Сварные соединения Исполнитель
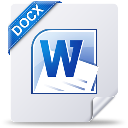
- Скачано: 31
- Размер: 158 Kb
Сварные соединения
Цель занятия: изучить конструктивные особенности сварных
соединений, их классификация, овладеть навыками расчета на прочность.
План:
1. Общие сведения и применение.
2. Конструкция сварных соединений и расчет их на прочность*
2.1. Соединение встык
2.2Соединение внахлестку
2.3. Соединение втавр
2.4. Соединение контактной сваркой.
3. Прочность сварных соединений и допускаемые напряжения
Опорные слова: неразъемное соединение, электрическая сварка, дуговая,
контактная, сварка под слоем флюса, соединение встык, прочность, швы. ОБЩИЕ СВЕДЕНИЯ И ПРИМЕНЕНИЕ
{spoiler=Подробнее}
Сварное соединение — неразъемное. Оно образуется путем сваривания материалов деталей в зоне стыка и не требует никаких вспомогательных элементов (заклепок, болтов и т. д.). Прочность соединения зависит от неоднородности и непрерывности материала сварного шва и окружающей его зоны.
Применяемые в современном машиностроении способы сварки весьма разнообразны. Каждый из них имеет свои конкретные области применения . Из всех способов сварки наиболее широко распространена электрическая. Различают два основных вида электросварки: дуговую и контактную.
Электродуговая сварка основана на использовании тепла электрической дуги для расплавления металла.
Для защиты расплавленного металла от вредного действия окружающего воздуха на поверхность электрода наносят толстую защитную обмазку, которая выделяет большое количество шлака и газа, образуя изолирующую среду. Этим обеспечивают повышение качества металла сварного шва, механические свойства которого могут резко ухудшиться под влиянием кислорода и азота воздуха.
С той же целью производят сварку под слоем флюса по методу, разработанному Институтом электросварки АН. Этот метод в настоящее время является основным методом автоматической сварки. Производительность автоматической сварки под флюсом в 10÷20 и более раз выше ручной. Повышение производительности достигают за счет применения тока силой от 1000 до 3000 А вместо 200—500 А при ручной сварке. Это обеспечивает более рациональное формирование шва.
В то время как при ручной сварке образование шва достигается в основном за счет металла электрода , при автоматической сварке шов формируется в значительной степени за счет расплавленного
основного металла , что не только сокращает время, но и значительно снижает расход электродного материала. Автоматическая сварка под слоем флюса обеспечивает высокие и, что особенно важно, однородные, независящие от индивидуальных качеств сварщика механические свойства соединений.
За последние годы разработан метод электрошлаковой сварки, при которой источником нагрева служит тепло, выделяющееся при прохождении тока через шлаковую ванну от электрода к изделию. Электрошлаковая сварка предназначена для соединения деталей большой толщины. Толщина свариваемых деталей практически не ограничивается.
Электрошлаковая сварка позволяет заменять сложные и тяжелые цельнолитые и цельнокованые конструкции сварными из отдельных простых отливок, поковок и листов, что значительно облегчает и снижает стоимость производства. Эта сварка применима и для чугунных отливок.
Контактная сварка основана на использовании повышенного омического сопротивления в стыке деталей и осуществляется несколькими способами.
При стыковой сварке через детали пропускают ток, сила которого достигает нескольких тысяч ампер. Основное количество тепла выделяется в месте стыка, где имеется наибольшее сопротивление; металл в этой зоне разогревается до пластического состояния или даже до поверхностного оплавления. Затем ток выключают, а разогретые детали сдавливают с некоторой силой — происходит сварка металла деталей по всей поверхности стыка. Этот метод рекомендуют применять для соединения встык деталей, площадь поперечного сечения которых сравнительно невелика.
При точечной сварке соединение образуется не по всей поверхности стыка, а лишь в отдельных точках, к которым подводят электроды сварочной машины.
При ленточной, или роликовой, сварке шов имеет вид узкой непрерывной ленты, расположенной вдоль стыка деталей. Это соединение выполняют с помощью электродов, имеющих форму роликов, которые катятся в направлении сварки.
