Основы программирование на станках с чпу Исполнитель
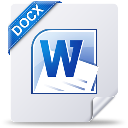
- Скачано: 30
- Размер: 308 Kb
Основы программирование на станках с чпу
План
- Числовая система программного управления
- Порядок подготовки программы
{spoiler=Подробнее}
Числовая система программного управления
Наиболее подробно станки с системой программного управления рассматриваются в специальном курсе. «Автоматизация производственных процессов».
Автоматизация технологического процесса механической обработки имеет место в условиях крупносерийного и массового производства, где применяются станки-автоматы, заменившие универсальные и специализированные станки. Автоматы управляются при помощи механических устройств, которые в условиях мелкосерийного и единичного производства нерентабельны- ввиду их сложной переналадки. Возникла необходимость в средствах автоматизации, которые позволяли бы производить частую переналадку станков при обработке деталей малых партий или отдельных деталей. Эта задача решается применением станков с электронными системами управления, которые называют станками с программным управлением.
Основным преимуществом таких станков является возможность их переналадки при переходе на обработку новой детали в весьма короткое время, при централизованной подготовке технологических программ. Программа позволяет проектировать системы дистанционного управления станками и создавать при этом легко переналаживаемые автоматические линии и участки комплексной обработки деталей. Если программа автоматического действия станка не имеет непосредственной связи с его структурой, кинематикой и конструкцией, или выражена в абстрактной форме при помощи кода (под которым понимается система символов, обусловливающая определенные действия, выраженные в виде цифр, букв, их комбинаций и т. д.), то такая система является принципиально отличной от применяемой на станках-автоматах и обладает большими потенциальными возможностями и эксплуатационными удобствами.
Рис. 27.1. Блок-схема ПУ
В качестве программоносителей служат перфокарты, перфоленты, магнитные ленты, а также штырьковые барабаны или панели, магазины переключателей и др. В обобщенном виде система программного управления представлена блок-схемой на рис. 27.1. Она имеет следующие элементы.
- -ввод программы. Назначение элемента считывать с программоносителя закодированные управляющие сигналы в виде электрических, магнитных, световых или других физических воздействий. Он включает в себя считывающее и транспортирующее программоноситель устройства, которые в зависимости от принятого метода записи программы различают по способу считывания: контактные и бесконтактные, непрерывные и периодического действия, последовательные и параллельные.
- -блок управления. Его назначение - преобразовывать соответствующие физические воздействия в электрические командные импульсы или потенциалы. Он также выполняет функции сопоставления задания с информацией датчика перемещений, расшифровывает введенную информацию и др. Элемент БУ является обобщающим понятием различных устройств программного управления: дешифратора, интерполятора, счетчика и др. в зависимости от принятой схемы реализации командных воздействий. Эти устройства предназначены для переработки управляющей информации и выполнения отдельных функций автоматического управления на основе использования электронных приборов.
- - усилитель. В случае необходимости он поднимает полученный, электрический потенциал до необходимого уровня, обеспечивающего надежное управляющее воздействие.
- -исполнительный орган. Реализует командные импульсы путем подключения рабочего органа станка к источнику движения или выполнения других функций автоматического управления. Элемент ИО обобщает различные сервомеханизмы, которыми обычно в станках являются контакторы, электромагниты, электромагнитные муфты, Шаговые двигатели, золотники и т.д.
- -рабочий орган. Фактически реализует командные воздействия, являясь целевым управляемым органом станка.
- - датчик перемещений. Его назначение - регистрировать фактическое перемещение рабочего органа станка. Наличие ДП определяет замкнутую систему программного управления, в отличие от более простой, открытой системы программного управления, у которой отсутствует этот элемент. Он обобщает различные системы путевого контроля, применяемые в замкнутых системах ЧПУ в качестве устройств обратной связи. На эти системы входят датчики, измеряющие величины фактического перемещения рабочего органа или положения управляемого объекта, и приборы формирования необходимого выходного сигнала.
Абсолютные датчики отражают непрерывное или дискретное изменение физического параметра контролируемого перемещения. Эти датчики могут быть со шкалой или без нее. Примером абсолютного датчика является реохорд, движок которого связан с рабочим органом.
