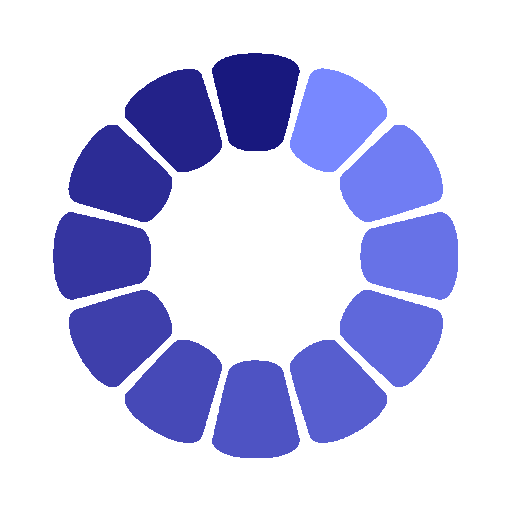
Ballarni quyidagi havolalar orqali stib olishingiz mumkin.
Точность обработки деталей
План:
- Понятия о точности. Основные факторы, влияющие на точность обработки.
- Погрешности обработки. Случайные и систематические погрешности.
- Точность при различных способах обработки.
{spoiler=Подробнее}
Ключевые слова по теме лекции::
Точность; экономическая точность; достижимая точность; неточность станков; геометрическая точность станка; геометрические погрешности станка; точность изготовления режущего и вспомагательного инструмента; погрешность приспособлений; метод пробных проходов; метод автоматического получения размера; погрешность базирования; погрешность закрепления; суммарная погрешность обработки ;
1. Понятия о точности. Основные факторы,
влияющие на точность обработки
При конструировании и проектировании машин необходимо наряду с расчётами кинематическими, расчётами на прочность, жесткость и износоустойчивость, проводить расчёты на точность.
Точность - основная характеристика деталей машин или приборов. Абсолютно точно изготовить деталь невозможно, так как при её обработке возникают погрешности, поэтому точность обработки бывает различной.
Точность детали, полученная в результате обработки, зависит от многих факторов и определяется:
а) отклонениями от геометрической формы детали или её отдельных элементов;
б) отклонениями действительных размеров от номинальных (заданных на чертеже);
в) отклонениями поверхностей и осей детали от точного взаимного расположения (например, отклонениями от параллельности, перпендикулярности, концентричности и др.).
Трудоёмкость и себестоимость обработки деталей в значительной мере зависят от требуемой точности - чем выше точность, предъявляемая к детали, тем выше стоимость обработки.
Точность обработки в производственных условиях зависит от многих факторов, поэтом обработку на станках ведут не с достижимой, а с так называемой экономической точностью.
Экономическая точность механической обработки - это такая точность, которая при минимальной себестоимости обработки достигается в нормальных производственных условиях, предусматривающих работу на исправных станках с применением необходимых приспособлений и инструментов при нормальной затрате времени и нормальной квалификации рабочих, соответствующей характеру работы.
Достижимая точность - это такая точность, которую можно достичь при обработке в особых, наиболее благоприятных условиях, необычных для данного производства, высококвалифицированными рабочими, при значительном увеличении затраты времени, не считаясь с себестоимостью обработки.
На точность обработки на металлорежущих станках влияют следующие основные факторы:
1. Неточность станка, являющаяся следствием неточности изготовления их основных деталей и узлов и неточности сборки, в частности - недопустимо больших зазоров в подшипниках или направляющих, износа трущихся поверхностей деталей и т.д.
2. Степень точности изготовления режущего и вспомагательного инструмента и его изнашивание во время работы.
3. Неточность установки инструмента и настройки станка на размер.
4. Погрешности базирования и установки обрабатываемой детали на станке или в приспособлении.
5. Деформация деталей станка, обрабатываемой детали и инструмента во время работы под влиянием силы резания вследствие недостаточной жесткости их и упругой системы станок - приспособление - инструмент - деталь (СПИД). (например, деформация детали при её закреплении для обработки).
6. Тепловые деформации обрабатываемой детали, деталей станка и режущего инструмента в процессе обработки и деформации, возникающие под влиянием внутренних напряжений в материале детали.
7.Погрешномти детали после обработки, которые может дать неправильные показания при измерениях.
8. Ошибки в измерениях вследствие неточности измерительного инструмента, неправильного пользованиия им, влияние температуры и т.п.
9. Ошибки исполнителя работы.
2. Погрешности обработки. Случайные и систематические погрешности
Рассмотрим некоторые из перечисленных выше факторов, влияющих на точность обработки.
Неточность станков. Точность станка в ненагруженном состоянии, называемая геометрической точностью станка, зависит главным образом от точности изготовлениия основных деталей и узлов станка и точности их сборки. Погрешности, допущенные в размерах и форме этих деталей и их взаимном расположении (плоскостность, цилиндричность, соосность и т.д.) называют иногода геометрическими погрешностями станка.
