Транспортные машины на карьерах Исполнитель
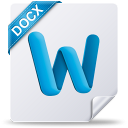
- Скачано: 71
- Размер: 894.5 Kb
Транспортные машины на карьерах используют для перемещения различных грузов. Грузы на карьерах подразделяются на основные и вспомогательные. К основным относят полезное ископаемое и вскрышные породы.
{spoiler=Продолжать Читать}
К вспомогательным – оборудование, взрывчатые вещества и горюче-смазочные материалы, запасные части и др. Основной объем грузоперевозок приходится на вскрышные породы и полезное ископаемое.
Для перевозки основных грузов на карьерах наибольшее распространение получили три вида транспорта: железнодорожный, автомобильный и конвейерный. Кроме того, применяют гидравлический транспорт, транспорт канатными подвесными дорогами, при помощи скиповых подъемных установок, иногда используют кабель-краны. К транспортным установкам относятся также питатели, дозаторы, затворы, используемые в транспортных комплексах для механизации погрузочных, перегрузочных и разгрузочных работ.
Горную массу на всем протяжении трассы можно перемещать одним видом транспорта или несколькими с перегрузкой с одного на другой. В последнем случае транспорт называют комбинированным. Наиболее распространены комбинации автомобильно-железнодорожного и автомобнльно-конвейерного транспорта, при которых в карьере от экскаватора до перегрузочного пункта горную массу перевозят автосамосвалами, а подъем из карьера и дальнейшее транспортирование осуществляют железнодорожным транспортом или ленточными конвейерами.
Железнодорожный транспорт наиболее выгодно использовать на карьерах средней и большой производительности с объемом перевозок от 10 до 100 млн. т горной массы в год при расстояниях транспортирования от 3 до 12 км. Наилучшие технико-экономические показатели при применении железнодорожного транспорта достигаются при большом сроке службы карьера и глубине до 160 м. Достоинство железнодорожного транспорта – независимость эффективности его работы от климатических условий.
Автомобильный транспорт используют на карьерах с годовой производительностью от 5 до 10 млн. т горной массы при расстояниях транспортирования от 1,5 до 3 км и глубине карьера до 150 м. Применение автосамосвалов грузоподъемностью более 100 т также эффективно на карьерах с годовой производительностью до 70 млн. т горной массы. Автомобильный транспорт целесообразно использовать в районах с сухим климатом и малым количеством дождевых осадков.
Конвейерный транспорт применяют на карьерах с годовой производительностью более 30 млн. т горной массы при глубине карьера более 150 м и расстояниях транспортирования 2,5 – 3 км. При использовании конвейерного транспорта внутри и за пределами карьера длина конвейерных линий может достигать 10 – 20 км. Фактором, ограничивающим применение конвейерного транспорта, является крупность транспортируемого груза. Ленточные конвейеры не рекомендуется использовать для транспортирования грузов крупностью более 400 мм, так как при этом быстро изнашивается лента. Кроме того, конвейерный транспорт нерационально применять для перемещения сильно увлажненных рыхлых пород, налипающих и намерзающих на конвейерную ленту. При низких температурах эффективность конвейерного транспорта резко снижается.
Транспортные комплексы
Транспортным комплексом называют управляемую систему транспортных машин, установок и вспомогательного оборудования (перегрузочные, погрузочные, разгрузочные устройства, средства диспетчеризации и автоматизации), предназначенную для перемещения насыпных грузов по определенной трассе в заданном направлении.
Выбор машин и оборудования, входящих в транспортный комплекс, зависит от типа погрузочной машины (обычно экскаватора), от характеристики груза и величины грузопотока, а также от ряда других факторов, которые будут рассмотрены далее.
Так, например, при разработке рыхлых пород экскаваторами непрерывного действия транспортные комплексы обычно состоят из нескольких последовательно установленных конвейеров, технологически связанных общим грузопотоком. Последним звеном такого комплекса может быть отвалообразователь. Передачу грузопотока с одной машины на другую осуществляют при помощи различных перегружателей, перегрузочных тележек, самоходных бункеров и т. д., которые иногда образуют не только технологическую, но и кинематическую связь между стыкующимися машинами.
Наиболее сложные комплексы используют при обслуживании грузопотока одного направления различными видами транспортных машин. Например, широкое распространение при разработке скальных пород и руд получил комплекс, в состав которого входит автотранспорт, осуществляющий перевозку горной массы от одноковшового экскаватора до перегрузочного пункта на подъемный ленточный конвейер. Перегрузочный пункт включает в себя бункер, питатели, дробилку, конвейеры небольшой длины (3 – 5 м) для подбора просыпающегося при перегрузке мелкого материала. Подъемный конвейер передает горную массу на магистральный или отвальный конвейеры, а последний – на отвалообразователь.
В комплексы железнодорожного транспорта кроме подвижного состава входит оборудование для механизации погрузочных и разгрузочных работ: бункеры, маневровые устройства, опрокидыватели и т.д.
Производительность транспортных машин
Производительностью транспортной машины называют количество груза, прошедшее через любое неподвижное поперечное сечение грузонесущего органа за единицу времени. Существуют понятия мгновенной производительности, минутной, часовой, сменной, суточной и т. д.
Мгновенная производительность Qм определяется из выражения
Qм=ΔG / Δt
где ΔG – приращение груза за весьма малый промежуток времени Δt.
Другие понятия производительности соответствуют ее среднему значению за соответствующие промежутки времени. Количество груза измеряют либо в единицах объема (м3), либо в единицах массы (т).
Производительность транспортных машин непрерывного действия определяют по формуле
Q = mv
где т – масса груза, приходящаяся на 1 м длины грузонесущего органа транспортной машины; v – скорость движения грузонесущего органа.
Производительность транспортных машин цикличного действия определяют по формуле
Q = G/T
где G – грузоподъемность машины (кузова автосамосвала или состава вагонов);
Т – время полного цикла (рейса).
Продолжительность полного цикла (рейса) определяется затратами времени на загрузку состава или кузова tз, движение с грузом tг, разгрузку tp, движение порожняком tп и маневровые операции tм, т. е.
Основные узлы и элементы транспортных машин и их параметры
Транспортные машины перемещают грузы в грузонесущих элементах, в качестве которых используют емкости различной формы в виде лотков, пластин и труб.
В процессе транспортирования груз может перемещаться вместе с грузонесущими элементами (например, в кузовах вагонов, автосамосвалов, в вагонетках канатных дорог, на конвейерных лентах) либо относительно неподвижного грузонесущего элемента (по наклонным лоткам, в трубах и т. д.). Основными параметрами грузонесущих элементов в виде емкостей являются: грузоподъемность – масса груза, которую можно поместить в грузонесущем элементе; вместимость – объем груза, который можно разместить в грузонесущем элементе, и геометрические размеры, в том числе габариты.
Грузонесущие элементы в виде лент, желобов, наклонных лотков характеризуются шириной, формой лотка и массой грузонесущего элемента длиной 1 м.
