Определение погрешности базирование на базовой плоскости. Исполнитель
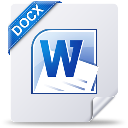
- Скачано: 0
- Размер: 720 Kb
Определение погрешности базирование на базовой плоскости.
План:
1.Установочные элементы и погрешность установки приспособления спутников.
2. Закрепление заготовок на приспособлениях спутниках.
3. Обработка координированных отверстий в автоматических линиях
{spoiler=Подробнее}
Приспособления являются важным элементом технологической системы, от них во многом зависят точность, производительность и себестоимость механической обработки, сборки и технического контроля изделий. Точность обработки (сборки), в свою очередь, зависит от точности установки в приспособление заготовки (детали, узла).
ПРИНЦИПЫ УСТАНОВКИ ЗАГОТОВОК В ПРИСПОСОБЛЕНИЯХ
Требуемая точность обработки обеспечивается определенным положением заготовки относительно режущего инструмента. Положение заготовки при обработке, как и любого твердого тела в пространстве, характеризуется шестью степенями свободы, определяющими возможность перемещения и поворота заготовки относительно трех координатных осей. При полном ориентировании заготовка лишается всех степеней свободы; при неполном — числа степеней свободы меньше шести.
В единичном и мелкосерийном производстве применяют установку заготовки с выверкой по рискам разметки, по обработанным или необработанным поверхностям, в массовом и крупносерийном производстве — установку с доведением базовых поверхностей заготовки до соприкосновения с установочными элементами (опорами) специальных приспособлений.
В зависимости от условий обработки осуществляют полную или частичную ориентацию заготовки в пространстве относительно режущего инструмента. В первом случае заготовке придают точное положение в приспособлении, во втором – точная установка в определенных направлениях не требуется, допускается произвольное положение (поворот) заготовки относительно какой – либо координатной оси (например, установка кольца в кулачки патрона при токарной обработке).
Установку заготовок выполняют, осуществляя плотный контакт базовых поверхностей с установочными элементами приспособления, жестко закрепленными в его корпусе. Это обеспечивается приложением к заготовке соответствующих сил закрепления. Для полной ориентации заготовки число и расположение опор должно быть таким, чтобы при соблюдении условия неотрывности баз от опор (т. е. при сохранении плотного и неподвижного контакта между ними) заготовка не могла сдвигаться и поворачиваться относительно координатных осей. При выполнении условия неотрывности заготовка лишается всех степеней свободы.
Число опор (точек), на которые устанавливают заготовку, не должно быть больше шести (правило шести точек). Для обеспечения устойчивого положения заготовки в приспособлении расстояние между опорами следует выбирать возможно большим; при установке заготовки на опоры не должен возникать опрокидывающий момент. С увеличением расстояния между опорами уменьшается влияние погрешностей формы базовых поверхностей на положение заготовки в приспособлении.
На рис. 2 показаны примеры установки заготовок с их полной и неполной ориентацией в пространстве. Схема установки прямоугольной заготовки с тремя взаимно перпендикулярными базовыми плоскостями для выдерживания размеров h, l и b при обработке прямоугольного паза показана на рис. 2, а. Опоры (точки) расположены на трех координатных плоскостях; стрелками показаны силы Q1, Q2, Q3, прижимающие заготовку к опорам. Закрепление заготовки осуществляют одной силой, например Q1, вызывающей возникновение силы трения между нижней базой и опорами, что препятствует смещению заготовки в остальных направлениях. Изменяя направление и точку приложения силы Q1, можно прижать заготовку ко всем опорам одновременно. При соблюдении условия неотрывности заготовки от всех шести опор (они показаны жирными точками) она не может быть сдвинута вдоль координатных осей и повернута вокруг них, т. е. лишается всех шести степеней свободы. На рис. 2, б показана практическая реализация предыдущей схемы. Опоры имеют ограниченную поверхность контакта и жестко закреплены в корпусе приспособления. После закрепления заготовки образуется замкнутся система заготовка – опоры – корпус – приспособления – зажимное устройство. Сила Q воспринимается элементами этой системы.
Рис. 2. Примеры установки заготовок с полной и неполной ориентацией.
