Технологические процессы в производстве Исполнитель
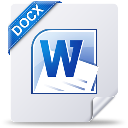
- Скачано: 37
- Размер: 175.5 Kb
Технологические процессы в производстве
План:
1.Понятия кибернетики и телемеханика.
2.Управления технологическими процессами.
3.Сведения об автоматизация автоматических линиях и промышленных роботов.
{spoiler=Подробнее}
Роботы и робототехника прошли короткий, но стремительный путь развития. Возникновение современных роботов следует отнести к 1959 г., когда в США были созданы первые промышленные
манипуляторы с программным управлением. В 1962 г. Появились первые американские промышленные роботы «Юнимейт» и «Версатран», созданные соответственно фирмами «Юнимейшн» и «Американ Машин энд Фаундри» и предназначенные для обслуживания технологических процессов: литья под давлением, ковки, механической обработки, точечной сварки, нанесения покрытий. Применение их в автомобильной и металлургической промышленности оказалось экономически выгодно: затраты на приобретение роботов «Юнимейт» или «Версатран» (25...35 тыс. долл. за 1 шт.) окупались за 1,5...2,5 года. Как было сказано в одной из статей, опубликованной в журнале «Машинери мэгэзин», в американской металлообрабатываюш1ей промышленности появился новый тип производственного рабочего, который не состоит в профсоюзе, не пьет кофе в обеденный перерыв, работает 24 ч в сутки и не интересуется пособиями или пенсионной оплатой. Этот рабочий осваивает новую работу за несколько минут и всегда выполняет ее хорошо, никогда не жалуется на жару, пыль и запахи и не получает увечий. Он — промышленный робот. Роботы можно классифицировать по самым различным признакам. Наиболее общими и содержательными являются классификации по назначению, решаемому классу задач и особенностям управления.
Поскольку с развитием робототехники неизбежно формирование новых поколений роботов и внедрение их в новые области и сферы, классификация по назначению и решаемому классу задач не является завершенной и, в известной мере, характеризует путь развития роботов, а поэтому может быть названа эволюционной. По назначению и решаемому классу задач роботы всех поколений могут быть разделены на две большие группы: промышленные и исследовательские (рис. 11.1). Промышленные роботы (ПР) — это роботы, предназначенные для выполнения тяжелой, монотонной, вредной и опасной для здоровья физической работы, а также для выполнения отдельных видов трудоемкой, напряженной и утомительной умственной работы (проектирование, информационное обеспечение, управление). Соответственно конкретным областям применения имеется ряд разновидностей промышленных роботов. Промышленные роботы, получившие наибольшее развитие в настоящее время, предназначены для автоматизации основных и вспомогательных операций в различных отраслях промышленности: в машиностроении и приборостроении, в горнодобывающей,
нефтехимической, металлургической, атомной и др. Промышленные роботы, в свою очередь, подразделяются на три группы по производственно-технологическим признакам: производственные, или технологические (ППР), для основных операций технологических процессов; подъемно-транспортные, или вспомогательные (ПТПР), выполняющие действия типа взять —перенести —положить; универсальные (УПР) для различных операций — основных и вспомогательных. По специализации промышленные роботы подразделяются на специальные, выполняющие строго определенные технологические операции или обслуживающие конкретные модели технологического оборудования; специализированные, или целевые, предназначенные для выполнения технологических операций одного вида (сварки, сборки, окраски и т.п.) или обслуживания определенной группы моделей технологического оборудования, объединенных общностью манипуляционных действий; универсальные, или многоцелевые, ориентированные на выполнение как основных, так и вспомогательных технологических операций различных видов и с различными группами моделей технологического оборудования.
2.Составные части и конструкции промышленных роботов .
Промышленный робот состоит из исполнительного устройства (собственно манипулятора) и устройства управления. Манипулятор ПР предназначен для выполнения всех его двигательных функций и представляет собой многозвенный еханизм с разомкнутой кинематической цепью, оснащенный приводами и рабочим органом, а также, в общем случае, устройством передвижения. Манипулятор состоит из опорных (несущих) конструкций, манипуляционной системы, рабочих органов, привода и устройства передвижения. Устройство управления ПР необходимо для формирования и выдачи управляющих воздействий манипулятору в соответствии с управляющей программой. Оно состоит из собственно системы управления, информационно-измерительной системы с устройствами обратной связи и системы связи. Структурная схема промышленного робота представлена на рис. 11.2.
Опорные конструкции служат для размещения всех устройств и агрегатов ПР, а также для обеспечения необходимой прочности и жесткости манипулятора. Опорные конструкции выполняются в виде оснований, корпусов, стоек, рам тележек, порталов и т.п.
