Монтаж горных машин и оборудования. Исполнитель
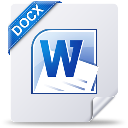
- Скачано: 27
- Размер: 1.87 Mb
Монтаж горных машин и оборудования.
План
- Общие сведения
- Подготовка фундаментов
- Монтаж оборудования
- Монтаж отдельных видов горных машин
Монтажом называют комплекс работ, выполняемых на месте эксплуатации машины или оборудования (монтажной площадке) по ее сборке, установке в рабочее (проектное) положение, подключению к источнику питания, наладке и сдаче в эксплуатацию. Лишь отдельные виды горных машин - бульдозеры, одноковшовые экскаваторы с объемом ковша до 2 м и др. прибывают на рабочее место в собранном виде и требуют монтажа только навесного оборудования, т.е. ввод их в эксплуатацию не занимает много времени. Остальное горное оборудование имеет большую массу и размеры, их доставляют с завода-изготовителя в разобранном виде, причем некоторые из них собираются в подземных выработках в стесненных условиях. Для ввода их в эксплуатацию необходимо проведение сложного комплекса монтажных работ (рис. 3.1).
Объем и содержание работ по монтажу горных машин и электрооборудования зависят от конкретных условий их проведения, которые разнообразны вследствие различий конструкций самих машин и условий их применения.
Способы монтажа горного оборудования очень разнообразны. Наиболее часто машины монтируются постепенным наращиванием или крупноблочным методом. Если оборудование поступило разобранным на блоки, то его собирают из этих блоков [5; 56].
При выборе технических средств монтажа принимают во внимание: габариты и массу ГМиО, условия стесненности монтажной площадки, наличие подъездных путей, электрической и тепловой энергии и т.п.
При ведении монтажных работ подготавливаются: проектно- конструкторская, технологическая и организационная документация.
Проектно-конструкторская документация включает в себя: чертежи монтажного оборудования и приспособлений; схемы разбивки негабаритного оборудования на постановочные блоки; маркировку постановочных блоков и деталей; схемы строповки оборудования и т.д.
Технологическая документация включает в себя: технологические схемы монтажа оборудования, технологические карты на транспортирование и монтаж основного оборудования, ведомости монтажного оборудования материалов и оснастки.
Организационные материалы состоят из графиков производства монтажных работ, потребности основного оборудования, материалов и конструкций для производства монтажных работ, графиков работы монтажных машин, потребности в людских ресурсах, расчета технико-экономических показателей монтажа.
Монтажные работы можно разделить на три основных этапа: подготовительные, производственные и заключительные.
В подготовительные работы, занимающие до 50% продолжительности всех работ, входят: подготовка вышеперечисленной документации; выгрузка элементов оборудования с транспортных средств; проверка комплектности машин; комплектование и сборка их в укрупненные единицы; подготовка транспортных путей; подготовка монтажных площадок (камер); монтаж вспомогательного оборудования и подготовка фундаментов.
Монтажная документация
Рис. 3.1. Содержание монтажных работ
При монтаже горных машин руководствуются следующими видами документации: технической, монтажной и конструкторской.
Техническая - включает проектно-сметную документацию, разрабатываемую проектной организацией, и конструкторскую документацию завода-изготовителя; нормативную, включающую ценники на монтаж оборудования, СНиПы, отраслевые стандарты, технические условия.
Монтажная включает в себя проект производства работ; технические карты; сетевые и линейные графики; журналы монтажных работ; исполнительные документы, составляемые в ходе и по завершению монтажных работ.
Конструкторская документация для горных машин и оборудования содержит паспорт, чертежи общего вида и его сборочных единиц; маркировочную схему; указания о производстве сварки соединений при монтаже; карты смазки и т.д.; инструкции завода-изготовителя по монтажу и эксплуатации машины.
Проект производства монтажных работ включает в себя: графическую часть; ведомости механизмов, инструментов и материалов; графики производства работ, поставки оборудования и движения рабочей схемы [53].
Для планирования работ по монтажу горного оборудования используются линейные и сетевые графики. Линейные достаточно подробно отражают очередность выполнения основных работ и операций. По такому графику можно установить перечень работ, их продолжительность и последовательность выполнения. Однако линейные графики не отражают взаимосвязей между отдельными работами, определяющими общую продолжительность монтажа.
