Фрезерные станки. Исполнитель
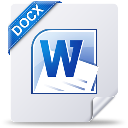
- Скачано: 46
- Размер: 652.5 Kb
Фрезерные станки.
План
- Назначение фрезерных станков.
- Горизонтально и вертикально фрезерные станки.
- Консольно-фрезерные станки.
- Делительные головки.
- Продольно фрезерные станки.
- Копировально-фрезерные станки.
- Шпоночно-фрезерные станки.
- Карусельно-фрезерные станки.
{spoiler=Подробнее}
Фрезерные станки предназначены для выполнения широкого круга операций. Они позволяют обрабатывать наружные и внутренние фасонные поверхности, прорезать прямые и винтовые канавки, фрезеровать зубья зубчатых колес и пр. Различают две основные группы фрезерных станков: универсальные (общего назначения) и специализированные. К первым относятся горизонтально – фрезерные, вертикально – фрезерные и продольно – фрезерные станки, ко вторым – шпоночно–фрезерные, шлице – фрезерные, карусельно – фрезерные и другие станки.
Горзонтальные-фрезерные станки
Горизонтально-фрезерные станки (рис.27) характеризуются горизонтальным расположением шпинделя. На фундаментальной плите 1 установлена станина 2, внутри которой размещен механизм главного движения с приводом от электродвигателя и коробка скоростей 3. В вертикальных направляющих станины смонтирована консоль 5, которая может перемещаться вертикально по направляющим станины. На горизонтальных направляющих консоли установлены поперечные салазки 6, на них – поворотная плита 7, а в направляющих последней – продольный (рабочий) стол 8. Таким образом, деталь, установленная на столе, в тисках или приспособлении, может получить подачу в трех направлениях. Наличие поворотной плиты позволяет поворачивать рабочий стол в горизонтальной плоскости и устанавливать его на требуемый угол. Некоторые горизонтально-фрезерные станки не имеют поворотной плиты. Такие станки называют простыми, в отличие от универсальных. Привод подач стола от отдельного электродвигателя и коробка подач 4 размещены внутри консоли 5.
На рис. 28. показана кинематическая схема широкоуниверсального горизонтально-фрезерного станка мод. 6Р82Ш. Привод главного движения электродвигатель 69 передает вращение шпинделю V следующими переключениями трехблочных зубчатых колес: от вала I колесами 1-2 на вал II, колесами7-8 или 5-6 или 3-4 на вал III; затем колесами 11-12 или 9-10 или 6-13 на вал IV и далее колесами 16-17 или 14-15 на шпиндель 5.
Рис.27. Горизонтально-фрезерный станок мод. 6Р82Ш.
Электродвигатель 63 с помощью передач 18-19, 20-21 вращает вал VIII, и далее через зубчатые колеса 22-23, 24-25 или 26-27, 27-28, 29-30 или же 31-32 вращение передается валу X. Отсюда движение на вал XI может быть передано через пару колес 33-34 (колесо 33 смещается вправо для сцепления с муфтой 75) или через перебор, состоящий из колес 35-36, 37-33 и 33-34 (при этом колесо 33 занимает положение, показанное на схеме). Широкое колесо 34 свободно насажено на вал XI и передает ему вращение при включении муфты 64. При включении дисковой фрикционной муфты 67 на вал XI может получить быстрое вращение, необходимое для осуществления ускоренных ходов. Цепь быстрого вращения приводится от электродвигателя 63 и состоит из группы передач 18-19, 19-52 и 52-53. Муфты 67 и 64 сблокированы: при включении первой муфты вторая выключается, и наоборот. Перемещения стола осуществляется с помощью винтовых механизмов: продольное-54-55, поперечное-56-57 и вертикальное-58-59. Гайка 55 закреплена в верхних салазках, гайка 57- в консоли, гайка 59-в тумбе 66.