Параметры грузонесущих элементов в виде труб – диаметр поперечного сечения и его площадь (для труб с круглым сечением), а также площадь, ширина и высота сечения (для труб с прямоугольным сечением).
Тяговые органы в транспортных машинах служат для передачи тягового усилия от привода к грузонесущему элементу или непосредственно к грузу для его перемещения.
Наиболее широко распространены следующие виды тяговых органов: колесные, ленточные, канатные и цепные. В установках трубопроводного транспорта перемещение груза осуществляется в жидкой или газообразной среде и роль тягового органа выполняет жидкость (как правило, вода) или сжатый газ (например, воздух). В транспортных машинах с колеблющимся или вибрирующим грузонесущим элементом тяговый орган отсутствует и перемещение груза осуществляется посредством передачи колебаний или вибраций грузонесущего элемента непосредственно грузу.
В некоторых транспортных машинах грузонесущий элемент и тяговый орган совмещены, в других – они разделены и каждый выполняет свою функцию.
Колесные тяговые органы используют в локомотивах и в автосамосвалах.
Колесами с жесткими ободами оборудуют подвижной состав железнодорожного транспорта, а колесами с эластичными пневмошинами – автосамосвалы и автопоезда.
Основной параметр тяговых колес – радиус качения rк. У колес с жесткими ободами он мало изменяется в процессе взаимодействия колеса с рельсом из-за малой деформации обода и практически равен номинальному радиусу колеса. Радиус качения колес с пневмошинами может значительно отличаться от номинального вследствие деформации шин при взаимодействии с дорожным покрытием, причем эта деформация тем больше, чем больше загружен автосамосвал.
Ленточные тяговые органы представляют собой различные конвейерные ленты. На карьерных конвейерах используют ленты с тканевыми прокладками и с основой из параллельно расположенных стальных тросов.
Основные параметры конвейерных лент – ширина, разрывное усилие и масса 1 м ленты. Для карьерных ленточных конвейеров приняты следующие значения ширины лент: 1000, 1200, 1600, 2000 мм. На некоторых конвейерах применяют ленту шириной 1800 мм, а в будущем предполагается использование лент шириной 2500 и 3000 мм. Прочность конвейерных лент оценивается по разрывному усилию, отнесенному к 1 мм ширины прокладки для резинотканевых лент или к 1 мм ширины ленты для резинотросовых. Масса 1 м ленты зависит от ее ширины и прочности и изменяется от 15 до 130 кг
Приводные барабаны и шкивы используют в транспортных машинах, оборудованных гибкими тяговыми органами: конвейерными лентами или тяговыми канатами. Основные параметры приводных барабанов – диаметр и ширина обечайки, а основной параметр приводного шкива – его диаметр. В некоторых расчетах необходимо учитывать массу барабана или шкива.
Транспорт для подземной разработки
При подземной разработке полезных ископаемых внутренний транспорт в зависимости от места расположения разделяют на забойный – для перемещения полезного ископаемого в пределах очистного забоя; участковый – для перемещения полезного ископаемого по участковым выработкам; магистральный – для перемещения от участковых транспортных средств до околоствольного двора; подъем – для перемещения полезного ископаемого от околоствольного двора до поверхности. При подземной разработке руд перемещение рудной массы от забоя очистной выемки до откаточного горизонта называют доставкой.
В зависимости от вида перемещаемых грузов внутренний подземный транспорт разделяют на основной, предназначенный для транспортирования полезного ископаемого и породы, и вспомогательный – для транспортирования оборудования, различных материалов и людей.
Транспортные машины, используемые на горнодобывающих предприятиях, можно классифицировать по следующим признакам: принципу действия, способу перемещения груза, конструкции тягового органа и др.
По принципу действия транспортные машины разделяют на установки непрерывного действия, перемещающие грузы непрерывным потоком с загрузкой и разгрузкой при движении рабочего органа, и периодического действия, загрузку и разгрузку которых производят при полной их остановке или на малой скорости. Работа транспортных машин периодического действия характеризуется периодами во времени (циклами).
По способу перемещения груза различают транспортные установки, на которых груз транспортируют по почве, неподвижным наклонным желобам или трубам под действием собственного веса (гравитации); по почве или желобам принудительным волочением; на подвижных грузонесущих элементах, например, в кузове вагонетки, ленте конвейера, ковше погрузочно-транспортной машины и др.; на качающихся или вибрирующих желобах силами инерции; по неподвижным трубам или желобам в водной среде или неподвижным трубам в рабочей воздушной среде.
По конструкции тягового органа различают транспортные установки с гибким тяговым органом (лентами, канатами или цепями); с приводными колесами, взаимодействующими с рельсовыми путями, почвой или дорожным покрытием; гусеничные механизмы, взаимодействующие с почвой. В некоторых транспортных установках тяговый орган отсутствует (гидро- и пневмотранспортные установки, качающиеся и вибрационные конвейеры, установки гравитационного транспорта).
На горнодобывающих предприятиях применяют различные конструкции транспортных машин. При подземной разработке полезных ископаемых для их перемещения широко используют гравитационные транспортные установки, рельсовый транспорт, скребковые, ленточные и другие типы конвейеров, самоходные погрузочные и погрузочно-транспортные машины и автомобильный транспорт, гидро- и пневмотранспортные установки. Для транспортирования различных вспомогательных грузов и людей используют канатную откатку, подвесные монорельсовые и канатные дороги, самоходные машины. К транспортным машинам относятся также различное вспомогательное оборудование: питатели, затворы, толкатели, вагоноопрокидыватели, лебедки и др.
Рудничный транспорт располагает большим количеством оборудования транспортных средств, предназначенных для механизации маневровых, загрузочных и разгрузочных работ, для аккумулирования груза в местах перегрузок с одних транспортных средств на другие, для очистки шахтных вагонеток и рельсовых путей, для дистанционного управления, автоматизации, сигнализации и др.
Перемещение грузов с помощью конвейеров и скреперов принято называть доставкой, перемещение грузов по рельсовым путям – откаткой, а по наклонным выработкам с углом наклона свыше 30° и по вертикальным выработкам – подъемом. На угольных шахтах основными видами транспорта по горным выработкам являются рельсовый и конвейерный. На рудных шахтах обычно применяется рельсовый, конвейерный и скреперный транспорт. По горизонтальным выработкам грузы перемещаются конвейерами и электровозами по рельсовым путям, по наклонным выработкам – конвейерами и лебедками по рельсовым путям.
Многообразие применяемого транспортного оборудования и сложность схем транспорта объясняются разнообразием горногеологических условий, способов вскрытия и систем разработки месторождений.
В зависимости от условий залегания угольных пластов различают три основные схемы подземного транспорта: при наклонном и крутом падении пластов, при горизонтальном залегании и при пологом залегании пластов. Схема подземного транспорта складывается из транспортировки вдоль очистного забоя, из забоев подготовительных выработок, по промежуточным штрекам, по наклонным и главным откаточным выработкам, в околоствольных дворах и на стыках транспортных участков.
Транспорт для открытой разработки
При добыче полезных ископаемых открытым способом применяется железнодорожный, автомобильный, конвейерный, комбинированный и гидравлический транспорт, подвесные канатные дороги.
