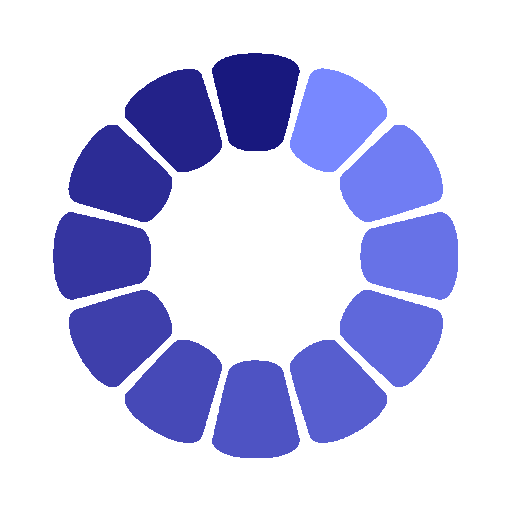
Ballarni quyidagi havolalar orqali stib olishingiz mumkin.
Черные металлы. Производство стали и чугуна, маркировка. Значение и применение черных металлов в технике, промышленности.
План:
1. Черные металлы. Руды, флюсы, легированные металлы, кокс и другие смеси.
2. Производство стали и чугуна, маркировка.
3. Значение и применение черных металлов
{spoiler=Подробнее}
Цель занятия: ознакомить студентов с черной металлургией. С производством черных металлов и их применением
Основная часть:
Черная металлургия. Значение этой отрасли в современной экономике определяется прежде всего тем, что она является главным поставщиком конструкционных материалов для машиностроения и одним из главных поставщиков этих материалов для строительства. В этом качестве черная металлургия испытывает в последние десятилетия нарастающую конкуренцию со стороны цветной металлургии, поставляющей материалы на основе сплавов легких металлов, со стороны химической промышленности, выпускающей конструкционные пластмассы, а также со стороны ряда новых производств, создающих материалы на основе керамики и разного рода композиционные материалы. На темпах выплавки черных металлов сказывается научно-технический прогресс в самой черной металлургии, обеспечивающий повышение качества чугуна и стали и тем самым ведущий к сокращению их удельного потребления на единицу конечной продукции, а также сокращение производственных потерь, особенно в связи с широким использованием методов непрерывной разливки стали. Большие колебания в выплавке черных металлов вызываются также циклическими экономическими кризисами, приводящими к сокращению заказов на металл. Максимума мировая выплавка чугуна (около 560 млн т) и стали (около 790 млн т) достигла в 1989 г., после чего она стала сокращаться и в 1992 г. составила соответственно 500 млн и 720 млн т (падение примерно на 10%), но в 1995 г. вновь увеличилась " до 526 млн и 750 млн т. В первом полугодии 1997 г. выплавка стали в мире велась на уровне 755"760 млн т в год.
Запасы железных руд
Мировые достоверные и вероятные запасы железных руд " основного исходного сырья для получения черных металлов " оцениваются по содержанию железа более чем в 100 млрд т, из которых около 1/3 залегает на территории бывшего Советского Союза. За пределами современного СНГ железными рудами наиболее богаты Бразилия, особенно выделяющаяся своими запасами высококачественных руд, Канада и Австралия: их общая доля в мировых запасах руд указанных категорий оценивается более чем в 2/5. Крупными запасами железных руд располагают также Индия, США, КНР, Швеция, Франция, Венесуэла, ЮАР, из стран СНГ: Россия, Украина и Казахстан.
Добыча железных руд
Товарная железорудная продукция, объединяемая часто понятием "товарная железная руда", фактически включает, помимо кусковой руды, также железорудный концентрат, окатыши и другие виды продукции, отгружаемой с железорудных предприятий, иногда даже агломерат. Ее мировое производство колеблется в 70"90-е годы в широких пределах, приближаясь в отдельные годы к 1 млрд т; в 1988 г. оно составило около 960 млн т, в 1991 г. " 906 млн т, в 1994 г. " 874 млн т. В разных странах тенденции развития железорудной промышленности в последние десятилетия существенно различались: в ряде стран, особенно в Бразилии, Австралии, КНР, преобладала тенденция к ее росту. В Китае годовое производство товарной железорудной продукции доходило до 170 млн т, в Бразилии " до 160 млн т, в Австралии превышало 130 млн т. В то же время в ряде стран с развитой черной металлургией, располагающих значительными железорудными запасами (например, в Великобритании, Германии, Франции), добыча железных руд неуклонно сокращалась, а железорудная промышленность находится на грани полного исчезновения из-за неконкурентоспособности. Из стран Западной Европы лишь Швеция полностью обеспечивает железными рудами себя, а также стабильно экспортирует их в количестве 16"18 млн т в год, чему благоприятствуют высокое качество руд, высокий уровень механизации добычи и близость к странам-импортерам.