Цепь продольной подачи соединяет вал XI с ходовым винтом 54 через передачи 38-39, 40-41-42, 43-44, 45-46 (на схеме стол повернут на 90º ). Цепь поперечной подачи состоит из зубчатых колес 38 – 39, 40 – 41 – 42 – 47. Цепь вертикальной подачи включает зубчатые колеса 38 – 39, 40 – 49 и 50 – 51. Для включения и выключения перемещений стола служат муфты 62, 65 и 70.
Станок оснащен шпиндельной головкой 96, смонтированной на выдвижном хоботе и имеющей привод от электродвигателя 75. Шпиндельная головка может поворачиваться под любым углом в двух взаимно перпендикулярных плоскостях. Она служит для обработки деталей, размеры которых превышают габарит стола.
Рис. 28. Кинематическая схема широкоуниверсального горизонтально-фрезерного станка мод. 6Р82Ш.
Вертикально-фрезерные станки
Вертикально-фрезерные станки отличаются от горизонтально-фрезерных вертикальным расположением оси шпинделя и поэтому строятся обычно на одной базе с ними, имея много унифицированных деталей и узлов. Вертикально-фрезерный станок имеет свою конструкцию станины и шпиндельного узла, а в кинематической схеме привода, главного движения пару конических зубчатых колес, передающих вращение на шпиндель. Устройство консольного стола этого станка такое же, как у горизонтально-фрезерного, за исключением наличия поворотной плиты, которой у вертикально-фрезерных станков нет.
Существуют другие типы станков данной группы, у которых шпиндель смонтирован не в станине, а в специальной головке. Головка может поворачиваться в вертикальной плоскости. В этом случае ось шпинделя можно устанавливать под углом к плоскости рабочего стола. У некоторых станков головка вместе со шпинделем может перемещаться в вертикальной плоскости.
Продольно-фрезерные станки
Продольно-фрезерные станки (рис. 29) предназначены для обработки плоскостей крупногабаритных деталей. На станине 1 этих станков смонтированы две вертикальные стойки 2 и 3, скрепленные в некоторых станках поперечной балкой. На вертикальных направляющих стоек расположены фрезерные головки 4 и 5 с горизонтальной осью шпинделя и траверса (поперечина) 6. На направляющих траверсы установлены две фрезерные головки 7 и 8 с вертикальной осью шпинделя. Обрабатываемую деталь устанавливают на столе 9, который смонтирован на направляющих станины Главным движением в станке является вращение шпинделей. Каждая фрезерная головка имеет самостоятельный привод: электродвигатель и коробку скоростей. Шпиндели допускают смещение их вдоль оси и могут быть установлены под углом. Продольную подачу имеет стол 9, поперечную - головки 7 и 8, а вертикальную - головки 4 и. 5. Привод движений подач для всех головок один. Траверсу 6 устанавливают на требуемой высоте и зажимают. Во время работы она неподвижна.
Рис. 29. Продольно-фрезерные станки
Делительные головки
Универсальные делительные головки предназначены для периодического поворота обрабатываемой заготовки вокруг оси (деление) и для непрерывного ее вращения, согласованного с продольной подачей стола при нарезании винтовых канавок.
На рис. 30, а показана схема обработки детали с использованием делительной головки. Заготовка 1 (в данном случае зубчатое колесо) Установлено на оправке в центрах шпинделя делительной головки 2 и задней бабки 3. Модульной дисковой фрезе 8 сообщают вращение, а рабочему столу – продольную подачу, в результате чего будет обработана впадина между двумя соседними зубьями. Возвратив стол в исходное положение, заготовку поворачивают на угол, соответствующий шагу зубчатого колеса. Так продолжают работу до тех пор, пока не будут профрезерованы все впадины.