Точечную и роликовую сварки применяют в соединениях внахлестку, преимущественно для листовых деталей толщиной не более 3—4 мм и тонких стержней арматурных сеток. В отличие от точечной роликовая сварка образует герметичное соединение
Рис. 3.2
Все рассмотренные способы контактной сварки — высокопроизводительны, их широко применяют в массовом производстве для сварки труб, арматуры, кузовов автомобилей, металлической обшивки железнодорожных вагонов, корпусов самолетов, тонкостенных резервуаров и т. д.
Оценивая сварное соединение, необходимо подчеркнуть, что оно является наиболее совершенным из не разьёмных соединений, так как лучше других приближает составление детали к цельным . При сварном соединении проще обеспечиваются условия равно прочности, снижения массы и стоимости изделия.
В настоящее время сварку применяют не только как способ соединения деталей, но и как технологический способ изготовления самих деталей. Сварные детали во многих случаях с успехом заменяют литые и кованые
Для изготовления сварных деталей не требуется моделей, форм или штампов. Это значительно снижает их стоимость при единичном и мелкосерийном производстве. Сварка таких изделий, как шестерня или коленчатые валы, позволяет изготовлять их более ответственные части (венец, шейка) из высокопрочных сталей, а менее ответственные (диск и ступица шестерни, щека коленчатого вала) — из дешевых материалов.
По сравнению с литыми деталями сварные допускают меньшую толщину стенок, что позволяет снизить массу деталей и сократить расход металла.
Большое распространение получили штампо –сварные конструкции , заменяющие фасонное литье, клепаные и другие изделия. Применение сварных и штампо –сварных конструкций позволяет во многих случаях снизить расход материала или массу конструкции на 30—50%, уменьшить стоимость изделий в полтора-два раза.
КОНСТРУКЦИЯ СВАРНЫХ СОЕДИНЕНИЙ И РАСЧЕТ ИХ НА ПРОЧНОСТЬ
Соединение встык
Это соединение во многих случаях является наиболее простым и надежным. В зависимости от толщины соединяемых элементов его выполняют по одному из вариантов, изображенных на рис.
При малых толщинах обработка кромок не обязательна, а при средних и больших толщинах она необходима по условиям образования шва на всей толщине деталей. Автоматическая сварка под флюсом позволяет увеличить предельные толщины листов, свариваемых без обработки кромок, примерно в два раза, а угол скоса кромок уменьшить до 30—35° .
Сваривать встык можно не только листы или полосы, но также трубы, уголки, швеллеры и другие фасонные профили. Во всех случаях составная деталь получается близкой к цельной.
Соединения встык могут разрушаться по шву, месту сплавления металла шва с металлом детали, сечению самой детали в зоне термического влияния.
Зоной термического влияния называют прилегающий к шву участок детали, в котором в результате нагревания при сварке изменяются механические свойства металла. Понижение механических свойств в зоне термического влияния особенно значительно при сварке термически обработанных, а также наклепанных сталей. Для таких соединений рекомендуют термообработку и наклеп после сварки.
Практикой установлено, что при качественное выполнении при качественном выполнении сварки соединения стальных деталей происходит преимущественно в зоне термического влияния. Поэтому расчет прочности сварного соединения встык принято выполнять по размерам сечения детали в этой зоне. Возможное снижение прочности деталей, связанное со сваркой учитывают при назначении допускаемых напряжений.
Например, при расчете полосы, сваренной встык на растяжение
на изгиб
где b и s — ширина и толщина полосы; [ σ']—допускаемое напряжение для сварных соединений Отношение [σ'] к допускаемому напряжению для основного металла [σ]р является коэффициентом прочности сварного соединения встык
φ=[σ']/[σ]р.
Величина φ колеблется в пределах от 0,9 до 1,0 ,т. е. соединение встык почти равнопрочно с соединенными деталями. В тех случаях, когда требуется повысить прочность соединения, применяют косые швы .
Расчет косого шва выполняют по формуле первой, в которой принимают [σ'] = [σ]р.
Соединение внахлестку
Соединения внахлестку выполняют с помощью угловых швов . В зависимости от формы поперечного сечения различают следующие виды угловых швов: нормальные 1, вогнутые .2, выпуклые 3. На практике наиболее распространены нормальные швы.