Лом. Около 2/5 используемого в черной металлургии железосодержащего сырья составляет лом " промышленный (образуемый на разных стадиях металлообработки) и амортизационный (получаемый в связи с износом оборудования), потребляемый главным образом в сталеплавильном производстве. В некоторых странах доля лома в сталеплавильном производстве превышает 1/2 (например, в Италии, Испании, Швеции, Аргентине, Венесуэле). Крупнейшие страны " экспортеры лома черных металлов: США, Великобритания, Франция, Германия; крупнейшие импортеры: Италия, Испания и Япония.
Чугун В межгосударственном распределении мировой выплавки чугуна в 70"80-е, и особенно в первой половине 90-х годов, когда она велась на годовом уровне 515"530 млн т, произошли большие изменения: быстрый рост выплавки в нескольких развивающихся странах, особенно в КНР (почти на 3/5), Индии и Южной Корее (почти наполовину), Бразилии (на 1/5), обвальным падением в группе постсоциалистических стран, особенно в России и Румынии (на 1/3), Казахстане (более чем на 1/2) и Украине (более чем на 3/5). Из промышленно развитых капиталистических стран значительный рост выплавки чугуна был зарегистрирован лишь в Австралии (почти на 1/4); в большинстве остальных стран этого типа выплавка либо стабилизировалась, либо даже сокращалась. При этом для них был характерен процесс концентрации доменного производства на уменьшающемся числе заводов, наиболее благоприятно расположенных в транспортно-географическом отношении (преимущественно в портовых центрах).
Сталь Во многом сходны сдвиги и в межгосударственном распределении мирового производства стали, которое велось с конца 80-х годов на уровне 730"785 млн т в год. Наиболее впечатляющим стал быстрый рост в 90-е годы выплавки стали в КНР, особенно на фоне ее сокращения в постсоциалистических странах Европы. В 1996 г. КНР обогнала по этому показателю даже Японию, выйдя на первое место в мире. К 2000 г. правительство КНР планирует довести мощности по выплавке стали до 135 млн т в год, а саму выплавку " до 120 млн т. Такими же быстрыми темпами растет выплавка стали в Южной Корее, которая в 1997 г. вплотную приблизилась к крупнейшему производителю стали в Западной Европе " Германии. В число крупнейших производителей стали выдвинулась также Бразилия, догнавшая Италию, которая занимает 2-е место в зарубежной Европе. Следует, однако, иметь в виду, что внушительные количественные показатели темпов и объемов производства черных металлов в указанных странах еще не свидетельствуют о выравнивании технического и технологического уровня их черной металлургии с ведущими металлургическими державами.
Одним из важных показателей уровня технологического развития черной металлургии на современном этапе может служить доля заготовок, получаемых с использованием установок непрерывной разливки стали (УНРС), дающих большой экономический эффект путем резкого сокращения
История развития сталеплавиьного производства
Сталью называют деформируемый (ковкий) сплав железа с углеродом и другими примесями. Получение железа в чистом виде представляет собой трудоемкий и дорогостоящий процесс. Механический свойства, в частности прочность, чистого железа ниже свойств сплавов железа. В чистом виде железо - материал дорогой, его используют для специальных целей. Обычно в техники и в быту сталь. Значение черных металлов вообще и стали в частности в народном хозяйстве огромно. Без использования стали не могли бы развиваться ни горная промышленность, ни транспорт, ни машиностроение, ни сельское хозяйство. За последние 60 - 100 лет во много раз увеличилось производство цветных металлов, особенно алюминия, однако доля черных металлов в мировом производстве продолжает оставаться преобладающей и почти неизменной - около 95% от общего производства металлов. В течение многих лет уровень экономической мощи того или иного государства определялся в первую очередь, количеством выплавленной стали. При этом основную массу составляли, так называемые рядовые марки стали; доля качественных и высококачественных марок была невелика.