Циклические датчики отражают повторяющиеся периодическое изменение физического параметра в пределах ограниченного участка пути. Примером может служить индуктивный датчик, схема которого приведена на. рис. 27.2. В показанном симметричном положении сердечника 2 относительно выступа линейки 1 тока в диагонали мостовой схемы (2 - 3) нет, ей стрелка прибора 4 будет стоять на нуле. При смещении сердечника в диагонали возникает ток, пропорциональный расстоянию между линиями симметрии; стрелка прибора 4 покажет его значение.
Рис. 27.2. Схема индуктивного датчика перемещений
Различают следующие виды программ много управления:
ПУ |
программное управление - управление станком по детерминированной программе;
|
ЦПУ | цикловое программное управление - управление циклами перемещений или режимами обработки по программе с заданием величин параметров на путевых переключателях или других измерительных преобразователях; |
NС(ЧПУ) |
числовое программное управление (numerical соntго1) - управление обработкой на станке по программе, заданной в алфавитно-цифровом коде;
|
HNC | разновидность устройства ЧПУ (Hand NC) с ручным заданием программы с пульта устройства (на клавишах, переключателях и т. п.); |
SNC |
разновидность устройства ЧПУ (Speicher NC, Memory NC), имеющая память для хранения всей управляющей программы;
|
CNC |
автономное управление, станком с ЧПУ (Computer numerical control) содержащее ЭВМ или процессор;
|
DNC | управление группой станков от общей ЭВМ (Direct numerical control), осуществляющей хранение программ и распределение их по запросам от устройств управления станков (у станков могут быть установлены устройства типов NC, SNC, CNC). |
Все многообразие структур устройств ЧПУ можно подразделить на две большие группы. К первой группе относятся устройства с постоянной структурой в которых осуществляется ввод кодированной программы на перфоленте или декодированной программы на магнитной ленте («Контур-2ПТ», Н22, «Контур-ЗП», «Размер-2М» и др.). Нашли также применение простые позиционные устройства ЧПУ с заданием программы, размещенным непосредственно у станка на штеккерных панелях. Созданы устройства с ручным вводом программы в электронную память с клавиатуры пульта (класса НNС).
Ко второй группе относятся устройства с переменной структурой. Их основные алгоритмы работы задаются программно и могут изменяться для различных применений. Эти устройства строятся на основе микро ЭВМ либо микропроцессоров (класса CNC). В устройствах классов CNC и SNC можно формировать нестандартные циклы обработки, что существенно упрощает подготовку и редактирование программы.
По виду движений исполнительных механизмов станка устройства ЧПУ подразделяются на позиционные, контурные (прямоугольные и криволинейные), комбинированные.
Позиционные устройства ЧПУ применяют для станков сверлильно-расточной группы. При позиционировании рабочий орган станка (например, координатный стол с деталью) перемещается в новую точку обработки.
В позиционных устройствах применяются абсолютные и неабсолютные датчики положения. В первом случае программа задается в абсолютных координатах, а работа заключается в сравнении показаний датчиков с координатами, задаваемыми программой. При этом применяется числовая индикация действительного положения рабочих органов. Такие устройства, работающие со ступенчатым или регулируемым приводом, называются устройствами сравнения; к ним относятся «Координата 0-68», «Координата Р-69», «Размер-2М». Во втором случае программа задается в абсолютных координатах (здесь возможна числовая индикация положения инструмента) или в приращениях.
Контурные прямоугольные устройства предназначены для обработки деталей с прямоугольными контурами (например, ступенчатых валов) на станках токарной и фрезерной групп. Траектория движения инструмента, задаваемая такими устройствами, состоит только из отрезков прямых, параллельных осям координат. Рабочие подачи осуществляются по всем координатам. При этом одновременно работает всегда одна координата при общем числе управляемых координат до пяти.
Контурные криволинейные устройства применяют в станках многих групп. Они обеспечивают формообразование при обработке за счет одновременного согласованного движения по нескольким управляемым координатам (более трех). Программа движения привода подач по отдельным координатам при контурной и объемной обработке рассчитывается исходя из заданной формы обрабатываемой детали и результирующей скорости движения, определяемой режимом резания.
Комбинированные устройства ЧПУ, отвечающие всем требованиям позиционных и контурных устройств, применяют в основном для управления многооперационными станками.
