Соединения деталей машин.общие сведения . Исполнитель
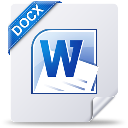
- Скачано: 44
- Размер: 286.5 Kb
Соединения деталей машин.общие сведения .
Резьбовые соединения.
Цель занятия: ознакомить студентов с общими основными понятиями соединения деталей машин, с особенностями соединения деталей машин при помощи резьбового соединения.
План:
1.Общие сведения о соединении деталей машин.
2. Резьба.
2.1.Основные определения и классификация резьбы по геометрической форме.
2.2.Методы изготовления резьбы.
2.3. Геометрические параметры, характеризующие резьбу 2Л. Основные типы резьб, их классификация и обоснование выбора профиля
резьбы.
3.Основные типы крепежных деталей.
3.1. Способы стопорения резьбовых соединений.
3.2. Теория винтовой пары.
4. Зависимость между моментом, приложенным к гайке, и осевой силой /винта.
4.1. Самоторможение и к.п.д. винтовой пары.
4.2 Распределение осевой нагрузки винта по виткам резьбы
5. Расчет резьбы на прочность.
{spoiler=Подробнее}
Опорные слова: детали, способ соединения, тип соединяемых деталей, резьба, классификация резьбы, параметры резьбы, крепежные детали, теория винтовой пары, расчет резьбы на прочность.
Общие сведения о соединении деталей машин.
Детали, составляющие машину, связаны между собой тем или иным способом. Эти связи можно разделить на подвижные, к которым относятся различного рода шарниры, подшипники, зацепления, и неподвижные — резьбовые, сварные, шпоночные и др.
Наличие подвижных связей в машине обусловлено ее кинематической схемой. Неподвижные связи (жесткие или упругие) вызываются потребностью расчленения машины на узлы и детали. Это делают для того, чтобы упростить производство машины, облегчить ее сборку, ремонт, транспортировку и т. д.
Неподвижные связи в технике называют соединениями.
По признаку разъемности все виды соединений можно разделить на разъемные и неразъемные.
Разъемные соединения позволяют разбирать узлы без повреждения деталей. К ним относятся резьбовые, штифтовые, клиновые, клеммовые, шпоночные, шлицевые и профильные соединения.
Неразъемные соединения не позволяют разбирать узлы без разрушения или повреждения деталей. Применение неразъемных соединений обусловлено в основном технологическими и экономическими требованиями. К этой группе соединений относятся: заклепочные, сварные и прессовые *.
По типу соединяемых деталей можно выделить:
а) соединения деталей типа вал и ступица: шпоночные, шлице-
вые, профильные и прессовые:
б) соединения всех других деталей (корпусных, листовых, трубчатых и т. д.): д) резьбовые, сварные, заклепочные.
Соединения являются весьма важными элементами конструкций. Многие аварии и прочие неполадки в работе машин и сооружений обусловлены неудовлетворительной конструкцией соединений.
Основным критерием работоспособности и расчета соединений является прочность — статическая и усталостная.
Необходимо стремиться к тому, чтобы соединение было равнопрочным с соединяемыми элементами **. Наличие соединения, которое обладает прочностью, составляющей, например, 0,8 от прочности других элементов конструкции, свидетельствует о том, что 20% нагрузочной способности этих элементов или соответствующая часть металла конструкции не используется. Во многих случаях неравно прочность соединения приводит к большим излишним затратам материала. Например, прочность некоторых заклепочных соединений листов, вследствие ослабления листов отверстиями под заклепки, составляет лишь 60% от прочности самих листов. При равнопрочном соединении, например сварном, толщину и вес этих листов можно уменьшить на 40%.
Желательно, чтобы соединение не искажало форму изделия, не вносило дополнительных элементов в его конструкцию и т. п. Например, соединение труб болтами требует образования фланцев на концах, труб, сверления отверстий под болты, установку самих болтов с гайками и шайбами. Соединение труб сваркой встык не требует никаких дополнительных элементов. Оно в наибольшей степени приближает составное изделие к целому. С этих позиций соединение болтами может быть оправдано только разъёмностью.