Настоящий период развития металлургии характеризуется коренным изменением как масштабов производство качественной и высококачественной стали и доли её в общем производстве, так и методов её получения. Это связано с рядом обстоятельство:
1) для производство стали требуются: добыча и обогащение железной руды, добыча угля и получения из него кокса, добыча добавочных материалов сооружение металлургических заводов, что связано с огромными и все возрастающими (в связи с истощением запасов богатых руд и дефицитом коксующихся угле) затратами материальных, энергетических и трудовых ресурсов;
2) развитие техники позволяет непрерывно повышать эффективность металлургического производства, т.е. из того же количества руды и угля получать все большее количество металлоизделий;
3)непрерывное и осуществляемое все возрастающими темпами перевооружение промышленности связанно с выводом из строя устаревшего оборудования и соответственно с получением большого количества металлолома; металлолом (а не железная руда) все в большей мере становится основным сырьем для производства стали (это относится прежде всего к развитым в промышленном отношении странам - странам с большой "металлоемкостью" народного хозяйства);
4) высокие требования к качеству стали привели к разработке новых технологий, что существенно изменило в последние годы положение дел в сталеплавильной промышленности. Требования новых отраслей техники к качеству многих марок стали, резко возросли 20-30 лет тому назад и продолжают возрастать. Это привело, к увеличению масштабов производства стали и сплавов, содержащих ничтожно малое количество газов, неметаллических включений и других нежелательных примесей, однородных по свойствам. Были разработаны новые способы отработки металла как в самом агрегате, так и вне его. Возможность получения стали с гарантированно низким содержанием вредных примесей при минимальном развитии ликвации, обеспечивает возможность роста промышленного производства, без увеличения количества выплавляемой стали.
Все это вместе взятое явилось причиной новой ситуации в промышленности, при которой масштабы выплавки стали уже не характеризуют промышленную мощь. Главными становятся высокие качество, чистота и надежность металлопродукции. Неизбежное при этом усложнение технологии оправдывается достигаемым результатом. Поясним это следующим расчетом. При работе по традиционной технологии, существовавшей 20 - 30 лет тому назад, из каждых 100 млн. т выплавленной и разлитой в слитки стали получают ~ 75 млн. т проката, из которого в свою очередь получают - 65 млн. т изделий. Из за отсутствия уверенности в высоком качестве металла, отсутствии в нем вредных примесей, возможной их ликвации, отсутствии местных нарушений сплошности металла (пузырей, включений, трещин и т.д.) конструктор закладывает в конструкцию запас прочности (в зависимости от характера нагрузки от 1,5 до 3,0). Если принять этот коэффициент равным 2, то оказывается, что эффективно используется лишь 30 млн. т из каждых 100 млн. т выплавленной стали.
При использовании непрерывной разливки вместо традиционных способов выход проката повышается до 95-97%; замена сортового проката (и обработки на металлорежущих станках) прокатом сложных профилей и листовым прокатом с последующей сваркой и штамповкой позволяет довести массу изделий до 80-85%. Получение стали с гарантированно низким содержанием вредных примесей исключает основную причину ликвации, газовых пузырей, трещин, расслоя и т.п. и позволяет приблизить коэффициент запаса к 1. В результате (учитывая все сказанное выше) оказывается, что из каждых 100 млн. т эффективно используются не 30 млн. т, а 60-70 млн. т. В связи с этом вопроси качества получаемой стали, чистой от нежелательных выключенный и газов, приобретают первостепенную важность.
Вся история металлургии характеризуется непрерывным совершенствованием технологии. Условно процесс непрерывного совершенствования методов и технологии производства стали можно разделить на ряд этапов.
