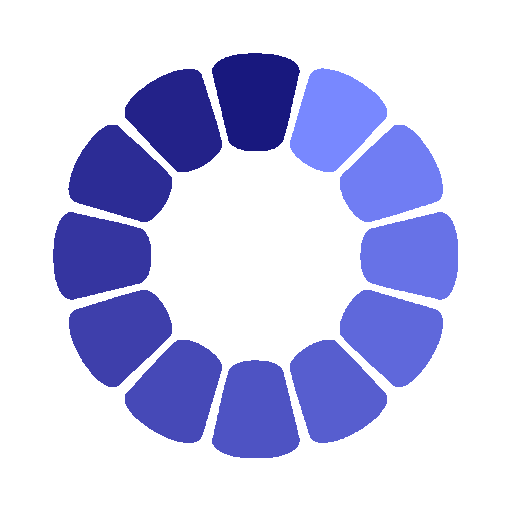
Ballarni quyidagi havolalar orqali stib olishingiz mumkin.
Механизация и автоматизация сборочных работ. Сборка типовых деталей и узлов машин
План:
- Механизация и автоматизация сборочных работ.
- Сборочные единицы с подшипниками
- Сборочные единицы с зубчатыми колесами
{spoiler=Подробнее}
Ключевые слова по теме лекции::
Механизация; автоматизация; сборочная единица; шарикоподшипник; роликоподшипник; зубчатое колесо; резьбовое соединение; сила зажима.
1. Механизация и автоматизация сборочных работ
В условиях серийных производств при сборке необходимо стремиться к замене ручных слесарных работ различными механизмами, например- электро и пневмодрели, гайковерты, отвертки, притирочные установки, клепальные машины, прессы и т. д.
Повысить производительность сборочных операций можно так же путем применения специальных приспособлений для установки и соединения деталей, для крепления базовых деталей собираемых узлов, съемников, скоб, захватов, поворотных приспособлений, контователей, проверочных приспособлений правильности сборки, регулировочных приспособлений и т. д.
В крупносерийном и массовом производстве широко применяются автоматизированные сборочные устройства и автоматические линии для сборки. Так, для подачи деталей к автоматизированным местам сборки используются различного рода бункерные загрузочные устройства, шиберные питатели с поштучной выдачей деталей, желоба, склизы для транспортировки и ориентации собираемых деталей, механические манипуляторы.
Автоматические сборочные устройства состоят из автоматизированной системы подачи деталей и исполнительного механизма проведения их сборки, например- устройство для автоматической подачи и завертывании винтов.
Автоматизированные линии сборки состоят из устройств, автоматически выполняющих ряд сборочных операций и стендов, на которых работают слесари- сборщики. Как правило, они выполняют более сложные и ответственные сборочные операции, автоматизировать которые нецелесообразно по различным причинам.
На автоматических линиях сборки изделия собираются от начала до конца без участия человека в операциях сборки, например- автоматическая линия по сборке подшипников качения, роторный стенд для сборки керамических резисторов и т. д. В последнее время появляются гибкие автоматические линии сборки изделий в условиях серийных производств. Такие линии снабжены переналаживаемыми автоматическими сборочными машинами, роботами- манипуляторами со сменной программой действий и транспортными механизмами с переменной скоростью перемещения собираемых изделий.
2. Сборка типовых деталей и узлов машин
сборочные единицы с подшипниками
Для обеспечения большей эксплуатационной надежности шарикоподшипников и предотвращения перекосов, их вращающееся кольцо должно собираться по посадке с натягом, а неподвижное кольцо- по посадке с зазором. При напрессовке внутреннего кольца шарикоподшипника на вал или наружного кольца- в корпус обязательно применение оправок и стаканов, которые направляют перемещение подшипника. Желательно, чтобы рабочий торец оправки упирался в торец запрессовываемого кольца (см. рис.10.2).
Рис.10.2. Оправки и стаканы для напрессовки шарикоподшипников на валы.
Усилие, необходимое для напрессовки, создается, как правило, при помощи прессов различной конструкции с реечным, пневматическим, гидравлическим или фрикционным приводом, либо специальными винтовыми устройствами.
При сборки узлов с коническими роликовыми подшипниками их наружные и внутренние кольца устанавливаются с зазором для последующего регулирования радиального разряда между роликами и рабочими дорожками колец. Радиальный натяг в коническом роликовом подшипнике регулируется путем осевого смещения наружного или внутреннего кольца за счет использования неподвижных или подвижных компенсаторов. На рис.10.3,а представлена конструкция узла, в которой набор прокладок 1 под крышкой 2 служит неподвижным компенсатором для обеспечения требуемого радиального натяга в коническом подшипнике. На рис.10.3,б натяг регулируется кольцевой гайкой с последующей фиксацией ее положения (подвижный компенсатор). Имеются также другие конструкции подвижных и неподвижных компенсаторов.
Рис.10.3. Способы регулирования радиального зазора в коническом роликовом подшипнике: а) набором прокладок (неподвижный компенсатор); б) кольцевой гайкой (подвижный компенсатор).