Выпуклый шов образует резкое изменение сечения деталей в месте соединения, что является причиной повышенной концентрации напряжений. Вогнутый шов снижает концентрацию напряжений и рекомендуется при действии переменных нагрузок. Вогнутость шва достигают обычно механической обработкой, которая значительно увеличивает стоимость соединения. Поэтому такой шов применяют только в особых случаях, когда дополнительные расходы оправдываются.
Основные геометрические характеристики углового шва — катет k и высота h; для нормального шва h = k sin 45° ≈ 0,7k. По условиям технологии минимальную величину k принимают равной 3 мм, если толщина листа s ≥ 3 мм. В большинстве случаев k = s.
В зависимости от расположения различают швы: лобовые, фланговые и косые.
Лобовой шов расположен перпендикулярно ,а фланговый – параллельно линии действия нагружающей силы.
Фланговые швы накладывают параллельно линии действия силы.
Основными напряжениями флангового шва являются касательные напряжения τ в сечении m — m. Это сечение проходит через биссектрису прямого угла и является наименьшим. По длине шва напряжения τ распределены неравномерно. На концах шва они больше, чем в середине. Неравномерность распределения напряжений объясняется следующим.
Предположим, что деталь 2 абсолютно жесткая, а деталь 1 и швы упругие. Тогда относительное перемещение точек b под действием силы Р больше относительного перемещения точек a на величину удлинения детали 1 на участке ab. При этом деформации сдвига и напряжения в шве непрерывно уменьшаются по всей длине шва справа налево. Если обе детали упругие, но жесткость их различна, напряжения в шве распределяются по закону некоторой кривой. При одинаковой жесткости деталей эпюра напряжений симметрична.
Учитывая жесткость деталей, можно вычислить величину напряжений в любом сечении по длине шва. Ясно, что неравномерность распределения напряжений возрастает с увеличением длины шва и разности жесткостей деталей.
В практике длину фланговых швов ограничивают условием l ≤ 50 k. Расчет таких швов приближенно выполняют по среднему напряжению, а условия прочности записывают в виде:
Здесь 0,7 k — толщина шва в сечении по биссектрисе m — m.
В тех случаях, когда короткие фланговые швы недостаточны для выполнения условий равно прочности, соединение усиливают прорезными. Условие прочности соединения с прорезным швом при k = s
Если одна из соединяемых деталей асимметрична, расчет прочности производят с учетом доли нагрузки, воспринимаемой каждым шагом. Пример — к листу приварен уголок .Равнодействующая нагрузка Р проходит через центр тяжести уголка и распределяется по швам обратно пропорционально плечам e1 и e2 Соблюдая условие равно прочности, швы выполняют с различной длиной так, чтобы
l1/l2= e1/ e2
При этом напряжения в обоих швах равны
Если соединение нагружено моментом то напряжения от момента распределяются по длине шва неравномерно, а их направление различно. Неравно-
мерность распределения напряжений тем больше, чем больше длина шва в отношении к ширине полосы b. В общем случае максимальные напряжения на концах шва можно определить по формуле кручения
τ=M/Wp
где Wp — полярный момент сопротивления, который подсчитывают для сечения швов в плоскости разрушения .
Для сравнительно коротких швов (l < b), распространенных в практике, применяют приближенный расчет по формуле
При выводе формулы условно полагают, что напряжения направлены вдоль швов и распределены по длине швов равномерно.. При этом напряжения в двух швах образуют пару сил с плечом b, которая уравновешивает момент нагрузкиM
Лобовые швы накладывают перпендикулярно к линии действия нагрузки Р. Напряженное состояние лобового шва неоднородно. Здесь наблюдается значительная концентрация напряжений, связанная с резким изменением сечения деталей в месте сварки и эксцентричным приложением нагрузки. Основными являются касательные напряжения τ на горизонтальной плоскости и нормальные напряжения σ на вертикальной плоскости.
По методу, принятому в инженерной практике ,лобовые швы рассчитывают только по τ . За расчетное сечение, так же как и во фланговых швах, принимают сечение по биссектрисе m — m. Разрушение швов именно по этому сечению подтверждают исследования.