При изменении условий монтажа линейные графики приходится пересматривать, поэтому для четкой взаимосвязи рабочих операций при монтаже и ремонте крупных машин широко применяют сетевые графики, которые представляют собой графическое изображение комплекса взаимоувязанных работ, выполняемых в определенной последовательности.
Сетевые графики позволяют расшифровывать резервы времени и намечать пути рационального использования этих резервов.
При построении сетевого графика пользуются такими понятиями, как работа, событие, путь.
В качестве исходных данных, необходимых для составления сетевого графика, подготавливается и заводится в компьютер следующая информация:
пооперационный перечень работ, подлежащих выполнению, с четким указанием их наименований;
сведения об объемах работ и их плановой продолжительности;
сведения об исполнителях работ, необходимых и имеющихся ресурсах, сроках поставки материалов, деталей, узлов;
очередность работ при выполнении ремонта.
Разработку сетевого графика начинают с составления определителя работ, где указаны наименования, продолжительность и коды работ (i-j), где i- предыдущее событие (начало работы), j- последующее событие (окончание работы). Начало и окончание каждой работы изображают на графике кружками, а процесс выполнения ее стрелкой. Стрелки указывают последовательность выполнения операций, причем исходная операция перемещается левее завершающейся. Длины линий будут произвольными, а продолжительность и трудоемкость работ при составлении графика определяют на основании существующих нормативов. Продолжительность каждой операции, кроме нулевой, соответствующей началу, находится в определенной взаимосвязи, и на графике располагается в соответствии с технологической очередностью монтажа. Продолжительность каждой операции указывают цифрой, проставляемой над линией, снизу - число занятых рабочих. Работы, связанные только логически, обозначаются на графике штриховыми линиями. Непрерывная последовательность работ называется путем, длина которого определяется суммой продолжительности выполнения расположенных на нем работ. Путь наибольшей длины между начальной и конечной операциями называется критическим путем. Его продолжительность определяет срок монтажа. Зная критический путь, можно разработать меры по его сокращению за счет использования резервного времени на остальных ветвях графика, механизации выполнения работ и т.д. (рис. 3.2).
Рис. 3.2. Пример сетевого графика: а) порядок записи события сетевого графика; б) вариант сетевого графика
Расчет сетевого графика позволяет установить обоснованные сроки начала и окончания работ, которые используются при последующем оперативно-календарном планировании, а также установить продолжительность монтажа (ремонта) «критический» путь. От своевременного завершения «критических» работ зависит общий срок окончания ремонта. Остальные работы, «некритические», имеют определенный резерв времени, который может быть установлен при расчете и при необходимости в дальнейшем использован при оптимизации исходного сетевого графика.
Целесообразно производить оптимизацию графика, которая заключается в ликвидации длительных простоев отремонтированных узлов и сокращении критического пути.
Подготовка фундаментов
Монтаж стационарных машин производится на фундаменты, предназначенные для передачи на грунт давления от массы оборудования, возникающих при его работе.
Размеры фундамента указываются на чертежах, поступающих с заводской документацией. Глубина закладки фундамента зависит от типа и габаритов механизмов, от характера грунта и глубины промерзания. Перед изготовлением фундамента уточняют его положение, роют котлован и приступают к изготовлению. В процессе бетонирования фундамента рекомендуется избегать перерывов в работе. Составные части бетона (цемент, песок, щебень) принимаются в пропорции 1:3:5, в ответственных случаях 1:2:3. Бетон утрамбовывается в форму из досок. Фундамент состоит из подошвы, передающей давление на грунт, собственно фундамента и закладочных деталей (анкерных болтов, плит, лаг, стелюг и др. для крепления оборудования).
Фундамент принимают после затвердения бетона и снятия опалубки. При приемке его простукивают молотком, твердость бетона проверяют зубилом.
Результаты приемки фундаментов под механизмы оформляют актом, в котором указывают фактические и проектные размеры фундаментов и закладных частей [22].
Монтаж машины начинается после изготовления фундамента через некоторый промежуток времени, достаточный для того, чтобы материал фундамента полностью затвердел. Бетонные фундаменты до начала монтажа должны стоять не менее 11-15 суток, пуск установленных машин должен быть произведен только через 30 суток после изготовления фундамента. При монтаже стационарных машин вначале устанавливают их рамы, которые крепят к фундаменту болтами.