Транспортирование горной массы от забоя до пунктов перегрузки на поверхности горного предприятия осуществляют одним или несколькими видами транспортных машин с перегрузкой в процессе транспортирования с одного вида транспортных машин на другой. Цепь взаимосвязанных и управляемых транспортных машин и механизмов, включающих перегрузочные пункты, средства диспетчеризации и автоматизации и обеспечивающих надежное перемещение грузов в заданном направлении, называют транспортными комплексами. На открытых работах транспортный комплекс, включающий несколько видов транспортных машин, называют комбинированным транспортом, например, автомобильно-железнодорожный или автомобильно-конвейерный транспорт.
Характеристика грузов.
На горных предприятиях при добыче полезных ископаемых перемещают насыпные и штучные грузы. К насыпным грузам относятся полезное ископаемое, породы, закладочные материалы, а к штучным – грузы в контейнерах, машины, элементы крепи, различное оборудование, а также люди.
Наиболее распространенными являются насыпные грузы, основные характеристики которых – кусковатость, плотность, угол естественного откоса.
Кусковатость насыпного груза характеризуется количественным распределением кусков (частиц) по крупности в отбитой горной массе. Крупность куска определяется его наибольшим размером (одним из трех по взаимно-перпендикулярным направлениям).
В зависимости от размеров кусков различают насыпные грузы: рядовые, если отношение максимального размера куска к минимальному равно или более 2,5, и сортированные, если это соотношение менее 2,5.
По размеру куска d насыпные грузы (кроме крепких руд) разделяют на крупнокусковые (d > 160 мм); среднекусковые (d = 60 ÷ 160 мм), мелкокусковые (d = 10 ÷ 60 мм), зернистые ( d = 0,5 ÷ 10 мм), порошкообразные (d = 0,05 ÷ 0,5 мм), пылевидные (d < 0,05 мм).
Отбитую руду, содержащую куски размером d = 100 мм и менее, называют рудной мелочью, размером d = 100 ÷ 300 мм – среднекусковой, а при d = 300 ÷ 600 мм – крупнокусковой. Максимально допустимый размер куска руды, который можно перемещать данным видом транспорта, называют кондиционным куском, а кусок руды, превышающий по размерам кондиционный, называют негабаритом.
Плотность горной массы – это масса 1 м3 в целике γц (т/м3) или в насыпке γ (т/м3). Плотность в насыпке разрыхленного угля γ = 0,9÷1,0 т/м3, руды γ=1,8 ÷ 3,5 т/м3, вскрышных пород γ= 1,2 ÷ 2,0 т/м3. Отношение γц/γ = кp – к оэффициент разрыхления горной массы. Для мягких пород кр= 1,1 ÷ 1,3, для крепких пород и руд кр= 1,4 ÷ 1,8.
Угол естественного откоса разрыхленной горной массы – это угол наклона между боковой поверхностью конуса свободно насыпанной горной массы и горизонтальной плоскостью, на которой лежит насыпанная горная масса. Различают угол естественного откоса горной массы в покое φп (лежащей на неподвижной плоскости), и угол естественного откоса горной массы в движении φд (перемещаемой транспортной машиной). Угол φд<φп, так как при транспортировании горной массы происходит ее ворошение или встряхивание. Для угля φд=15 ÷ 20°; для крепких руд φд = 30 - 35°.
Кроме того, горная порода характеризуется коэффициентом крепости по шкале проф. М.М. Протодьяконова абразивностью, влажностью, липкостью и др.
Основные характеристики штучных грузов, транспортируемых раздельно или в упаковке (контейнерах, кассетах, пакетах) – габариты, форма и масса.
Количество груза, выраженное в т или м3, перемещаемое в единицу времени (смену, сутки, год), называют грузооборотом. На горных предприятиях большую часть грузооборота составляет транспортирование полезного ископаемого. Грузооборот характеризует проектную мощность горного предприятия.
Необходимая производительность транспортных машин определяется грузопотоком, т. е. количеством груза (в т или м3), транспортируемым по определенной трассе в единицу времени. На горных предприятиях основным грузопотоком является грузопоток полезного ископаемого и породы в направлении от забоя до поверхности шахты или карьера (прямой грузопоток), а вспомогательным – грузопоток оборудования, стройматериалов и людей, большая часть которого направлена с поверхности в забой (обратный грузопоток).
В связи со сложными горно-геологическими условиями добычи, изменением режимов работ выемочных машин, организационными факторами величина грузопотка значительно изменяется во времени. Степень изменения грузопотока характеризуется коэффициентом неравномерности кн равным отношению максимального грузопотока Qmax в единицу времени (т/ч или т/мин) к среднему грузопотоку Qcp, т. е. кн = (Qmax/Qcp) > l Величина коэффициента неравномерности грузопотока в шахтных условиях в зависимости от различных факторов изменяется от 1,25 до 2,0.
Для сглаживания неравномерности грузопотока применяют промежуточную бункеризацию горной массы, т. е. в транспортной линии устанавливают аккумулирующие емкости (бункера, перегрузочные пункты и др.).
Величина грузопотока в угольных шахтах достигает 2 – 3 тыс. т/ч, в рудных шахтах 6 – 8 тыс. т/ч, в карьерах при транспортировании мягких вскрышных пород 20 – 25 тыс. т/ч.
Технологические схемы рудничного транспорта.
Транспортные машины на горных предприятиях эксплуатируются в сложных и тяжелых условиях, к которым относятся: необходимость частой передвижки по мере перемещения фронта горных работ, большая кусковатость транспортируемых насыпных грузов и их абразивность, возникновение внезапных перегрузок, а в шахтных условиях – сесненность рабочего пространства, влажность и химическая активность шахтных вод, взрывоопасность рудничной атмосферы, высокая температура на больших глубинах и др. Поэтому транспортные машины должны иметь повышенную надежность и безопасность, приспособленность к дистанционному и автоматизированному управлению, обеспечивать заданную производительность при высоких технико-экономических показателях.
Соблюдение этих условий возможно только при правильном выборе видов и типов транспортных машин с учетом горно-геологических и горнотехнических условий их эксплуатации, т.е. правильным выбором технологической схемы рудничного транспорта.
Технологической схемой рудничного транспорта называют графическое изображение горных выработок или трассы транспортирования с указанием в этих выработках или по трассе видов и типов транспортных машин, длины транспортирования и размеров грузопотоков.
В зависимости от условий эксплуатации для каждого горного предприятия или группы предприятий характерна своя рациональная схема транспорта, которая должна включать наиболее прогрессивные транспортные машины и полную взаимную увязку средств транспорта отдельных звеньев схемы.
Основным показателем технико-экономической эффективности технологической схемы рудничного транспорта является минимум приведенных затрат на 1 т (м3) транспортируемого груза.
В шахтных условиях схема подземного транспорта определяется такими основными факторами, как схема вскрытия, способ подготовки, система разработки, угол падения пласта.
