Токарные станки. Токарные станки с чпу. Токарные гибкие производственные модули. Исполнитель
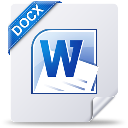
- Скачано: 21
- Размер: 643 Kb
Токарные станки. Токарные станки с чпу. Токарные гибкие производственные модули.
План
- Назначение и принцип работы токарных станков.
- Токарно – винторезные станки и их настройка.
- Токарные станки с ЧПУ.
- Токарные гибкие производственные модули.
{spoiler=Подробнее}
Токарные станки делятся на универсальные и специализированные. Универсальные станки предназначены для выполнения самых разнообразных операций: обработки наружных и внутренних цилиндрических, конических, фасонных и торцовых поверхностей; нарезания наружных и внутренних резьб; отрезки, сверления, зенкерования и развертывания отверстий. На специализированных станках выполняют более узкий круг операций, например обтачивание гладких и ступенчатых валов, прокатных валков, осей колесных пар железнодорожного транспорта, различного рода муфт, труб и т. п. Универсальные станки подразделяются на токарно-винторезные и токарные. Токарные станки предназначены для выполнения всех токарных операций, за исключением нарезания резьбы резцами.
Наша промышленность выпускает различные модели токарных и токарно-винторезных станков - от настольных до тяжелых. Наибольший, диаметр обрабатываемой поверхности на токарных станках колеблется от 95 до 5000 мм при длине заготовки от 125 до 24000 мм. Некоторые токарно-винторезные станки оснащаются копировальным устройством, которое позволяет обрабатывать сложные контуры без специальных фасонных резцов и комбинированного расточного инструмента, а также значительно упрощает наладку и подналадку станка.
Рис. 7. Структурная схема токарно-винторезного станка.
Структурная схема токарно-винторезного станка представлена на рис. 7. Формообразование обеспечивается вращательным движением заготовки (В1) по цели электродвигатель 1,- шпиндель 2 со звеном настройки iv, и поступательным движением инструмента (п1 и п2) по цепи шпиндель двухходовой - вал 4 (при точении) или шпиндель - ходовой винт 3 (при нарезании резьбы) со звеньями настройки ir и iкн.
Токарно-винторезный станок мод. 16К20
Назначение станка - наружное и внутреннее точение, нарезание правой и левой метрической, дюймовой, модульной и питчевой резьб, одно - и многозаходных резьб с нормальным и увеличенным шагом, торцовой резьбы и т. д. Станок применяется в единичном и мелкосерийном производстве.
На рис. 8 показан общий вид токарно-винторезного станка. Станина 1, установленная на передней 2 и задней 8 тумбах, несет на себе все остальные узлы станка. Слева на станине размещена передняя бабка 4. В ней имеется коробка скоростей со шпинделем 5, на переднем конце которого закрепляется патрон. Справа установлена задняя бабка 6. Ее можно перемещать вдоль направляющих станины и закреплять в зависимости от длины обрабатываемой детали на требуемом расстоянии от передней бабки. Режущий инструмент закрепляют в резцедержателе суппорта 7.
Продольная и поперечная подачи суппорта осуществляются с помощью механизмов, расположенных в фартуке 11 и получающих вращение от ходового вала 9 или ходового винта 10. Первый используется при точении, второй - при нарезании резьбы. Величину подачи суппорта устанавливают настройкой коробки подач 3. В нижней части станины имеется корыто 12, куда собирается стружка и стекает охлаждающая жидкость.
Техническая характеристика станка мод. 16К20
1. | Наибольший диаметр детали, устанавливаемой над станиной, мм | 400 |
2. | Расстояние между центрами, мм................ | 710, 1000 и 1400 |
3. | Диаметр отверстия шпинделя, мм.............. | 52 |
4. | Число значении час ют вращения шпинделя | 24 |
5. | Частота вращения шпинделя, об/мин | 12,5-1600 |
6. |
Подачи на один оборот шпинделя, мм: продольные...................... поперечные...................... |
0,05-2,8 0,025 -1,4 |
7. |
Шаг нарезаемой резьбы: метрической, мм................. дюймовой (число ниток на 1").............. модульной, модуль................... питчевой, питч...................... |
0,5-112 56-0,25 0,5-112 56-0,25 |
8. | Мощность электродвигателя, кВт................ | 10 |
Кинематическая схема станка представлена на рис. 9.