Соединения деталей с помощью резьбы являются одним из старейших и наиболее распространенных видов разъемного соединения. К ним относятся соединения с помощью болтов, винтов, винтовых стяжек и т. д.*
РЕЗЬБА
Основные определения и классификация по геометрической форме
Цилиндрическая резьба (рис. 1.1) — поверхность,
образованная при винтовом движении плоского контура (например,
abc по цилиндру.) Профиль резьбы — контур сечения резьбы в плоскости, проходящей через ось цилиндра.
По форме профиля резьбы разделяют на треугольные, прямоугольные, трапецеидальные, круглые и др.По направлению винтовой линии различают правую и. левую резьбы У правой резьбы винтовая линия идет слева направо и вверх, у левой — справа налево и вверх. Наиболее распространенной является правая резьба. Левую резьбу применяют только в специальных случаях.
Если по параллельным винтовым линиям перемещают два или несколько рядом расположенных профилей, они образуют резьбу. По числу заходов резьбы делят на однозаходную, двух заходную. и т. д. Наиболее распространенной является однозаходная резьба. Все крепежные резьбы однозаходные.
Число заходов больше трех применяется редко.
Кроме цилиндрической, изготовляют коническую резьбу, основной поверхностью для которой служит конус. Наиболее распространена цилиндрическая резьба. Коническую резьбу применяют для плотных соединений труб, масленок, пробок и т. п.
Методы изготовления резьбы
Резьбу можно изготовлять следующими способами:
1. Нарезкой вручную метчиками (плашками). Способ малопроизводительный. Его применяют в индивидуальном производстве и ремонтных работах.
2.Нарезкой на токарно-винторезных или специальных станках.
3.Методом фрезерования на специальных резьбо фрезерных станках. Применяют для нарезки винтов больших диаметров с повышенными требованиями к точности резьбы (ходовые и грузовые винты,
резьбы на валах и т. д.).
4.Методом накатки на специальных резьбонакатных станках-
автоматах. Этим высокопроизводительным и дешевым методом изготовляют большинство резьб стандартных
крепежных деталей (болты, винты и т. д.).
5.Методом отливки. Этим методом изготовляют резьбы на литых деталях из чугуна, стекла, пластмассы, металлокерамики и др.
6.Методом выдавливания. С помощью этого метода изготовляют резьбу на тонко стенных давленых и штампованных изделиях из жести, пластмассы и т. д.
Геометрические параметры, характеризующие резьбу
Резьба характеризуется следующими основными геометрическими параметрами, которые рассмотрим на примере метрической резьбы (рис. 1.2): d — наружный диаметр резьбы; d1 — внутренний диаметр Рис. 1.2 резьбы; d2 — средний диаметр резьбы (диаметр воображаемого цилиндра, поверхность которого пересекает резьбу в таком месте, где ширина витка равна ширине впадины *); h — рабочая высота профиля, по которой соприкасаются витки винта и гайки; .S — шаг резьбы (расстояние между одноименными сторонами двух соседних витков, измеренное в направлении оси винта);
S1 — ход резьбы (величина поступательного перемещения образующего профиля за один оборот, или величина поступательного перемещения гайки или винта за один оборот. Для однозаходной резьбы S1= S; для многозаходных резьб .S1 =nS, где n— число заходов); — угол профиля; — угол подъема резьбы (угол, образованный касательной к винтовой линии
в точке на среднем диаметре резьбы и плоскостью, перпендикуляр-
ной к оси резьбы — рис.)
Все геометрические параметры большинства резьб и допуски на их размеры стандартизованы.
Основные типы резьб, их классификация и обоснование выбора профиля резьбы
Резьбы разделяют по назначению и форме профиля.
1. Резьбы крепежные: метрическая с треугольным профилем (см. рис. 1.2) — является основной крепежной резьбой; трубная (рис. 1.4, а) треугольная со скругленными вершинами и впадинами; (рис. 1.4, б); резьба винтов для дерева (рис. 1.4, б).
Рис. 1.4
2. Резьбы винтовых механизмов (ходовые резьбы): прямоугольная (рис. 1.5, и);трапецеидальная симметричная (рис. 1.5, б); трапецеидальная не симетричная или упорная (рис. 1.5, в).
Приведенная классификация не является строгой, так как в практике встречаются случаи применения метрической резьбы с мелким шагом в точных измерительных винтовых механизмах и, наоборот, трапецеидальных резьб как крепежных.