На большинстве отечественных угольных шахт, разрабатывающих горизонтальные, пологие и наклонные пласты с углом падения до 18°, применяют в основном комбинированные схемы транспорта, включающие конвейерный транспорт на участковых горизонтальных и наклонных выработках, на магистральных наклонных выработках и локомотивный рельсовый транспорт по главным горизонтальным выработкам. Конвейерный транспорт наиболее широко используют при панельном способе подготовки шахтного поля и системе разработки длинными столбами с отработкой обратным ходом, при этом возможна отработка столбов единичными или спаренными лавами. Схема конвейерного транспорта от лавы до пункта погрузки локомотивной откатки может иметь два варианта: расположенный под лавой надвижной перегружатель с перегрузкой угля на обычный ленточный конвейер, или расположенный под лавой хвостовой перегружатель с перегрузкой угля на укорачивающийся телескопический конвейер. На рис. 1 показана схема транспорта угольной шахты при разработке трех пологих пластов. На всех выемочных участках шахты транспортирование угля осуществляется ленточными конвейерами. По мере подвигания очистных забоев для укорачивания конвейерных линий под лавами 1, 2, 5, 6 – 8 установлены перегружатели (скребковые разборные конвейеры), а под лавами 3 и 4 – телескопические конвейеры со скребковыми перегружателями.
С ленточных панельных конвейеров уголь перегружается на уклонные конвейеры и далее на магистральный локомотивный транспорт.
В качестве вспомогательного транспорта по ярусным штрекам используют локомотивную откатку (лавы 1, 2, 5 и 6) или монорельсовые дороги с канатной тягой (лавы 3 и 4), а по панельным наклонным вспомогательным выработкам – одно-концевую канатную откатку (панели I, II и IV) или монорельсовую дорогу (панель III).
Наиболее прогрессивное направление на угольных шахтах, разрабатывающих пологие пласты, полная конвейеризация транспорта угля от очистных забоев до пункта погрузки угля в железнодорожные вагоны на поверхности. В качестве вспомогательного транспорта применяют монорельсовые дороги с локомотивной или канатной тягой.
На угольных шахтах, разрабатывающих пласты крутого падения, для транспортирования угля и вспомогательных грузов применяют в основном локомотивную откатку.
При подземной разработке камерно-столбовыми системами или длинными очистными забоями некрепких руд обычно применяется полная конвейеризация транспорта от забоя до около ствольного двора.
На шахтах по добыче некрепких марганцевых руд при системах разработки длинными столбами с заходками руда в заходках, по выемочным и аккумулирующим штрекам доставляется обычно ленточными конвейерами до погрузочного пункта локомотивной откатки. Возможна полная конвейеризация транспорта марганцевых руд от забоя до поверхности.
При подземной разработке крепких руд черных и цветных металлов, горно-химического сырья схема транспорта зависит от залегания рудного тела и системы разработки. При разработке горизонтальных, слабонаклонных и наклонных до 40° рудных тел доставка руды в очистном забое осуществляется по следующим возможным схемам: погрузка взорванной руды погрузочными машинами, экскаваторами или погрузчиками в автосамосвалы или самоходные вагоны, которые доставляют руду до рудоспусков с последующей ее перегрузкой в вагоны локомотивной откатки и транспортированием до околоствольного двора; доставка руды погрузочно-транспортными машинами до рудоспусков и далее, транспорт руды локомотивной откаткой; доставка автосамосвалами от забоя до околоствольного двора или от забоя на поверхность по наклонному стволу.
При подземной разработке крутопадающих рудных залежей отбитая взрывом руда выпускается самотеком (гравитационный выпуск) на подэтажные или откаточные выработки, при этом возможен донный (площадный) или торцевой (слоевой) выпуск руды.
На рис. 2, a – д показаны схемы доставки при донном выпуске руды. Руда из воронок 1 выпускается самотеком через односторонние или двусторонние выпускные выработки (дучки) 2 на почву доставочной выработки 3, в которой из руды образуется насыпь 4. Руда из насыпи 4 по почве выработки 3 доставляется до рудоспуска 5 скреперной установкой 6, погрузочно-транспортной машиной 7 или питателем 8 и конвейером 9. С целью улучшения истечения руды в дучках устанавливают вибрационные питатели 8, с которых руда поступает на почву выработки 3, на конвейер, в рудоспуск или в вагонетки 10 локомотивной откатки.
При торцевом выпуске руды (рис. 3) наиболее широко применяются доставка погрузочно-транспортными машинами или комплексами; погрузочная машина – автосамосвал или самоходный вагон.
При подземной добыче крепких руд наиболее распространенным транспортом по откаточным выработкам является локомотивная откатка до околоствольного двора, где руда подвергается дроблению и доставляется на поверхность по вертикальным стволам в скипах или реже по наклонным стволам ленточными конвейерами.
12.13.14. КОНВЕЙЕРНЫЙ ТРАНСПОРТ
Общие сведения
Несмотря на сравнительно небольшие объемы горной массы, которые перемещают на открытых разработках с применением конвейерного транспорта, его без оснований считают весьма перспективным. Конвейерный транспорт обеспечивает непрерывность грузопотока и поэтому может эффективно использоваться с добычными машинами непрерывного действия (роторными и многоковшовыми, цепными экскаваторами).
Достоинством конвейерного транспорта является высокая, практически любая требующаяся производительность. В настоящее время известны конвейеры, имеющие производительность до 30 000 т/ч и работающие в комплексе с несколькими роторными экскаваторами. В отличие от железнодорожного и автомобильного транспорта конвейеры можно использовать при больших углах наклона трассы (до 18 – 20°). При этом значительно уменьшаются затраты на горно-капитальные работы по подготовке трассы, поэтому конвейерный транспорт выгодно применять при весьма больших грузопотоках (от 20 млн. т горной массы в год и выше) и при значительной (более 100 м) глубине карьера. Применение конвейерного транспорта приводит к заметному росту производительности труда при транспортировании, так как этот вид транспорта легко автоматизируется. Статистика показывает, что, по сравнению с железнодорожным и автомобильным транспортом, конвейерный транспорт наиболее безопасен.
К недостаткам конвейерного транспорта следует отнести требование строгой прямолинейности трассы в плане, малый срок службы конвейерной ленты, на долю которой приходится от 20 до 40% стоимости всей конвейерной установки. Кроме того, он обладает более высокой энергоемкостью перемещения груза по сравнению с железнодорожным транспортом. Конвейерный транспорт чувствителен к характеру перевозимого груза.
Обычными ленточными конвейерами, получившими наибольшее распространение на открытых разработках, можно перемещать грузы крупностью до 300 – 400 мм. Транспортирование липких, сильно увлажненных грузов связано с трудностями, возникающими при очистке ленты после разгрузки.
Схемы карьерного конвейерного транспорта
Схемы карьерного конвейерного транспорта отличаются большим разнообразием, так как они в значительной мере зависят от горно-геологических условий залегания полезного ископаемого и от принятой технологии разработки месторождения. Однако по уровню конвейеризации они могут быть разделены на две группы: с полной конвейеризацией транспортирования горной массы от выемочного забоя до породного отвала или пункта отгрузки полезного ископаемого на поверхности карьера и с частичной конвейеризацией транспортирования горной массы, когда конвейеры используются только на некоторых звеньях транспортной цепи.