В машинах небольшой и средней мощности фундаментные болты устанавливаются заранее, в крупных - они вставляются через отверстие в раме. После предварительного крепления рамы вставляются строго горизонтально при помощи клиньев и подкладок. На рис 3.3 представлен набор прокладок.
Допускается (для насосов, вентиляторов и компрессоров) общий наклон фундамента вдоль оси не более 0,15 мм, а в поперечном направлении 0,3 мм на 1 м длины.
После окончания монтажа основных узлов в зазор между рамой и фундаментом производится подливка жидкого цементного раствора, когда заливка затвердеет окончательно, затягивают фундаментные болты и заканчивают установку оборудования. На рис. 3.4 приведена схема подливки рамы, анкерного болта и формы болтов, на рис. 3.5 - крепление нижнего конца анкерного болта.
Монтаж горного оборудования, как правило, ведет предприятие, которое в дальнейшем будет эксплуатировать его, в редких случаях монтаж ведет специализированная организация. Для руководства монтажными работами, соблюдения сроков назначается начальник монтажа. Техническое руководство монтажными работами, регулировку механизмов и наладку оборудования осуществляет шеф-инженер, приглашенный с завода- изготовителя [13].
Для монтажа оборудования на горных предприятиях используют различного вида инструменты, приспособления и механизмы.
Рис. 3.3. Набор прокладок: а - клиновые; б - плоские
Рис. 3.4. Подливка анкерного болта (а), подливка рамы (б), различные формы болтов для полной заливки бетоном (в);
а) 1 - анкерный болт; 2 - бетонная подливка; 3 - песок; 4 - анкерная плита;
б) 1 - основной фундамент; 2 - подливка; 3 - прокладки; 4 - рама; 5 - окна
Упор
Рис. 3.5. Крепление нижнего конца анкерного болта: а - анкерный болт с прямоугольной головкой; б - анкерная шпилька с гайкой
Монтаж оборудования
Для погрузочно-разгрузочных работ на промплощадке горного предприятия можно применять мостовые, автомобильные, гусеничные и железнодорожные краны и автопогрузчики.
Подъемно-транспортные механизмы на автомобильном или пневмохо- ду, без устройства специальных путей, называются монтажными кранами.
Тали и тельферы предназначены для подъема грузов на незначительную высоту. Наибольшее применение получили тали с червячным приводом.
Ручную таль с червячным приводом подвешивают к конструкции на крюке. Приводное колесо связано с червяком. Сварная калиброванная цепь перекинута через колесо. Приводное колесо вращают, перебирая цепь руками. При вращении приводного колеса вращается червячная шестерня со звездочкой. Через нижний блок тали и звездочку проходит грузовая цепь, которая сокращается по длине и поднимает груз.
Ручные тали имеют ограниченный радиус действия, поэтому, чтобы его расширить, применяют электрические тали с тележкой, передвигающейся по монорельсу. Передвигают электроталь вручную или с помощью электрического привода. Управляют подъемом и передвижением с пульта, который подвешен на тросике (рис. 3.6).
В качестве монтажных подъемных механизмов часто применяют маневровые и проходческие лебедки различной грузоподъемности.
Домкраты используют для выполнения вспомогательных операций при такелажных работах. С их помощью производят подъем оборудования и его деталей на небольшую высоту, а также перемещение в горизонтальной плоскости. По принципу действия домкраты делятся на винтовые, реечные и гидравлические (рис. 3.7).
Реечные домкраты применяют для подъема оборудования и различных конструкций незначительной массы, их грузоподъемность не превышает 3-5 т. При работах в стесненных условиях и правке элементов конструкции применяют распорно-винтовые домкраты грузоподъемностью до 20 тонн.
Для подъема груза и деталей большой массы применяют гидродомкраты с ручным или машинным приводом грузоподъемностью до 200 тонн.
Рис. 3.6. Электрическая таль
Блоки монтажные и полиспасты являются одним из простейших приспособлений для перемещения грузов. Блоки могут быть одноролико- выми и многороликовыми. На монтажных работах применяют простые (одинарные) полиспасты с одной тяговой (ходовой) ветвью каната идущей на лебедку. При отсутствии инвентарных блоков и лебедок нужной грузоподъемности применяют сдвоенные полиспасты (рис. 3.8).