Рис. 30. Схема обработки детали в делительных головках
Поворот заготовки и ее фиксирование осуществляются делительной головкой. Внутри корпуса головки смонтирован шпиндель 4, который периодически поворачивают, вращая рукоятку 5. Положение рукоятки фиксируется делительным диском (лимбом) 6 с рядами отверстий, равномерно расположенных по концентрическим окружностям. В любое из этих отверстий может заходить различным количеством рядов и отверстий в каждом ряду. Одна из конструкций головки имеет двухсторонний диск, на каждой стороне которого расположено по 11 окружностей со следующими числами глухих отверстий: 24 – 25 – 28 – 30 – 34 – 37 – 38 – 39 – 41 – 42 – 43 и 46 – 49 – 51 – 53 – 57 – 58 – 59 – 62 – 66. Различают лимбовые и безлимбовые головки; первые получили наибольшее распространение. На рис. 31. показаны кинематические схемы лимбовых (рис.31, а–в) и безлимбовых (рис. 31, г) делительных головок. Вращение шпинделю передается от рукоятки 1 через группы зубчатых колес 3 – 6 и червячную передачу 7 – 8. положение рукоятки при повороте на необходимый угол фиксируется делительным диском 2. Передаточное отношение всех передач, кроме червячной и сменных колес, обычно равно единице.
Существуют три способа настройки Универсальных делительных голшовок: Для непосредственного, простого и дифференциального делений.
Непосредственное деление. На шпинделе делительной головки установлен диск, имеющий определенное число пазов на равных расстояниях друг от друга. Диск поворачивают рукояткой. При 12 пазах диска шпиндель головки можно повернуть на , , , и оборота, т. Е. делить окружность на 2, 3, 4, 6 и 12 частей. Таким образом, область использования непосредственного деления весьма ограничена.
Простое деление (рис. 31,а) применяют в тех случаях, когда передаточное отношение цепи между валом с рукояткой и шпинделем головки может быть выражено в виде простой дроби. Если z – Число равных частей, на которое необходимо произвести деление, то величина периодического вращения шпинделя головки составляет 1/z оборота. Для этого рукоятку 1 нужно повернуть относительно неподвижного диска 2 на npоборотов, т.е.
(13)
обозначая
и решая уравнение (13), найдем потребное число оборотов рукоятки
Величину N называют характеристикой головки. Чаще всего N=40. полученное значение np выражают в виде простой дроби:
(14)
где
В-число отверстий, на одной из окружностей делительного диска;
А-число отверстий, на которое нужно повернуть рукоятку.
При отсчете делений на диске пользуются раздвижным сектором 7 (см рис.30,а), состоящим из двух радиальных линеек. Их раздвигают на угол, соответствующий числу отверстий, отсчитываемому на диске, и скрепляют. Если левую линейку упереть в фиксатор рукоятки, то правая линейка окажется совмещенной с отверстием, в которое надо будет при очередном повороте ввести фиксатор. После фиксирования рукоятки в новом положении левую линейку снова упирают в фиксатор.
Дифференциальное деление применяют в тех случаях, когда подобрать диск с необходимым количеством отверстий способом простого деления не удается. Сущность дифференциального деления состоит в следующем. Подбирают фиктивное число частей zф , на которое необходимо произвести деление, близкое к заданному z и удовлетворяющее простому способу деления. Если выполнить простое деление, то шпиндель повернется на 1/zф оборота вместо 1/z. Для компенсации полученной разницы шпинделю сообщают дополнительный поворот, равный 1/z-1/zф. если эта разность будет положительна, то дополнительный поворот делают в ту же сторону, что и основной; если разница отрицательна, то поворот делают в противоположную сторону.
Таким образом, рукоятка 1 должна совершить основной поворот, чтобы разделить окружность на zф частей, и дополнительный, чтобы компенсировать указанную выше разницу. Это достигается путем медленного поворота диска 2 на величину дополнительного поворота рукоятки. Когда последняя будет повернута на угол, соответствующий заданному числу отверстий, отверстие, в которое должен быть введен фиксатор вместе с диском 2, уйдет вперед или назад. Поэтому для того чтобы ввести фиксатор в отверстие, необходимо рукоятку дополнительно повернуть в ту или другую сторону до совпадения оси фиксатор с осью отверстия. Вращение диску передается от шпинделя делительной головки через сменные колеса а-b, c-d, коническую пару 9-10 и зубчатые колеса 3-4.