В свою очередь, при полной конвейеризации транспортирования вскрышных пород можно выделить три основные группы схем, которые классифицируются по направлению перемещения горной массы.
Первую группу схем (рис. 2) с перемещением вскрышных пород в выработанное пространство поперек линии фронта выемочных пород применяют при относительно небольшой мощности вскрышных пород, объемы которых можно разместить внутри карьера. При этом для транспортирования пород используют транспортно-отвальные мосты (рис.2,а), отвалообразователи (рис.2,б), перегружатели или комбинации тех и других (рис.2, в), основным элементом которых являются ленточные конвейеры. Существуют конструкции, в которых роторный или цепной многоковшовый экскаватор объединен с транспортно-отвальным мостом в единый агрегат (рис.2, г).
Если необходимо произвести буровзрывные работы для подготовки горной массы к транспортированию (крепкие вскрышные породы) и погрузку осуществляют с использованием одноковшовых экскаваторов, то перед погрузкой горной массы на ленточный конвейер отбирают негабарит при помощи передвижного грохота (рис.3,а) либо дробят его передвижными или самоходными дробильными агрегатами (рис.3, б).
Вторая группа схем (рис.4) предусматривает перемещение вскрышных пород во внутренний отвал по периметру карьера. Эти схемы универсальнее, так как позволяют размещать внутренние отвалы на более обширной площади. На рис. 19.4 приведен пример схемы транспортирования при разработке вскрышной породы и бурого угля экскаваторами непрерывного действия на буро-угольном разрезе. Роторный экскаватор 2 через загрузочное устройство 1 грузит вскрышную породу на забойный конвейер 3, с которого она поступает на бортовый передаточный конвейер 4 и затем на отвальный конвейер 5, откуда в промежуточной точке с помощью двухбарабанной разгрузочной тележки 6 сгружается на приемную консоль отвалообразователя 7 и укладывается во внутренний отвал. Уголь цепным экскаватором нижнего черпания 8 грузится на забойный конвейер 9 и затем передается межуступным перегружателем 10 на бортовые передаточные конвейеры 11 и далее поступает на магистральный конвейер 12. Забойные конвейеры вскрышных и угольных уступов, а также отвальные являются передвижными и перемещаются параллельно фронту очистных работ. Передаточные конвейеры могут быть передвижными или стационарными. В случае применения передвижных конвейеров они перемещаются вдоль своей продольной оси. Стационарные конвейеры периодически наращиваются или сокращаются. При разработке скальных вскрышных пород в забое устанавливают передвижной грохот для отбора негабарита или самоходный дробильный агрегат, после которых горная масса поступает на конвейерную линию.
15.16.17.18. 19. Принципиальная схема скребкового конвейера
Принципиальная схема скребкового конвейера представлена на рис. 1. Конструкция скребкового конвейера включает тяговый орган 1, на котором закреплены скребки 2, рештачный став 3, приводную станцию 4 и натяжную станцию 5. Рабочей может быть верхняя ветвь (рис.1, а) или реже – нижняя ветвь (рис. 1, б). При движении тягового органа горная масса, загружаемая на скребковый конвейер в любой точке по его длине, перемещается скребками волочением по желобам рештачного става 3 или по направляющим, уложенным на почве. Разгрузка горной массы происходит в головной части конвейера (рис. 1, а) млн перед приводной звездочкой (рис. 1, б).
Наиболее широкое распространение получили скребковые конвейеры с верхней рабочей ветвью для доставки угля и горючих сланцев в очистных забоях с пластами мощностью 0,55 м и более, с углами падения по простиранию до 35°, а также при машинной выемке калийных руд для их доставки по очистному пространству.
В зависимости от выполняемых функций различают доставочные, агрегатные и тормозные скребковые конвейеры. Доставочные конвейеры выполняют только транспортные функции. Агрегатные конвейеры входят в состав выемочных комплексов или агрегатов. Став агрегатного конвейера используется в качестве направляющих для перемещения выемочной машины. Тормозные скребковые конвейеры иногда применяют для ограничения скорости движения угля при его спуске вниз под большими углами наклона. По способу перемещения конвейеров в забое различают конвейеры переносные разборные, перемещаемые отдельными частями (обычно вручную), и передвижные неразборные, перемещаемые гпдропередвпжчиками.
Скребковые конвейеры применяются также в некоторых транспортных установках, например, перегружателях, предназначенных для перегрузки угля на другие транспортные средства (конвейеры или самоходные вагоны), в перегрузочных машинах, механизированных бункерах.
Преимущества скребковых конвейеров: высокая производительность, надежность работы на трассе с небольшими искривлениями в вертикальной и горизонтальной плоскостях, возможность загрузки в любой части по длине конвейера, простота удлинения и укорачивания рештачного става, малые габариты линейной части по высоте.
Недостатки скребковых конвейеров: несовершенство принципа транспортирования горной массы волочением, что вызывает износ тяговых цепей и рештаков, высокий расход энергии, большая металлоемкость, измельчение транспортируемого груза, что влечет за собой в некоторых случаях ухудшение его сортности (например, угля).
Производительность современных забойных конвейеров 120 – 600 т/ч, длина по горизонтали до 300 м в одном ставе, суммарная мощность приводных станций одного конвейера до 330 кВт.
Основные элементы скребкового конвейера.
Основные элементы скребкового конвейера: тяговый орган со скребками, рештачный став, приводная станция и натяжное устройство.
В качестве тягового органа скребкового конвейера применяют одну или две круглозвенные, реже – разборные цепи. На коротких скребковых конвейерах, например используемых в днищах кузовов самоходных вагонов, применяют пластинчатые цепи.
Круглозвенные цепи (рис. 2, а) изготавливают электросваркой из стального прутка диаметром 14 – 28 мм с шагом t от 50 до 100 мм, с разрывной прочностью 230 – 750 кН. Круглозвенные цепи по сравнению с другими типами цепей обеспечивают пространственную гибкость, что позволяет использовать их на передвижных изгибающихся конвейерах. Они обеспечивают возможность передвижки конвейера без разборки рештачного става и сравнительно простое крепление скребков к звеньям цепи.
Разборная цепь (рис. 2, б) состоит из внутреннего звена 1, наружного звена 2 и валика 3. Все элементы разборной цепи изготовляются штамповкой без последующей механической обработки. Недостаток разборных цепей по сравнению с круглозвенными – значительно меньшая прочность при одинаковой линейной массе и возможность самопроизвольного рассоединения.
Цепь приводится в движение приводной звездочкой (рис. 2, в), вращающейся со скоростью (м/с) vзв = ωR, где ω — частота вращения звездочки, с-1; R — радиус начальной окружности звездочки, м.
При постоянной частоте вращения цепь движется неравномерно, так как ее звенья ложатся не на окружность постоянного радиуса, а на стороны многоугольника, в связи с чем периодически изменяется мгновенный радиус навивки цепи на приводную звездочку.