Выбор профиля резьбы в зависимости от ее назначения определяется многими факторами. Важнейшими из них являются прочность, технологичность и величина трения в резьбе (величина потерь) Так, например, крепежная резьба должна обладать высокой прочностью и трением, предохраняющие крепежными детали от самоотвинчивания.
Резьбы винтовых механизмов должны быть с малым трением, чтобы повысить к.п. д. и уменьшить износ. Прочность во многих случаях не является здесь основным фактором, определяющим размеры винтовой пары.
На рис. 1.6 сопоставляются прямоугольная и треугольная резьбы. Осевая сила Р, действующая по стержню винта, воспринимается гайкой через элементарные нормальные силы, распределенные по поверхности резьбы. Считая условно эти силы сосредоточенными, получим выражение для суммарной окружной силы трения в резьбе в следующем виде *. для прямоугольной резьбы
для треугольной резьбы
где f — действительный коэффициент трения; f/' — фиктивный, или приведенный, коэффициент трения в резьбе
Так как для треугольной резьбы α= 60° и 0,86, то трение
в ней примерно на 14% больше, чем в прямоугольной резьбе.
В дальнейшем будет показано, что прочность резьбы на срез рассчитывается по сечениям с—с (см. рис. 1.6). Следовательно, при одном и том же шаге резьбы S треугольная резьба примерно в два раза прочнее прямоугольной. По этим причинам основные крепежные резьбы имеют треугольный профиль, а ходовые резьбы — прямоугольный или близкий к нему.
Рассмотрим некоторые дополнительные характеристики отдельных типов резьб.
Резьба метрическая (см. рис. 1.2) получила свое название потому, что все ее размеры измеряются в мм (в отличие от дюймовой резьбы, размеры которой измеряются в дюймах *). Вершины витков и впадин
притуплены по прямой или по дуге окружности, по вершинам и впадинам образован зазор. Такая конструкция облегчает обработку, уменьшает концентрацию напряжений и предохраняет резьбу от повреждений (забоин) в эксплуатации.
Стандарт предусматривает метрические резьбы с крупным и мелким шагом. Для одного и того же наружного диаметра d* мелкие резьбы отличаются от крупной величиной шага S Например, для диаметра 14 мм стандарт предусматривает крупную резьбу с шагом 2 мм и пять мелких резьб с шагом 1,5; 1,25; 1; 0,75 и 0,5 мм [12]. При уменьшении шага соответственно уменьшаются глубина резьбы (рис. 1.7) и угол подъема резьбы—см. формулу (1.1).
Уменьшение глубины резьбы или увеличение диаметра d1 повышает прочность стержня винта, а уменьшение угла подъема увеличивает самоторможение в резьбе (см. ниже), т. е. уменьшает возможность самоотвинчивания. По этим причинам мелкие резьбы находят применение для динамически нагруженных деталей, полых тонкостенных и мелких деталей (авиация, точная механика, радиотехника и т. п.).
В общем машиностроении основное применение имеют крупные резьбы как менее чувствительные к ошибкам изготовления и износу. Резьбы трубные (см. рис. 1.4, а) применяются для герметичного соединения труб и арматуры (масленки, штуцера и т. п.). На тонкой стенке трубы невозможно нарезать крупную метрическую резьбу без резкого уменьшения прочности трубы. Поэтому трубная резьба имеет мелкий шаг. В международном стандарте для трубной резьбы до настоящего времени еще сохранено дюймовое измерение.
За номинальный диаметр трубной резьбы принят внутренний диаметр трубы dтр- Наружный диаметр резьбы в действительности больше номинального на две толщины стенки.
Для лучшего уплотнения трубную резьбу выполняют с закруглениями профиля и без зазоров по выступам и впадинам.
Высокую плотность соединения дает коническая трубная резьба. Плотность здесь достигается за счет пластических деформаций вершин резьбы при затяжке соединения. Коническая резьба в изготовлении сложнее цилиндрической. В настоящее время вместо трубных резьб часто применяют мелкие метрические резьбы.
Резьба круглая (см. рис. 1.4, б) удобна для изготовления отливкой на чугунных, стеклянных, пластмассовых и других изделиях, а также накаткой и выдавливанием на тонкостенных металлических и пластмассовых деталях.
Резьбы винтов, предназначенных для дерева или других мало прочных материалов (см. рис. 1.4, е). Конструкция этих резьб обеспечивает равнопрочность резьбы в деталях из разнородных материалов. Например, для резьбы деревянной детали расчетным размером на срез является S а для резьбы металлического винта .S'. При этом S>S'.