На рис. 2, в приведена схема установки с базированием на плоской и криволинейной поверхности; при выполнении условия неотрывности заготовка и здесь лишается всех степеней свободы. На рис. 2, г дан пример частичной (неполной) ориентации заготовки. Плоским торцом она опирается на три точки, а цилиндрической поверхностью соприкасается с двумя остальными. Поскольку площадку (показана жирной линией) можно выполнить в произвольном месте, то для установки заготовки достаточно пяти опор. На рис. 2, д показана схема установки сферической заготовки для сверления в ней сквозного отверстия. Для данных условий (сверление отверстия в произвольном месте) необходимой достаточно трех опор, к которым заготовка прижимается планкой 1.
При обработке недостаточно жестких заготовок возникает необходимость увеличения числа опорных точек сверх шести. На рис. 2, е показана установка прямоугольной заготовки с длинным кронштейном, у которого обрабатываются торцы бобышки. Помимо основных шести опор, на которые ставят заготовку базовыми плоскостями, применена дополнительная индивидуально подводимая опора 1; к ней заготовка прижимается силой Q’. Это существенно повышает жесткость технологической системы, позволяя использовать более производительные, режимы резания.
Основные опоры жестко связаны с корпусом приспособления. Несмотря на наличие погрешностей формы и размеров базовых поверхностей заготовок, они всегда имеют контакт с опорами в шести точках в одних и тех же местах, поэтому установка всей партии заготовок получается одинаково устойчивой. Если, например, нижняя базовая плоскость в заготовках (см. рис. 2, е) имеет погрешность формы в виде выпуклости, то ее контакт с опорами приспособления у всех заготовок происходит в определенных местах.
Дополнительные опоры выполняют только регулируемыми или самоустанавливающимися. При установке заготовки опоры индивидуально подводятся (самоустанавливаются) к поверхности заготовки, а затем стопорятся, превращаясь на время выполнения данной операции в жесткие опоры. Число дополнительных опор не ограничено, однако для упрощения конструкции приспособления это число следует брать минимальным.
Точечные опоры приспособлений конструктивно оформляют в виде установочных элементов с малой поверхностью контакта. К ним относятся постоянные опоры, призмы для установки цилиндрических заготовок и другие детали. Они обеспечивают достаточную устойчивость заготовок независимо от погрешностей их размеров и формы. К недостаткам установки на точечные опоры относятся возможность повреждения базовых поверхностей заготовок при большой силе закрепления и смещение (осадка) заготовок в результате контактных деформаций в местах соприкосновения опор с базами. При малой шероховатости поверхности баз несущую поверхность опор увеличивают, и малые погрешности формы баз не оказывают заметного влияния на устойчивость системы установки. При установке на плоские базы используют опорные пластины. Чем ниже точность и больше 'шероховатость базовых поверхностей заготовок, тем в большей степени локализуют места их контакта с опорами приспособления. Возможна установка заготовок одной базой на опоры с большой поверхностью контакта, а остальными базами — на точечные опоры.
Из изложенного следует, что правило шести точек наиболее полно отвечает установке заготовок на точечные опоры при их полной ориентации в пространстве.
Кроме установки заготовок с полным прижатием их базовых поверхностей к опорам приспособления применяют установку по охватывающим или охватываемым базовым поверхностям. При этом заготовку надевают на установочный элемент или вставляют в него с некоторым гарантированным зазором. Пример установки по внешнему контуру прямоугольной заготовки 1 показан на рис. 3, а. Заготовка лишена всех степеней свободы, не считая малых сдвигов в пределах зазоров D для вхождения в контурную полость приспособления 2. Установка вала в центрах на конические поверхности центровых гнезд является примером оставления одной степени свободы — возможности установки вала в любом месте по углу его поворота. На рис 3, б показана схема комбинированной установки. Заготовку а насаживают базовым отверстием с зазором на жесткий палец б и плотно прижимают торцом к его борту. Для лишения заготовки всех степеней свободы применяют и другие комбинированные способы, например установку на два отверстия с параллельными осями и перпендикулярную им плоскость.
Для схем установки по охватывающим или охватываемым поверхностям с полной ориентацией заготовки в пространстве также применимо правило шести точек. Для схемы установки, показанной на рис. 3, б, эти точки определяются следующим образом. Поверхность базового отверстия может быть представлена четырьмя точками, две из которых (1 и 2) лежат на левой верхней образующей, а две (3 и 4) — на правой. Точка 7 (палец имеет вырезы, уменьшающие поверхность сопряжения) не является установочной, она ограничивает перемещение заготовки пределами посадочного зазора. Точка 5 ориентирует заготовку в осевом направлении, а точка 6 (конец рычага) определяет ее угловое положение. Правило шести точек наглядно прослеживается при использовании опор с ограниченной поверхностью контакта.
