Контрольные приспособления. Исполнитель
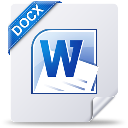
- Скачано: 44
- Размер: 145.5 Kb
Контрольные приспособления.
План
- Назначение и типы контрольных приспособлений.
- Основные элементы контрольных приспособлений.
{spoiler=Подробнее}
Контроль качества изделий весьма важен в современном машиностроении; в особенности велика роль контроля при производстве изделий по принципу полной взаимозаменяемости. Применение универсальных измерительных инструментов и калибров малопроизводительно, не всегда обеспечивает нужную точность и удобство контроля, а в условиях поточно–автоматизированного производства вообще неприемлемо.
Контрольные приспособления повышают производительность труда контролеров, улучшают условия их работы, повышают качество и объективность контроля. Так, при контроле гладкого валика диаметром 40 мм в трех сечениях микрометром обеспечивается производительность 90 деталей в час, при использовании предельной скобы-300 деталей, контрольного приспособления одним индикатором-400, контрольного приспособления с тремя электроконтактными головками и световой сигнализацией–1000 и контрольно-сортировочного автомата-1500. Контрольные приспособления уменьшают попадание брака в годные детали и пропуск годных деталей в брак.
Контрольные приспособления применяют для проверки заготовок, деталей и узлов машин. Приспособления для проверки де талей применяют на промежуточных этапах обработки (межоперационный контроль) и для окончательной приемки, выявляя точность размеров, взаимного положения поверхностей и правильность их геометрической формы.
Высокая точность современных машин обусловливает использование в контрольных приспособлениях измерителей высокой чувствительности и важность правильного выбора принципиальной схемы и конструкции приспособления.
Погрешность измерения, под которой понимают отклонение найденного значения величины от ее истинного значения, должна быть по возможности малой.
Однако чрезмерное повышение точности измерения может привести к усложнению и удорожанию приспособления и снижению его производительности.
Погрешности измерения в зависимости от назначения изделия допускают в пределах, 8—30 % поля допуска на контролируемый объект. Общая (суммарная) погрешность измерения определяется рядом ее составляющих: погрешностью, свойственной самой схеме; погрешностью установки контролируемого изделия; погрешностью настройки приспособления по эталону, износам деталей приспособления, а также колебаниями температуры.
При распределении первичных погрешностей по закону Гаусса поле суммарной погрешности измерений
где D1 D2, .... D n - поля первичных погрешностей.
При конструировании контрольных приспособлений необходимо изучить условия возникновения первичных погрешностей и выявить пути их уменьшения или полного устранения. На выбор принципиальной схемы контрольного приспособления большое влияние оказывает заданная производительность контроля. При 100 %-ной проверке деталей в поточном производстве время контроля не должно превышать темпа работы поточной линии. Для выборочного контроля деталей при стабильных технологических процессах их изготовления требования к производительности контрольного приспособления могут быть снижены.
Для проверки небольших и средних деталей применяют стационарные контрольные приспособления, а для крупных — переносные. Наряду с одномерными находят широкое применение многомерные приспособления, где за одну установку проверяют несколько параметров.
Контрольные приспособления делят на пассивные и активные. Пассивные применяют после выполнения операций обработки. Активные устанавливают на станках; они контролируют детали в процессе обработки, давая сигнал на органы станка или рабочему на прекращение обработки или изменение условий ее выполнения при появлении брака. Контрольные приспособления из самостоятельных устройств превращаются в составную часть автоматических систем. Это позволяет снизить себестоимость продукции в результате устранения брака и исключения контроля как самостоятельной операции.
Контрольные приспособления, обычные и автоматические, должны обеспечивать заданную точность и производительность контроля, быть удобными в эксплуатации, простыми в изготовлении, надежными при длительной работе и экономичными.