Резьба прямоугольная (см. рис. 1.5, я), широко применявшаяся ранее в винтовых механизмах, в настоящее время не стандартизована и почти вытеснена трапецеидальной. При износе прямоугольной резьбы образуются осевые зазоры (осевая «игра))), которые трудно устранить. Изготовить эту резьбу на резьбофрезерных станках невозможно, так как для образования чистой и точной резьбы у фрезы должны быть режущими не только передние, но и боковые грани (сравни профили рис. 1.5, а и 1.5, б *).
Прямоугольную резьбу изготовляют резцами на токарно-винторезных станках. Этот способ имеет низкую производительность и невысокую точность.
Резьба трапецеидальная изготовляется с симметричным (см. рис. 1.5, б) и несимметричным (см. рис. 1.5, е) профилем. Симметричную резьбу используют для передачи двустороннего (реверсивного) движения под нагрузкой. Несимметричная резьба предназначается Для одностороннего рабочего движения при больших нагрузках и называется упорной резьбой. Она применяется для винтов-домкратов, прессов и т. д.
Закругление впадин (см. рис. 1.5, е) повышает динамическую прочность винта. Малый угол наклона (3°) упорной стороны профиля резьбы понижает потери на трение в сравнении с симметричным профилем и в то же время позволяет изготовлять винты на резьбофрезерных станках.
ОСНОВНЫЕ ТИПЫ КРЕПЕЖНЫХ ДЕТАЛЕЙ
Здесь рассматриваются только принципиальные вопросы, относящиеся к применению того или иного типа крепежных деталей. Геометрические формы и размеры крепежных деталей не рассматриваются, так как они весьма разнообразны и с исчерпывающей полнотой описаны в справочниках и стандартах крепежных изделий [12]. Для соединения деталей можно применять болты (винты с гайками, рис. 1.8, а)*, винты (рис. 1.8, б*) или шпильки (рис. 1.8,е). Основным преимуществом болтового соединения является то, что оно не требует нарезания резьбы в соединяемых деталях. Это особенно важно в тех случаях, когда материал детали не может обеспечить достаточную прочность и долговечность резьбы. К недостаткам болтового соединения можно отнести следующее: обе детали должны иметь место для расположения гайки или головки винта; при завинчивании и отвинчивании гайки необходимо удерживать головку винта от проворачивания; по сравнению с винтовым, болтовое соединение несколько увеличивает вес изделия и больше искажает его внешние очертания. Винты и шпильки применяют в тех случаях, когда по конструкции соединения постановка болта не рациональна.
Если при эксплуатации деталь часто снимают и затем снова ставят на место, ее следует закреплять болтами или шпильками, так как винты при многократном завинчивании могут повредить резьбу в детали.
Простую шайбу ставят под гайку или головку винта для уменьшения смятия детали гайкой, если деталь изготовлена из менее прочного материала (пластмассы, алюминия, дерева и т. п.); для предохранения чистых поверхностей деталей от царапин при завинчивании гайки (винта); для перекрытия зазора отверстия при большой его величине В других случаях простую шайбу ставить нецелесообразно.
Кроме простых шайб, применяют стопорные, или предохранительные шайбы. Эти шайбы предохраняют соединение от самоотвинчивания.
СПОСОБЫ СТОПОРЕНИЯ РЕЗЬБОВЫХ СОЕДИНЕНИЙ
Предохранение от самоотвинчивания является весьма важным для повышения надежности резьбовых соединений и совершенно необходимым для соединений, воспринимающие переменные и ударные нагрузки. Самоотвинчивание разрушает соединения и может привести к аварии.
Практика показывает, что самоотвинчивание наблюдается преимущественно в резьбовых соединениях, воспринимающих переменные и ударные нагрузки или подверженных вибрации. Вибрации понижают трение и нарушают условие самоторможения в резьбе.
Существует очень много способов стопорения или предохранения от самоотвинчивания. Описание этих способов приводится в справочниках и специальной литературе ( 12], [21].
На практике применяют следующие три основных принципа стопорения:
1. Повышают и стабилизируют трение в резьбе путем постановки контргайки (рис. 1.9, а), пружинной шайбы (рис. 1.9, б), применения резьбовых пар с натягом в резьбе и т. п.