Рис. 3. Схемы установок заготовок.
а) по внешнему контуру; б) комбинированный
Для устранения влияния зазора на положение заготовки в приспособлении применяют разжимные или самоцентрирующие установочные (установочно-зажимные) устройства. К ним относятся самоцентрирующие патроны, цанги, разжимные оправки, гидропластовые втулки, центры и др.
Если в качестве одной из баз служит поверхность, подлежащая обработке на данной операции, и при этом необходимо обеспечить съем симметричного припуска, то используются схемы установки, показанные на рис. 4. Пружинные центрирующие пальцы 1 (рис. 4, а), опускаемые борштангами 2, используют в приспособлении для растачивания головок шатуна 3; выравнивающую скалку 4 (рис. 4, б) применяют в приспособлении для растачивания отверстий в бобышках поршня 5. После выравнивания и закрепления поршня силой Q скалку удаляют и отверстия растачивают (нижняя проекция).
Правильное положение заготовки в приспособлении обеспечивается несколькими способами. В простейшем случае базовые поверхности заготовки вручную доводятся до соприкосновения с опорами приспособления. Одновременное прижатые заготовки по всем опорам обеспечивается зажимными устройствами. В отдельных конструкциях приспособлений для контроля положения заготовки используют электроконтактные датчики и светофорные устройства.
Рис.4. Схемы установки заготовок по обрабатываемым поверхностям
При использовании необходимых баз с параметром шероховатости поверхности Ra>20 мкм установочные элементы следует выполнить с ограниченной опорной поверхностью для уменьшения неровностей этих баз на устойчивость заготовки. Установочные элементы не должны портить базовые поверхности, особенно те, которые не подвергаются повторной обработке.
Установочные элементы должны быть жесткими. Их жесткость повышают, улучшая качество сопряжения элементов с корпусом приспособления, применяя шабрение или шлифование поверхностей стыков, а также сильно прижимая элементы к корпусу приспособления крепежными деталями.
Износостойкость опор повышают, изготовляя их из сталей (У8А, 45, 20, 20Х)с последующей термической обработкой до твердости НRC 55-60. Изнашивание опор можно уменьшить хромированием их несущих поверхностей и наплавкой твердым сплавом, а также шлифованием поверхностей до получения Rа=0.63-0.32 мкм. Для ускорения ремонта приспособления установочные элементы выполняют легкосменными, что особенно важно при массовом производстве.
ПОГРЕШНОСТИ УСТАНОВКИ ЗАГОТОВОК В ПРИСПОСОБЛЕНИЯХ
Погрешность установки е, как одна из составляющих общей погрешности .выполняемого размера, суммируется из погрешностей базирования eб закрепления eз, и погрешности положения заготовки, вызываемой неточностью приспособления eпр. По своему физическому смыслу величина е выражает погрешность положения заготовки.
Погрешностью базирования называют отклонение фактического положения заготовки от требуемого. Оно возникает при несовмещении измерительной и технологической баз заготовки: положение измерительных баз отдельных заготовок в партии будет различным относительно обрабатываемой поверхности. Погрешность базирования представляет собой расстояние между предельными положениями проекций измерительной базы на направление выполняемого размера. Величина е, не является абстрактной, она относится к выполняемому размеру при данной схеме установки и поэтому должна иметь индекс соответствующего размера.
На рис. 5, а показана схема установки, для которой погрешность базирования по отношению к размеру А равна нулю: eбА = 0 (технологическая и измерительная базы совмещены в плоскости 1), а по отношению к размеру В равна допуску на размер С заготовки: eбВ =d (технологическая база 1 не совмещена с измерительной базой 2).
Рис.5. Схемы для определения погрешностей базирования и закрепления заготовок.
При установке в охватывающую иди на охватываемую поверхность к погрешности базирования, определяемой предыдущим способом, добавляется величина проекции смещения измерительной базы на направление выполняемого размера; смещение обусловлено зазором между технологической базой и установочным элементом. На рис. 5, б показана установка заготовки 3 базовым отверстием на палец 4 приспособления. При посадке без зазора (разжимной палец) погрешность базирования для размера А равна половине допуска на диаметр D заготовки. При наличии зазора (жесткий палец) погрешность базирования для этого же размера возрастает на величину диаметрального зазора D;
Погрешность базирования влияет на точность выполнения размеров (кроме диаметральных и размеров, связывающих поверхности, одновременно обрабатываемые одним инструментом или одной инструментальной наладкой), на точность взаимного положения поверхностей и не влияет на точность формы последних. Для уменьшения погрешности базирования следует совмещать технологические и измерительные базы, выбирать рациональные размеры и расположение установочных элементов, устранять или уменьшать зазоры при посадке заготовки на охватываемые или охватывающие установочные элементы.