Первый этап. Прямое получение железа из руды. Получение железа непосредственно из руды - наиболее древний способ производство желез а. В глубокой древности железо получали восстановлением его из руды в примитивных горнах. Поскольку в этом процессе использовался не подогретый воздух (сырое дутье), способ получил название сыродутного. Сущность сыродутного способа получения железа заключается в следующем: в горн загружают древесный уголь и железную руду; уголь разжигают и начинают подавать дутье; по мере сгорания и оседания угля руда отпускаются, подвергаясь непрерывному контакту с восстановительными газами и раскаленным углем и постепенно при этом восстанавливаясь. Расчетная температура горения угля в холодном воздухе с нормальной влажностью ~ 1400 °С. Учитывая неизбежные потери тепла, можно предполагать, что температура процесса составляла 1300-1350 °С. При таких температурах, шлак образовывался в жидком виде. Поскольку шлак в основном состоял из оксидов железа, то значительная часть железа руды переходила в шлак и терялась и только 2/3, восстанавливалось до железы. В результате процесса получали раскаленный ком (крицу) восстановленного железа (с прожилками шлака), который вытаскивали из горно и обрабатывали под молотами, уплотняя крицу и выдавливая из нее шлак. Состав металла зависел от состава пустой породы руды, а также от температуры процесса и продолжительности пребывания крицы в горне.
Существовало много разновидностей сыродутного процесса, причем в некоторых установках получали за одну операцию, длившуюся 6-7 ч, до 200 кг железа. Недостатки сыродутного способа производство (малая производительность, большой расход топлива, значительные потери железа со шлаком, высокая трудоемкость процесса и низкое качество металла) определили повсеместное исчезновение этого способа к концу ХIX в. (в ХХ в. сыродутные горны ещё можно было встретить в Африке).
Второй этап. Получение кричного (сварочного) железа из чугуна. По мере усовершенствования сыродутного процесса горны строили большей вместимости, более высокими, подачу дутья интенсифицировали, что приводило к повышению температуры в горне и к более продолжительному пребыванию шихтовых материалов в зоне высоких температур. В результате в ряде случаев происходило заметное на углераживание железа; в этом случае продуктом процесса оказывалось не низкоуглеродистое губчатое железо, а высокоуглеродистое, т.е. чугун. Поскольку чугун не обладает пластическими свойствами, то его считали нежелательным продуктом и выбрасывали. Поже было замечено, что при загрузке в горн чугуна вместо железной руды (или при оставлении в горне высокоуглеродистой крицы и продолжении операции) также получается низкоуглеродистая железная крица. Такой двух стадийный процесс (вначале получение чугуна, а потом получение из чугун, низкоуглеродистого металла) оказался более производительным. Так возник более совершенный способ получения железа - так называемый кричный процесс. Дата появления кричного процесса, так же как сыродутного, неизвестна, но уже в XII-XIII. кричный способ был распространен.
Сущность кричного способа переработки чугуна в железо и сталь заключается в расплавлении чугуна в горне на древесном угле и окислении углерода, кремния, марганца и других примесей кислородом дутья и действием шлаков, богатых оксидами железа.
Выложенный огнеупорными материалами или водо-охлаждаемыми чугунными плитами горн наполняют древесным углем, разжигают его и подают дутье. После того как уголь хорошо разгорелся, присаживают чугун и богатые оксидами железа шлаки (или окалину, или богатую железную руду). Чугун помещают обычно на уровне фурмы или несколько выше ее, он постепенно плавится и капельками стекает вниз. Одновременно с этим под действием кислорода дутья и оксидов железа шлака происходит окисление (выгорание) примесей чугуна. По мере окисления примесей чугуна (в частности, углерода) повышается температура его плавления (температура плавления чугуна 1100-1200°С, низкоуглеродистого железа ~ 1500°С). Температура в горне достигает 1300-1400°С, т.е. достаточного для расплавления чугуна, но недостаточна для поддержания в жидком виде образующегося низкоуглеродистого сплава. По мере окисления примесей металл становится все более тугоплавким и все более вязким. В результате на дне горна получается зернистая, тестообразная, железистая масса, которую собирают в один ком, или крицу, извлекают из горна и подвергают обработке под молотом для удаления из металла шлака и образования возможно более плотного и однородного куска железа.