Контргайка создает дополнительное натяжение и дополнительное трение в резьбе. Пружинная шайба поддерживает натяг и трение в резьбе на большом участке самоотвинчивания (до 1—2 оборотов гайки). Кроме того, упругость шайбы значительно уменьшает влияние вибраций на трение в резьбе.
2. Гайку жестко соединяют со стержнем винта. Например, с помощью шплинта (рис. 1.10) или прошивают группу винтов проволокой (рис. 1.11, а, б).
Способы стопорения этой группы позволяют производить только ступенчатую регулировку затяжки соединения
3.Гайку жестко соединяют с деталью. Например, с помощью специальной шайбы (рис1.12, а), планки (1.12, б) или приваркой (рис.1.12,в).
Конструктор должен уделять большое внимание предохранению резьбовых соединений от самоотвинчивания.
ТЕОРИЯ ВИНТОВОЙ ПАРЫ
Зависимость между моментом, приложенным к гайке, и осевой силой винта
Если винт нагружен осевой силой Р (рис. ИЗ), то для завинчивания гайки к ключу необходимо приложить момент Тк, а к стержню винта реактивный момент Тр,, который удерживает стержень от вращения.
Зависимость между Тк и Р можно получить из уравнения работ
где Ак — работа момента, приложенного к ключу; Ат — работа сил трения на опорном торце гайки; Ар — работа сил трения в резьбе;
Ар —работа силы Р на осевом перемещении.
Реактивный момент Тр в уравнении работ не участвует, так как стержень не вращается и работа этого момента равна нулю.
Рассматривая один оборот гайки, получаем:
Здесь Тт — момент сил трения на опорном торце гайки (рис.).
Не допуская существенной погрешности, можно принять, что приведенный радиус сил трения на опорном торце гайки равен среднему радиусу этого торца или Dср/2.
При этом
Тт=Рf(Dср/2),
где Dср — (D1 + Dотв)/2; D1 — наружный диаметр опорного торца гайки; dотв —диаметр отверстия под винт; f— коэффициент трения.
Если принять равномерное распределение давления по торцу гайки, то получим
,
где Удельное давление на торце гайки;
- приведенный радиус сил трения.
Сумму работ (Ар + Ар) за один оборот гайки можно определить, рассматривая движение груза Р по наклонной плоскости, угол которой равен углу подъема резьбы )3 (рис. 1.14, б), а высота — ходу 5,. Работа, затраченная на подъем груза по наклонной плоскости с учетом трения, равна работе подъема того же груза по некоторой фиктивой наклонной плоскости без учета трения. При этом угол подъема фиктивной плоскости больше угла подъема действительной на угол трения
где f' — приведенный коэффициент трения в резьбе — см. формулу
Таким образом, получаем )после сокращения на 2 найдем искомую зависимость между Р и Tк
Здесь первый член правой части есть момент сил трения на торце гайки — см. формулу (1.5), а второй член является моментом сил в резьбе
Анализируя полученные зависимости, отметим:
1.По формуле (1.7) можно подсчитать отношение осевой силы винта Р к силе,R приложенной на ручке ключа (Р/R — выигрыш в силе). Для стандартных метрических резьб при стандартном ключе (L15d) и при f 0.15 P/R 70 - 80 (см. табл. 1.6).
2. Реактивный момент, необходимый для удержания стержня
винта от проворачивания при завинчивании гайки, равен моменту
сил в резьбе Tр.
3. Стержень винта будет не только растягиваться силой Р, но и закручиваться моментом Tр (момент ключа Tк не полностью передается стержню, так как часть его, равная Тт., затрачивается на преодоление трения на торце гайки).
4. Формула (1.5) для момента трения на торце гайки остается приближенно справедливой и для других подобных случаев. Например, величину момента трения на торце винта для зажима резца (рис. 1.15) получим, приняв D1=dт и
dотв =0
Самоторможение и к. п. д. винтовой пары
На рис. 1.14, б изображен случай подъема груза. Нетрудно понять, что для случая опускания груза угол трения р' надо вычитать из р. До тех пор, пока угол фиктивной плоскости (р — р') положительный, груз опускается сам под действием силы тяжести — самоторможения нет. При отрицательном значении (β — р') груз находится в покое — самоторможение.