Погрешность закрепления заготовки eз представляет собой разность наибольшей и наименьшей проекций смещения измерительной базы на направление выполняемого размера при приложении к заготовке силы закрепления. Для партии заготовок погрешность закрепления равна нулю, если величина смещения постоянна; при этом поле допуска выполняемого размера не изменяется, его положение корректируют настройкой станка. Согласно определению
где a— угол между направлением выполняемого размера и направлением смещения измерительной базы.
Выражение в скобках представляет собой расстояние между предельными положениями измерительной базы. Умножая его на cosa, получаем погрешность закрепления для выполняемого размера. Погрешность закрепления eз для размеров А и В (см. рис. 5, а) не равна нулю (a=0), а для размера и Е eз=0, так как боковая (измерительная) база перемещается при зажиме заготовки в собственной плоскости (a=90°).
Сила закрепления должна надежно прижимать заготовку к опорам приспособления. При неправильной схеме закрепления, когда это условие по обеспечивается, часто происходит поворот или смещение заготовки на значительную величину от исходного положения. Такое смещение вызывается неправильной схемой установки. Так, при закреплении в тисках (рис. 5, в) заготовка 3 может повернуться вокруг точки О с нарушением контакта ее нижней базы с опорой тисков.
Смещение измерительной базы заготовки происходит в результате деформации звеньев цепи, через которую передается сила закрепления (заготовка – установочные элементы – корпус приспособления). Из всего баланса перемещений в этой цепи наибольшую величину имеют перемещения в стыке заготовка — установочные элементы. Контактные деформации в постоянных сопряжениях приспособления, деформации сжатие заготовки и деталей приспособления малы.
Зависимость контактных деформаций для стыков заготовка–опоры приспособления выражается нелинейным законом
у=CQ n
Где Q-сила, приходящаяся на опору (n<1); С–коэффициент, характеризующий вид контакта, материал, шероховатость поверхности и верхний слой заготовки. Для типовых случаев С и n находят экспериментально.
Из приведенных зависимостей следует, что eз =0 при постоянной силе закрепления заготовок (Q=const) и одинаковом качестве их базовых поверхностей (С = const), -а также при смещении заготовок перпендикулярно выдерживаемому размеру (a = 90°). Величину eз уменьшают, стабилизируя силу закрепления (применение пневматических и гидравлических зажимов вместо ручных), повышая жесткость стыка опоры приспособления (базовая поверхность заготовки), улучшая качество базовых поверхностей, а также увеличивая жесткость приспособления в направлении передачи силы закрепления.
Погрешность закрепления, как и погрешность базирования, не влияет на точность диаметров и размеров, связывающих обрабатываемые при данном установе поверхности, а также на точность формы обрабатываемых поверхностей.
Погрешность положения заготовки eпр, вызываемая неточностью приспособления, определяется погрешностями при изготовлении и сборке его установочных элементов e ус, износом последних eи и ошибками установки приспособления на станке eс.
Составляющая eус характеризует неточность положения установочных элементов приспособления. При использовании одного приспособления это — систематическая постоянная погрешность, которую частично или полностью устраняют настройкой станка. При использовании нескольких одинаковых приспособлений (приспособлений-дублеров, приспособлений-спутников) эта величина не компенсируется настройкой станка и полностью входит в состав eпр. Технологические возможности изготовления приспособлений обеспечивают eус в пределах 0 – 15 мкм, а для прецизионных приспособлений — 0 – 10 мкм.
Составляющая eи характеризует износ установочных элементов приспособления. Величина износа зависит от программы выпуска изделий (времени работы приспособления), их конструкции и размеров, материала и массы заготовки, состояния ее базовой поверхности, а также условий установки заготовки в приспособление и снятия ее. Больше всего изнашиваются постоянные (ГОСТ 13440—68 и 13441—68) и регулируемые опоры, у которых контакт с заготовкой осуществляется по малым площадкам. Сильно изнашиваются боковые поверхности призм, контактирующие с заготовкой по узкой площадке. Менее интенсивно изнашиваются опорные пластины (ГОСТ 4743—68) и круглые пальцы. При контакте с необработанными поверхностями заготовок со следами окалины и формовочного песка опоры приспособлений -изнашиваются сильнее, чем при контакте с обработанными поверхностями.
