Прогрессивные методы литья. Исполнитель
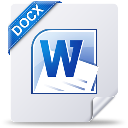
- Скачано: 41
- Размер: 443.5 Kb
Прогрессивные методы литья.
План.
- Литьё по выплавляемым моделям.
- Литьё под давлением.
- Литьё в кокиль.
- Центробежное литьё.
{spoiler=Подробнее}
Сущность способа литья по выплавляемым моделям заключается в процессе получения отливок из расплавленного металла в фор мах, которые не требуют разъема, так как рабочая полость образуется в результате удаления (вытекания) легкоплавкого материала модели при ее предварительном нагревании. Выплавляемые модели изготовляют из модельных составов, состоящих из двух и более компонентов. Для изготовления моделей широко используют модельный состав Р-3, который содержит парафин, синтетический церезин, буроугольный воск и кубовый остаток. Этот состав хорошо заполняет полость пресс-формы, дает четкий и чистый отпечаток. Выплавляемые модели изготовляют в пресс-формах, состоящих из двух и более частей с вертикальным или горизонтальным разъемами. Для извлечения моделей из пресс-форм применяют специальные толкатели.
Модельный состав в пастообразном состоянии запрессовывают в пресс-формы (рис. 12, а) на автоматических установках или вручную. После затвердевания модельного состава пресс-форма раскрывается и модель выталкивается в ванну с холодной водой. Затем модели собирают в блоки (рис. 12, б) с общей литниковой системой, которая создается припаиванием, приклеиванием или механическим скреплением частей. В один блок объединяют от 2 до 100 моделей. Формы по выплавляемым моделям изготовляют из специальной огнеупорной смеси, состоящей из связующего, гидролизованного раствора этило-силиката, огнеупорного наполнителя — пылевидного кварца и других компонентов. Формы по выплавляемым моделям изготовляют многократным погружением разовой модели в огнеупорную смесь (рис. 12, в) с последующей обсыпкой (рис. 12, г) и отверждением на воздухе. Обсыпку обычно наносят в три - пять слоев.
Модели из форм удаляют выплавлением при нагреве (рис. 12, д, е) в горячей воде или паром. После удаления модельного состава тонкостенные литейные формы заформовывают в опоки (рис. 12, ж), а затем прокаливают в печи (рис. 12, з) в течение 6—8 ч при температуре 850—950 °С для удаления остатков модельного состава, продуктов неполного гидролиза, спекания частичек связующего с частичками огнеупорного материала, испарения воды и. т. д.
Рис. 11, Схема работы автоматической линии для без опочной формовки:
а __ сдув смеси и прессование; б — протяжка левой полу модели; в — проталкивание формы вперед; е — возврат прессовой платы и закрывание камеры
Рис. 12. Последовательность операций формовки
при литьё по выплавлявмим моделям
Заливку форм по выплавляемым моделям производят в нагретом состоянии сразу же после прокалки. Заливка может быть (Свободной, под действием центробежных сил, в вакууме и т. п. После затвердевания расплавленного металла и охлаждения отливки удаляют из форм механическими, а также химическими методами, очищают, обрубают и, как правило, подвергают термической обработке.
Процесс изготовления заготовок литьем. по выплавляемым моделям механизирован и автоматизирован. Литье по выплавляемым моделям обеспечивает получение точных и сложных отливок из любых сплавов, сокращает объем механической обработки, создает благоприятные условия для хорошего заполнения литейных форм, что позволяет получать отливки из сплавов с низкими литейными свойствами. Этим способом получают отливки массой 0,02—15 кг с отверстиями диаметром до 1 мм и толщиной стенок до 0,5 мм. Литьем по выплавляемым моделям отливают многие детали и заготовки для приборостроительной, авиационной и других отраслей промышленности. Вместе с тем недостатком этого способа является сложность и длительность процесса изготовления отливок, применение специальной дорогостоящей оснастки.
Сущность литья в оболочковые формы заключается в получении отливок заливкой расплавленного металла в формы, изготовленные по горячей модельной оснастке из специальной смеси с термореактивными связующими материалами. Формовочную смесь приготовляют из мелкозернистого кварцевого песка или из цирконового перемешиванием с термореактивными связующими материалами, в частности, с пульвербакелитом (смола ПК 104). В формовочную смесь добавляют увлажнители (керосин, глицерин), растворители (ацетон, этиловый спирт) и другие вещества.