Условие самоторможения: β<'. (1.9)
При этом статическая нагрузка винта не вызывает самоотвинчивания гайки.
Для крепежных резьб величина угла подъема р лежит в пределах от 1,5 до 4°, а угол трения р' изменяется в зависимости от величины коэффициента трения в пределах от 6° (f/0,1) до 16° (f/0,3) *.
Таким образом, все крепежные резьбы — самотормозящие ходовые резьбы выполняют как самотормозящие, так и не самотормозящие.
К. п. д. винтовой пары η представляет интерес главным образом для винтовых механизмов."Его можно вычислить по отношению работы, затраченной на завинчивание гайки без учета трения, к той же работе с учетом трения или по отношению Т/к/Тк, в котором Тк определяется по формуле (1.7), а Т/к по той же формуле, но при f = 0 и р' = 0.
Учитывая потери только в резьбе (Tт = 0), найдем к. п. д. собственно винтовой парыВ самотормозящей паре, где < р',< 0,5. Так как большинство винтовых механизмов самотормозящие, то их к. п. д. меньше 0,5.
Формула (1.11) позволяет отметить, что возрастает с увеличением и
с уменьшением р'. График в зависимости от при р' 6° изображен на рис. 1.16.
Максимальное значение можно определить из выражения (1.11), приравняв нулю производную
. Получим при = 45° — р'/2.
Для увеличения угла подъема резьбы β в винтовых механизмах применяют многозаходные винты. В практике редко используют винты, у которых р больше 20÷25°, так как дальнейший прирост к. п. д. незначителен, а изго-товление резьбы затруднено. Кроме того, при большем значении р становится малым выигрыш в силе или передаточное отношение винтовой пары (см. гл. 13).
Для повышения к. п. д. винтовых механизмов используют также различные средства, понижающие трение в резьбе: антифрикционные металлы, тщательную обработку и смазку трущихся поверхностей, установку подшипников под гайку или упорный торец винта, применение шариковых винтовых пар и т. п.
Распределение осевой нагрузки винта по виткам резьбы
На рис. 1.17 изображена схема винтовой пары. Осевая нагрузка Р винта передается через резьбу гайке и уравновешивается реакцией ее опоры. При этом каждый виток резьбы нагружается соответственно силами Р1, Р2, ... , Рz. Сумма Р1 + Р2 + ... + Рz, = Р.
При равномерном распределении нагрузки в резьбе
где z — число витков резьбы гайки.
Эпюра осевых сил в различных сечениях стержня винта при равномерном распределении нагрузки в резьбе изображена на рис. 1.17, а. Здесь в каждом последующем сечении нагрузка уменьшается равномерно на величину Р/z.
Приближенно-равномерное распределение нагрузки по виткам Резьбы можно получить, только применяя гайки специальной формы
В простых гайках витки резьбы нагружаются неравномерно
Одной из причин неравномерного распределения нагрузки в резьбе является неблагоприятное сочетание деформаций винта и гайки. Например, в рассматриваемом случае винт растягивается, а гайка сжимается. При этом точки И, В, С и D винта и гайки
Рис. 1.17
перемещаются вниз соответственно на ΔA, ΔB, Δс и Δд. Вследствие растяжения участка AB винта
вследствие сжатия участка СD гайки
ΔD<Δс. (б)
Все деформации витка резьбы и в том числе прогиб витка пропорциональны его нагрузке. Выражая прогиб через относительное перемещение точек A и D (ΔAD), В и С (ΔBC) и т. д., где
ΔAD=ΔA-ΔD
ΔBC=ΔB-ΔC
и учитывая неравенства (а) и (б), находим
ΔAD>ΔBC (г)
Следовательно, нагрузка первого витка больше нагрузки второго и т. д.