Скорость изнашивания возрастает с увеличением массы заготовки и сдвига по опорам при ее установке в приспособлении. Изнашивание неравномерно во времени и носит местный характер. Опорные пластины больше изнашиваются в середине и с одного края, а пальцы – со стороны установки заготовки.
Составляющая eс выражает погрешность установки приспособления на станке, обусловленную смещением корпуса приспособления на столе станка. В массовом производстве при неизменяемом закреплении приспособления на станке eи доводится выверкой до определенного минимума и постоянна во времени. Она может быть компенсирована настройкой станка. В серийном производстве периодически сменяют приспособления на станках, величина eс становится при этом некомпенсируемой случайной. То же происходит на автоматических линиях при использовании приспособлений-спутников. Величина eс составляет 10 – 20 мкм.
ТИПОВЫЕ СХЕМЫ УСТАНОВКИ ЗАГОТОВОК В ПРИСПОСОБЛЕНИЯХ
Установка на плоскости. При установке заготовок на необработанные базовые поверхности используют постоянные опоры с рифленой и сферической головкой (рис. 6, а, в).
Рис. 6. Опоры для установки на плоские поверхности (размеры, мм)
(ГОСТ 13442 – 68), а также регулируемые опоры (ГОСТ 4084 – 68; ГОСТ 4086–68). Первые запрессовывают в корпусе приспособления и при износе меняют. Вторые ввертывают в корпус на резьбе и стопорят в нужном положении контргайкой (рис. 6, г). Их регулируют для компенсации износа и при переналадке приспособления. Установку заготовок обработанными базами осуществляют на опоры с плоской головкой (рис. 6, б) и опорные пластины (рис. 6, д) по ГОСТ 4743—68.
Установка заготовок на внешнюю цилиндрическую поверхность и перпендикулярную к ее оси плоскость производится в опорные призмы и самоцентрирующие патроны с упором в торен или уступ ступени. Для заготовок диаметром 5 – 150 мм с обработанной поверхностью применяют широкие опорные призмы (ГОСТ 12195 – 66; ГОСТ 12197–66) (рис.7, а), для заготовок с необработанной поверхностью узкие призмы (рис. 7, б); при этом в результате локализации контакта уменьшается влияние макрогеометрических погрешностей баз заготовок на их устойчивость в призме. В приспособлениях находят применение, главным образом, призмы с углом a=900. Призмы и втулки изготовляют из стали 20Х, применяя цементацию на глубину 0,8-1,2 мм и закалку рабочих поверхностей (HRС 55–60). Призмы больших размеров выполняют из серого чугуна с привернутыми стальными калеными щеками. Недостаток такой конструкции – пониженная жесткость из-за наличия дополнительных стыков. Призмы крепят к корпусу приспособления винтами и фиксируют контрольными штифтами. Нижнюю и боковые (рабочие) поверхности призм шлифуют до Rа = 0,63¸0,32 мкм.
Рис.7. Типы призм и схема установки заготовки по втулку.
Установка на внешние цилиндрические поверхности с пересекающимися осями характерна для заготовок деталей типа тройников и крестовин. В деталях первого типа (тройники-фитинги, краны) обрабатывают обычно отверстия и торцы. Установку заготовок производят в три узкие призмы (рис. 8, а) при необработанных базовых поверхностях на шесть точек, чем обеспечивается ее полная ориентация в пространстве. Закрепляют заготовку вертикально приложенной силой. Обработку заготовки с использованием необработанных баз стремятся выполнять за одну установку, применяя поворотные приспособления (при последовательной обработке) или агрегатные многошпиндельные станки (при параллельной и параллельно-последовательной обработке).
Обработку деталей типа крестовин нередко ведут в приспособлениях с четырьмя призмами. Такая схема установки теоретически неправильна, так как обеспечить контакт одновременно по восьми точкам (для узких призм) или по длине всех образующих (для широких призм) невозможно. Следует применять схему установки на три призмы; вместо четвертой призмы используют (если необходимо) самоустанавливающуюся опору 1 (рис. 8, б).