Манипуляционная система предназначена для переноса и ориентации рабочего органа или объекта манипулирования в заданной точке рабочей зоны и представляет собой многозвенный пространственный механизм с разомкнутой кинематической цепью.
Рабочий орган манипулятора ПР, необходимый для непосредственного воздействия на объект манипулирования при выполнении технологических операций или вспомогательных переходов, представляет собой захватное устройство или рабочий инструмент. Привод предназначен для преобразования подводимой энергии в механическое движение исполнительных звеньев манипулятора в соответствии с командными сигналами, поступающими от системы управления, и в общем виде содержит энергоустановку, двигатели и передаточные механизмы. Устройство передвижения служит для перемещения манипулятора или ПР в целом в необходимое место рабочего пространства и состоит из ходовой части и приводных устройств.
Система управления необходима для непосредственного формирования и выдачи управляющих сигналов и состоит из пульта управления, запоминающего устройства, вычислительного устройства, блоков управления приводами манипулятора и технологическим оборудованием. Информационно-измерительная система, предназначенная для сбора и первичной обработки информации для системы управления о состоянии элементов и механизмов ПР и внешней среды, входит в состав устройства управления ПР и включает всебя устройство обратной связи, устройство сравнения сигналов и датчики обратной связи. Систему связи используют для обеспечения обмена информацией между ПР и оператором или другими роботами и технологическими устройствами с целью формулировки заданий, контроля за функционированием систем ПР и технологического оборудования, диагностики неисправностей, регламентной проверки и т.п.
На рис. 11.3 представлена одна из конструкций промышленного робота.
3. Технические характеристики промышленных роботов
Технические характеристики современных ПР можно подразделить на основные и дополнительные. К основным техническим характеристикам ПР относятся номинальная грузоподъемность; число степеней подвижности; величины и скорости перемещения по степеням подвижности; рабочая зона, рабочее пространство и зона обслуживания ПР; погрешность позиционирования или отработки траектории. Номинальная грузоподъемность ПР — наибольшее значение массы предметов производства или технологической оснастки, при которой гарантируются их захватывание, удержание и обеспечение установленных значений эксплуатационных характеристик. Для многорукого ПР номинальную грузоподъемность определяют как сумму грузоподъемностей всех его рук. Для некоторых типов ПР важным показателем является усилие (или крутящий момент), развиваемое исполнительным устройством. По величине номинальной грузоподъемности ПР подразделяются на сверхлегкие (до 1 кг); легкие (свыше 1 до 10 кг); средние (свыше 10 до 200 кг); тяжелые (свыше 200 до 1000 кг); сверхтяжелые (свыше 1000 кг). В настоящее время выпускают до 65 % моделей ПР легкого и среднего типов с грузоподъемностью от 5 до 80 кг. Число степеней подвижности ПР определяют как сумму возможных координатных движений его рабочего органа или
объекта манипулирования относительно опорной системы. Для некоторых типов ПР дополнительно учитывают число степеней подвижности захватного устройства, равное числу степеней свободы всех его звеньев относительно узла крепления к руке робота. Среди степеней подвижности отдельного манипулятора различают переносные и ориентирующие. Переносные степени подвижности используются для перемещения рабочего органа ПР, ориентирующие — для его ориентации в рабочей зоне. Для перемещения объекта манипулирования в заданное место рабочей зоны без его ориентации достаточно трех переносных степеней подвижности, для полной ориентации — трех ориентирующих. Для переноса и полной пространственной ориентации необходимо шесть степеней подвижности; дальнейшее увеличение числа степеней подвижности повышает маневренность манипуляционной системы робота, улучшает динамику, однако усложняет конструкцию и программирование, снижает точность позиционирования и увеличивает стоимость ПР. Поэтому предпочитают ограничиваться четырьмя-пятью степенями подвижности; шесть и более применяют лишь в наиболее сложных технологических процессах.
По подвижности ПР подразделяются на три группы: малую (до трех степеней подвижности), среднюю (четыре —шесть) и высокую (более шести). Число степеней подвижности ПР в значительной мере определяет его универсальность. Современные ПР имеют обычно от двух до семи степеней подвижности: самые простые — одну-две; наиболее сложные — семь, иногда и более. В структуре современного мирового парка ПР преобладают конструкции с четырьмя и пятью степенями подвижности (63 %).
Учитывая все большее применение подвижных роботов, наряду со степенями подвижности манипуляционной системы робота следует рассматривать также степени подвижности устройств его передвижения, так называемые координатные. Величины и скорости перемеидения рабочс о органа по каждой степени подвижности характеризуют геометрию рабочего пространства ПР, а также особенности движения и ориентации переносимого предмета и определяются механикой манипулятора ПР и возможностями привода.