Процесс сборки подшипников скольжения состоит из их установки (с натягом), пригонки, фиксации от проворота и иногда- регулирование опор, если их более двух. По конструкции подшипники скольжения бывают цельными (втулки) и разъемными (вкладыши). Подшипники- втулки устанавливаются обычно с натягом по наружному диаметру с упором в буртик втулки. От проворачивания используют, например, установочный винт, отверстие под который обрабатывается после запрессовки. Иногда для получения посадки со значительным зазором сборку проводят с нагревом корпуса, либо с охлаждением самой втулки. После запрессовки тонкостенных подшипниковых втулок возможно окончательное развертывание или растачивание рабочего отверстия.
Под разъемными вкладышами подготавливаются отверстия по 6- 7 квалитету точности, а для предотвращения их проворачивания на торцах разъема вкладышей выштамповываются специальные выступы, упирающиеся в плоскость разъема крышки.
Сборочные единицы с зубчатыми колесами
Правильность зацепления зубчатых колес, собранных на валы, зависит от положения самих валов в корпусе. Наличие и величину зазора между зубьями предварительно можно проверить « на ощупь»- по углу свободного поворота одного из колес. Более точно зазор между зубьями можно проверить индикатором на магнитной стойке.
Рис.10.4. Виды отпечатков (пятен касания) на рабочих поверхностях зубьев при проверке качества сборки зубчатых колес краской: а) правильная сборка; б) межцентровое расстояние увеличено; в) межцентровое расстояние уменьшено; г) и д) - перекос осей валов.
Зацепления зубчатых колес проверяют по пятку контакта поверхностей зубьев с помощью краски, которую равномерным слоем наносят на зубья одного из колес. При провороте парных зубчатых колес на другом колесе в местах контакта рабочих поверхностей зубьев появятся отпечатки, по положению которых можно судить о качестве сборки пары зубчатых колес (см. рис 10.4). При качественной сборке пятно касания должно равномерно располагаться в районе середины высоты зуба и занимать до 75% площади рабочей поверхности зуба.
При сборке конических зубчатых колес правильность зацепления регулируется осевым перемещением одного из зубчатых колес по валу с последующей фиксацией его положения. Боковой зазор в зацеплении конических зубчатых колес можно проверить щупом, или прокатыванием между зубьями свинцовой пластинки, толщина которой будет равна зазору в зубчатом зацеплении.
При сборке червячных пар контролируют зазор в зацеплении зубьев колеса с витками червяка и смещение средней плоскости колеса относительно оси червяка. Практически правильность сборки червячного зацепления можно проверить по величине угла поворота червяка (люфта) до начала движения червячного колеса, Который не должен быть более 10- 15°.
Сборка резьбовых соединений
Качество сборки резьбовых соединений зависит от: а) качества поверхностей соприкосновения торцов болта или гайки с закрепляемой деталью; б) усилие затяжки резьбового соединения; в) последовательности затяжки много- болтовых соединений на одной детали.
Наиболее распространенная причина срыва резьбы или обрыва болтов является перекос болта или гайки. Поэтому поверхность детали, соприкасающаяся с торцом болта или гайки должна быть механически обработана. На необрабатываемых поверхностях всех деталей под торцы резьбового крепежа выполняются цекованием (цилиндрическим зенкерованием) небольшие по глубине ступенчатые отверстия с чисто обработанными торцами. Иногда на литых поверхностях для этих целей изготавливают цилиндрические выступы- бобышки (бонки), торцы которых обрабатываются фрезерованием на проход, либо цекованием поштучно.
Сборка резьбовых соединений на болтах и гайках осуществляется гаечными ключами в ручную или механизированными одно- и многошпиндельными гайковертами - пневматическими, электрическими, механическими. Длинна гаечного ключа принимается не более 15 диаметров резьбы, что обеспечивает нормальную затяжку и исключает возможность срыва резьбы. В ответственных резьбовых соединениях оптимальное усилие затяжки резьбы, гарантирующее отсутствие самоотворачивания рассчитывается по известным формулам и обеспечивается при сборке тарированными динамометрическими ключами. В случае механизированной затяжки на шпиндели гайковертов устанавливают пружинно- кулачковые муфты, которые начинают прокручиваться при возрастании крутящего момента больше заданной величины.
Следующий способ контролирующей затяжки - с замером угла поворота гайки (болта) после заворачивания до упора. Наиболее точный способ затяжки болта (шпильки) - с замером удлинения стержня от действия сил затяжки и доведения удлинения до заданной величины, заранее рассчитанной для сечения стержня болта с учетом материала его изготовления. Этот метод применяется при автоматической затяжке гаек при сборке крышек шатунов двигателей внутреннего сгорания.
При многоболтовых соединениях последовательность сборки следующая: а) заворачиваются все болты в любой последовательности только до упора; б) проводится предварительная затяжка болта (гаек) по правилу « от середины к кроям, крест- накрест».
На работающих машинах от толчков и вибраций, воздействующих на резьбовые соединения последние могут самопроизвольно ослабляться. Для предотвращения самоотвинчивания болтов и гаек используются многие способы их стопорения, наиболее распространенные из которых: а) использование контргайки; б) шклинта; в) пружинной или замковой шайбы; г) кернение на гайке специального пояска; д) кернение головки винта « в потай»; е) обвязка болтов проволокой через отверстия в головках и т. д.
Вопросы для самопроверки
- Для чего необходима механизация и автоматизация сборочных процессов?
- Приведите примеры сборки с подшипниками?
- На что необходимо обратить внимание при сборке зубчатых колёс?
- Как проверяется точность сборки зубчатых колёс?
- Как расчитывается усилия затяжки резьбового соединения?
{/spoilers}