При изготовлении оболочковых форм модельную плиту и модель нагревают в печи до 200—250 °С и пульверизатором наносят разделительную смазку для облегчения последующего съема оболочки, затем плиту / закрепляют на опрокидывающемся бункере 2 (рис. 13, а) с формовочной смесью 3 и поворачивают его на 180° (рис. 13, б). Формовочная смесь насыпается на модельную плиту и выдерживается 10—30 с. От теплоты модельной плиты термореактивная смола в пограничном слое расплавляется, склеивает песчинки и отвердевает с образованием песчано-смоляной оболочки 4 толщиной 5—15 мм в зависимости от времени выдержки. Бункер возвращается в исходное положение (рис. 13, e)t излишки формовочной смеси ссыпаются с готовой оболочки 5, модельная плита с оболочкой прокаливается в печи при температуре 300—350 °С, при этом смола переходит в твердое необратимое состояние. Твердая оболочка снимается с модели специальными выталкивателями 6 (рис. 13, г).
Кроме оболочковых форм этим способом изготовляют оболочковые стержни, при изготовлении которых используют нагреваемые металлические стержневые ящики. При сборке форм полуформы склеивают специальным клеем на прессах, что обеспечивает высокую прочность шва.
Заливка форм производится в вертикальном или горизонтальном положении оболочки. При заливке форм в вертикальном положении их помещают в опоку 7 и засыпают чугунной дробью 8 для предохранения от преждевременного разрушения (рис, 13, д).
Выбивку отливок проводят на вибрационных решетках или на специальных выбивных установках. При очистке отливок удаляют заусенцы, зачищают на наждачных станках места подвода питателей и подвергают отливки дробеструйной обработке,
В промышленность внедрены многопозиционные автоматические машины и автоматические линии изготовления оболочковых форм и стержней. Литье в оболочковые формы обеспечивает высокую точность отливок, малую шероховатость поверхности, снижает расход формовочных материалов и объем механической обработки, повышает производительность труда. В оболочковых формах изготовляют отливки массой 0,20—50 кг и толщиной стенок 3—15 мм из всех литейных сплавов для приборов, автомобилей, тракторов, металлообрабатывающих станков и др.
Изготовление отливок в металлических формах. Сущность способа литья в кокиль заключается в получении отливок из расплавленного металла в металлических формах — кокилях. Формирование отливки происходит в условиях интенсивного отвода теплоты от расплавленного металла и от затвердевающей и охлаждающейся отливки к массивному металлическому кокилю.
Отливки с простой конфигурацией изготовляют в вытряхных кокилях (рис. 14, а). Несложные отливки с небольшими выступами и впадинами на наружных поверхностях изготовляют в кокилях с вертикальным разъемом (рис. 14, б). При изготовлении крупных» простых по конфигурации отливок используют кокиля с горизонтальным разъемом (рис. 14, в). Кокили с комбинированным разъемом применяют при изготовлении сложных отливок. Полости в отливках оформлены песчаными или металлическими стержнями. Металлические стержни удаляют из отливки до извлечения ее из кокиля, после образования прочной корки в отливке.
Расплавленный металл в форму подводят сверху; если снизу — сифоном, сбоку — через щелевидный питатель или питатели, расположенные на нескольких уровнях. Для удаления воздуха и газов по плоскости разъема кокиля прорезают вентиляционные каналы. Отливки из полости кокиля извлекают выталкивателями. Заданный тепловой режим литья обеспечивает система подогрева и охлаждения кокиля. Кокили изготовляют из серого и высокопрочного чугунов, стали и алюминиевых сплавов литьем, механической обработкой и другими способами.
Рис. 14. Конструкции кокилей:
Технологический процесс изготовления отливок в кокиль включает нагрев кокиля до 150-300°С, нанесение на рабочую поверхность слоя теплоизоляционного покрытия толщиной 0,3—0,8 мм, установку стержней, соединение и скрепление частей кокиля, заливку расплавленного металла, выдержку для затвердевания залитого металла и формирования отливки, раскрытие и выбивку отливки. Для уменьшения скорости затвердевания и охлаждения отливки, а также для повышения стойкости кокиля на его рабочую поверхность наносят теплоизоляционные покрытия, приготовленные из огнеупорных материалов (кварцевой муки, талька, графита и др.) и связующего материала (жидкого стекла).
Все операции технологического процесса механизированы и автоматизированы. Применяют однопозиционные и многопозиционные автоматические кокильные машины и автоматические кокильные линии изготовления отливок. Литье в кокиль позволяет сократить, а во многих случаях полностью исключить расход формовочных и стержневых смесей, а также трудоемкие операции формовки и выбивки форм, повысить точность размеров отливок и уменьшить шероховатость поверхности, снизить объем механической обработки отливок. Литье в кокиль позволяет получать разнообразные отливки с толщиной стенок 3—100 мм и массой от 0,1 до 500 кг. Литье в кокиль применяют при изготовлении корпусов приборов, деталей двигателей внутреннего сгорания и других деталей из чугуна, стали и сплавов цветных металлов.