Расчет настройки сводится к определению передаточного отношения сменных зубчатых колес a-b, c-d. Чтобы повернуть шпиндель на 1/z и 1/zф оборота, нужно согласно уравнению (14) повернуть рукоятку на np=N/z оборота при заданном числе делений и на оборота при фиктивном числе делений.
Рис. 31. Кинематические схемы универсальных делительных головок
Величина дополнительного вращения рукоятки равна величине поворота диска:
np доп. = - (15)
За время деления шпиндель делительной головки повернется на 1/z оборота и, следовательно, сообщит диску
оборота. (16)
Приравнивая выражения (15) и (16), получим
np. доп = N ( - ) =
Обозначая через С (обычно С = 1) и решая данное уравнение, после преобразований получим
= .
Пример. Определить параметры настройки делительной головки для фрезерования зубьев цилиндрического колеса с z = 69. Пусть характеристика головки N = 40 и
с = 1; Примем zф = 70. Тогда число оборотов рукоятки
nф = = .
Необходимо взять диск с 28 отверстиями и поворачивать рукоятку при делении на 16 отверстий. Передаточное отношение сменных колес согласно уравнению (17) будет
= = .
Фрезерование винтовых канавок, расположенных равномерно по окружности, осуществляется следующим образом (см. рис. 30, б). Заготовку 1, установленную в центрах делительной головки 2 и задней бабки 3, вместе со столом 9 поворачивают на угол β, равный углу наклона винтовой линии канавки. В результате этого средняя плоскость дисковой фрезы 8 совпадает с направлением канавки. Заготовке сообщают непрерывное вращение, а столу – продольную подачу вдоль линии ab.
Шпиндель делительной головки вращают от ходового винта продольной под ачи стола (см. рис. 38, в ) по цепи сменных зубчатых колес а1 – b1 , c1 – d1 , далее через пары 9 – 10, 3 – 4 и диск 2 на рукоятку 1, передачи 5 – 6 и 7 – 8. за один оборот шпинделя стол должен переместиться на величину шага винтовой линии канавки tp
Уравнение кинематического баланса на основании равенства (7) примет вид
1 об. заг. tв = tр,
где tв – шаг ходового винта.
Учитывая, что
= ,
получим уравнение настройки кинематической цепи
= N .
В практике винтовую линию канавки задают не шагом tp, а углом наклона β (или углом подъема винтовой линии φ = 90º - β) и диаметром d. В этом случае шаг
t p = πd/tgβ.
Шпоночно-фрезерные станки
Шпоночно-фрезерные станки предназначены для фрезерования шпоночных пазов. Схема обработки паза представлена на рис. 32. Диаметр D пальцевой фрезы подбирают по ширине В шпоночного паза. Фреза получает вращательное главное движение, прямолинейную подачу вдоль оси паза и вертикальную подачу в конце хода.
На рис. 33 показан вертикальный одношпиндельный шпоночно-фрезерный станок. На основании 1 размещены станина 2 и ее головка 3. На прямоугольных направляющих 4 головки смонтирована шпиндельная каретка 5, получающая от гидропривода продольное перемещение. На вертикальных направляющих 6 станины смонтирована консоль 7 со столом 8. Стол, на котором закрепляется обрабатываемая деталь, кроме вертикальных имеет и поперечные движения от рукоятки 9. В конце каждого хода шпиндельной каретки шпиндель автоматически перемещается на глубину снимаемого за один проход слоя.
Станок работает по полуавтоматическому циклу. Гидрокинематическая схема станка изображена на рис. 34. Шпиндель 15 смонтирован внутри пинали 12 и вращается от двухскоростного электродвигателя 3 через трёхступенчатую клиноременную передачу 13 — 14, которая позволяет иметь три различные угловые скорости шпинделя.
