Резьбонарезные станки Исполнитель
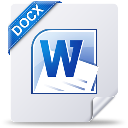
- Скачано: 79
- Размер: 300 Kb
Резьбонарезные станки
План
- Резьбонарезные станки
- Резьбофрезерные станки
- Резьбонакатные станки.
{spoiler=Подробнее}
Резьбонарезные станки
Для нарезания резьбы применяют различные способы, из которых наиболее распространенными являются нарезание на токарных станках резцами, гребенками. Метчиками, плашками и резьбонарезными головками, дисковыми и групповыми резьбовыми фрезами, одно- и многониточными шлифовальными кругами, а также накатывание роликами или плашками.
Сущность резьбофрезерования заключается в следующем (рис. 23.1., а). Дисковой фрезе 1, имеющей профиль нарезаемой резьбы, сообщают вращение вокруг ее оси (главное движение). Одновременно с этим осуществляют движение подачи, состоящее из медленного вращения детали 2 (круговая подача) и продольного перемещения ее или фрезы вдоль оси. Последнее равно величине шага нарезаемой резьбы за время одного оборота детали. В начале процесса обработки фрезе или заготовке сообщают дополнительно и поперечную подачу для врезания инструмента на полную глубину резьбы.
Рис. 23.1. Схемы резьбофрезерования
Резьбофрезерование выполняется с помощью дисковых, гребенчатых, червячных и пальцевых фрез. Для нарезания резьбы с большим шагом применяют дисковые фрезы (рис. 23.1., а), а для коротких и мелких резьб большого диаметра – гребенчатые фрезы (рис. 23.1., б).
Гребенчатая фреза представляет собой как бы набор дисковых фрез, поэтому процесс фрезерования значительно ускоряется, так как витки по всей длине резьбы обрабатываются одновременно. За один оборот заготовки конец канавки, нарезанный одним из резьбовых дисков фрезы, совпадает с началом канавки, нарезанной следующим диском. Таким образом, резьба фрезеруется за один оборот заготовки. Однако, имея в виду процесс врезания фрезы во время вращения детали, практически для получения полной резьбы детали необходимо совершить более одного оборота. Обычно этот цикл заканчивается за 1,2 – 1,4 оборота детали, в зависимости от конструкции станка. Минимальная длина фрезы должна быть на 2-3 шага больше фрезеруемой резьбы.
Ось гребенчатой фрезы располагается параллельно оси детали, что приводит к некоторому искажению профиля резьбы. Величина искажения тем больше, чем больше шаг резьбы, диаметр фрезы и чем меньше диаметр резьбы. Однако при нарезании обычных треугольных резьб, имеющих небольшой наклон витков винтовой линии, такое искажение не является существенным.
Гребенчатыми фрезами можно фрезеровать как наружные (рис. 23.1., б), так и внутренние (рис. 23.1., в) резьбы. В первом случае фрезе и детали сообщают вращение в одну сторону, во втором случае – в разные стороны.
1. Резьбофрезерный полуавтомат мод. 5Б63
для фрезерования резьб.
В условиях крупносерийного и массового производства применяется резьбофрезерный полуавтомат мод. 5Б63 он предназначен для фрезерования коротких наружных и внутренних резьб резьбовыми гребенчатыми фрезами. Станок работает по полуавтоматическому циклу. Рабочий, обслуживающий станок, производит лишь закрепление детали, пуск станка и смену детали.
Цикл обработки следующий: закрепление детали; пуск станка нажатием кнопки, быстрое продольное движение каретки с фрезой по направлению к изделию; медленное продольное движение каретки по направлению к изделию при подходе упора каретки к копиру продольного перемещения; продольное перемещение каретки на шаг нарезаемой резьбы (копиром продольного перемещения); одновременное врезание фрезы в изделие на глубину резьбы (копиром поперечного перемещения); отвод фрезы от изделия; быстрое перемещение каретки в исходное положение и остановка.
Управление нарезанием резьбы осуществляется при помощи двух копиров, кинематически связанных и управляющих продольным перемещением каретки на величину шага и одновременным поперечным перемещением ее на глубину резьбы. Копир 42 продольного перемещения каретки (рис. 23.2) расположен в корпусе шпиндельной бабки 44 и получает движение от шпинделя изделия с передаточным отношением 1,31 (один оборот копира соответствует 1,31 оборотам шпинделя). Цикл обработки, включающий подвод и врезание фрезы в изделие, фрезерование на полную глубину и перемещение на шаг резьбы, зачистку резьбы и вывод фрезы и резьбы, совершается за один оборот копиров. Копир 43 поперечного перемещения фрезерной головки вращается с угловой скоростью, равной скорости продольного копира.
Шпиндельная бабка изделия 44 жестко крепится на станине. Шпиндель, установленный на подшипниках скольжения, приводится во вращение от электродвигателя 47 через клиноременную передачу 1-2 и коробку скоростей со сменными шестернями a-b, c-d, которая обеспечивает 16 частот вращения шпинделя в пределах 0.5-16 об/мин. Передаточное отношение зубчатых колес 9-11, 12-13 на вал VI на котором находится сменный копир 42 для каждого шага резьбы, составляет 1,31. Для обеспечения остановки копира 42 в положении, соответствующем начала цикла, вал VI копира отключается от приведенной цепи при помощи муфты зубчатым колесом 14.