Скребки выполняют штампованными или коваными и закрепляют на тяговых цепях с помощью специальных соединительных звеньев. В двухцепных скребковых конвейерах скребки своими концами закреплены на цепях, которые перемещаются в направляющих пазах рештачного става (рис. 3, а), или скребки закреплены на сдвоенных, вынесенных из направляющих пазов цепях (рис.3, б). Шаг крепления скребков к тяговым цепям составляет 640 – 1024 мм.
Став скребкового конвейера состоит из отдельных унифицированных рештаков, штампованных или сварных желобов длиной 1 – 2,5 м, соединяемых между собой с помощью проушин с болтами или специального стержня с элементами соединения (безболтовое соединение).
Конструкции узлов соединения рештаков в передвижных скребковых конвейерах позволяют рештакам изгибаться относительно друг друга в вертикальной и горизонтальной плоскостях в пределах ±3°.
Сварные рештаки (рис. 3, а и б) состоят из двух профильных боковин и днища, разделяющих верхнюю грузовую и нижнюю порожнюю ветви тягового органа. В других конструкциях скребковых конвейеров штампованные рештаки укладывают один над другим, образуя открытый желоб для верхней ветви и закрытый для нижней ветви (рис. 3, в) или укладывают горизонтально, образуя два параллельных желоба (например, в скребковых конвейерах, применяемых для доставки угля при отработке тонких пластов).
20. 21. Общие сведения пластинчатого конвейера
Пластинчатые конвейеры в последние годы получают все большее применение па угольных шахтах для транспортировки полезного ископаемого, пустой породы и закладочного материала, а также для доставки материалов и оборудования. С помощью пластинчатых конвейеров можно транспортировать груз вверх при угле наклона до 28° и вниз при угле наклона до 22°. При установке на полотне поперечных перегородок груз можно транспортировать на подъем до 40 – 45°.
Пластинчатый конвейер (см. рис. 5) состоит из тягового органа, несущего полотна, опорных конструкций, приводной головки, натяжного и разгрузочного устройств.
Тяговым органом пластинчатых конвейеров является круглозвенная или пластинчатая цепь. По числу тяговых цепей конвейеры бывают одно- и двухцепными. Круглозвенные цепи (рис. 5, а) применяется на конвейерах, которые устанавливаются в криволинейных выработках, как имеющие большую гибкость во всех направлениях. Они изготовляются отрезками, которые при монтаже соединяются специальными звеньями 5. Пластинчатые тяговые цепи (рис. 5, б) состоят из пластин, пальцев и самотормозящих шайб. Они обладают гибкостью только в одной плоскости и поэтому применяются преимущественно для конвейеров, устанавливаемых в горизонтальных выработках. Преимуществом пластинчатых цепей является возможность разборки ее в любом месте става.
Несущее полотно 2 конвейера (см. рис. 5) состоит из несущих пластин и ходовых роликов. Пластины штампуются из листовой стали толщиной 2 – 3 мм. Для придания им жесткости на поверхности выштамповываются ребра жесткости. Пластины несущего полотна сопрягаются между собой встык или внахлестку. При сопряжении встык зазор между пластинами перекрывается гибкой резиной, а при сопряжении внахлестку концы отбортовываются в разные стороны или им придается полукруглая форма. По профилю пластины бывают прямоугольные, трапециевидные и полукруглые. Наибольшее распространение имеют трапециевидные пластины (см. рис.5).
Прямоугольные пластины применяются в тех случаях, когда отогнутые борта трапециевидных пластин задевают за раму конвейера на криволинейных участках трассы. Полукруглые пластины применяются только для изгибающихся конвейеров. Ширина пластинчатого полотна конвейера колеблется от 500 до 1200 мм. Ширина и высота лотка зависят от требуемой производительности конвейера, кусковатости транспортируемого материала и места установки конвейера. Пластинчатое полотно крепится к круглозвенной цепи с помощью штырей и хвостовиков, а к пластинчатой цепи – заклепок или болтов.
К пластинчатому полотну конвейера крепятся опоры с ходовыми роликами 4 (см. рис. 5), которые собираются на шарикоподшипниках и имеют торцовые металлические уплотнения. Опорная конструкция или несущая рама става конвейера состоит из стоек и верхних и нижних направляющих для ходовых роликов. Направляющие изготовляются из проката и штампованных деталей. Рама става состоит из отдельных секций длиной 2,5 – 3,5 м. На криволинейных участках при закруглении с радиусом 40 м опорную конструкцию собирают из прямолинейных укороченных или криволинейных секций, длина которых в два раза меньше обычных. При малых радиусах закруглений устанавливают батарею направляющих роликов. Наибольшее распространение получили направляющие для роликов из углового проката. В выработках, имеющих неспокойную гипсометрию, применяют направляющие из швеллеров. Для нормальной эксплуатации конвейеров большое значение имеет правильная стыковка направляющих. Чтобы защитить направляющие от засорения транспортируемым материалом и обезопасить работу обслуживающего персонала, ходовые ролики закрываются щитками, которые крепятся к опорным стульям.
В пластинчатых конвейерах применяются концевые и промежуточные приводные головки. Концевые головки собираются с одним или двумя электродвигателями в головной и хвостовой части става. Промежуточные приводные головки устанавливаются на трассе конвейера и применяются для разгрузки концевых приводов при больших длинах пластинчатых конвейеров. На рис. 2 показана приводная головка пластинчатого конвейера КПИ-1 с двумя электродвигателями мощностью по 32 квт каждый.
Натяжное устройство пластинчатых конвейеров совмещено с хвостовыми поворотными устройствами и может быть выполнено жестким или податливым. Наибольшее распространение получили жесткие натяжные устройства.
22.23.24. ЛЕНТОЧНЫЕ КОНВЕЙЕРЫ
Конструктивная схема ленточного конвейера
Ленточный конвейер (рис.1) состоит из замкнутого контура ленты 1, которая перемещается по роликовому ставу 2 и служит как тяговым, так и грузонесущим органом.
Лента приводится в движение при помощи тяговых барабанов 3, входящих в приводную станцию. Для обеспечения необходимого натяжения ленты предусмотрено натяжное устройство 4.
Конвейерные ленты
В ленточном конвейере обычной конструкции конвейерная лента является одновременно грузонесущим и тяговым органом, в связи с этим к ней предъявляются особые требования. Конвейерная лента должна обладать высокой прочностью, чтобы воспринимать большие тяговые усилия; должна хорошо сопротивляться ударным нагрузкам, которые могут иметь место при погрузке на нее транспортируемого груза, кроме того, она должна обладать гибкостью и высокой износостойкостью.
Для ленточных конвейеров, которые используются на открытых разработках, наибольшее распространение получили тканевые многопрокладочные ленты. Для мощных стационарных конвейеров все чаще используются резинотросовые конвейерные ленты.