Шпиндельная каретка перемещается от силового цилиндра продольной подачи, шток которого закреплен, на станине. Подача на глубину фрезерования в конце каждого хода производится от силового цилиндра 7 вертикальной подачи. Его поршень имеет два штока 7.1 и 7.2; шток 7.1 выполнен заодно с поршнем, шток 7.2 смонтирован на подшипниках и может вращаться. На шток 7.2 насажен червяк 8; при движении штока вправо червяк поворачивает червячное колесо 9 и зубчатое колесо 10, которое перемещает рейку 11, закрепленную на пиноли 12. Пиноль вместе со шпинделем получает вертикальную подачу. Положение, шпинделя по высоте можно регулировать вручную, вращая рукояткой червяк 8. Обычно это делают так. Поршень цилиндра вертикальной подачи упирают в правый торец крышки цилиндра и вращением червяка опускают пиноль и шпиндель с фрезой на полную глубину фрезеруемого шпоночного паза. Циклом обработки управляют с помощью гидропанели и реверсивного золотника. Масло нагнетается насосом 1 через фильтр 2, по трубопроводу 16 подается в гидропанель 6 и распределяется по системе.
Рис. 32. Схема обработки паза
Рис. 33. Вертикальный одношпиндельный шпоночно-фрезерный станок
Рис. 34. Гидрокинематическая схема шпоночно-фрезерного станка
Реверсивный золотник 4 состоит из трех частей: корпуса 4.1, реверсивного гидравлического золотника 4.2 и вспомогательного золотника 4.3. Последний предназначен для управления перемещением реверсивного золотника 4.2 и дозирующего золотника 6.3 гидропанели. Когда вспомогательный золотник находится в позиции, показанной на схеме, масло через отверстие 4.23, каналы 4.24 и 4.25 поступает в правую полость реверсивного золотника 4.2 и перемещает его влево. При смещении корпуса 4.1 относительно вспомогательного золотника 4.3, влево масло поступает из канала 4.31 через выточку 4.18 в левую полость реверсивного золотника и перемещает его вправо.
Для осуществления продольной подачи шпиндельной каретки необходимо направить масло из гидропанели 6 через дроссель 6.1 и по трубопроводу 21 в обе полости силового цилиндра 5 продольной подачи. В левую полость оно попадает через отверстия 4.23, 4.26 золотника 4.2 и трубопровод 25, а в правую - по трубопроводу 22. Вследствие неравенства площадей сторон поршня цилиндр вместе с кареткой перемещается влево. Масло, вытесняемое из правой полости, через отверстия 4.23, 4.26 и 4.27 золотника 4.2 переливается в левую. Движение цилиндра с кареткой влево будет происходить до тех пор, пока вспомогательный золотник 4.3 не встретит неподвижный левый упор и не остановится. Движущийся вместе с кареткой корпус 4.1 сместится влево. При этом он перекроет отверстие 4.27, а отверстие 4.32 соединит с каналом 4.33 и сливным баком. Благодаря этому левая полость цилиндра продольной подачи соединяется со сливом, в то время как в правую полость продолжает поступать масло. В результате цилиндр вместе со шпиндельной кареткой начнет перемещаться вправо до тех пор, пока вспомогательный золотник 4.3 не встретит правый неподвижный упор.
В конце каждого хода шпиндельной каретки должна осуществляться вертикальная подача шпинделя. Этого достигают выпуском порции масла из правой полости цилиндра 7 вертикальной подачи, в результате чего шток 7.2, смещаясь вправо, подает шпиндель вниз. Работа гидравлического привода происходит следующим образом. Масло из гидропанели 6 по каналу 6.34, через кран 6.2 и трубопровод 35 поступает в левую полость цилиндра и создает постоянное давление на поршень 7.1. Правая полость трубопроводами 36 и 6.37 связана с дозирующим золотником 6.3 и поршнем 6.4. При встрече с правым упором вспомогательный золотник 4.3 занимает положение, показанное на схеме. Масло по трубопроводу 17, 4.18 и 19 поступает в нижнюю полость дозирующего золотника 6.3. Одновременно на золотник действует давление масла со стороны канала 6.20, поэтому он займет верхнее положение, так как диаметр нижнего поршня больше. Масло из правой полости цилиндра вертикальной подачи по трубопроводу 36 через золотник 6.3 поступит в цилиндр дозатора и переместит поршень 6.4 до упора в винт. Последний регулирует величину хода поршня 6.4 и следовательно, дозу масла, выпускаемую из правой полости цилиндра.