Величины этих погрешностей определяются испытаниями станка. Например, радиальное биение шпинделей токарных и фрезерных станков у конца шпинделя в ненагруженном состоянии допускается на более 0,01-0,015 мм. Погрешность прямолинейности и параллельности направляющих токарных и продольно строгальных станков на длине 1000мм допускается не более 0,02 мм и на всей длине не более 0,05-0,08 мм.
Степень точности изготовления режущего и вспомагательного инструмента, приспособления и их изнашивание во время работы. Степень точности изготовления режущего и вспомагательного инструмента оказывает большое влияние на точность механической обработки деталей. Инструмент, как и всякое другое изделие, не может быть изготовлен с абсолютно точными размерами, и некоторые погрешности при его изготовлении неизбежны. Эти погрешности часто в зависимости от вида инструмента переносятся в некоторой мере на обрабатываемую деталь. Поэтому чем точнее изготовлен инструмент, тем точнее и размеры детали, образуемые данным инструментом.
Расчёт погрешности, вызываемой размерным износом режущего инструмента. Износ режущего инструмента от пут резания характеризуется приработкой режущей кромки и размерным износом. Последний характеризуется удельным износом Ко за время пути резания в 1000м. Резания L в м при точении определяется по формуле
Где D-диаметр обрабатываемой поверхности в мм; l-длина обрабатываемой поверхности в мм; s - подача в мм/об.
Путь резания LN для партии заготовок N обрабатываемой в период между подналадками станка,
LN =LN
Путь для приработки режущей кромки принимают равным 1000 м, тогда полная длина пути резания для партии деталей
Принимая по нормативным данным величину удельного размерного износа К0* резца, определяют суммарный износ Ер по формуле
Погрешность приспособлений. Погрешность приспособлений возникает в результате неточности его изготовления и износа при эксплуатации. В общем случае погрешность изготовления приспособлений не должна превышать 1/3-1/5 доли допуска на соответствующий обрабатываемый размер детали.
Неточность обработки, зависящая от установки инструмента и настройки станка на размер. Установку инструмента на размер при обработке в единичном производстве на станках общего назначения выполняет рабочий, изготавливающий деталь. В серийном и массовом производстве детали обрабатывают на станках, настроенных на размер наладчиком.
В единичном производстве требуемый размер детали получается методом пробных проходов ( взятием пробнях стружек): после каждого прохода инструментом небольшого участка поверхности деталь измеряют и, если необходимый размер не получен, установку инструмента на нужный размер корректируют по делениям лимба или по показаниям индикатора. Так как при этом глубина резания на участке пробных проходов и на всей остальной части обрабатываемой поверхности может оказаться неодинаковой вследствии неровностей, возникает неточность обработки.
Более совершенным является метод автоматического получения требуемого размера. При работе по этому методу станки предварительно настраивают на заданный размер, т.е. рабочим звеньям станка, приспособлениия и инстрмента придаётся определённое взаимное положение, которое обеспечивает автоматическое получение требуемого размера обрабатываемой детали.
Погрешности установки и базирования заготовки на станке или в приспособлении. Погрешность установки является одной из величин, составляющих общую погрешность при выполнении заданного размера обрабатываемой детали.
Погрешность установки (eу) определяется суммой погрешности базирования (eб) и погрешности закрепления (eз).
Погрешность базирования возникает вследствие несовмещения установочной базой с измерительной. Эта погрешность определяется величиной колебания (т.е. разностью) предельных (наибольшего и наименьшего) расстояний измерительной базы от режущей кромки установленного на размер инструмента.
Погрешность закрепления возникает вследствие смещения заготовки под действием зажимной силы, прилагаемой для фиксации её положения. Смещение заготовки из положения, определяемого установочными элементами, а значит и смещение её измерительной базы происходят вследствие деформаций отдельных звеньев цепи, через которые передаётся сила зажатия. Смещения заготовки могут быть радиальные, осевые и угловые. Погрешность закрепления равна разности между предельными (наибольшей и наименьшей) величинами смещения измерительной базы по направлению выполняемого размера.
При обработке плоских поверхностей можно принять, что векторы погрешностей базирования и закрепления направлены в одну сторону; в этом случае погрешность установки определяется по формуле
eу=eб + eз
При обработке поверхностей тел вращения, векторы погрешностей базирования и закрепления могут иметь взаимное распоожение под разными углами. В этом случае погрешность установки определяется по формуле
При совмещении установочной базы с измерительной, погрешность базирвоания равна нулю (eб = 0), поэтому следует, если возможно, принимать в качестве установочной базы поверхность, которая является в то же время измерительной базой (правило совмещения баз).