Тканевые многопрокладочные ленты (рис.2) состоят из нескольких прокладок (слоев), пропитанных резиной, между которыми расположены тонкие резиновые прослойки (сквиджи). Прокладки составляют прочную основу (каркас) ленты и защищаются от ударов и пробоев, а также от проникновения влаги верхней, нижней и бортовыми обкладками. Все составные части ленты соединяются между собой при помощи вулканизации. Обычно верхняя обкладка, на которой лежит транспортируемый груз, делается более толстой. В конвейерных лентах отечественного производства верхнюю обкладку делают толщиной 3 – 6 мм, а нижнюю – 1 – 3 мм, толщина прокладок принимается 1,5 – 2,5 мм, толщина сквиджей – 0,2 – 0,3 мм. Прокладки представляют собой полосы специальной хлопчатобумажной или синтетической ткани, имеющей прочные продольные основные нити, переплетенные поперечными уточными нитями.
Роликовый став
По всей длине конвейерная лента поддерживается роликоопорами. К роликоопорам предъявляются следующие требования: ролики должны обладать Малым сопротивлением вращению; на грузовой ветви роликоопора должна придавать ленте лотковость для лучшего заполнения ленты, грузом; роликоопоры должны обеспечивать центрирование ленты при движении, а также должны быть прочными и долговечными.
Основным элементом роликоопор является ролик. В одной роликоопоре может быть от одного до пяти роликов. Наибольшее распространение получили трехроликовые опоры для поддержания грузовой ветви ленты и одно- или двухроликовые – для поддержания порожней ветви.
Ролики могут быть с жесткими и гибкими осями. Иногда выполняются ролики с цапфами. Гибкие оси могут быть из стального каната или из отрезков цепи. Наиболее широко используются ролики с жесткой осью.
Роликоопоры принято разделять на жесткие (рис.4) и податливые – подвесные (рис.5). В жестких – ролики устанавливают при помощи кронштейнов на планки, которые монтируются на поддерживающих конструкциях, выполненных в виде легких, но прочных ферм из стального проката.
Поддерживающие конструкции передвижных конвейеров (забойных и отвальных) выполняются в виде отдельных секций длиной 4,5 – 6,0 м, которые устанавливают на деревянных или полых стальных шпалах. Шпалы соединяют между собой двумя нитками рельсов, которые служат для передвижки конвейеров с помощью различного рода передвижчиков, а иногда используются для перемещения вдоль конвейера разгрузочных и загрузочных устройств.
Ролики, поддерживающие обратную ветвь конвейерной ленты, подвержены загрязнению, так как они соприкасаются с грузовой ее стороной.
Значение конвейеризации и область применения конвейерного транспорта
Применение конвейерного транспорта способствует интенсифиации и концентрации очистных работ, обеспечивает непрерывность грузопотока, ритмичность работы и повышение производительности труда при наиболее низких энергоемкости и трудоемкости процесса транспортирования горной массы.
Основные преимущества конвейерного транспорта: высокая производительность достигающая в отдельных случаях 6000 т/ч; большая длина транспортирования в одном ставе; относительно малая энергоемкость; благоприятные условия для автоматизации и централизованного управления; повышение безопасности и улучшение условий труда. Недостатки конвейерного транспорта: сложность транспортирования абразивных скальных грузов; ограниченная кусковатость; интенсивный износ гибких тяговых органов; высокая стоимость оборудования и его монтажа; сложность транспортирования липкой горной массы.
Основные области эффективного применения конвейерного транспорта на подземных работах – транспортирование угля, калийных и марганцевых руд из забоя до пунктов перегрузки в другие транспортные средства или полная конвейеризация из забоя до поверхности и на поверхности до обогатительной фабрики. Например, на угольных шахтах с пластами пологого падения практически закончена конвейеризация главных наклонных выработок, конвейеризировано около 15% горизонтальных выработок, предназначенных для транспортирования угля.
На угольных калийных шахтах в очистных забоях применяют скребковые конвейеры, а по участковым и магистральным выработкам и наклонным стволам – ленточные конвейеры, реже – ленточно-канатные. На марганцевых шахтах в забое и по выемочным и аккумулирующим штрекам руду транспортируют в основном ленточными конвейерами.
В подземных условиях применяют стационарные и полустационарные ленточные конвейеры. Стационарные конвейеры устанавливают на длительный срок в главных капитальных выработках. В выработках, примыкающих к лаве, устанавливают полустационарные ленточные конвейеры, конструкция которых позволяет осуществлять периодическое или непрерывное изменение их длины.
Кроме скребковых и ленточных конвейеров на угольных шахтах находят ограниченное применение пластинчатые конвейеры.
Использование конвейерного транспорта при подземной разработке крутопадающих месторождений крепких руд позволяет сократить количество рудоспусков в отрабатываемых блоках и объем проходческих работ, а также сроки подготовки и отработки блоков. При большинстве применяемых систем разработок с обрушением руды и вмещающих пород, для выпуска руды, доставки ее в пределах блока и погрузки в транспортные средства широко применяются вибрационные питатели. Начато внедрение виброкомплексов, включающих вибропитатель и виброконвейер, которыми руда доставляется до участкового рудоспуска.
Ленточные конвейеры используют для транспортирования только дробленых крепких руд на концентрационных горизонтах, по наклонным стволам до поверхности и на поверхности горнорудных предприятий.
Наряду с традиционными типами конвейеров в определенных условиях эксплуатации находят применение телескопические ленточные конвейеры, ленточные перегружатели, ленточно-канатные конвейеры, ленточно-тележечные конвейеры для транспортирования крупнокусковых скальных грузов.
Ленточные конвейеры
Принципиальная схема ленточного конвейера представлена на рис. 8. Замкнутая бесконечная лента 1, которая является одновременно тяговым и несущим органом, огибает головной приводной барабан 2 и хвостовой натяжной 3. На длине става верхняя рабочая и нижняя порожняковая ветви ленты поддерживаются роликоопорами 4 и 5. Загрузку ленточного конвейера осуществляют обычно в его хвостовой части через загрузочную воронку 6, однако загрузка возможна практически в любом месте рабочей ветви конвейера. Разгрузка конвейера производится, как правило, в головной части при сходе ленты с барабана.
Ленточные конвейеры в горной промышленности получили широкое применение благодаря следующим преимуществам: относительная простота конструкции, высокая производительность и большая длина в одном ставе, меньшие масса и энергоемкость по сравнению с другими типами конвейеров, возможность полной автоматизации работы и др. Недостатки ленточных конвейеров: необходимость прямолинейной установки става конвейера в плане, ограниченная кусковатость транспортируемого груза (до 350 – 400 мм), высокая стоимость, относительно небольшой срок службы конвейерной ленты, ограниченный угол наклона конвейера с гладкой лентой до +18° или – 16°.