Контрольное приспособление состоит из установочных, зажимных, измерительных и вспомогательных элементов, смонтированных в корпусе приспособления. На установочные элементы (опоры) ставят проверяемую деталь, заготовку (узел) своими измерительными базами в процессе контроля. Для установки на базовые плоскости применяют постоянные опоры со сферическими и плоскими головками, опорные пластины (см. рис. 8), а также специальные детали (секторы, кольца) в зависимости от конфигурации базы в плане. Опоры со сферическими головками применяют для установки деталей на необработанные базы; для установки на обработанные базы используют опоры с гладкой и достаточно развитой поверхностью. Для повышения износостойкости опоры рекомендуется термически обрабатывать до твердости НRС 55—60.
Рис. 52. Призмы с роликами (а) и с переставными валиками (б) | Рис. 53. Схема контроля цилиндрической детали в призме |
Для установки на внешние цилиндрические поверхности используют призмы (см. рис. 7, а). Поскольку контакт детали с призмой происходит по узким площадкам (теоретически — линиям), наблюдается сравнительно быстрое изнашивание опорных плоскостей и потеря точности контрольного приспособления. Для устранения этого применяют призмы с роликами (рис. 52, а) или переставными валиками (рис. 52, б). На рабочие поверхности призм для повышения их износостойкости напаивают также пластинки из твердого сплава. Угол призмы a и положение измерительного элемента влияют на точность измеряемого диаметрального размера.
Используя приведенный ранее вывод погрешности базирования для размера Н, получим поле погрешности измерения при плоском торце измерительного наконечника
где d-допуск на диаметр детали; b-угол установки измерительного инструмента (рис. 53, а). Наибольшая точность измерения получается при Sinb/Sin= 1, так как при этом D= 0. Для наиболее употребительных призм с углом a=90° значение b следует принимать равным 45°. Пользуясь призмой, можно проверить правильность цилиндрической поверхности. Эллиптичность поперечного сечения выявляется как разность x между большой а и малой b осями эллипса при вращении детали в призме (рис. 53, б) с углом к = 90°. В этом случае ось детали не меняет своего положения по высоте. Конусность обнаруживается по разности показаний измерительного прибора в двух различных поперечных сечениях детали. Для проверки деталей на радиальное или осевое биение применяют установку на одно или два соосных цилиндрических отверстия. Простейшую схему установки используют при посадке проверяемой детали на гладкую цилиндрическую оправку или палец. Однако здесь возникает погрешность измерения из-за радиального зазора между базовым отверстием и оправкой. Чтобы устранить влияние зазора, применяют конические оправки (конусность 1:1000-1:10000) или разжимные оправки и пальцы. На конической оправке проверяемая деталь не имеет точной фиксации по длине, и ее торец может иметь осевое биение. Величина биения на радиусе r D= rk , где k -конусность оправки. Эти оправки неприменимы для установки на соосные отверстия.
Контрольные оправки должны иметь гладкую рабочую поверхность (Ra~0,4¸0,1мкм). Погрешность формы этой поверхности допускается не более 5 мкм.
Для повышения износостойкости оправки подвергают термической обработке до твердости HRC 55-60. Оправки диаметром более 60 мм целесообразно выполнять полыми. При проверке деталей на биение оправки устанавливают в центры или в призмы. При установке в центры необходимо учитывать несоосность и погрешность исполнения центровых гнезд. От повреждения центровые гнезда предохраняют защитными фасками или торцовыми выточками. Установку деталей отверстиями на оправки и пальцы применяют не только для проверки концентричности и перпендикулярности торцов, ее используют и в контрольных приспособлениях для проверки соосности отверстий, межосевых расстояний, а также расстояний от оси отверстий до параллельно расположенных плоскостей.
При установке деталей ступенчатым отверстием на палец или оправку нужно учитывать возможное отклонение от соосности ступеней отверстия. Согласно рис. 54 ось оправки установится в этом случае под углом b. При малых е
где е — отклонение от соосности отверстий детали; L-расстояние между торцами отверстий, в которые вводится оправка;
величины dA, d’A , d и d’ указаны на чертеже.
Если межосевое расстояние измеряется на расстояние l от торца детали, то погрешность установки оправки в этом сечении e=l tgb+e1.