Рис. 23.2. Кинематическая схема полуавтомата мод. 5Б63
Фрезерная головка 45 устанавливается на салазках каретки 46 и может занимать по отношению к ней такое положение, при котором ось шпинделя либо параллельна оси шпиндельной бабки изделия (при нарезании цилиндрических резьб), либо будет образовывать с осью последний угол 30030’ (при нарезании конических резьб). Вместе с салазками фрезерная головка может перемещаться в поперечном направлении для врезания на глубину резьбы.
На корпусе фрезерной головки размещается электродвигатель 48, от которого через клиноременную передачу 21-22, сменные колеса a’-b’ c’-d’ и колеса 25-26-27 движение передается шпинделю фрезы, которой вращается с частотой 160-2500 об/мин.
Каретка 46 фрезерной головки имеет продольное и поперечное перемещения. Продольное перемещение каретки может быть быстрым при подводе к копиру 42, замедленным в момент соприкосновения с копиром и рабочим при нарезания резьбы. Продольное перемещения при подводе каретки осуществляется винтом 50, получающим вращение от механизма быстрых перемещений по цепи: электродвигатель 49, муфта 52, зубчатые колеса 32-35, 36-38 (при включенной муфте 52) на винт. В конце быстрого подвода каретки к копиру выключается муфта 53, чем обеспечивается медленное перемещение каретки по цепи колес 28-31, 34-35 и 36-38 на винт 50. Плавающая гайка винта связана с кареткой через пружину 39, которая служит для каретки к копиру 42 в процессе нарезания резьбы, т. Е. обеспечивает перемещение каретки на шаг нарезаемой резьбы при неподвижном винте 50. В конце подвода каретки переключением электромагнитных муфт 52-53 включается замедленная передача через зубчатые колеса 28-29, 30-31, муфту 53 и колеса 34-, 36-38 и винт 50.
Поперечное установочное перемещение каретки фрезерной головки осуществляется вручную маховиком 40 через передачи 19-20 и винтовую пару 51. рабочее перемещение осуществляется от копира 43 поперечного перемещения, который связан жесткой кинематической цепью зубчатых колес 18-17, валом VII и колесами 16-15-14-13 с копиром продольного перемещения 42. Копир 43 поперечного перемещения – открытого типа, сменный для определенного диапазона шагов резьб.
Резьбонакатные станки.
Для получения резьбы на деталях широкое распространение получили резьбонакатные станки. Эффективность замены нарезания резьбы ее накатыванием заключается в значительном повышении производительности процесса и качества резьбы. По виду накатного инструмента станки бывают с плоскими резьбовыми плашками (рис. 23.3., а), с круглыми резьбовыми роликами (рис. 23.3., б) и с круглым резьбовым роликом и дуговой плашкой (рис. 23.3., в).
Рис. 23.3. Способы накатки резьбы
Рассмотрим резьбонакатный станок мод. 5933, работающий круговыми роликами. Техническая характеристика станка: диаметр накатываемой резьбы 6-30 мм, наибольшая длина резьбы 40 мм, наибольший шаг резьбы 2,5 мм. Кинематическая схема станка обеспечивает следующие формообразующие движения (рис. 23.4.): вращение накатного ролика, сидящего в шпинделе I неподвижной бабки; вращение заготовки и ее перемещение в процессе накатывания.
Кинематическая цепь, передающая вращение накатному ролику, берет начало от электродвигателя 14 и идет через клиноременную передачу 1-2, сменные колеса гитары скоростей a-b, колеса 3-4, шпиндель I. Набором сменных колес a-b можно регулировать частоту вращения накатного ролика в пределах 39-256 об/мин. От шпинделя I неподвижной бабки через кулачковую муфту 13 приводятся во вращение колеса 5, 6, 7 и шпиндель II подвижной бабки. Скорость вращения шпинделя II такая же, как и шпинделя I. Поскольку подвижная бабка перемещается, связь между шпинделями осуществляется посредством шарнирного соединения рычагов 8 и 9.
Поперечное перемещение подвижной бабки осуществляется от кулачка 15, который вращается по следующей цепи: шпиндель II, сменные колеса a1-b1, червячная пара 10-11, кулачок. За один оборот кулачка 15 образуется резьба на поверхности детали, после чего станок выключается путем отключения муфты 12. Частота вращения кулачка устанавливается сменными колесами a1-b1 в зависимости от продолжительности накатывания резьбы.
Перед работой станка необходимо вершины резьб роликов сместить относительно друг друга на половину шага. Это достигается поворотом одного из шпинделей при выключенной муфте 13. Муфта имеет 100 зубьев, т. е. при повороте на один зуб вершины резьбы сместятся на величину 0,01 шага резьбы.
Рис.23.4. Кинематическая схема резьбонакатного станка мод. 5933
Контрольные вопросы
- Методы обработки резьбовых поверхностей?
- Резьбонарезные станки.
- Токарно-винторезные станки.
- Резьбофрезерные станки
- Резьбонакатные станки.
{/spoilers}