6)При выполнении монтажно-демонтажных работ широко используют канаты, стальные цепи и стропы. Грузовые канаты для оснастки монтажных лебедок и полиспастов, подвергаемых перегибам на барабанах и блоках, должны обладать высокой прочностью и гибкостью. Этим требованиям соответствуют канаты типа ЛК-РО конструкции 6*36+1 о. с. Для подвешивания грузов к крюку или захвату подвижного блока полиспаста применяют стропы, захваты и траверсы. На монтажных работах используются преимущественно канатные стропы, реже - цепные.
Захваты и траверсы применяют при необходимости сократить высоту строповки, а также тогда, когда поднимаемые элементы не могут выдержать сжимающую монтажную нагрузку (рис. 3.9).
К основным средствам механизации монтажных работ относят монтажные краны и станки, с помощью которых производят монтаж (демонтаж) механизированных крепей, погрузку и разгрузку горно-шахтного оборудования в горных.
Рис. 3.7. Домкраты: а - клиновой; б - гидравлический; в - схема подъёма груза домкратом двойного действия; I-VI- этапы подъема; 1 - клин; 2 - подъемная плита; 3 - цилиндр; 4 - поршень; 5 - пружина для возврата (втягивания) поршня
в цилиндр; 6 - брусья
Для монтажа и доставки по монтажной камере секций механизированных крепей 2М 81Э, М 130 предназначен монтажно-транспортный кран МТК-3М. Кран целесообразно применять на пластах мощностью 1,8 -3,2 м с углом падения до 32° [21; 44; 47; 48].
Кран (рис. 3.10) состоит из стойки (3) платформы (6) на рельсовом ходу с прицепным устройством и рельсовыми захватами, каретки (5), стрелы (2), навесного оборудования (1), навесной установки (4) с пультом управления.
Для доставки к монтажной камере кран снабжен съемными транспортными полускатами с колеей 900 мм. Конструктивно - это стреловой кран на рельсовом ходу. Все манипуляции крана осуществляются гидродомкратами [41].
Рис. 3.8. Монтажные полиспасты: а - одинарный полиспаст грузоподъемностью 100 т; б - схема запасовки каната, сбегающего с неподвижного блока; в - схема запасовки сдвоенного полиспаста с одной лебедкой; г - то же, с двумя лебедкой; I-V- ветви каната полиспаста; 1 - неподвижный блок; 2 - подвижный блок; 3 - отводной блок; 4 - тяговая ветвь каната; 5 - траверса; 6 - уравнительный блок
д),г)
Рис.3.9. Разновидности гибких канатных стропов: а - УСК-1; б - УСК-2; в - строповка груза в обхват; г - то же, «на удав»; д - 1СК; е - 2СК; ж - 3СК; з - 4СК; и - витой строп; к - сечения витых стропов из 19 и 37 канатов; 1 - канат; 2 - концевое крепление; 3 - коуш; 4 - подвеска; 5 - крюк
Монтажники чаще всего применяют ручной слесарный инструмент. Из ударного наиболее распространенными являются молотки и кувалды. При рубке металла - зубила с различной длиной режущего лезвия. Для обработки поверхности и опиливания металла применяют напильники и надфили.
Почти во все наборы инструмента общего назначения включены плоскогубцы, круглогубцы, торцевые и боковые кусачки и пассатижи. Из них наиболее универсальными являются плоскогубцы.
Рис. 3.10. Кран монтажно-транспортный МТК -3М
Слесарно-монтажные отвертки - стержневого, квадратного и крестообразного сечения (рис. 3.11). Для монтажа двигателей, редукторов, шинопроводов и т.д. применяют гаечные ключи: односторонние, кольцевые, комбинированные, торцевые (рис. 3.12).
Резку черных и цветных металлов, пластмассовых и стальных труб и т.д. осуществляют при помощи ручных раздвижных ножовочных станков (рис. 3.13).
Наиболее распространенным измерительным инструментом являются металлические линейки, складные металлические или пластмассовые линейки, самосвертывающиеся или металлические рулетки, микрометры, штангенциркули, щупы, динамометры (рис. 3.14).
