. Третий способ основан на использовании эталонной детали, с помощью которой проверяют положение установочных элементов относительно направляющих элементов.
На рис. 66 показана схема проверки размера Н у расточного приспособления. Вместо заготовки в приспособление устанавливают эталонную деталь 1, у которой этот размер точно выдержан. Через направляющие (кондукторные) втулки вводят эталонную скалку 2. Если в изготовленном приспособлении расстояние от плоскости установочных элементов 3 до оси кондукторных втулок не соответствует размеру Н, то скалка не пройдет через эталон.
Приспособления периодически осматривают и проверяют. В серийном производстве приспособления периодически снимают со станков и сдают на склад или хранят у рабочего места. В это время их осматривают и проверяют точность размеров. В массовом производстве приспособления проверяют на станке в перерывах между сменами. Здесь наиболее удобен контроль по эталонам. На крупных заводах периодическую проверку приспособлений осуществляют работники ОТК. Результаты проверки фиксируются в паспорте приспособления. На основе периодических осмотров и проверок выявляется необходимость профилактического и текущего ремонтов, а также замены изношенных элементов и узлов приспособления. В паспорт приспособления вносят следующие данные: шифр приспособления; наименование и номер операции; номер чертежа приспособления; инвентарный номер станка, на котором используется приспособление; дата проверки, заключение и подписи приемщиков; время работы приспособления; число обработанных деталей; замечания рабочих и мастера; дата и причина ремонт»; дата выхода приспособления из строя и причина. Данные паспорта учитываются при конструировании аналогичных приспособлений. Новое контрольное приспособление проходит наладку, проверку перед сдачей в эксплуатацию и периодические проверки на рабочих и контрольных постах. При приемке контрольные приспособления подвергают полному метрологическому исследованию, сопоставляя результаты измерений деталей в приспособлении с результатами измерения универсальными инструментами. Погрешности измерения анализируют и определяют стабильность работы приспособления. На принятое приспособление составляют аттестат, инструкцию для пользования и карту периодической проверки.
Периодическая проверка контрольных приспособлений в процессе их эксплуатации производится ОТК. Проверку осуществляют инспектора центральной измерительной лаборатории (ЦИЛ) по специальной инструкции, имея чертеж приспособления и карту периодической проверки. При обнаружении дефектов и износа приспособления направляют в ремонт. После ремонта приспособления проходят контрольную проверку ОТК. Измерения при проверке приспособления выполняют универсальными мерителями, а также с помощью эталонных деталей. Последние используют для периодической настройки контрольных приспособлений, снабженных отсчетными измерительными средствами (индикаторами, миниметрами и т, п.). На эталонные детали составляют паспорта, а сами они проходят периодическую проверку в ЦИЛ.
Рис. 66. Проверка расточного приспособления по эталонной детали.
Вопросы для самоповторения
- Методы изготовления приспособлений.
- Как осуществляется приемка приспособлений в эксплуатацию.
- Как осуществляется процесс периодического контроля приспособлений?
- Куда отправляют приспособления при обнаружении дефектов и износа?
{/spoilers}