Цикловые устройства содержат в цифровом виде только информацию о цикле и режимах обработки, а величина перемещения рабочих органов - задается настройкой упоров, воздействующих на путевые переключатели. В обозначении моделей станков с программным управлением в конце шифра ставится буква Ф и после нее цифра. Например, 243ВФ4. Имеются следующие разновидности станков:
1. С числовым позиционным программным управлением (индекс Ф2);
2. С непрерывным программным управлением (индекс ФЗ);
3. Обрабатывающие центры с числовым позиционным программным управлением (индекс Ф4);
4. Обрабатывающие центры с числовым непрерывным программным управлением (индекс Ф5).
Указанные разновидности станков с ПУ могут оснащаться устройствами цифровой индикации, а также цифровой индикацией с преднабором (индекс Ф1).
Разрабатываются самонастраивающиеся (адаптивные) системы программного управления. В открытой системе имеется только один поток информации - от элемента «ввод программы» к рабочему органу; в замкнутой системе, кроме того, имеется дополнительная корректирующая информация по линии обратной связи о фактическом перемещении рабочего органа. В идеальном случае желательно также иметь информацию о факторах случайного характера, связанных с конкретным состоянием режущего инструмента, отклонениях физических свойств заготовки от заданных, температурных колебаний в процессе резания, а также о различных силовых и других воздействиях на систему СПИД. Система программной управления, в которой, помимо основного, имеется ряд дополнительных потоков информации, позволяющих корректировать процесс обработки с учетом маловероятных воздействий, называется самонастраивающейся. Точность обработки на станках с программным, управлением зависит от назначения и конструкции станка, а также от вида встроенной системы. Обычно регламентируется цена командного импульса или, в общем случае, дискретность программирования, Для токарных станков она находится в пределах 5 - 50 мкм (нижнее значение относится к поперечной подаче); для сверлильно-расточных станков по соблюдению координатных расстояний - в пределах 2-8 мкм (нижнее значение относится к координатно-расточным станкам) и по соблюдению глубины ступенчатой обработки - 200-250 мкм; для фрезерных станков по любой координате - в - пределах 20 - 25 мкм,
Порядок подготовки программы
Основным мероприятием при подготовке к работе станков с программным управлением является составление программ обработки конкретных деталей с записью на программоносителе размерной, технологической и вспомогательной информации применительно к заложенной на станке системе управления. Для общего представления о характере указанной работы рассмотрим пример процесса программирования и записи программы.
Сначала технолог определяет переходы обработки заготовки па станке, исходное положение режущего инструмента и последующее его относительное перемещение, режим обработки, порядок выполнения различных технологических воздействий и т. п. Полученные данные заносят в расчетный бланк технологической карты. Устанавливается положение точки 0 расчетных координат (рис. 29.3.), от которых начинает движение режущая кромка инструмента. Затем траектория относительного движения инструмента разбивается на отдельные участки, ограничиваемые так называемыми опорными точками а. На прямолинейных участках обрабатываемой детали эти точки обычно устанавливают на границах участков, если даже они не параллельны направляющим. На криволинейных участках, в зависимости от способа аппроксимации кривой и требуемой точности ее воспроизведения, опорные точки расставляют на небольших интервалах по кривой.
Между опорными точками информация о соответствующем взаимном перемещении рабочих органов станка определяется автоматически электронными устройствами — интерполяторами, которыми информация выдается, с унитарном коде. Интерполяторы могут быть встроены в систему станка или представлять собой самостоятельный агрегат. По сложности устройства и точности аппроксимации кривых различают линейные, линейно-круговые и линейно-параболические интерполяторы.
Рис. 27.3. Схема переходов на станках с ЧПУ
Затем положение каждой опорной точки устанавливается относительно расчетного начала координат программистом, и полученные данные заносятся в технологическую карту. Графы технологической карты и последовательность их заполнения должны отвечать установленному порядку кодирования программы.
После этого оператор переносит данные технологической карты при помощи перфоратора на ленту в установленном порядке записи каждого перехода. При этом программа автоматически кодируется. Если необходимо, то программу записывают на магнитную ленту, однако следует иметь представление о сложности этого процесса. Более просто запись произвести на перфоленту. В этом случае программу легко проконтролировать визуально или автоматически и внести исправления, пробивкой дополнительных отверстий или заклейкой ненужных, чего нельзя сделать на магнитной ленте.
Запись программы на современных станках осуществляется унитарным или двоично-десятичным кодом. При унитарном коде число выражается одним символом - единицей, поэтому, чтобы записать, например, число 7, нужно поставить подряд семь единиц. Такое выражение числа используется при записи программы на магнитных лентах в виде импульсов определенной цены.