В связи с тем что горючие материалы, применяющиеся в кричном производстве, находятся в тесном соприкосновении с металлом, они должны быть чистыми от золы и вредных примесей (главным образом, серы). Таким требованиям лучше всего удовлетворяет древесный уголь. Сера во время процесса удаляется в незначительной степени. Фосфор удается удалить на 50-60%, чему способствуют умеренная температура процесса и высокое (иногда >90%) содержание оксидов железа в шлаке. Готовая крица содержит, %: С 0,03-0,05; Si 0,01-0,02; Mn 0,08; Р 0,01-0,04; S 0,004-0,006. Кричный способ производства имеет целый ряд существенных недостатков: низкую производительность, высокий угар железа (до 20%), большой расход топлива, значительную трудоемкость процесса и др.
В большинстве промышленных стран кричный процесс как крайне непроизводительный и дорогой исчез в конце XIX - начале ХХ вв. Низкая производительность и высокая стоимость кричного передела, а также массовое уничтожение лесов вокруг промышленных центров, вызванное необходимостью получения больших количеств древесного угля, - все это заставляло искать более производительный способ производства кричного железа, причем такой, при котором можно было заменить чистый древесный уголь другим топливом более дешевым и менее дефицитным. Такой способ был предложен в 1784 г. Г. Кортом (Англия). Способ заключался в получении стали окислительным плавлением чугуна на поду отражательной печи. Печь получила название пудлинговой. Процесс называют пудлинговым (to puddle англ. - местить, примешивать). При этом способе можно сжигать в топке любое топливо, причем чистота его не играла такой роли, как при кричном переделе, так как непосредственного контакта топлива с металлом не было.
В пудлинговые печи загружали чугунные чушки и расплавляли их. Под воздействием кислорода, содержащегося в печных газах, шлаке и материале футеровки печи, углерод чугуна окислялся. По мере уменьшения содержания углерода в металле возрастала температура его плавления, т.е. металл становился все более и более тугоплавким (температура плавления низкоуглеродистого железа равна примерно 1500°С), а чугуна - около 1100°С). Поскольку температура в печи не превосходила 1400-1450°С, обезуглероженый металл становился все более и более вязким. Сгущающийся сплав перемешивали, добиваясь однородности его состав, и затем "накатывали" из него куски - так называемые "крицы" массой 30-50 кг (рис. 1), которые вытаскивали из печи и проковывали. На обычных печах (садкой около 0,5 т) проводили 10-12 плавок в сутке; расход топлива при этом составлял 0,7-1,0 на 1т металла; угар железа 12-15%.
Получаемые крицы представляли собой комья сварившихся между собой зерен металла. Окончательная сварка зерен происходила при последующих нагревах и обработке металла давлением, поэтому продукты и кричного, и пудлингового процессов часто называют сварочным железом.
Усовершенствованные регенеративные пудлинговые печи со сдвоенным рабочим пространством позволяли получать в сутки ~ 15 т металла при расходе угля ~ 9 т. В начале XX в. стоимость пудлингового железа ненамного превышала стоимость мартеновской стали (в 1908 г. в России стоимость пуда кричного железа 94 коп., пудлингового 80 коп., мартеновского 75 коп.). Недостатками пудлингового процесса являются: высокий расход топлива, низкая производительность, низкий выход годного, невозможность получения литой стали; этот процесс также не выдержал конкуренции с появившимися конвертерным, а затем мартеновским.
Третий этап. Возникновение способа получения жидкой (литой) стали. Наиболее древним из всех существующих способов получения стали в жидком, расплавленном виде, т.е. так называемой литой стали, является тигельный процесс. Точная дата появления этого способа неизвестна. O булатной стали (от перс. "пулад" - сталь) упоминает еще Аристотель. Изготавливаемое из тигельной булатной стали оружие (очень дорогое) называлось в Индии "вуц", в Иране "хорасан", в Сирии "дамасская сталь". Считают, что секрет технологии тигельной плавки утерян в средние века. Возрождение этого способа в Западной Европе произошло в конце первой половины XVIII в. В России производство высококачественной стали тигельным процессом было развито на Златоустовском, Обуховском, Путиловском и других заводах. Знаменитый русский металлург П. П. Аносов, работавший на Златоустовском заводе в течение 30 лет (1817-1847 гг.), предложил методы тигельной выплавки и последующей обработки булатов (сталей, сочетающих высокую упругость с высокой твердостью).
