Первичная переработка полезных ископаемых, обогащение руд, подготовка к металлургической переработке Исполнитель
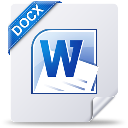
- Скачано: 53
- Размер: 77.5 Kb
Первичная переработка полезных ископаемых, обогащение руд, подготовка к металлургической переработке. Применяемые машины-механизмы и приспособления.
План:
1. Общие сведения по обогащению
2. Подготовка руд к металлургической переработке
3. Применяемые машины-механизмы и приспособления.
{spoiler=Подробнее}
Цель занятия: дать сведения о первичной переработки полезных ископаемых, обогащение руд, подготовка к металлургической переработке. Применяемые машины-механизмы и приспособления.
Основная часть:
Эффективность использования того или другого полезного ископаемого зависит, прежде всего, от содержания в нем ценного компонента и наличия вредных примесей.
Содержание ценных компонентов в добываемом сырье может составлять от долей процента (медь, олова, молибден и др.) до нескольких десятков процентов (железо, алюминий, титан и др.). Непосредственная переработка такого сырья на металлургических или химических заводах технически и экономически невыгодна. Поэтому в большинстве случаев полезные ископаемые подвергаются специальной подготовке с целью их обогащения.
Обогащение полезных ископаемых представляет собой совокупность процессов механической переработки, минерального сырья с целью извлечения ценных компонентов и удаления пустой породы. Около 90 % всех полезных ископаемых подвергается обогащению.
Экономическое значение обогащения полезных ископаемых обусловлено не только тем, что лишь после него становится возможным их использование в различных отраслях народного хозяйства, но и тем, что последующая переработка продуктов обогащения обходится значительно дешевле, чем природной руды, за счет снижение расхода топлива, электроэнергии, материалов. Предварительное обогащение полезных ископаемых позволяет:
- увеличить промышленные запасы сырья (расширить сырьевую базу) за счет использование месторождений бедных полезных ископаемых с низким содержанием ценных компонентов;
- повысит производительность труда на горных предприятиях и снизить стоимость добываемой руды за счет сплошной выемки руды вместо выборочной;
- осуществить комплексное использование сырья, так как предварительное обогащение дает возможность извлечь из него не только основные ценные компоненты, но и сопутствующие, содержащиеся в малых количествах;
- снизить расходы на транспортировку к потребителю более богатых продуктов, а не всего объема добываемого сырья;
- выделит из минерального сырья те вредные примеси, которые при дальнейшей его переработке могут загрязнять окружающую среду и ухудшать качество готовой продукции.
На обогатительных фабриках в результате обогащения получают концентрат (один или несколько), промежуточные продукты (промпродукты) и хвосты.
Концентрат – окончательный продукт обогащения, который по содержанию ценного компонента (минерала или металла) богаче исходный руды и пригоден для дальнейшей переработки. Содержание ценного компонента и примесей в концентрате (качество концентрата) определяется требованиями последующего металлургического передела, а также содержанием металла в минерале и в руде.
Хвосты – продукт обогащения, который по содержанию ценного компонента беднее исходной руды и состоит в основном из минералов пустой породы (кварца, полевых шпатов и др.). Хвосты, не подлежащие дальнейшему использованию в настоящее время, называются отвальными, потери металлов в них должны быть сведены до минимума.
Промпродукт – продукт, выделяющийся в процессе обогащения и требующий дополнительной переработки; по содержанию ценного компонента он богаче хвостов, но беднее концентрата; по содержанию металла может быть одинаковым с исходной рудой.
Технологические показатели обогащения
Процесс обогащения характеризуется следующими технологическими показателями: содержание металла в руде или продукте обогащения; выходом продукта; степенью сокращения и извлечением металла.
Содержание металла в руде или продукте обогащения – это отношение массы этого металла в руде или в продукте обогащения к массе сухой руды или продукта, выраженных в процентах. Содержание металла принято обозначать греческими буквами α (в исходной руде), β (в концентрате) и θ (в хвостах). Содержание драгоценных металлов выражается обычно в единицах массы (г/т).