При двоичном счислении применяют два символа выражения числа - 0 и 1, которые в электрических и электронных системах легко воспроизводятся в виде двух состояний соответствующих приборов: выключено - включено, обесточено - под током, размагничено - намагничено, а на перфоленте - отсутствием или наличием отверстия. В двоично-десятичном коде используются только четыре разряда двоичного счисления, которыми выражают десятичные числа в каждом отдельном разряде. Некоторые выражения десятичного числа одного разряда двоичным числом и различными его комбинациями, принятыми в системах программного управления, приведены в табл. 27.1.
Международной организацией по стандартизации ISO разработан и рекомендуется для применения в вычислительных машинах и устройствах обработки информации код ISO - 7 bit. Он является семизначным кодом и позволяет позицировать 128 символов (рис. 27.5.). Дорожкам 1д, 2д, 3д и 4д приписан двоичный код 1 - 2 - 4 - 8, что обеспечивает получение 16 кодовых обозначений (0 - 15).
Таблица 8
Выражение десятичною числа двоичным числом и его комбинациями
Система счисления | Коды | Система счисления | Коды | |||||
10x | 2x | EA (США) | ISO - 7 bit | 10x | 2x | EA (США) | ISO - 7 bit | |
0 | 0 | 100000 | 0000 | 5 | 101 | 010101 | 0101 | |
1 | 1 | 000001 | 0001 | 6 | 110 | 010110 | 0110 | |
2 | 10 | 000010 | 0010 | 7 | 111 | 000111 | 0111 | |
3 | 11 | 010011 | 0011 | 8 | 1000 | 001000 | 1000 | |
4 | 100 | 00100 | 0100 | 9 | 1001 | 011001 | 1001 |
Код рассчитан на восьмидорожечную перфоленту шириной 25,4 мм. Для кодирования информации используются семь дорожек, восьмая предназначена для контроля считывания информации и дополняет количество пробивок в строке до четного числа. Информация на строках перфорированной ленты располагается поперек, ее движения, а на дорожках ленты - вдоль ее движения. Каждый символ кода (адрес, цифры, знак или признак) располагается, в виде комбинации пробивок (перфораций) на одной строке ленты. Например, адрес X кодируется пробивками по 4д, 5д и 6д дорожкам, цифра 3 - пробивками по 1д, 2д, 5д и 6д дорожкам, знак «плюс» пробивками по 1д, 2д, 4д и 6д дорожкам и т. п. Дорожка - с/д с перфорациями предназначена для протяжки ленты в считывающем устройстве.
Рис. 27.4. Код ISO - 7 bit
Группа адресов, одновременно отрабатываемых системой, образует фразу (кадр). В одной фразе может быть произвольное количество неповторяющихся адресов, а сами кадры имеют переменную длину (различное количество строк).
Код ISO - 7 bit (рис. 27.4) имеет следующие адреса:
А - поворот вокруг оси X;
В - поворот вокруг оси Y;
С - поворот вокруг оси Z;
D и Е - поворот вокруг специальной оси;
F - скорость подачи;
G - режим работы системы;
H, J, I, К и L - резервы;
М - вспомогательные команды;
N - номер фразы (кадра);
О - резерв;
Р - третичное перемещение вдоль оси X;
Q - третичное перемещение вдоль оси Y;
R - третичное перемещение вдоль оси Z;
s - скорость главного движения;
Т - номер (код) инструмента;
U - вторичное перемещение вдоль оси X;
Y - вторичное перемещение вдоль оси Y;
W - вторичное перемещение вдоль оси Z;
X - перемещение вдоль оси X;
Y - перемещение вдоль оси Y;
Z - перемещение вдоль оси Z.
Служебные символы кода:
(+) и (-) - направления перемещения;
LF - конец фразы (кадра);
% - начало программы;
Del - забой (строка не читается).
Пример составления программы
Процесс подготовки программы разделяется на следующие этапы:
а) разработка операционного чертежа и чертежа заготовки;
б) технологическая проработка операции;
в) разработка схемы установки или схемы наладки;
г) построение циклограммы (схемы движения инструмента);
д) расчет приращений координат опорных точек;
е) буквенно-цифровая запись программы (программная карта);
ж) кодирование в двоично-десятичном коде на перфоленте;
з) проверка перфоленты,
На токарно-винторезном станке мод. 16К20ФЗС5 необходимо обработать деталь, указанную на рис. 27.5., а. В станке применяется устройство числового программного управления Н-22-1М. Оно обеспечивает линейную и круговую интерполяцию геометрической информации, заложенной в программе.