Главное движение. Главным движением в станке является вращение шпинделя, которое он получает от электродвигателя 1 через клиноременную передачу со шкивами 2—3 и коробку скоростей. На приемном валу II установлена двусторонняя фрикционная муфта 6. Для получения прямого вращения шпинделя муфту смещают влево, и привод вращения, осуществляется по следующей цепи зубчатых колес: 4-8 или 5-9, 10-13 или 11-14, либо 12-15, вал IV, колеса 18-21 или 19-22, шпиндель V. От вала IV вращение можно передать через перебор 16-23 или 17-24, 25-27 и 26-22 при перемещении вправо блока 21-22 па шпинделе. Переключая блоки колес, можно получить 12 вариантов зацепления колес при передаче вращения с вала IV непосредственно на шпиндель и 12 вариантов - при передаче вращения через перебор.
Рис. 8. Общий вид токарно-винторезного станка мод. 16К20
Реверсирование шпинделя выполняют перемещением муфты 6 вправо. Тогда вращение с вала II на вал III передается через зубчатые колеса 7-28, 29-12, и последний получает обратное вращение.
Движение подачи. Механизм подачи сообщает движение суппорту по четырем кинематическим цепям: винторезной, продольной и поперечной подачи, быстрого перемещения. Вращение валу VIII от шпинделя V передается через зубчатые колеса 20-32, а при нарезании резьбы с увеличенным шагом - от шпинделя V через звено увеличения шага: колеса 22-26, 27-25, 23-16 или 24-17 и через колеса 16-33.
С вала VIII движение передается через реверсивный механизм с колесами 30-35 или 31-34-35 на вал IX, далее через сменные колеса а-b-d или а-b-с-d на входной вал X коробки подач. Переключением муфт 116, 60, 43 и 50, а также перестановкой блочных зубчатых колес 57 и 58, 45 и 46, 47 и 48, 52 и 53 осуществляются различные комбинации соединения колес 36...64 коробки подач. От выходного вала XV коробки подач вращения может быть сообщено либо ходовому винту 61, либо ходовому валу XVI. В первом случае - через муфту 60, во втором - через колеса 59-62, 63-66, муфту обгона 67 и колеса 68 — 64.
Винторезная цепь. При нарезании резьбы подача суппорта осуществляется от ходового винта 61 через маточную гайку, закрепленную к в фартуке. Необходимый шаг резьбы можно получить переключением зубчатых колес и муфт в коробке подач или установкой сменных колес а, b, с, d на гитаре. В последнем случае муфтами 116 и 60 механизм коробки подач отключается. Для предупреждения поломок при случайных перегрузках служит муфта 117.
Продольная и поперечная подачи суппорта. Для передачи движения механизму фартука служит ходовой вал XVI. По нему вдоль шпоночного паза скользит зубчатое колесо 65, передающее вращение через колеса 69, 70, 71 при включенной муфте 72 и червячную пару 13-14 валу XVII.
Для получения продольной подачи суппорта и его реверсирования включают одну из кулачковых муфт - 11 или 84. Тогда вращение от вала XVII передается зубчатыми колесами 15-83-16 и 79-92 или 85-92 валу XVIII и далее реечному колесу 94, которое, перекатываясь по неподвижно связанной со станиной станка рейке 95, осуществляет продольное перемещение суппорта.
Поперечная подача и ее реверсирование осуществляется включением муфт 81 или 90. В этом случае от вала XVII через передачи 75-86 и 88-93-98—96 или 75-86-89 и 91-93-98-96 вращение передается винту 97, который сообщает движение поперечной каретке суппорта.
Установочные перемещения суппорта, резцовых салазок и пиноли задней бабки. Для осуществления быстрого (установочного) перемещения суппорта ходовому валу XVI сообщается быстрое вращение от электродвигателя 113 через клиноременную передачу 114-115. Механизм подачи суппорта через коробку подач при этом можно не включать, так как в цепи привода ходового вала установлена муфта обгона 67. С помощью ходовых винтов 109 и 112 можно вручную через колеса 110- 111 и непосредственно перемещать резцовые салазки и пиноль задней бабки. Станок может быть оснащен механическим приводом салазок. В этом случае от ходового вала XVI через механизм фартука, колеса 65...98 подключается колесо 99 вала XIX, а затем через колеса 100...108 движение передастся винту 109 резцовых салазок.
Через клиноременную передачу 118-119 от вала I подключен насос смазки 120.
Рассмотрим некоторые узлы стайка.
Рис. 9. Кинематическая схема токарно-винторезного станка мод. 16К20 | |
Рис. 10. Коробка скоростей станка мод. 16К20 |
Передняя бабка. На рис. 10 показана конструкция передней бабки с коробкой скоростей. Описание кинематических цепей коробки дано ранее по рис. 9. Все валы коробки скоростей и шпиндель вращаются на опорах качения, которые смазываются как разбрызгиванием (коробка залита маслом), так и принудительно, с помощью насоса. Движение подачи от шпинделя VI передается валу VIII трензеля и далее - на механизм подач.