Выплавка стали в тиглях производится следующим образом: в тигли вместимостью обычно 25-35 кг загружают металлическую шихту, по составу близкую к стали, которую необходимо получить. Закрытые крышками тигли помещают в горны или пламенные регенеративные печи (передача тепла металлу осуществляется через стенки тигля).
Тигельная сталь характеризуется очень высокими механическими свойствами как вдоль, так и поперек направления прокатки или ковки. Отсутствие окислительной атмосферы и раскисляющее действие материала тигля, а также сравнительно невысокие температуры процесса, не позволяющие перегреть металл, дают возможность получать плотную сталь с ничтожным количеством неметаллических включений и низким содержанием газов.
Однако тигельный процесс также имеет ряд существенных недостатков, к ним относятся низкая производительность труда, высокие требования к чистоте исходных материалов, малая стойкость тиглей (до трех плавок), высокий расход топлива и другие.
Четвертый этап. Возникновение относительно простых и дешевых способов массового производства литого металла. Простой и дешевый способ получения литой стали в больших количествах путем продувки жидкого чугуна воздухом, был предложен в 1855 г. английским механиком Генри Бессемером. Продувку чугуна проводили в специальном агрегате - конвертере с кислой футеровкой. Способ получил название конвертерного (бессемеровского).
В 1878-1879 гг. Томасом (Англия) был разработан вариант конвертерного процесса, при котором футеровку конвертера выполняли из доломита (материала, обладающего основными свойствами). Этот процесс получил название томасовского или основного конвертерного. В 1865 г. во Франции Эмиль и Пьер Мартены успешно осуществили выплавку стали из чугуна и железного лома в регенеративных пламенных печах. Получение в этих печах высокой температуры, достаточной для расплавления стали, стало возможным благодаря подаче в печь подогретых газа и воздуха.
Принцип использования тепла отходящих газов для подогрева топлива и воздуха в так называемых регенераторах был разработан Сименсом, поэтому в ряде стран процесс называют сименс-мартеновским. Во Франции и в России он получил распространение под названием мартеновского.
Конвертерный и мартеновский способы явились базой, обеспечивающей бурный рост индустриальной мощи промышленно развитых стран. Менее чем за 100 лет, мировое производство стали возросло более чем в тысячу раз (с 330 тыс. т в 1868 г. до 346 млн. т в 1960 г.)
Пятый этап. Развитие электрометаллургии стали. Во второй половине ХIX в. появился ряд предложений по использованию для плавки стали электрической энергии. В конце ХIX - начале ХХ вв. был созданы и начали работать электропечи различных конструкций. Особенно бурными темпами электросталеплавильное производство развивается в последние десятилетия. Появились дуговые сталеплавильные печи вместимостью 200-350 т. Доведение удельной мощности трансформаторов до 700-800 кВт×А/т позволяет расплавлять такую массу металла за 1,5-2 ч. Развитие электрометаллургии стимулируется также возможностью переплава больших количеств такой дешевой шихты, как металлический лом. К настоящему времени уже большое число промышленно развитых стран выплавляют в электродуговых печах более 20-30 % всей стали. Высокопроизводительные дуговые электросталеплавильные печи часто устанавливают на смену старых, отслуживших свой срок мартеновских печей.
Шестой этап. Интенсификация сталеплавильного процесса кислородом. Замена воздуха, используемого в сталеплавильных агрегатах для сжигания топлива или окисления примесей чугуна, чистым кислородом существенно изменяет тепловой баланс процессов (исключаются потери тепла вследствие нагрева балластного азота, поступающего вместе с кислородом воздуха), а также облегчает решение проблемы повышения качества металла. Однако высокая стоимость кислорода длительное время препятствовала осуществлению этой замены. Лишь в послевоенные годы появившиеся относительно дешевые способы получения кислорода позволили начать в широких масштабах разработку соответствующей технологии. Одной из первых стран, где были развернуты эти работы, был бывший СССР. Исследования проводили во второй половине 40-х годов под общим руководством акад. И. П. Бардина.