Рис. 3.11 Слесарно-монтажный инструмент: а - молотки; б - зубила; в - плоскогубцы, круглогубцы, кусачки и пассатижи;
г- отвертки
Рис. 3.12. Гаечные ключи
Рис. 3.13. Ножовочные станки: а - конструкция, применяемая при выполнении слесарных работ; б - усовершенствованная конструкция
Рис. 3.14 Измерительный инструмент: а - измерительные металлические линейки; б - складной метр; в - измерительные рулетки
Для опрессовки гильз и кабельных наконечников применяют ручные механические или гидравлические прессы или клещи.
К измерительному строительному инструменту относятся: инструмент для выверки осей машин, фундаментных плит - струны, отвесы, скобы, индикаторы, угольники, уровни. Виброметры, тахометры, счетчики оборотов, термометры и термопары (рис. 3.15).
Рис. 3.15. Уровни
К рабочему инструменту относится: строительный инструмент для такелажных и земляных работ - лопаты, ломы, пилы, топоры, буравы и приспособления - колодки для полировки коллекторов, протачивания валов, снятия шкивов и полумуфт.
Кроме того, при монтаже горных машин применяют электросварочные аппараты, оборудование для газовой резки металла, пневматический и электрический инструменты.
При работе с электрооборудованием необходимо использовать защитные средства: резиновые перчатки, коврики, боты; диэлектрические подставки и слесарный инструмент с диэлектрическими рукоятками [21].
Монтаж отдельных видов горных машин
Монтаж металлических конструкций. Металлические конструкции поставляются на монтаж в виде небольшого числа укрупненных блоков или в виде проката, из которого их изготавливают на месте монтажа или в мастерских.
Металлоконструкции перед сборкой подлежат тщательной ревизии для выявления повреждений, появившихся при транспортировании и в результате коррозии в процессе длительного хранения. Их элементы тщательно очищают от грязи, ржавчины, льда, противокоррозийной краски в стыковых соединениях. Краску удаляют растворителями или скребками с последующим обжигом. Стыковые поверхности подготавливают не ранее чем за 6 часов до сборки стыка, используя газопламенные горелки, специальные пасты и пескоструйную обработку.
Погнутые стержневые элементы подвергают правке. Плавный изгиб устраняют обратным остаточным изгибом без подогрева, а значительные местные искривления исправляют при нагреве до светло-красного каления участка, в 1,5 - 2 раза больше, чем участок искривления.
При постановке укрупненными блоками сборка металлоконструкций состоит из соединения блоков по монтажным стыкам. Сборку ведут с использованием стреловых кранов.
При монтаже стыков добиваются максимального совпадения отверстий под болты и заклепки, а также плотного прилегания деталей (щуп 0,3 мм в любом месте стыка не должен проходить на глубину более 20 мм).
Заклепочные соединения. Клепку осуществляют преимущественно снизу с помощью ручных пневматических молотков. Заклепки диаметром до 11,5 мм клепают в холодном состоянии, а диаметром 13,5 мм и выше - в нагретом. Нагрев выполняется в переносных горнах. По окончании клепки нагретая заклепка должна иметь еще темно-бурый цвет. Качество клепки проверяют остукиванием и внешним осмотром.
Болтовые соединения. Болтовые соединения обеспечивают более надежную работу при действии на стык сдвигающих усилий, устанавливают с зазором более 0,48 мм.
Сварные соединения. Соединения этого типа применяют при стыковке элементов металлоконструкций. Для сварки несущих металлоконструкций из углеродистых сталей, работающих при температуре до -40°С, применяют электроды марки УОНИ 13/45, СМ-11, МР-3, ОЗС-3, ОЗС-4, УП1/45, АНО-2, АНО-3 с диаметром электродов 3,4,5 и 6 мм. При температуре ниже 20°С детали в месте шва предварительно прогревают. Качество сварных швов в условиях монтажной площадки проверяют осмотром, выявляя размеры швов и их дефектов: подрезов, трещин, непроваров, пор и др., сверлением с последующим травлением (выявляют глубину шва и отсутствие внутренних дефектов) и испытанием контрольных образцов. Также проверяют неразрушающий контроль сварных швов с помощью приборов.