Задняя бабка (рис. 11) имеет плиту и может перемещаться по направляющим станины. В отверстии корпуса 2 задней бабки имеется выдвижная пиноль 3, которая перемещается с помощью маховика 8 и винтовой пары 5-6. Рукояткой 4 фиксируют определенный вылет пиноли, а вместе с ней и заднего центра 1. Корпус 2 бабки с помощью винтовой пары 13 может смещаться в поперечном направлении относительно плиты 10. Рукояткой 7 с помощью эксцентрика 9, тяги 11 и башмака 14 задняя бабка может закрепляться на станине станка. Винтами 12 и 15 регулируется степень ее закрепления. В корпусное гнездо пиноли можно установить не только задний центр, но и режущий инструмент для обработки отверстий (сверло, зенкер и др.). Задняя бабка имеет пневматическое устройство, которое служит, для создания воздушной подушки, облегчающей перемещение бабки по станине и снижающей износ направляющих. Пневматические устройства подключаются к цеховой сети сжатого воздуха.
Рис. 11. Задняя бабка станка 16К20
Коробка подач (рис. 12) закреплена на станине ниже передней бабки и имеет несколько валов, на которых установлены подвижные блоки зубчатых колес 3, 9, 11, 12 и переключаемые зубчатые муфты 1, 2, 4 и 10. В правом положении муфты 4 получает вращение ходовой винт 5, а в левом ее положении (как показано на рисунке) через муфту обгона 8-7 вращается ходовой вал 6.
Суппорт (рис. 13) состоит из следующих основных частей: нижней каретки 1 для продольного перемещения суппорта по направляющим 4 станины, поперечных салазок 11 и резцовых салазок 9. Поперечные салазки перемещаются в направляющих нижней каретки с помощью винта 2 и безлюфтовой гайки 3. При ручной подаче винт 2 вращается с помощью рукоятки 6, а при автоматической - от зубчатого колеса 5.
В круговых направляющих поперечных салазок установлена поворотная плита 10, в направляющих которой перемещаются резцовые салазки 9 с четырехпозиционным резцедержателем 7. Такая конструкция позволяет устанавливать и зажимать болтами поворотную плиту 10 с резцовыми салазками под любым углом к оси шпинделя. При повороте рукоятки 8 против часовой стрелки резцедержатель 7 расфиксируется. После поворота резцедержателя и фиксирования в новом положении его зажимают, повернув рукоятку 8 в обратном направлении.
Рис. 12. Коробка подач станка 16К20
Механизм фартука (рис. 14) расположен в корпусе, привернутом к каретке суппорта. От ходового вала через ряд передач получает вращение червячное колесо 1 и связанное с ним колесо 20. Оба колеса сидят свободно на валу III. Отсюда вращение передается на колеса 19, 17, 21 и 22, свободно сидящие на валах I, II, IV и V. На этих валах установлены муфты 16, 18, 23 и 25 с торцовыми зубьями, которыми включается подача суппорта в одном из четырех направлений.
Продольное перемещение суппорта (влево или вправо) осуществляется при включении муфты 16 или 18 через колеса 3 или 2, далее через колесо 12, закрепленное на втулке 14. Последняя подвижным шпоночным соединением связана с реечным колесом 15, передающим движение через рейку (на рисунке не показана) суппорту. Колесо 15 может быть выведено из зацепления с рейкой кнопкой 11. Поперечное перемещение суппорта (вперед или назад) осуществляется при включении муфт 23 или 25. Тогда движение зубчатых колес 24 или 26 передается на колесо 13, свободно сидящее на втулке 14, и далее - на винт поперечной подачи суппорта.
Расчет кинематической настройки токарно-винторезного станка мод. 16К20
Настройка кинематических цепей станка для нарезания резьб сводится к подбору передаточных отношений передач коробок подач и других механизмов, что осуществляется переключением соответствующих рычагов. Исключение представляет нарезание особо точных резьб или резьб с ненормализованным шагом. Конечным звеном резьбонарезной цепи являются ходовой винт 55 (см. рис. 9) и маточная гайка, поэтому уравнение настройки согласно равенствам (4) и (7) можно написать в следующем виде (имея в виду однозаходность винта):
1об. шп.=i×tв=tи (9)
где
tн - шаг нарезаемой резьбы;
tв- шаг ходового винта;
i - передаточное отношение кинематической цепи от шпинделя до ходового винта.
Поскольку для рассматриваемого случая валы X, XV и ходовой винт 61, связанные муфтами 116 и 60 (см. рис. 9), представляют собой единое звено, то передаточное отношение цепи
i=iп×iг (10)
где
iп - передаточное отношение постоянных передач;
iг- передаточное отношение сменных колес звена настройки (гитары).