Рассмотрим пример. На рис.4 показана схема установки на плоскую поверхность. Погрешность базирования по отношению к размеру L равна нулю (eб=0), так как базы измерительная и установочная совмещены (А-А). Погрешность базирования по отношению к размеру К имеет место, так как установочная (А-А) и измерительная (В-В) базы не совмещены; погрешность базирования в этом случае равна допуску d на размер Н заготовки: eбК = Тз.
При установке детали базовым отверстием на цилиндрическую поверхность (палец) (рис.5) следует учитывать смещение измериельной базы в направлении выдерживаемого размера. При посадке на разжимной палец, т.е. без зазора, погрешность базирования по отношению к размеру L выражается величиной половины допуска Т на диаметр D заготовки: eб = Т/2.
При посадке на жесткий палец с зазором погрешность базирования будет больше на величину предельного колебания диаметрального зазора Dз и в этом случае выразится величиной
eб = Т/2 + Dз
Рис. 4. Схема установки Рис.5. Схема установки детали
детали на плоскую поверхность. на цилиндричекую поверхность.
При обработке деталей на металлорежущих станках силы резания, зажатия и другие воздействуют на детали станка, обрабатываемую деталь и режущий инструмент, вследствие чего происходит их деформация, изменение величины стыковых зазоров, изменение положения режущей кромки инструмента относительно обрабатываемой детали. Поэтому размеры обрабатываемой детали изменяются, появляются отклонения от правильной геометрической формы (конусность, овальность и т.п.).
Рис.6. Возможные отклонения от правильной цилиндрической формы вала в результате деформации, возникающей при обработке.
На рис.6. показаны возможные виды отклонений от правильной геометрической формы вала вследствие влияния деформации, возникающей при обработке.
Большое значение для точности оработки деталей на металлорежущих станках имеет жесткость упругой системы СПИД.
Жесткость упругой системы - способность системы оказывать сопротивление действию сил, стремящихся её деформировать.
Жесткость упругой системы СПИД выражается соотношением
jc = Py/y [кГ/мм];
где jc - жесткость системы в кГ/мм; Py - радиальная составляющая силы резания в кГ; у - смещение режущей кромки инструмента (деформация упругой системы) в мм.
Величина, обратная жесткости, называется податливостью упругой ссистемы (w)
w = 1/ jc [мм/кГ]
На точность обработки детали в значительной мере влияют силы, действующие при её закреплении. Эти силы деформируют обрабатываемую деталь, в частности - её поверхностные слои, которыми деталь сопрягается с поверхностями станка, или приспособления при установке для обработки.
На рис.7а изоброжено кольцо (или втулка), деформированное силой зажатия в трёхкулачковом патроне; после растачивания в патроне отверстие приобрело правильную форму окружности (рис.7б); после освобождения детали из трёхкулачкового патрона наружная поверхность её принимает первоначальную форму окружности, а форма расточенного отверстия становится неправильной, искажённой (рис.7в).
Рис.7. Деформации кольца (втулки) при
закреплении в трёхкулачковом патроне.
На точность механической обработки деталей при выполнении окончательных операций существенно влияют температурные деформации обрабатываемой детали и деталей станка, вызываемые их нагревом.
Тепловые деформации происходят по следующим причинам: 1) нагрева теплом, выделяющимся при резании металла; 2) нагрева теплом, образующимся при трении движущихся частей станка; 3) непостоянства температуры помещения, вследствие чего происходят неравномерный нагрев или охлаждение системы СПИД.
Особое влияние тепловые деформации оказывают на точность обработки деталей по IT5 - IT6 квалитетам точности.
При обработке с охлаждением детали и инструмента смазывающе-охлаждающей жидкостью тепловые деформации системы СПИД значительно уменьшаются.
Качество поверхности детали после обработки может существенно влиять на точность показаний при измерении. Если поверхность детали после обработки имеет большую шероховатость, то при контроле размера детали измерение производят по вершинам или впадинам неровностей, что не дает правильного, определённого представления о размере. Поэтому, чтобы достичь заданной точности размеров детали и установить при контроле, действительно ли получен заданный размер, необходимо обеспечить при обработке надлежащий класс шероховатости поверхности.
Как видно из изложенного, погрешностей, возникающих в процессе обработки и дающих в результате неточные размеры и искажения формы детали, много. Происхождение этих погрешностей, их характер и направленность разные: одни погрешности дают увеличение размеров (плюс), другие - уменьшение размеров (минус), одни - компенсируют ("гасят") другие и таким образом уменьшают погрешность, другие, наоборот, накладываются, накапливают и увеличивают общую погрешность. Некоторые погрешности приводят к искажению формы детали.