При встрече золотника 4.3 с левым упором трубопровод 19 соединяется с отверстиями 4.30 и 4.29, и масло поступает на слив. Золотник 6.3 занимает нижнее положение. Из правой полости цилиндра выходит следующая порция масла, которая через отверстия 6.31 и 6.38 поступает в нижнюю полость дозатора и перемещает поршень 6.4 вверх.
Работа протекает до тех пор, пока поршень цилиндра вертикальной подачи не упрется в торец правой крышки цилиндра. Это, как было указано, способствует конечному положению фрезы на глубине шпоночного паза.
Возврат шпинделя в исходное положение осуществляется поворотом крана 6.2. Тогда масло по каналам 6.34, 6.39 и 6.37 и трубопроводу 36 поступает в правую полость цилиндра вертикальной подачи, перемещая шток 7.2 влево. Из левой полости масло подается на слив через кран 6.2.
Для прекращения действия гидропередачи при работающем насосе стержень жесткого упора (например, правого) вывертывают. Реверсирования при этом не происходит, и каретка останавливается. Все поступающее от насоса масло сбрасывается через переливной клапан. При ввертывании стержня упора золотник 43 перемещается внутри корпуса и возобновляет движение всей системы.
Конструкция шпиндельной каретки позволяет создавать различные компоновки многошпиндельных шпоночно-фрезерных станков, способных одновременно обрабатывать несколько шпоночных пазов одного вала.
Карусельно – фрезерные станки
Карусельно – фрезерные станки предназначены для обработки плоскостей литых, кованных и штампованных деталей по методу непрерывного торцового фрезерования.
На рис. 35 показан карусельно – фрезерный двухшпиндельный станок. На станине 1 установлена стойка 2, в вертикальных направляющих которой смонтирована шпиндельная бабка 3. Бабка имеет два шпинделя 4 с приводом вращения от коробки скоростей 5, помещенной в верхней части стойки. На горизонтальных направляющих станины смонтирован стол 6, получающий во время работы медленное вращение в виде круговой подачи. Такая компоновка узлов станка позволяет вести фрезерование непрерывно. Обработанные детали, выйдя из зоны резания, могут быть заменены заготовками. Наличие двух шпинделей дает возможность совместить в одной операции черновое и чистовое фрезерование.
Рис. 35. Карусельно – фрезерный станок
Привод главного движения осуществляется от электродвигателя 27, расположенного в верхней части стойки, через систему зубчатых передач 1 – 2, 3 – 4 и 5 – 6 и гитару скоростей а1 - b1 (рис. 36)
Вертикальный вал I проходит внутри шлицевой втулки с насаженными на ней косозубыми колесами 7 и 9. Первое связано с колесом 8 чернового шпинделя II, второе – с колесом 10 чистового шпинделя III. Шпиндели смонтированы в гильзах 12, которые с помощью реечных передач 11 могут устанавливаться на необходимую высоту. Вращением рукоятки 26 шпиндельную бабку перемещают вертикально.
Частота вращения чистового шпинделя примерно в 1,8 раза больше, чем чернового.
Привод круговой подачи стола состоит из отдельного электродвигателя 28 и цепи зубчатых передач 13 … 24 со звеном настройки а/b. Подача выключается выводом из зацепления зубчатых колес 19 и 20. Ручной поворот стола производится при помощи червяка 25 при выключенной подаче.
Рис. 36 Кинематическая схема карусельно – фрезерного станок
Копировально-фрезерные станки.
Копировально-фрезерные станки предназначены для обработки разнообразных плоских профилей (изготовление кулачков, шаблонов, матриц и т.д.) и пространственно сложных поверхностей (объёмное фрезерование). По числу шпинделей станки делят на одношпиндельные и многошпиндельные, а по принципу действия на станки прямого и станки следящего действия. В копировальных станках прямого действия всякое изменение формы задающего устройства (шаблона и копира) производит непосредственное воздействие на копировальный ролик или палец, связанный жёстко с фрезой. В станках следящего действия посредством копировального ролика или пальца воспринимается всякое изменение формы задающего копира и передаётся фрезер через усилительное устройство. Фрезерование производят про помощи ощупывания модели копировальным пальцем двумя способами: способом горизонтальных строчек и способом вертикальных строчек.