Для одного лобового шва
τ=Р/(0,7kl)≤[τ']
Для двух швов (нежелательная конструкция)
τ=Р/( 2·0,7kl)≤[τ']
Косой шов обычно применяют в сочетании с фланговыми. Условие прочности косого шва имеет вид
τ=Р/(0,7kl)≤[τ']
моментом M На рис. изображен случай, когда соединение одним угловым швом нагружено. При этом напряжения σ по торцу полосы будут распределяться подобно тому, как распределяются нормальные напряжения в поперечном сечении балки при
изгибе. Переходя к ранее рассмотренному условному расчету лобовых швов по касательным напряжениям, получаем
Комбинированное соединение лобовыми и фланговыми швами рассчитывают на основе принципа распределения нагрузки пропорционально несущей способности отдельных швов. При этом для соединения, изображенного на рис. получим
В приближенном расчёте полагают, что сопротивление комбинированного шва равно сумме сопротивлений составляющих швов или
,
где и - моменты, воспринимаемые фланговым и лобовым швами.
Если учесть, что по условиям равнопрочности необходимая длина фланговых шагов в комбинированном соединении не превышает , здесь модно применить формулу для определения . Для определения используем формулу и запишем . В месте пересечения швов и одно и тоже напряжение, т.е. . Обозначая это напряжение через , после подстановки и несложных преобразований получим
.
Напряжения в швах от действия силы определяют по формуле . Обозначив эти напряжения через , то получим суммарное максимальное напряжение .Оценивая соединения внахлестку, отметим, что формуле расходу материала они уступают соединениям встык, но не требуют обработки кромок.
Соединение втавр
Втавр (впритык) соединяют элементы, расположенные во взаимно перпендикулярных плоскостях. Это соединение выполняют стыковым швом с разделкой кромок или угловыми швами без
4)
разделки кромок . При нагрузке, показанной на рис .прочность соединения определяют по формулам:
для стыкового шва
для угловых швов
При выводе формулы (3.16) учтено, что напряжения от момента М распределяются по длине шва аналогично напряжениям изгиба в поперечном сечении балки. За расчетное сечение по-прежнему принято сечение по биссектрисе m — m.
На рис.показано соединение втавр, нагруженное изгибающим и крутящим моментами. Напряжения в шве от крутящего момента
В уравнении принято, что катет шва k мал в сравнении с размером детали d. При этом можно считать, что напряжения τk распределены равномерно по кольцевой площадке разрушения шва, Равной 0,7kπdср, а средний диаметр этой площадки
dср=(d+0,7k)≈d
Напряжения в шве от изгибающего момента
τи=M/Wи≈4M/(0,7kπd2).
В этой формуле Wи для сварного шва определяют по сечению условной трубы с внутренним диаметром d и толщиной стенки 0,7 k. Для такого сечения приближенно Wи≈π/4(d2срt), где dср≈d — средний диаметр, а t ≈ 0,7 k — толщина стенки.
Напряжения τk и τи в сечении m — m. взаимно перпендикулярны: τk перпендикулярно к плоскости чертежа, а τи лежит в плоскости чертежа. Поэтому суммарное напряжение
Соединение контактной сваркой
Стыковая контактная сварка при соблюдении установленных правил технологии обеспечивает равно прочность соединения и деталей, поэтому можно не выполнять специальных расчетов прочности соединения при статических нагрузках.
Это справедливо только в том случае, если разогрев металла в зоне сварки не влечет за собой снижения его прочности (например, низкоуглеродистые и низколегированные конструкционные стали, не подвергающиеся термообработке). В противном случае допускаемое напряжение при расчете деталей в месте стыка снижают с учетом уменьшения прочности материала в зоне термического влияния. При переменных нагрузках допускаемые напряжения ; понижают против статических так же, как и для стыковых соединений дуговой сваркой (см. ниже).Точечная сварка применяется преимущественно для соединений деталей из тонкого листового материала при соотношении толщин ≤3. Диаметр сварной точки выбирают в зависимости от толщины, меньшей из свариваемых деталей:
d = 1,2 s+4 мм при s ≤ 3 мм
d = 1,5 s+5 мм при s ≤ 3 мм
Минимальный шаг t ограничивается явлением шунтирования тока ранее сваренной точкой. Расстояние от кромок t1 и t2 нормируется с учетом технологических и силовых факторов. Обычно принимают:t=3d; t1=2d; t2=1,5d
Соединения точечной сваркой работают преимущественно на срез.