Если каждому из вышеперечисленных видов погрешностей придать буквенное обозначение, то суммарную погрешность, можно выразить как алгебраическую сумму отдельных видов погрешностей:
Då = aст+bин+gн.с+eу+iд.с+rд.з+lт.д+wк+yисп+Xост ,
где aст - неточность станка; bин - неточность изготовления режущего и вспомагательного инструмента, его изнашивание во время работы и неточность приспособления; gн.с - неточность обработки: зависящая от установки инструмента и настройки станка на размер; eу - погрешность установки детали на станке или в приспособлении; iд.с- деформация деталей станка, обрабатываемой детали и инструмента; rд.з- деформация детали, возникающая при её закреплении для обработки; lт.д - тепловые деформации и внутренние напряжения; wк - неточность измерения вследствие влияния качества поверхности; yисп - ошибки исполнителя работы; Xост - остальные, неучтённые погрешности.
Неточность обработки поверхности детали является следствием влияния ряда факторов. Некоторые из этих факторов создают систематические погрешности, которые имеют постоянный или переменный характер.
Если, например, отверстия у деталей всей партии обработаны развёрткой, имеющей неправильный размер, то погрешность в размере, полученном при обработке этой развёрткой, является систематической, имеющей постоянный характер.
Так как развёртка в процессе работы изнашивается и вследствие этого диаметр её уменьшается, то и диаметр отверстия у поочередно обрабатываемых деталей также будет уменьшаться. Эта погрешность тоже является систематической, но имеющей переменный характер.
Систематические погрешности, как постоянные, так и переменные, подчиняются определённой закономерности. Систематическими являются, например, погрешности, происходящие вследствие неточности станка, инструмента, приспособления, деформации детали, станка и инструмента во время обработки от действующих сил или нагрева и т.п.
Некоторые из факторов, влияющих на точность обработки, создают случайные погрешности.
Случайные погрешности имеют различное значение для отдельных деталей одной и той же партии. Эти погрешности вызываются случайными причинами или действиями многих факторов, влияние которых на процесс обработки имеет случайный характер. Например, случайные погрешности возникают вследствие неоднородности и неодинаковой твёрдости обрабатываемого материала, колебания величины припуска и т.д. Благодоря случайным погрешностям размеры деталей в партии получаются различными, с колебаниями размеров в пределах допуска. Часть деталей будет иметь размеры, близкие к верхнему пределу допуска, часть – близкие к нижнему пределу допуска и часть – в середине поля допуска.
Для выявления закономерности погрешностей, возникающих при обработке, пользуются методом математической статистики.
3. Точность при различных способах обработки
Необходимая точность обработки, отвечающая требованиям заданного квалитета точности, достигается на различных станках разными способами.
Точность обработки отверстия по IT7 квалитету достигается чистовым развёртыванием, протягиванием, шлифованием, притиркой, доводкой абразивными головками (хонингование), суперфинишем. Этими же способами можно получить точность IT6 квалитета, но при более тщательной работе на хорошо выверенных и вполне исправных, неизношенных станках.
Точность обработки отверстия по IT9 и IT10 квалитету достигается чистовым развёртыванием; такую же точность можно получить и чистовым резцом на вполне исправных станках и при тщательной работе; экономичнее этот квалитет точности достигается шлифованием.
Точность обработки отверстия по IT11 квалитету можно получить растачиванием чистовыми резцами на токарных или револьверных станках или сверлением с помощью кондуктора.
Точность обработки отверстия по IT12 и IT14 квалитету можно получить сверлением или растачиванием на всех станках, включая автоматы, выполняющие такие операции.
Точность обработки валов по IT5-IT6 квалитету после предварительной токарной обработки достигается последовательным шлифованием - черновым (предварительным) и чистовым (окончательным).
Для обработки валов по IT7 квалитету применяется шлифование после предварительной обработки на токарных и револьверных станках. Эту точность можно получить и не применяя шлифования, если на токарных и револьверных станках работают токари высокой квалификации.
По IT9-IT10 квалитету точности валы обрабатываются на токарных и револьверных станках, а также на автоматах отделочными резцами.
Для получения валов с точностью IT11 квалитета необходима черновая и чистовая обработка на токарных и револьверных станках.
Точность IT12-IT14 квалитета достигается на универсальных токарных и револьверных станках с использованием универсального режущего инструмента.
Возможную точность, достигаемую различными способами чистовой обработки, можно представить в такой последовательности:
а) чистовое обтачивание деталей малых размеров - до 0,02мм (20мкм);
б) точное шлифование - до 0,005 мм (5 мкм);
в) шлифование в прецизионных работах - до 0,0025мм (25 мкм);
г) притирка - до 0,0005 мм (0,5 мкм);
д) доводка - до 0,00005 мм (0,05 мкм).
Вопросы для самоконтроля.
- Что такое точность?
- Перечислите основные факторы, влияющие на точность обработки.
- Какие погрешности называются систематическими?
- Какие погрешности называются случайными?
- Приведите примеры случайных и систематических погрешностей.
{/spoilers}