Теоретическое решение задачи о распределении нагрузки по виткам резьбы было дано Н. Е. Жуковским в 1902 г. В дальнейшем это решение неоднократно подтверждалось экспериментальными исследованиями на прозрачных моделях. Установлено, например, что при стандартной крепежной гайке с шестью витками первый виток резьбы воспринимает около 52% нагрузки Р, второй — 25%, третий — 12% и последний, шестой виток —только 2%
Указанные теоретические и экспериментальные исследования позволили разработать конструкции специальных гаек, выравнивающих
распределение нагрузки в резьбе (рис. 1.18). На рис. 1.18, а изображена висячая гайка. Выравнивание нагрузки в резьбе здесь достигают благодаря тому, что винт и гайка имеют однозначные деформации растяжения. При этом неравенство (б) изменится и будет ΔD > Δс, а разность между ΔAD и ΔBC уменьшится. Кроме того, в наиболее нагруженной нижней зоне висячая гайка обладает повышенной податливостью, что также способствует выравниванию нагрузки в резьбе. При соответствующем подборе формы висячей гайки можно получить равномерное распределение нагрузки в резьбе. На рис. 1.18, б показана разновидность висячей гайки — гайка с кольцевой выточкой.
Рис.1.18
У гайки, изображенной на срезаны вершины нижних витков резьбы под углом15—20°. При этом увеличена податливость нижних витков винта, так как они соприкасаются с гайкой не всей поверхностью, а только своими вершинами. Увеличение податливости витков в наиболее нагруженной зоне снижает нагрузку. этих витков
Специальные гайки особенно желательно применять для соединений, подвергающихся действию динамических нагрузок. Разрушение таких соединений, как правило, имеет усталостный характер и происходит в зоне наибольшей концентрации напряжений у нижнего (наиболее нагруженного) витка резьбы. Уменьшение нагрузки нижних витков повышает прочность соединения. Опытом установлено, что применение специальных гаек позволяет повысить динамическую прочность резьбовых соединений на 20—30%.
РАСЧЕТ РЕЗЬБЫ НА ПРОЧНОСТЬ
Действительный характер распределения нагрузки по виткам гайки, кроме указанных выше причин, зависит от ошибок изготовления и степени износа резьбы, что затрудняет определение истинных напряжений. Поэтому в практике расчет резьбы на прочность производится не по истинным, а по условным напряжениям, которые сравнивают с допускаемыми напряжениями, установленными на основе опыта.
При определении условных напряжений полагают, что все витки нагружены равномерно , принято рассчитывать:
1.по напряжениям смятия на винтовой поверхности (рис. 1.19),
2.по напряжениям среза в сечении аb винта или се гайки.
Условия прочности резьбы по напряжениям смятия:
3)
где z= H/S — число витков резьбы в гайке высотой H.
Формула (1.12) является общей для винта и гайки. Вывод формулы прост и не требует дополнительных объяснений. Все элементарные преобразования здесь и в других подобных случаях изучающим рекомендуется производить самим.
Условия прочности резьбы по напряжениям среза:
для винта
для гайки,
где К=ab/S или К=ce/S — коэффициент, учитывающий тип резьбы;
для треугольной резьбы К 0, 8; для прямоугольной резьбы К = 0,5; для трапецеидальной резьбы К = 0,65.
Если материал винта и гайки одинаков, то по напряжениям среза рассчитывают только винт, так как d >d1. Равнопрочность резьбы и стержня винта является одним из условий назначения высоты стандартных гаек. Так, например, приняв в качестве предельных напряжений пределы текучести материала на растяжение и сдвиг и учитывая, что 0,6σТзапишем условия равнопрочности резьбы на срез и стержня винта на растяжение в виде:
откуда при К = 0,8 получаем Н0,5d1.
Здесь = σ—напряжение растяжения в стержне винта,рассчитанное приближенно по внутреннему диаметру резьбы.d1
Учитывая сложность напряженного состояния резьбы, а также предусматривая ослабление резьбы от истирания и возможных повреждений при завинчивании, высоту стандартных гаек крепежных изделий принимают
По тем же соображениям устанавливают нормы на глубину завинчивания винтов и шпилек в детали: стальные детали H1»d, в чугунные и силуминовые H1»1.5d
При этом прочность резьбы превышает прочность стержня.
Стандартная высота гайки и глубины завинчивания исключают необходимость расчета на прочность резьбы стандартных крепежных деталей.
Вывод: изучив данную тему студенты поличили сведения о способах соединения деталей машин, о резьбовых соединениях, о методах ее
изготовления.
Контрольные вопросы:
1. Какие соединения можно отнести к резьбовым соединениям?
2. Что собой представляет цилиндрическая резьба?
3. Перечислите методы изготовления резьбы?
4. Перечислите основные геометрические параметры резьбы?
Литература:
1 . М.Н. Иванов «Детали машин»
{/spoilers}