Кроме рассмотренных схем установки в контрольных приспособлениях применяют также различные сочетания элементарных поверхностей в качестве установочных баз (плоскость-наружная цилиндрическая поверхность, плоскость-отверстие и др.).
Контролируемая деталь (заготовка, узел) имеет две измерительные базы, между которыми на ее чертеже проставлен проверяемый размер. При выборе схем контрольного приспособления следует совмещать установочную и одну из измерительных баз детали, придавая им строго фиксированное, положение. Другая измерительная база должна контактировать с измерительным элементом приспособления в установленном месте. При невыполнении этих условий возникает погрешность базирования eб и погрешность положения измерительного элемента eиз; эти погрешности снижают точность измерения проверяемой детали и принципиально нежелательны.
Рис. 54. Схема для расчета погрешности установки на два отверстия со смещенными осями.
Применение многомерных контрольных приспособлений повышает качество контроля, высвобождает значительную часть контролеров и сокращает издержки на контрольно-измерительную оснастку. Для использования многомерных приспособлений необходимы простановка проверяемых размеров от единой измерительной базы и возможность совмещения этой базы с удобной для контроля установочной базой детали. В отдельных случаях необходим пересчет допусков на проверяемые размеры с учетом специфики многомерного контроля.
Зажимные устройства в контрольных приспособлениях предупреждают смещения установленной для проверки детали (узла) относительно измерительного устройства и обеспечивают плотный контакт установочных баз детали с опорами приспособления. Работа зажимного устройства контрольного приспособления существенно отличается от работы аналогичных устройств в станочных приспособлениях. Для предупреждения деформаций проверяемых изделий силы закрепления должны быть небольшими, а их величина-стабильна. Необходимость в зажимных устройствах отпадает, если деталь занимает в плане устойчивое положение на опорах приспособления и силы от измерительного устройства не нарушают этой устойчивости. Для повышения производительности контроля зажимное устройство выполняют быстродействующим и удобным для обслуживания.
В контрольных приспособлениях применяют ручные зажимные устройства (рычажные, пружинные, винтовые, эксцентриковые), а также устройства с приводом (пневмозажимы), в которых сжатый воздух используется и для привода вспомогательных механизмов приспособления (подъем, поворот или выталкивание детали).
Часто применяют комбинированные зажимные устройства, обеспечивающие одновременный и равномерный прижим контролируемых деталей к нескольким опорным элементам приспособления. Место приложения силы закрепления выбирают так, чтобы исключить недопустимые деформации детали и элементов контрольного приспособления. Влияние зажимного устройства на показания измерительного прибора не должно превышать 5 % величины контролируемого параметра детали. При стабильной величине силы закрепления эта погрешность измерения получается постоянной, и ее можно учесть в процессе настройки измерительного устройства по эталонной детали. Если эта погрешность колеблется от максимального значения Dmax до минимального Dmin в результате нестабильной силы закрепления, то разность между ними не может быть учтена настройкой. Назовем эту разность погрешностью закрепления и обозначим e3.
Регламентированную погрешность изготовления, а также износ опор и измерительного устройства приспособления обозначим eпр. При определении eпр учитываем ту величину износа, которая имеет место между периодическими настройками приспособления. Как и в станочных приспособлениях, значения eб, e3 и eпр представляют собой поля рассеяния случайных величин, распределение которых можно в первом приближении принять подчиняющимся закону Гаусса. Погрешность установки найдем по формуле
Измерительные устройства контрольных приспособлений делятся на предельные (бесшкальные) и отсчетные (шкальные). Особую группу составляют устройства, работающие по принципу нормальных калибров.
Предельные устройства не дают численного значения измеряемых величин, а все проверяемые изделия делят на три категории; годные, брак по переходу за нижнюю границу допуска и брак по переходу за верхнюю границу допуска. Иногда годные изделия разбивают на несколько размерных групп для селективной сборки.