Выход продукта – отношение массы продукта, полученного при обогащении, к массе переработанной исходной руды, выраженное в долях единицы или процентах. Выход концентрата (γ) показывает, какую долю от общего количества руды составляет концентрат.
Степень сокращения – величина, обозначающая во сколько раз выход полученного концентрата меньше количества переработанной руды. Степень сокращения (К) выражает количество тонн рукды, которое нужно переработать, чтобы получить 1 т концентрата, и рассчитывается по формуле:
К = .
Для руд цветных и редких металлов характерен малый выход концентрата и, следовательно, высокая степень сокращения. Выход концентрата определяется прямым взвешиванием или по данным химического анализа по формуле:
γ = %.
Степень обогащения, или степень концентрации (R) рассчитывается по формуле:
R = ,
и показывает, во сколько раз увеличилось содержание металла в концентрате по сравнению с содержанием металла в руде. При обогащении бедных руд этот показатель может составлять 1000…10000.
Извлечение металла ε – это отношение массы металла в концентрате к массе металла в исходной руде, выраженное в процентах:
ε = .
Уравнение баланса металла
εα = γβ
связывает основные технологические показатели процесса и позволяет рассчитать степень извлечения металла в концентрат, которая, в свою очередь, показывает полноту перехода металла из руды в концентрат.
Качественно-количественное показатели обогащения характеризует техническое совершенство технологического процесса на фабрике.
Качество конечных продуктов обогащения должно соответствовать требованиям, предъявляемым потребителями к их химическому составу. Требования к качеству концентратов называются кондициями и регламентируются ГОСТ, техническими условиями (ТУ) или временными нормами и разрабатываются с учетом технологии и экономики переработки данного сырья и его свойств. Кондициями устанавливается минимально или максимально допустимое содержание различных составных компонентов полезного ископаемого в конечных продуктах обогащения. Если качество продуктов соответствует кондициям, то эти продукты называются кондиционными.
Понятия о методах и схемах обогащения
Обогатительная фабрика является промежуточным звеном между рудником и заводом и входит в состав горно-обогатительного (ГОК) или горно-металлургического (ГМК) комбината. Руда, поступающая на фабрику, проходит различные стадии переработки, которые в зависимости от назначения, называются подготовительными основными и вспомогательными процессами.
К подготовительным относятся процессы дробления, измельчения, грохочения и классификации. При дроблении и измельчении уменьшение крупности кусков руды и раскрытие минералов в результате разрушения сростков полезных минералов с пустой породой (или сростков одних ценных минералов с другими). Грохочения и классификация применяются для разделения по крупности полученных при дроблении и измельчении механических смесей. Задача подготовительных процессов - доведение минерального сырья до крупности, необходимой для последующего обогащения.
К основным обогатительным относятся процессы разделения минералов по физическим и физико-химическим свойствам (по форме, плотности, магнитной восприимчивости, электропроводности, смачиваемости, радиоактивности и др.): сортировка, гравитация, магнитное и электрическое обогащение, флотация, радиометрическое обогащение и др. в результате проведения основных процессов получают концентраты и хвосты. Применение того или другого способа обогащения зависит от минералогического состава руды.
К вспомогательным относятся процессы обезвоживания продуктов обогащения (путем их сгущения, фильтрования и сушки) для доведения их влажности до установленной нормы.
Совокупность последовательных технологических операций переработки, которым подвергаются руды на обогатительных фабриках, называются схемой обогащения. Различают качественные, количественные, водно-шламовые и схемы цепи аппаратов.
Качественная схема (рис.1.1.) дает представление о принятой технологии переработки руды, последовательности процессов и операций, которым подвергается руда при обогащении.
Количественная схема включает данные о распределении ценного компонента по отдельным технологическим операциям и продуктам (извлечение, содержание, выход).
Качественно-количественная схема совмещает в себе данные качественной и количественной схем обогащения.
Водно-шламовая схема содержит данные о количестве воды в каждой операции и продуктах обогащения.