Рис. 8. Схема установки заготовок на наружные цилиндрические поверхности с пересекающимися осями
Установка заготовок на внутреннюю цилиндрическую поверхность и перпендикулярную к ее оси плоскость. Такую установку производят на пальцы и оправки. Торец заготовки координирует ее положение но длине, а различные элементы (шпоночная канавка, радиальное отверстие и др.) определяют ее угловое положение. С повышением точности и быстроходности машин возрастают требования к концентричности поверхностей деталей вращения. Во многих случаях отклонение от соосности поверхности не должно превышать 0,01 мм. Это достигается обработкой поверхностей с одного установа и применением точных центрирующие зажимных приспособлений (оправок и патронов). Оправки изготовляют из стали 20Х, цементуют на глубину 1,2-1,5 мм и закаливают до твердости HRC 55–60. Рабочие поверхности шеек шлифуют до Ra - 0,63¸0,32 мкм. При конструировании оправки с запрессовкой обрабатываемой заготовки определяют диаметр ее рабочей шейки.
Погрешности установки на пальцы характеризуются смещениями заготовки на величину диаметрального зазора между поверхностями сопряжения. Если базовый торец заготовки неперпендикулярен к оси отверстия, возможно отклонение оси отверстия от оси пальца. В табл. 1 приведены погрешности базирования для типовых случаев установки заготовок на пальцы и оправки.
Установка заготовки на два цилиндрических отверстии с параллельными осями и перпендикулярную к ним плоскость используется при обработке деталей типа корпусов, плит и картеров. Ее преимущества: простота конструкции приспособления, возможность соблюдения постоянства баз на большинстве операций технологического процесса и относительно простая передача а фиксация заготовок на поточных и автоматических линиях. По сравнению с установкой на шесть точек эта схема обеспечивает большую доступность режущего инструмента к обрабатываемой заготовке. Заготовка закрепляется приложением силы, перпендикулярной к ее базовой плоскости. Такая установка наиболее npигодна для заготовок, имеющих размеры базовой плоскости, большие или сопоставимые с их высотой. Базовую плоскость заготовки подвергают чистовой обработке, а отверстия развертывают с точностью Н7. Установочными элементами служат опорные пластины (ГОСТ 4743-68) и два жестких или выдвижных пальца (посадка Последние применяют при автоматизированной обработке.
Схема установки показана на рис. 9. Заготовку 1 ставят на пластины 2. Палец 3 выполняют цилиндрической, а палец 4 -срезанной (ромбической) формы. Ввиду наличия допуска и на расстояние L между осями базовых отверстий одно из них (рис. 9) может занимать при установке партии заготовок два предельных положения.
Рис. 9. Схема установки заготовки базовыми отверстиями на пальцы
Установка заготовки на внутренние цилиндрические поверхности с пересекающимися (перекрещивающимися) осями применяется для баз с обработанной и необработанной поверхностями. Если базовые поверхности сплошные, то при установке и снятии заготовки с приспособления необходимо применять выдвижные установочные элементы. При установке заготовки на частичные (неполные) базовые поверхности установочные элементы могут быть выполнены неподвижными.
Установка заготовки на центровые гнезда и конические фаски применяется при обработке деталей класса валов. В качестве установочных элементов используют центры с углом 60°. Их конструктивные разновидности показаны на рис. 10. Схема установки на жесткий центр приведена на рис. 10, а; на рис. 10, б дана схема установки конической фаской на срезанный центр, характерная для деталей типа гильз; на рис. 10, в показана схема установки на специальный центр с тремя узкими ленточками 1 на кромки отверстии заготовки. На рис. 10, г приведена конструкции поводкового центра, передающего крутящий момент от вдавливания рифлений в поверхность конической фаски при приложении к центру осевой силы. Этот центр обеспечивает передачу момента, необходимого при чистовой обработке, но ухудшает поверхность базовой фаски. На рис.10, д показана конструкция поводкового центра, передающего момент через рифления, вдавливаемые в торцовую плоскость заготовки. Центры выполняют из сталей 45, У6А, У8А и подвергают термической обработке до твердости HRC 55–60, износостойкость повышают наплавкой твердого сплава. Форму заднего центрового гнезда при токарной обработке сохраняют применением вращающихся центров.
Рис. 10. Центры.
Вопросы для самоповторения.
- Что такое погрешность установки?
- Как устанавливается круглые заготовки?
- Какие типовые схемы применяется при установке заготовок в приспособлениях?
- На каких станках применяются центры.
{/spoilers}