Металлоконструкции, как базовые элементы машин, должны отвечать высоким требованиям в части точности сборки. Геометрические размеры элементов большой длины проверяют металлическими рулетками
Монтаж типовых механизмов и деталей. Механизмы современного горного оборудования поставляются на монтаж комплектными сборочными единицами. Поэтому вопросы сборки их составных элементов - валов, осей, подшипников, муфт, зубчатых, цепных передач решаются в основном на заводах изготовителях. На монтажных площадках обычно выполняются работы по соединению механизмов с помощью муфт, гибких передаточных элементов (цепей), зубчатых передач, трансмиссионных валов и др. Важное значение в этих условиях имеет обеспечение правильного расположения соединяемых механизмов и деталей, чтобы обеспечить уравновешенность элементов машин.
Валы и муфты. При монтаже валов возможны отклонения от правильного расположения геометрических осей (рис. 3.16).
Рис.3.16. Правильное расположение валов в пространстве и виды
отклонений:
а - соосны и горизонтальны; б - перекос осей; в - радиальное смещение осей; г - перекос и смещение осей; д - перпендикулярны; е - неперпендикулярны; ж - боковое смещение; з - неперпендикулярность и смещение; и - параллельны; к - непараллельны; л - перекрещиваются
Отклонение от соосности вызывает торцевое биение соединительных муфт, при перекосе осей, а также радиальное биение валов и муфт, при радиальном смещении осей. Все это приводит к недопустимым вибрациям и перегрузкам, вызывающим разрушение валов, муфт и подшипников.
Допустимые отклонения от перпендикулярности и параллельности валов, кинематически связанных передач зависят от частоты их вращения: чем она больше, тем меньше допустимые отклонения.
Существует много способов контроля взаимного расположения валов (рис. 3.17). Наиболее точные - микрометрические (рис. 3.17 д, е) Применение скоб повышает точность, даже при увеличении диаметра на участке измерения.
При монтаже муфт возникают те же отклонения от соосности, что и у валов. Несоосность муфт вызывает радиальные нагрузки на подшипники и детали муфты, которые могут выводить их из строя. Методы их проверки такие же, как и у валов.
Рис. 3.17. Способы проверки взаимного расположения валов и муфт: а - по линейке; б - по клиньям; в - по скобе; г - по скобе с регулировочными болтами; д. - по скобе с индикаторами; е - по скобе с микрометрометром; ж - по скобе, отвесу и уровню; з - по струне и скобам; и - по струне и угольникам; к - по струне, отвесам и скобе; л - по угольнику; м - схема центровки; н - схема записи результатов
При монтаже втулочно-пальцевых муфт обращают внимание на затяжку гаек пальцевых и резиновых колец. Пакет колец должен иметь гладкую цилиндрическую поверхность, без выступов. В зубчатых муфтах должен обеспечиваться радиальный зазор между зубчатыми втулками.
Завершающей операцией монтажа соосных валов и муфт является их центровка. Центровку производят по полумуфтам, которые сами установлены на валах концентрично, а их торцевые поверхности параллельны. Валы считаются отцентрованными, если зазоры, а иbв четырех диаметрально противоположных точках полумуфт (рис. 3.17, н) будут соответственно одинаковыми.
Подшипники. Начальное положение подшипников (разбивку опор) определяют по струнам и отвесам. Окончательную установку и закрепление подшипников соосных валов совмещают с их центровкой.
Подшипники скольжения требуют трудоемкой подгонки вкладышей к корпусу и валу. Сначала подгоняют их к корпусу так, чтобы не было зазора, и вкладыш не проворачивался. Окончательная точность достигается шабрением с проверкой на краску. Гнездо вкладыша покрывают тонким слоем краски, вставляют в корпус, легкими ударами молотка, постукивая по вкладышу, поворачивают последний на 1-2 см в обе стороны, затем вынимают и опиливают по следам краски. При необходимости эту операцию повторяют несколько раз. Аналогично выполняют пригонку вкладыша по валу.
Основной контрольный размер - верхний зазор между подшипником и валом.
Монтаж подшипников качения сводят к установке их на вал с помощью молотка и оправки при малых размерах или с предварительным подогревом в масле (до 90°С) - при больших размерах и значительных натягах. При правильной их сборке должен быть зазор между телами качения и кольцами.
При установке конических подшипников обеспечивают осевые зазоры, предусмотренные документацией. При неправильной установке подшипники демонтируют при помощи съемника.