Схема цепи аппаратов показывает пути движения руды и продуктов обогащения через аппараты.
Основное понятие и назначение процессов обогащение
Грохочение – процесс разделения сыпучего зернистого материала на продукты различной крупности (классы) с помощью просеивающих поверхностей. Аппараты, предназначенные для грохочения, называются грохотами, которые имеют одну или несколько рабочих (просеивающих) поверхностей – сит, установленных в одном или нескольких коробах, совершающих качательные или встряхивающие движения.
По технологическому назначению различают два основных вида грохочения:
- предварительное – для выделения готового по крупности продукта (после дробилок);
- контрольное, или проверочное – для контроля крупности дробленного продукта (после дробилки).
Дробление – это процесс уменьшения размеров кусков руды путем разрушения их под действием внешних сил, преодолевающих силы внутреннего сцепления кристаллов твердого вещества. Условно считают, что при дроблении продукты крупностью до 5 мм. Для дробления применяют дробилки различных конструкций. К дробилкам, использующим механический способ разрушения твердых тел, относится щековые, конусные, валковые и молотковые. Дробление производится как сухим способом (основным), так и мокрым (для глинистых руд).
Измельчение, как и дробление, - процесс уменьшения размеров кусков руды путем разрушения их под действием внешних сил. Условно считают, что при измельчении получают зерно крупностью <5 мм. в отличие от дробления при измельчении происходит максимально полное раскрытие сростов минералов.
Измельчение проводят, главным образом, в барабанных мельницах различного типа, отличающихся друг от друга формой барабана, измельчающей средой, способом разгрузки продукта измельчения и принципом действия.
В зависимости от вида измельчающей среды, различают мельницы шаровые, стержневые, галечные и рудно-галечные, самоизмельчения и полусамоизмельчения; по способу измельчения – мельницы для сухого и мокрого измельчения; по способу разгрузки – с центральной разгрузкой и с разгрузкой через решетку.
Гидравлическая классификация – процесс разделения смеси минеральных зерен на классы крупности по скоростям падения в воде. После измельчения руды должна иметь определенную крупность для дальнейшего эффективного обогащения. Достигается это благодаря разделению материала по крупности в классифицирующих аппаратах – гидравлических классификаторах. Работа мельницы в замкнутом цикле с классифицирующим аппаратом нужна для своевременного вывода из процесса готового по крупности продукта. В результате классификации получают два продукта: более крупный – называется песками и возвращается в мельницу, более мелкий – сливом.
В качестве классифицирующих аппаратов применяется механические классификаторы, гидроциклоны и гидравлические классификаторы. В отличие, от грохочения, производящего разделение материала по крупности, гидравлическая классификация делит материалы на классы по равнопадаемости, т.е. каждый класс, полученный при гидравлической классификации, содержит зерна, имеющие одинаковую скорость падения в воде.
Гидравлическая классификация не является собственно обогатительным процессом и относится к подготовительным операциям. В качестве подготовительной операции гидравлическая классификация применяется при подготовке материала перед гравитационным обогащением.
Гравитационными процессами обогащения называются процессы, в которых разделение минеральных зерен, отличающихся плотностью, размером или формой, обусловлено различием в характере и скорости их движения в среде под действием силы тяжести и сил сопротивления. Гравитационное обогащение остается одним из наиболее важных способов разделения минералов. особенно эффективны гравитационные процессы для обогащения руд, содержащих золото, олово, вольфрам, титан, тяжелые черные и цветные металлы, а также для обогащения угля, асбеста, каолина и др., так как в этих полезных ископаемых имеется максимальное различие в плотности между ценных компонентом и минералом пустой породы. Все минералы условно можно разделить на тяжелые, имеющие плотность >2,7 т/м3, и легкие с плотностью < 2,7 м3. к легким минералам относятся кварц, полевые шпаты, сланец, тальк, кальцит, графит, уголь. К тяжелым – галенит, вольфрамит, халькопирит, сфалерит, касситерит, ильменит и др. в качестве среды, в которой осуществляется гравитационное обогащение, используются вода, тяжелая жидкость и тяжелая суспензия.