Литье под давлением является процессом получения отливок в металлических формах (пресс-формах), при котором заливка расплавленного металла в форму и формирование отливки осуществляются под давлением в условиях интенсивного отвода теплоты от залитого металла и от затвердевающей и охлаждающейся отливки к массивной металлической пресс-форме. Изготовляют отливки на специальных машинах для литья под давлением с холодной или горячей камерами прессования.
При изготовлении отливок на машинах с холодной горизонтальной камерой прессования (рис. 15, а) порцию расплавленного металла заливают в камеру прессования /. Пресс-форма состоит из подвижной 4 и неподвижной 3 полуформ, в которые металл подается плунжером 2. Полости в отливке получают металлическим стержнем 5. После затвердевания металла пресс-форма раскрывается, и отливка 7 удаляется из полости выталкивателями 6. Машины с холодной камерой прессования применяют для изготовления отливок из медных, алюминиевых, магниевых и цинковых сплавов массой до 45 кг. Давление плунжера на расплавленный металл составляет от 50 до 200 МПа.
В машинах с горячей камерой прессования (рис. 15, б) камера прессования 2 расположена в обогреваемом тигле / с расплавленным металлом. При верхнем положении плунжера 3 через отверстие 4 сплав заполняет камеру прессования. При движении плунжера вниз отверстия перекрываются, сплав под давлением от 10 до 30 МПа заполняет полость пресс-формы 5. После затвердевания отливки плунжер возвращается в исходное положение, остатки расплавленного металла из канала сливаются в камеру прессования, а отливка удаляется из пресс-формы выталкивателями 6. Такие машины используют при изготовлении отливок из свинцово-сурьмянистых, цинковых и алюминиевых сплавов массой от нескольких граммов до 25 кг.
Литье под давлением является высокомеханизированным процессом. Автоматизируют заливку расплавленного металла, очистку рабочих поверхностей пресс-формы, нанесение смазки и т. д. Литье под давлением позволяет получать отливки, максимально приближающиеся по форме, массе и размерам к готовой детали, дает возможность изготовлять сложные тонкостенные отливки с толщиной стенки от 0,8 до 0,6 мм и отверстиями диаметром до 1 мм. Литьем под давлением изготовляют корпуса приборов, декоративные изделия, детали двигателей легковых автомобилей и др. Недостатком этого способа является высокая стоимость пресс-форм, сложность их изготовления, ограниченный срок их службы, опасность появления трещин в отливках.
Сущность центробежного литья заключается в получении отливок из расплавленного металла во вращающихся формах. Формирование отливки осуществляется под действием центробежных сил на специальных машинах с горизонтальной или вертикальной осями вращения.
В машинах с горизонтальной осью вращения (рис. 16, а) расплавленный металл из ковша / заливают по специальному желобу 2 во вращающуюся форму 3 с частотой вращения от 200 до 1400 об/мин. Попадая на внутренние стенки формы, жидкий металл образует полую цилиндрическую отливку 4, которую после затвердевания извлекают из формы. На таких машинах получают детали и заготовки типа труб, втулок, гильз.
В машинах с вертикальной осью вращения (рис. 16, б) расплавленный металл из ковша 1 заливают во вращающуюся форму 2 с частотой вращения от 160 до 500 об/мин. Растекаясь по дну формы, металл увлекается центробежными силами и прижимается к боковой цилиндрической стенке, образуя вокруг нее кольцевой слои J. Форма вращается до полного затвердевания металла, после чего форму останавливают и из нее извлекают отливку. На таких машинах получают отливки небольшой высоты, но большого диаметра: кольца, венцы зубчатых колес и др. При вращении формы вокруг вертикальной оси внутренняя свободная поверхность расплавленного металла имеет форму параболоида вращения, что приводит к разностенности отливки но высоте. Это снижает возможность применения таких машин. При центробежном литье исключаются затраты на изготовление стержней, уменьшается расход металла на литниковую систему, улучшается заполняемость форм металлом и повышается плотность отливок по сравнению с литьем в песчаные формы.
а б
Рис. 16. Схемы изготовления отливок на центробежных машинах с осью вращения: а — горизонтальной; 6 – вертикальной
Контрольные вопросы
- Расскажите сущность процесса литьё по выплавляемым моделям.
- Какие материалы обычно отливаются под давления?
- Как определяется конструкция кокилей.
- Какие отливки обычно получают центробежным литьём.
{/spoilers}