Где z-число сварных точек; i-число плоскостей среза. Для конструкции по рис. , а, z = 4,i = 1 , б, z = 2, i = 2. При нагружении точечных сварных соединений моментом в плоскости стыка деталей расчетную точку и ее нагрузку определяют так же как и для заклепочных соединений или соединений с болтами, поставленными без зазора .
Точечному соединению свойственно высокая концентрация напряжений. Поэтому оно сравнительно плохо работает при переменных нагрузках. Концентрация напряжений образуется не только в сварных точках, но и в самих деталях в зоне шва.
Это явление учитывают снижением допускаемых напряжений при расчете прочности деталей при переменных нагрузках .
Точечные сварные соединения часто применяют не как рабочие, воспринимающие основную нагрузку, а как связующие (крепление обшивки к каркасу, продольные швы составных штампо -сварных балок и т. п.).
Ленточная или роликовая сварка при расчетах может рассматриваться как непрерывный ряд перекрывающих друг друга точек. Напряжения среза
Исследования показывают, что концентрация напряжений в ленточных швах меньше, чем в точечных
ПРОЧНОСТЬ СВАРНЫХ СОЕДИНЕНИЯ И ДОПУСКАЕМЫЕ НАПРЯЖЕНИЯ
Прочность сварного соединения зависит от следующих основных факторов: качества основного материала, определяемого его способностью к свариванию; совершенства технологического процесса сварки; характера действующих нагрузок (постоянные или переменные нагрузки).
Хорошо свариваются низкоуглеродистые и среднеуглеродистые стали. Высокоуглеродистые стали, чугуны и сплавы цветных металлов свариваются хуже.
Значительно снижают прочность такие пороки сварки, как не провары и подрезы , шлаковые и газовые выключения, скопление металла в месте пересечения швов и т. п. Эти дефекты являются основными причинами образования трещин как в процессе сварки, так и при эксплуатации изделий.
Влияние технологических дефектов сварки значительно усиливается при действии переменных и ударных нагрузок.
Эффективными мерами повышения прочности сварных соединений являются: автоматическая сварка под флюсом и сварка в среде защитных газов; термообработка сваренной конструкции ,наклеп дробью и чеканка швов. Эти меры позволяют повысить прочность сварных соединений при переменных нагрузках в 1,5 — 2 раза и даже доводить ее до прочности целых образцов.
При точечной сварке концентрация напряжений связана с сосредоточенной передачей нагрузки в зоне сварной точки, резкими переходами сечений в этой точке и др.
Многообразие факторов, влияющих на прочность сварных соединений, а также приближенность и условность расчетных формул вызывают необходимость экспериментального определения допускаемых напряжений. Нормы допускаемых напряжений устанавливают с учетом конкретных качеств сварки и характера нагрузки швов.
Для переменных нагрузок допускаемые напряжения, взятые из табл ., понижают умножением на коэффициент γ, меньший единицы [см. формулу ], а расчет выполняют по максимальному напряжению цикла (σmax или τmax) так, как если бы это напряжение было статическим.
При переменных нагрузках рекомендуют рассчитывать прочность не только сварного шва, но и самих деталей в зоне этого шва. Допускаемое напряжение для деталей в зоне шва также умножают на коэффициент γ. Hа основе экспериментальных и теоретических исследований величину γ вычисляют по формуле
где r - σmin/σmax или r = τmin/τmax – коэффициент асимметрии цикла напряжений; Кэф — эффективный коэффициент концентрации напряжений верхние знаки при растягивающем наибольшем по абсолютной величине напряжении, нижние – при сжимающем. В переходной зоне ( r = — 1 или близко к этому) расчет ведут по более опасному случаю.
Вывод: изучив данную тему студенты усвоили материал о неразъемном соединении, электрической сварке, дуговой, контактной, сварке под слоем флюса, соединении встык, прочность, швы.
Контрольные вопросы:
1. Как образуется сварное соединение?
2. На какие два основных вида делят электросварку?
3. На чем основана электродуговая сварка?
4. Что называют зоной термического влияния?
5. От чего зависит прочность сварных соединений?
6. Какие меры принимаются для повышения прочности сварных соединений?
{/spoilers}