К гравитационным процессам относятся отсадка, концентрация на столах, обогащение в шлюзах, винтовых сепараторах, струйных желобах, конусных сепараторах, обогащение в тяжелых средах, можно также отнести дезинтеграцию и промывку глинистых руд и россипей.
Отсадка – процесс, основанной на различии в скоростях движения минеральных зерен в пульсирующей в вертикальном направлении среде разделения (воде или воздухе). В результате исходный материал делится на слои, отличающиеся по плотности и крупности. В нижних слоях концентрируется тяжелый продукт, а верхних – легкий.
Обогащение на концентрационных столах является процессом разделения рудных частиц по плотности в тонком слое воды, текущей по слабо наклонной плоской деке, совершающей при помощи привода возвратно-поступательные движения в горизонтальной плоскости перпендикулярно направлению движения воды.
Концентрация на столах применяется для обогащения руд олова, вольфрама, редких, цветных, благородных и черных металлов, а также угля крупностью –4+0,01 мм.
Обогащение на шлюзах, винтовых сепараторах, струйных желобах, конусных сепараторах основано на том же принципе, что и обогащение на концентрационных столах.
Обогащение на шлюзах применяется для переработки песков россыпных месторождений золота, олова и редких металлов, для которых характерно значительное различие в плотности тяжелых и легких минералов.
Шлюз представляет собой наклонный узкий желоб прямоугольного сечения с параллельными бортами, но дно которого укладываются улавливающие покрытия (жесткие трафареты или ворсистые мягкие покрытия, предназначенные для удержания осевших частиц тяжелых минералов).
Винтовые сепараторы представляет собой аппараты, в которых разделение минералов по плотности происходит в безнапорном наклонном потоке малой глубины. У винтовых сепараторов желоб выполнен в виде спирали с вертикальной осью.
Струйный желоб – разновидность шлюза, имеет плоское днище, суживающееся к разгрузочному концу, устанавливается под углом 15…20 град к горизонту, узкой частью вниз. Длина желоба 610…1200 мм, ширина у загрузочного конца 230 мм, у разгрузочного – 25 мм. улавливающие покрытий желоб не имеет.
Конусные сепараторы является разновидностью струйных аппаратов, в которых разделение минералов происходит в тонком слое плотной пульпы (50…60 % твердого).
Обогащение полезных ископаемых в тяжелых средах основано на различии в плотности разделяемого минерала. Минералы меньшей плотности, чем тяжелая среда, всплывают в ней (легкая фракция), а более тяжелые погружаются, представляя собой тяжелую фракцию (концентрат).
Обогащение в тяжелых суспензиях средне- и крупнокускового материала производят в сепараторах, принцип работы которых основан на использовании гравитационных сил. Обогащение мелкозернистого материала осуществляется в центробежных аппаратах (гидроциклонах). Наиболее распространение в мировой практике получили три типа сепаратора: конусные, колесные и барабанные. Колесные сепараторы чаще всего применяют при обогащении угля, магнетитовой руды. Барабанный сепаратор применяется для обогащения железных руд, руд цветных и редких металлов и неметаллических полезных ископаемых.
Главным методом обогащения многих руд цветных металлов является флотация – процесс, основанный на различии в смачиваемости поверхности разделяемых минералов водой. Флотационный процесс обогащения руд заключается в избирательном закреплении минеральных частиц на поверхности раздела двух фаз (жидкой и газообразной). Различают несколько видов флотации (пенная, пленочная, ионная электрофлотация и др.), в промышленности наиболее часто применяется пенная флотация.
Более подробная характеристика процессов обогащения полезных ископаемых приведены в курсе «Минералогия и обогащение полезных ископаемых».
Контрольные вопросы:
1. Дайте общие сведения по обогащению
2. Подготовка руд к металлургической переработке
3. Применяемые машины-механизмы и приспособления.
{/spoilers}