Зубчатые и червячные передачи. Зубчатое зацепление при монтаже выверяют по положению и размеру пятна касания, а также по боковым и радиальным зазорам, определяемым по толщине свинцовой проволоки.
При выверке по пятну касания поверхность зубьев шестерни покрывают тонким слоем краски, которая позволяет выявить отпечаток зоны контакта.
При выверке цилиндрических зубчатых колес расположение пятна касания на головке (1) (рис. 3.18) указывает на недопустимое увеличение межосевого расстояния (А), на ножке (2) - на недопустимое его уменьшение, а на делительной окружности (3) - на отсутствие отклонения. Аналогичным образом пятна указывают на непараллельность в общей плоскости (рис. 3.18, б) и перекрещивание валов (рис. 3.18, в).
Расположение пятен касания конических зубчатых колес указывает на отклонение межосевого угла Ау (рис. 3.18, г) и межосевого расстояния ДА (рис. 3.18, д). Пятно касания (рис. 3.18, е) соответствует нормативному зацеплению червячной пары, а на рис. 3.18, ж, з - зацеплению при смещениях осей червяка и червячного колеса.
Цепные передачи. Взаимное расположение звездочек цепной передачи выверяют путем измерения расстояний а, а1, а2 до струны С-С (рис.3.19). Угол перекоса звездочки у не должен превышать 10'. Для новой цепной передачи принимают провисание f=0,02 А, где А - межцентровое расстояние.
Соединение деталей. Болтовые соединения, воспринимающие переменные нагрузки, необходимо предохранять от отворачивания.
Резьбовые соединения трубопроводов должны быть уплотнены, т.е. затянуты до отказа. В ответственных случаях болтовые соединения затягивают, пользуясь динамометрическим ключом, или ключом предельного момента.
Герметичность разъемных соединений обеспечивают прокладками и мастиками.
Шпонки подгоняют так, чтобы их боковые грани плотно сидели в гнездах (щуп не должен входить между гранями гнезда и шпонки). Слабо посаженая шпонка не обеспечивает надежную работу соединения.
Рис. 3.18 Положение пятен касания цилиндрических, конических и червячных зубчатых колес: а - нормальное положение зубчатых колес; б, в - ненормальное положение зубчатых колес; г, д - коническое зацепление; е, ж, з - червячное зацепление
Сборка шлицевых (зубчатых) соединений требует соблюдения следующих правил: тщательной проверки шлицы, удаления заусениц и зади- ров; в тугих соединениях охватывающую деталь напрессовывать с использованием специального приспособления или предварительным нагревом до 80-120°С в масле; в особо ответственных соединениях проверка прилегания шлицев по краске; подвижное соединение собирают вручную. Шли- цевое соединение не должно качаться.
Соединение с гарантированным натягом применяют в комбинации с другими соединениями (шпоночными, штифтовыми). Детали небольших размеров запрессовывают вручную легкими ударами молотка по медной оправке.
Рис. 3.19. Проверка положения звездочек в цепной передаче
При запрессовке больших деталей используют винтовые и реечные прессы и гидравлические домкраты. Перед запрессовкой сопрягаемые поверхности тщательно осматривают, удаляют заусеницы и смазывают машинным маслом. Запрессовку начинают с небольшой скорости (5-7 мм/с), при этом проверяют отсутствие перекоса. Перед сборкой деталей больших размеров охватывающую деталь нагревают в ванне с водой или маслом. При использовании тепловых методов отпадает надобность в прессовом оборудовании, которое не всегда имеется на монтажной площадке [22; 44; 53].
Вопросы для самоконтроля
Дайте определение монтажа горного оборудования.
Назовите методы ведения монтажных работ.
Какие документы готовятся для монтажа машин и оборудования на горных предприятиях?
По каким видам графиков ведется монтаж горного оборудования?
Какие исходные данные используются для построения сетевых графиков?
Дайте определение «критического» пути.
Объясните процесс оптимизации сетевого графика.
Назовите этапы изготовления фундаментов под стационарные и передвижные горные машины.
Назовите основное монтажное оборудование, инструменты и приспособления.
Как производится монтаж металлоконструкций?
Расскажите порядок монтажа валов и соединительных муфт.
Расскажите порядок монтажа подшипников.