В качестве простейших устройств применяют, встроенные в контрольные приспособления, жестко закрепленные или выдвижные предельные элементы (скобы, пробки, щупы). Примеры таких приспособлений для контроля размеров детали показаны на рис. 55. При наличии жестко установленных скоб проверяемая деталь последовательно передвигается по плите приспособления к отдельным измерителям. Если деталь в процессе проверки должна оставаться неподвижной, то применяют выдвижные предельные элементы (рис. 55, а). Эти устройства используют при сравнительно грубых допусках на проверяемый размер-для жестких элементов не выше 8-9-го квалитетов, а для выдвижных-не выше 11-го. Для контроля размеров заготовок с допусками более 0,5 мм иногда применяют стержневые глубиномеры (рис. 55, б). Годность изделия соответствует положению верхнего торца стержня между ступеньками в и г.
Рис. 55. Приспособления с выдвижными предельными элементами
Широкое распространение получили электроконтактные датчики; их применяют в контрольных приспособлениях и контрольно-сортировочных автоматах. Схема контрольного приспособления с электроконтактным датчиком для одномерного контрольного приспособления приведена на рис. 56. Если проверяемый размер D находится в поле допуска, то лампы 1 и 2 не загораются. Если размер D меньше минимально допустимого, замыкаются нижние контакты и загорается лампа 1. При большом максимально допустимом размере загорается лампа 2. Лампа 3 загорается при размыкании обоих контактов, т, е. когда детали годны, Сопротивления этой моcтиковой схемы подобраны так, что при замыкании одного из контактов лампа 3 гаснет. Таким образом, на любой стадии работы приспособления горит одна из трех ламп. Неисправность схемы и перегорание ламп обнаруживается по отсутствию света. Электроконтактные датчики удобны для многомерных контрольных приспособлений светофорного типа. Они обеспечивают значительное повышение производительности и облегчают труд контролеров. Технические требования на датчики регламентированы ГОСТ 3899—68.
Рис. 56. Приспособление с электроконтактными датчиками
Применяют также многоконтактные датчики для сортировки деталей на размерные группы. Электроконтактные датчики выпускают двух типов: предельные и амплитудные. Первые применяют для контроля размеров, вторые-для контроля формы и расположения поверхностей детали.
Электрические схемы включения электроконтактных датчиков бывают с силовым и сеточным контактами. Недостатком датчиков первого типа является понижение точности работы из-за подгорания контактов. Для повышения надежности работы датчиков их контакты выполняют из вольфрама и включают в цель низкого напряжения (3—5 В). Датчики настраивают и периодически проверяют по эталону. Датчики второго типа не имеют отмеченного недостатка, они долговечны и работают устойчиво.
Электроконтактные датчики обеспечивают точность измерения 1 мкм (1-й класс) и ±3 мкм (2-й класс); такая точность сохраняется до 25 тыс. измерений без регулировки датчиков. Предел измерения 1 мм, а сила измерения 1-2 Н. Реже применяют емкостные, индуктивные и фотоэлектрические датчики. Приспособления с отсчетными устройствами применяют при обычном и статистическом контроле. Они необходимы также для проверки настройки станков на размер.
В качестве отсчетных измерителей обычно используют индикаторы с рычажной или зубчатой передачами. Индикаторы часового типа (ГОСТ 577-68) имеют цену деления 0,01 мм и выпускаются с пределами измерения 0-5 и 0-10 мм. Малогабаритные индикаторы имеют суженные пределы измерения 0-2 или 0-3 мм. Сила прижатия измерительного наконечника в начале и конце хода 0,8-2 Н.
По точности исполнения индикаторы выпускаются нулевого 1-го и 2-го классов с погрешностью показаний соответственно 0,01, 0,015 и 0,02 мм за один оборот стрелки. Индикаторы крепят за ножку или за ушко на их задней крышке. При цене деления 0,01 мм индикаторы часового типа используют для проверки деталей с допусками от 0,03 мм и больше. При меньших допусках эти индикаторы могут применяться с увеличивающей рычажной передачей. Для более точных измерений применяют индикаторы с ценой деления 0,002 мм (микроиндикаторы) и миниметры (цена делении до 0,001 мм). Получили распространение также пневматические микрометры. Их использование в контрольных приспособлениях обеспечивает точность измерений 0,5-0,2 мкм.