Первые же опыты подтвердили теоретические расчеты, однако потребовалось несколько лет, прежде чем были отработаны оптимальные приемы работы и конструкции агрегатов, фурм, горелок и т.п. К концу 50-х годов использование кислорода в сталеплавильном производстве стало обычной практикой, которая оказала существенное влияние на масштабы выплавки стали, в мире. В результате только за 10 лет (с 1960 по 1970 г) мировое производство стали возросло с 346 до 603 млн т. Основная масса стали, производимой в настоящее время в мире, выплавляется в агрегатах, где роль окислителя выполняет технически чистый кислород.
Седьмой этап. Появление и распространение переплавных процессов. На процессы удаления из стали вредных примесей влияют такие факторы, как изменение давления, увеличение поверхностей контакта взаимодействующих фаз, ускорение процесса, охлаждения металла, использование плазменной и электронно-лучевой технологии и других. В результате появились и получили за последние годы, значительное распространение такие способы переплава стали, как вакуумный индукционный (ВИП), вакуумный дуговой (ВДП), электрошлаковый (ЭШП), электроннолучевой, плазменный и другие. Поскольку в этих процессах, осуществляется переплав стали, предварительно выплавленной в "обычном" агрегате (конвертерах, мартеновской печи, электродуговой печи), такие процессы называют переплавными. Эти способы сравнительно дорогостоящие и малопроизводительные, но обеспечивают получение металла очень высокого качества с особыми свойствами.
Восьмой этап. Появление и развитие внепечной, вторичной или ковшевой металлургии. Многие технологические операции, проводимые для уменьшения содержания вредных примесей в металле и повышения его качество, можно перенести из плавильного агрегата в ковш (или иной агрегат, заменяющий ковш), специально оборудованный устройствами для соответствующей обработки жидкого металла. Производительность плавильного агрегата при этом возрастает, одновременно, обеспечивается повышение качества стали. Для удаления из металла вредных примесей, усреднения состава и регулирования температуры металл в ковше подвергают вакуумированию, продувают инертными газами, обрабатывают жидкими или порошкообразными смесями или специальной лигатурой, подвергают электромагнитному перемешиванию и т.п. Поскольку эти операции в некоторых случаях продолжительны, а металл постепенно охлаждается, были созданы устройства для подогрева металла в процессе его обработки, т.е. ковш превратился в самостоятельный иногда довольно сложный агрегат. Эти методы получили название ковшевой (или вторичной) металлургии, внепечной обработки или внепечного рафинирования. Помимо повышения качества, внепечная обработка обеспечивает стабильность (от плавки к плавке) свойств металла данной марки, что очень важно потребителям; в результате она за очень короткий срок (в течение 70-х годов ХХ в.) получила повсеместное распространение. В настоящее время сотни миллионов тонн выплавляемой и мире стали подвергают той или иной внепечной обработке. Мероприятия, проводимые для повышения степени чистоты стали (главным образом, в результате внепечной обработки) и выхода годного (главным образом, в результате перехода на непрерывную разливку), вот уже в течение десяти последних лет обеспечивают развитие машиностроения без увеличения количества выплавляемой стали.
Девятый этап. Развитие методов непрерывной разливки. Создание работоспособных агрегатов непрерывной разливки стали позволило:
а) существенно снизить расход жидкой стали для получения 1 т проката;
б) улучшить условия для повышения качества стали;
в) обеспечить реальное начало нового этапа в металлургии: получение стального готового продукта или полупродукта непосредственно из жидкого металла ("прямая прокатка");
г) повысить производительность труда металлургов.
В настоящее время в промышленно развитых странах практически вся выплавляемая сталь разливается на установках непрерывной разливки.
Приведенная выше схема исторического развития сталеплавильного производства условна. Появление тех или иных новых способов производства стали и методов, обеспечивающих повышение ее качества, происходит во времени и многие способы (и старые, и новые) существуют одновременно.