Величины перемегцений по линейным координатам задаются в метрах, по угловым — в градусах или радианах; скорости выражаются в метрах в секунду для линейных и градусах радианах)
в секунду для угловых координат. По величине линейного перемещения или хода рабочего органа различают ПР с малым (до 300 мм), средним (от 300 до 1000 мм) и большим (более 1000 мм) ходом. Скорости перемещений звеньев манипулятора характеризуют важное качество ПР — быстродействие, от которого зависит время обслуживания технологического оборудования. Обычно
скорости линейных перемещений рабочих органов манипуляторов не превышают 1 м/с, хотя имеются отдельные роботы со скоростями до 2 м/с и более. Угловые скорости движений рабочих органов находятся преимущественно в диапазоне 15...360 Vc (0,25...6,3 рад/с).
4. Манипуляционная система промышленных роботов
Манипуляционная система (МС) промышленного робота является составной частью манипулятора ПР, обеспечивающей перенос и ориентацию рабочего органа или объекта манипулированияв заданной точке пространства и определяющей форму и объем рабочей зоны ПР, а также характер движений рабочего органа. В совокупности с опорной конструкцией, приводом, передаточными механизмами и рабочим органом манипуляционная система образует манипулятор ПР; при этом часть элементов опорной конструкции, привода и передаточных механизмов может непосредственно входить в состав манипуляционной системы в качестве ее звеньев, что обусловливает применения в робототехнике общего понятия «манипулятор», как в отношении собственно манипулятора ПР, так и его манипуляционной системы.
На рис. 11.4 представлен один из типов манипулятора. Звенья манипуляционной системы обозначены цифрами 1, 2, ..., 7, характер и возможные направления движения звеньев — стрелками I, И, ..., VI. Манипулятор содержит неподвижное звено 1 в виде основания или корпуса ПР, на котором установлено вращающееся вокруг вертикальной оси (в направлении стрелки I) звено 2 — колонна манипулятора. Относительно колонны вертикально (И) движется звено 3 — каретка, в направляющих которой перемещается в радиальном направлении (HI) звено 4 — рука манипулятора. К руке, в свою очередь, присоединяется звено 5, вращающееся (IV) относительно ее продольной оси, и далее звено б, связанное шарнирно со звеном 5 и вращающееся в направлении стрелки V В совокупности звенья 5 и 6 по аналогии с рукой человека могут быть названы кистью. Звено 7 представляет собой рабочий
орган, в данном случае —механический схват с захватными элементами (губками), которые могут совершать движения (VI), за счет чего обеспечивает-
Рис. 11.4. Манипулятор ПР:
1 — неподвижное звено; 2 — поворотная колонна; 3 — каретка манипулятора; 4 — рука манипулятора; 5, 6 — звенья, аналогичные руке человека; 7 — губки; 1...VI — направления движения звеньев.
Кинематическая схема робота М20П.40.01 представлена на рис. 11.6 (t — числа зубьев шестерен и приводных шкивов, шаги винтов), а координаты перемещения робота показаны на рис. 11.7. Основание робота 1 (рис. 11.7) представляет собой жесткую отливку. Вал, служащий опорой для привода перемещений по оси Z, смонтирован в шариковом сдвоенном радиально-упорном подшипнике и шариковом радиальном подшипнике. На основании робота установлены червячный редуктор с передаточным числом 38 и электродвигатель ростоянного тока со встроенным датчиком обратной связи. Червячный редуктор и электродвигатель соединены между собой зубчатой муфтой. Выбор зазора в зубчатом зацеплении производится горизонтальным перемещением червячного редуктора.
Привод вертикального перемещения 3 включает в себя электродвигатель постоянного тока со встроенным датчиком обратной связи, шариковую передачу винт—гайка качения. Электродвигатель и винт соединены между собой зубчатой муфтой. Для исключения падения механизма выдвижения руки при отключении двигателя на верхнем конце винта установлен нормально замкнутый электромагнитный тормоз. Привод горизонтального перемещения 2 состоит из электродвигателя постоянного тока со встроенными датчиками обратной связи, шариковой передачи винт —гайка качения. Вращение от электродвигателя передается на винт плоскозубчатым ремнем с передаточным отношением 1:1. Приводом перемещений 5 по координате а служит неполно- поворотный пневматический двигатель с двухпозиционным управлением. Специальные стопоры предназначены для фиксации поворота на 90 и 180°. Привод перемещений 4 по координате О имеет реверсивный пневмодвигатель, волновой редуктор с передаточным отношением 1:159. Вращение от пневматического двигателя передается волновому редуктору через плоскозубчатый ремень.
Для контроля положения используются бесконтактные датчики, импульсы от которых поступают в устройство управления. Конечные выключатели служат для ограничения перемещения по координате а в диапазоне 90... 180°.
{/spoilers}