Для выбора отсчетных измерительных средств в зависимости от допусков и серийности производства необходимо учитывать их метрологические и экономические показатели. К метрологическим показателям относятся цена деления шкалы, предел измерения, чувствительность (т. е. отношение изменения сигнала на выходе к вызывающему его изменению измеряемой величины), погрешность показаний (отклонение результата измерения от истинного значения измеряемой величины), порог чувствительности (наименьшее значение измеряемой величины, которое может вызвать изменение положения указателя прибора), период успокоения стрелки, что существенно влияет на производительность контроля, а также давление при измерении.
Рабочий наконечник измерительного устройства может быть сферическим (для проверки плоскости или отверстия), плоским (для проверки сферы) и ножеобразным или сферическим (для контроля наружных цилиндров).
К экономическим показателям относятся; затраты на измерительное устройство; продолжительность его работы до ремонта; время, затрачиваемое на измерение; квалификация контролера; время и затраты на установку измерительного устройства; увеличение затрат вследствие уменьшения допусков, вызываемого погрешностью измерительного устройства. Влияние каждого показателя меняется в каждом конкретном случае. Наибольшее влияние на себестоимость контроля обычно оказывает последний показатель. Применение малоточных средств измерения вызывает необходимость уменьшения допуска на изготовление. Установлено, что затраты на повышение точности измерения малы по сравнению с возможным уменьшением допуска. При выборе измерительных устройств необходимо в каждом конкретном случае найти наиболее выгодное решение для получения изделий с наименьшей себестоимостью.
В качестве устройств, работающих по принципу нормальных калибров, в контрольных приспособлениях используют контурные, плоские или объемные шаблоны. Оценка соответствия проверяемых деталей производится с помощью щупов или на просвет. Часто в приспособлениях этого типа проверяют координацию контура базовым отверстием. Это осуществляют с помощью контрольных скалок (пробок). Деталь бракуют, если не удается установить ее в приспособлении и ввести пробки, а также если ее установка производится с большим зазором.
Вспомогательные устройства контрольных приспособлений имеют различное целевое назначение. В приспособлениях для проверки радиального или осевого биения применяют поворотные устройства, в приспособлениях для проверки прямолинейности или параллельности используют ползуны для перемещения измерительных элементов. Для контроля правильности формы шеек цилиндрических деталей или соосности ступеней применяют приводные механизмы для их вращения. Для установки и снятия деталей используют подъемные устройства и выталкиватели. Многие из этих устройств выполняют аналогично соответствующим устройствам станочных приспособлений.
Специфичными являются передаточные устройства между контролирующим элементом и отсчетным измерителем (индикатором, электроконтактным датчиком).
Простейшая схема приспособления — схема с жесткими предельными элементами для проверки высоты уступов (размеры Н1 и Нг) ступенчатой детали, которую в процессе контроля передвигают по плите вручную (рис. 57). Контроль производят от нижней базовой плоскости. Схема приспособления с выдвижными предельными элементами показана на рис. 55; на этом приспособлении проверяют размеры Нъ Нг и Н3.
Рис. 57. Приспособление с жесткими предельными элементами | Рис. 58. Индикаторные приспособление для проверки соосности двух без отверстий |
Схема индикаторного приспособления для проверки соосности двух отверстий дана на рис. 58. Контролируемую деталь 1 надевают на консольный пустотелый палец 2 и в процессе проверки поворачивают рукой на один оборот. При эксцентриситете малого отверстия измерительный наконечник 3 передает движение через рычаг 4 и штифт 5 на индуктор 6. На его шкале отмечается удвоенная величина эксцентриситета.
Вопросы для самоповторения.
- Какую функцию выполняет контрольные приспособления?
- Основные элементы контрольных приспособлений.
- Для чего применяется индикаторы часового типа?
- Что такая калибирная пробка?
- Какие мерительные инструменты применяется в серийном производстве?
{/spoilers}