Масштабы производства стали и мире меняются незначительно (740-750 млн. т в год), меняется лишь эффективность использования стали. Основными производителями стали являются: Япония, США, Китай, Россия, Германия, Украина, Южная Корея, Италия, Бразилия, Франция, Великобритания, Индия, Канада, Испания. На эти страны приходится, >75 % выплавляемой стали в мире. При этом производство стали (в мире в целом) составляет: в конвертерах - около 60 %, в дуговых электропечах – около 30 %, остальное - в мартеновских и двух ванных печах. Черная металлургия в России достигла расцвета во второй половине XVIII в., когда Россия занимала первое место по производству черных металлов. Русское кровельное железо экспортировалось за границу и считалось лучшим в мире. К первом половине XIX в. относится деятельность П. П. Аносова. Помимо своих выдающихся открытий в области изучения свойств стали, П.П. Аносов был по существу первым металлургом, которому удалось получить булатную сталь и описать этот процесс в литературе.
В 1913 г., перед первой мировой войной, по количеству выплавляемой стали Россия стояла на пятом месте в мире. В это время в России выплавлялось ~ 4,3 млн т стали в год. После разрухи, вызванной интервенцией и гражданской войной, на территории бывшего СССР выплавлялось < 200 тыс. т стали. В период восстановления народного хозяйства и за годы пятилеток в результате героического труда советского народа производство стали увеличилось более чем в четыре раза по сравнению в дореволюционным. Такое значительное увеличение производства стало возможным в результате строительства ряда новых крупных металлургических комбинатов: Магнитогорского, Кузнецкого, Нижнетагильского, а также коренной реконструкции старых заводов.
Во время Великой Отечественной войны 1941-1945 гг. в результате оккупации врагом значительной территории страны производство стали уменьшилось вдвое, объем производства черных металлов в стране снизился до уровня 1933г. Благодаря исключительному мужеству, самоотверженности, высокой организованности и сознательности советским металлургам уже в марте 1942 г. удалась приостановить снижение выпуска черны металлов. За годы войны на Востоке страны было построено 10 доменных, 29 мартеновских и 16 электродуговых печей, сталеплавильщики Урала освоили выплавку высоколегированной, в том числе броневой, стали в 185-т мартеновских печах, мартеновцы Кузнецка и Магнитки впервые в мировой практике сумели удвоить вместимость действующих мартеновских печей. Начиная с весны 1942 г. производство стали в стране неуклонно возрастало и в 1945 г. было выплавлено уже более 12 млн. т. Огромная работа было проведена по восстановлению разрушенных врагом металлургических заводов, расположенных в центральных районах РСФСР и на Украине. В результате выплавка стали в стране превзошла довоенный уровень в полтора раза. К концу пятой пятилетки (в 1955 г.) в бывшем СССР было выплавлено уже более 45 млн. т стали. Такой значительный рост производства стали после войны, был достигнуть в основном не за счет строительства новых заводов, а за счет увеличения производственных мощностей на действующих предприятиях, увеличения вместимости печей и в первую очередь совершенствования технологии и организации.
В настоящее время черная металлургия России включает 37 комбинатов и заводов, производственная мощность которых по стали составляет около 90 млн. т стали в год.
Около 2/3 стали выплавляется на восьми крупных металлургических комбинатах: Магнитогорском (ММК), Новолипецком (НЛМК), Череповецком (ЧерМК), Кузнецком (КМК), Западно-Сибирском (ЗСМК), Челябинском (ЧелМК), Нижнетагильском (НТМК), Орско-Халиловском (ОХКМ). Три из них (НЛМК, ЗСМК и ЧерМК), построенные сравнительно недавно, являются современными высокотехнологическими, предприятиями, вполне конкурентоспособными на мировом рынке.
В настоящее время в черной металлургии России осуществляется комплекс работ, направленных на совершенствование производство и повышение его эффективности. Работы ведутся в соответствии с "Федеральной программой технического переоснащения и развития металлургии России на период 1993-2000 годы". Реализация Программы позволит увеличить долю прогрессивных сталеплавильных процессов до 70 %, непрерывной разливки до 69 %, снизятся расходы металла на прокат, расходы энергоресурсов и т.д.
Контрольные вопросы:
1. Черные металлы. Руды, флюсы, легированные металлы, кокс и другие смеси.
2. Расскажите о производстве стали и чугуна, маркировка.
3. Значение и применение черных металлов
{/spoilers}