На основании уравнений (9) и (10)
Обозначив 1/iп через С, получим
(11)
Передаточное отношение iп чаще всего равно 1:1 или 1:2. Применительно к кинематической схеме, изображенной на рис. 9, значение iп может быть различным в зависимости от положения блоков с зубчатыми колесами 21-22, 23-24 и 32-33. Если колесо 20, сидящее на шпинделе, сцеплено с колесом 32, то вращение механизму подач сообщает непосредственно шпиндель, и передаточное отношение постоянных передач iп от шпинделя к звену настройки (гитаре) будет (валы V, VIII и IX).
При нарезании резьбы с большим шагом (16 - 112 мм) передача движения осуществляется через звено увеличения шага. В этом случае блок колес 21-22 на шпинделе занимает правое положение, и колесо 16 на валу зацепляется с колесом 33 на валу VIII. Передаточное отношение цепи от шпинделя до вала IX при сцеплении колес в такой последовательности будет иметь два варианта:
Таким образом, включение звена увеличения шага из двух вариантов зацепления колес дает увеличение передаточного отношения от шпинделя до вала VIII в 8 и 32 раза, что соответственно увеличивает шаг нарезной резьбы во столько же раз.
Нарезание многозаходной резьбы. При многозаходной резьбе под шагом tн понимают расстояние между параллельными сторонами профиля двух соседних витков. Поэтому для получения резьбы заданного шага механизм подачи должен за один оборот заготовки переместить суппорт на величину хода резьбы s=k×tн, где к - число заходов нарезаемой резьбы. Такого типа резьбы нарезают на ходовых винтах, многозаходных червяках и других деталях.
Многозаходная резьба нарезается двумя способами: после нарезания первой нитки заготовку поворачивают на часть оборота 1/к; предварительно разомкнув винторезную цепь или оставляя заготовку неподвижной, перемещают инструмент вместе с резцовыми салазками продольно на величину шага резьбы tн. Затем нарезают следующий заход и т. д.
На станке 16К20 имеется специальное делительное устройство для нарезания многозаходных резьб. Оно состоит из кольца с риской, укрепленного на корпусе передней бабки, и диска с делениями, насаженного на шпиндель и имеющего на периферии 60 делений. После нарезания первого захода шпиндель надо повернуть на число делений, равное 60/к. Это устройство позволяет нарезать резьбы с числом заходов 2, 3, 4, 5, 6, 10, 12, 15, 20, 30, 60. На станках, не имеющих делительного приспособления, пользуются поводковой делительной планшайбой.
Обработка конических и фасонных поверхностей на токарных станках
Обработка конических поверхностей на токарных станках производится тремя способами.
Первый способ заключается в том, что корпус задней бабки смещают в поперечном направлении на величину h (рис. 15, а). Вследствие этого ось заготовки образует определенный угол a с осью центров, а резец при своем движении обтачивает коническую поверхность. Из схем видно, что h=L×sina;
(12)
Решая совместно оба уравнения, получим
Для изготовления точных конусов этот способ непригоден вследствие неправильного положения центровых отверстий относительно центров. Второй способ (рис. 15, б) заключается в том, что резцовые салазки поворачивают на угол a, определяемый уравнением (12). Данный способ используют при обработке конусов небольшой длины.
Третий способ основан на применении специальных приспособлений с копировальной линейкой 1, укрепленной на задней стороне станины на кронштейнах 2 (рис. 15, в). Ее можно устанавливать под требуемым углом; к линии центров. По линейке скользит ползун 3, соединенный через палец 4 и кронштейн 5 с поперечными салазками 6 суппорта. Винт поперечной подачи салазок разобщен с гайкой. При продольном перемещении всего суппорта ползун 3 будет двигаться по неподвижной линейке 1, сообщая одновременно поперечное смещение салазкам 6 суппорта. В результате двух движений резец образует коническую поверхность, конусность которой будет зависеть от угла установки копировальной линейки, определяемого уравнением (12). Этот способ обеспечивает получение точных конусов любой длины.
Обработка фасонных поверхностей. Если в описанном копировальном устройстве вместо конусной линейки установить фасонную то резец будет перемещаться по криволинейной траектории, обрабатывая фасонную поверхность.
Для обработки фасонных и ступенчатых валов токарные станки иногда оснащают гидравлическими копировальными суппортами, которые располагают чаще всего на задней стороне суппорта станка. Нижние салазки суппорта имеют специальные направляющие, расположенные обычно под углом 45° к оси шпинделя станка, в которых и перемещается копировальный суппорт.
На практике встречаются самые различные модели токарных и токарно-винторезных станков, от настольных до тяжелых, с широким диапазоном размеров. Наибольший диаметр обработки на современных станках колеблется от 85 до 5000 мм при длине заготовки от 125 до 24000 мм.
{/spoilers}