При первом способе (рис 37, а) стол станка совершает автоматическое задающее горизонтальное перемещение, а фрезерная головка непрерывное следящее продольное и периодическое вертикальное перемещение на величину строки. При втором способе (рис 37, б) фрезерная головка совершает задающее вертикальное и следящее продольное перемещение, а стол периодическое горизонтальное перемещение на величину s. Палец следящего устройства касается модели и автоматически дает команду (импульсы) приводам для одновременного перемещения фрезы по обрабатываемой детали и пальца по рельефу копируемой модели, поскольку и следящий палец и фреза смонтированы на общем корпусе фрезерной головки.
Рис.37. Способы ощупывания модели | Рис. 38. Схема работы следящего пальца |
Схема работы следящего пальца показана на рис 38. палец 1 касается поверхности (рельефа) модели А под определенным давлением; в случае изменения этого давления палец может иметь осевое перемещение, которое через шарик передается его тыльной частью втулке 2, а последняя через пружину касается острия регулировочного винта. Таким образом, осевые перемещения пальца управляются в зависимости от давления на палец. Указанные осевые перемещения через подвешенный на пружине 4 груз 3, соединенный со втулкой 2, передаются к сердечнику 5 трансформатора. Сердечник подвешен на конце указанных грузов, его перемещение в магнитном поле трансформатора изменяет электромагнитные импульсы, которые направляются в усилительное устройства, а затем поступают в цепи управления электродвигателями подач.
Рис. 39. Горизонтальный копировально-фрезерный полуавтомат
На рис. 39 представлен горизонтальный копировально-фрезерный полуавтомат, предназначенный для объемного фрезерования деталей по моделям, выполненным в натуральную величину. Кинематика станка обеспечивает следующие движения детали и фрезы относительно друг друга: главное движение – вращение фрезы 5, вертикальное и поперечное перемещение шпиндельного блока 4 по стойке 2, продольное перемещение стола 6 по станине 1 совместно с кронштейном 3, на котором установлена обрабатываемая модель.
Цепь главного вращательного движения фрезы (рис. 40) начинается от электродвигателя 32 через ременную передачу, зубчатые колеса 1–2 или 3–4 или 5– 6 колеса 7-9 -8 или 7–9–10 и заканчивается шпинделем. Поскольку электродвигатель двухскоростной, то на шпинделе станка можно получить 12 различных скоростей.
Цепь вертикального перемещения шпиндельного блока 4 берет начало от электродвигателя постоянного тока, затем через зубчатые передачи 17-18, 19-20, 22-21, и заканчивается винтом 29. поперечное перемещение шпиндельного блока осуществляется от электродвигателя постоянного тока 35 и через зубчатые колеса 11-12, 13-14, 15-16 передается на винт 30.
Продольное перемещение стола 6 осуществляется от самостоятельного электродвигателя постоянного тока 34 и через зубчатые колеса 23-24, 25-26, 27-28, передается на винт 31.
Рис. 40. Кинематическая схема электрокопировального фрезерного полуавтомата мод. 6Б443Г
Сравнительно небольшое количество моделей фрезерных станков вполне удовлетворяет промышленность. Консольно-горизонтально-фрезерные, универсальные и вертикально-фрезерные станки имеют унифицированные столы размером 160х320, 200х800, 250х1000, 320х1250, 400х1600мм. Одностоечные станки строят с размером стола от 500х1250 до 1600х5000мм, а в двухстоечном исполнении – от 400х1250 до 2500х8000мм. Копировально-фрезерные станки выпускают в ограниченном количестве, с размером стола 200х320, 320х1250, 630х1250мм.
{/spoilers}