Согласно чертежу осуществляется технологическая проработка для получения информации о выборе инструмента, о последовательности переходов и проходов, о скоростях подачи суппорта и вращения шпинделя и о распределении технологических команд. Для указанной детали принята однорезцовая обработка. Схема движения инструмента относительно детали дана на циклограмме (рис. 27.5., б). Запись движений по всем отрезкам циклограммы сведена в табл. 27.2.
Распределение движения по кадрам Таблица 27.2.
На станке программоносителем является восьмидорожечная перфолента шириной 25,4 мм. Система кодирования ISO - 7 bit (ГОСТ 13052-74). Программа обработки детали составляется из определенного количества кадров информации. Кадр состоит из слов, слово - из адресной и числовой частей. Порядок записи слов в кадре дан в табл. 27.3. Рассмотрим обозначение кадровых комбинаций.
В начале кадра обозначается номер кадра буквой N. За буквой проставляется разрядность. Например, первый кадр - N 001. Затем буквой G обозначается подготовительная функция, определяющая режим работы
пульта ЧПУ. Разрядность ее состоит из двух цифр. Ниже дана расшифровка подготовительных функций для рассматриваемого станка.
G01 - линейное перемещение. Программируется при отработке нормальных размеров.
G10 - линейное перемещение. Программируется при отработке длинных размеров.
G11 - линейное перемещение. Программируется при отработке коротких размеров.
G02 - круговое перемещение по часовой стрелке. Программируется при отработке нормальных размеров.
G20 - круговое перемещение по часовой стрелке. Программируется при отработке длинных размеров.
G21 - круговое перемещение по часовой стрелке. Программируется при отработке коротких размеров.
G03 - круговое перемещение против часовой стрелки. Программируется при отработке нормальных размеров.
G30 - круговое перемещение против часовой стрелки. Программируется при отработке длинных размеров.
G31 - круговое перемещение против часовой стрелки.
G04 - останов на запрограммированную выдержку времени.
G25 - возврат в «О» станка.
G26 - работа в относительной системе координат (в приращениях).
G27 - работа в абсолютной системе координат.
G33 - нарезание резьбы.
G40 - отмена коррекции инструмента.
G58 - линейное смещение «0» детали.
Функции G25, G33, G58 автоматически предполагают использование длинных размеров.
После обозначения подготовительной функции записываются координаты конечной точки перемещения x и z с обязательным указанием знака перемещения «+» или «-». Цена импульса по координате z - 0,01 мм, по координате x - 0,005 мм. Например, необходимо по оси z переместить суппорт на 10 мм влево; тогда на кадре будет следующее обозначение:
|
Скорость подачи F задается пятью разрядами. Старший разряд после адреса - признак диапазона подач. «1» - диапазон рабочих подач от 1 до 1200 мм/мин; «2» — диапазон рабочих подач от 0,05 до 60 мм/мин; «7» — скорость быстрого хода. Остальные разряды обозначают величину подачи в мм/мин. Скорость быстрого хода по координате 2 — 4800 мм/мин, по координате х - 2400 мм/мин.
Рис 27.5. Обрабатываемая деталь и циклограмма движения инструмента
Состав кадра Таблица 27.3.
«%» - Начало программы. Предшествует первому кадру.
«/» - Пропуск кадра. Ставится перед кадром, который может быть пропущен при обработке программы. Пропуск кадра происходит только при нажатии клавиши «Пропуск кадра» на пульте ЧПУ.
Далее обозначаются технологические команды S, М, Т. Они имеют три разряда. Старший разряд после адреса принимает значения «0» или «1». При наличии «0» выполнение технологических команд начинается вместе с отработкой геометрической информации. При наличии «1» отработка следующего кадра начинается только после ответа от станка об исполнении технологической команды,
Выбор скорости определяет функция «S». При S000 - S099 выбор номера скорости происходит без выдачи сигнала от станка о выполнении команды. При S100 - S199 выбор номера скорости сопровождается обязательной выдачей сигнала от станка о выполнении команды.
Контрольные вопросы
- Числовая система программного управления.
- Порядок подготовки программы.
- Возможности станков с ЧПУ.
- Классификация систем СЧПУ.
{/spoilers}