Основные элементы ленточного конвейера: лента, привод, роликоопоры, став и натяжное устройство. Ленточные конвейеры оснащают устройствами для очистки ленты, для улавливания ленты в случае ее обрыва на наклонном конвейере, а также различными датчиками и приспособлениями для контроля за работой и автоматизации отдельных конвейеров и конвейерных линий. На подземных ленточных конвейерах наиболее распространены резинотканевые и резинотросовые ленты. В резинотканевой ленте (рис. 9, а) се основу (каркас) обеспечивающую необходимую прочность и передачутяговых усилий, составляют тканевые прокладки 1, покрытые верхней рабочей обкладкой 2, нижней обкладкой 3 и бортами 4, защищающими каркас от механических повреждений и проникновения влаги. Прокладки выполняют из ткани полотняного переплетения с основными нитями, направленными вдоль ленты, и уточными нитями, расположенными поперек ленты. Тяговое усилие передают только основные нити прокладок ленты.
До недавнего времени на конвейерах небольшой мощности и длины применялись ленты с прокладками, выполненными из ткани типа бельтинг, с удельной разрывной прочностью 550 – 1100 Н/см ширины одной прокладки. В настоящее время прокладки для таких лент изготовляют из комбинации полиэфирного и натурального волокон типа БКНЛ.
Для ленточных конвейеров средней и большой мощности применяют ленты с синтетическими прокладками на основе полиамидных и полиэфирных волокон, обладающих удельной разрывной прочностью до 3000 Н/см ширины одной прокладки (типа 2К-300 и 2А-300).
Находят применение ленты с прокладками из лавсановых тканей с удельной разрывной прочностью 1200 Н/см.
25.26.27. Определение ширины ленты.
Ширина В лотковой ленты определяется в зависимости от заданной часовой производительности Q и принятой скорости движения ленты u:
м,
где u - скорость ленты, м/сек; для типовых конвейеров скорость ленты следует принимать не более 1,5 м/сек;
g - насыпной вес материала, т/м3; для угля составляет 0,85, для антрацита 1,1, для руды 1,8-2,0 и для породы 1,6 т/м3.
kn – коэффициент производительности; при лотковой ленте принимается равным 310 (для угля).
На наклонных конвейерах рекомендуется уменьшить коэффициент производительности kn при углах 10-150 на 5-10%, а при углах 15-180 – на 10-15%.
Полученное по формуле значение ширины ленты должно быть проверено по кусковатости транспортируемого материала
В ³ 2а¢max+ 200, мм,
где 2а¢max – максимальный размер куска транспортируемого материала, мм.
- Определение сопротивления движению:
груженой ветви ленты
Wгр = [(q + qл+ q¢р) w¢ cos b ±(q + qл) sin b] L, кг
(знак минус принимается для расчета конвейера на бремсберге);
порожняковой ветви
Wпор = [(qл+ q¢¢р) w cos b ± qл sin b] L, кг
(знак плюс принимается для расчета конвейера на бремсберге),
где q = – вес груза на 1 м ленты, кг/м;
qл – вес 1 м ленты, кг/м;
q¢р и q¢¢р – вес вращающихся частей соответственно верхних и нижних роликов, кг/м;
w¢ - коэффициент сопротивления движению ленты, зависящий от конструкции и состояния роликов; для забойных и штрековых конвейеров при мало благоприятных условиях эксплуатации w¢ = 0,04 – 0,06, для стационарных конвейеров при хороших условиях эксплуатации w¢ = 0,03 – 0,04.
Вес 1 м ленты
qл = 1,1В (1,25i + d1 + d2), кг/м,
где i – число прокладок в ленте;
d1 и d2 – толщина обкладок соответственно на рабочей и холостой ветвях, мм;
Вес 1 м резинотросовой ленты при отсутствии заводских данных приближенно можно подсчитать по формуле
кг/м,
где d1 – толщина ленты, мм;
dт – диаметр троса, мм;
qт – вес 1 м троса, кг/м;
l1 – число тросов в ленте.
- Определение веса вращающихся частей роликов: для груженой ветви
кг/м;
для порожней ветви
кг/м,
где Gp¢ и Gp¢¢ - вес вращающихся частей соответственно верхних и нижних роликов трехроликовой опоры, кг; принимается по заводским данным;
l¢ и l¢¢ - расстояние между роликоопорами соответственно рабочей и холостой ветвей, м.
28.29. специальные виды конвейерного транспорта на карьерах
К специальным типам конвейеров относят ленточно-канатные, крутонаклонные и конвейеры для перемещения крупнокусковых грузов. В настоящее время на открытых разработках используют ленточно-канатные конвейеры, крутонаклонные, а конвейеры для крупнокусковых грузов находятся в стадии опытно-промышленных испытаний.
Ленточно-канатный конвейер
Основная отличительная особенность ленточно-канатного конвейера (рис.1) использование раздельных тягового и грузонесущего органов.
Тяговым органом служат два параллельных замкнутых каната, приводящихся в движение шкивами приводного устройства. В ленточно-канатных конвейерах используют стальные канаты односторонней свивки с линейным касанием проволок. Диаметр канатов принимают от 32 до 50 мм.
Грузонесущая лента специальной конструкции (рис. 1, б) снабжается одной или двумя тканевыми прокладками и имеет по краям продольные утолщения с клиновидными канавками. Для придания ленте поперечной жесткости внутри нее через 60 – 100 мм завулканизированы стальные стержни (рессоры) прямоугольного или квадратного поперечного сечения.
Продольными канавками лента ложится на тяговые канаты и движется вместе с ними. Из рис. (рис. 1, б) видно, что утолщения, которыми лента ложится на канаты грузовой ветви, могут располагаться ближе к продольной оси ленты, что позволяет принимать ленту большей ширины. На современных ленточно-канатных конвейерах используют ленты шириной 760 – 1400 мм.
Тяговые канаты поддерживаются роликами, установленными на балансирах, вследствие чего уменьшаются перегибы канатов при движении. Для снижения износа канатов ролики футеруют специальными пластмассами. Роликоопоры устанавливают на вертикальных стойках через определенные интервалы. В головной и хвостовой частях конвейера лента огибает разгрузочный и натяжной барабаны. При подходе к барабанам тяговые канаты выводятся из-под ленты или подводятся под нее при помощи системы отклоняющих роликов (см. рис 1, а).
Натяжение канатов и ленты осуществляется натяжными устройствами грузового или лебедочного типа, конструкция которых аналогична устройствам, используемым в обычных ленточных конвейерах;
Приводное устройство состоит из двух шкивов с раздельными приводами.
- Крутонаклонный конвейер
Крутонаклонными называют конвейеры, способные перемещать насыпные грузы по трассам с углом наклона более 20°.
По принципу удержания груза на конвейерной ленте крутонаклонные конвейеры можно разделить на три группы.
К первой группе относят конвейеры, на которых удержание груза на ленте при больших углах наклона обеспечивается созданием повышенной силы сцепления груза с поверхностью ленты. Для этого используют конвейерные ленты, грузовая поверхность которых имеет выступы небольшой высоты (до 40 мм) различной формы.
Выступам придают такую конфигурацию, при которой, двигаясь по роликоопорам, грузовая ветвь ленты приобретает лотковость, а порожняковая ложится выступами на роликоопору порожняковой ветви. Опыт показывает, что конвейеры с такими лентами могут перемещать насыпные грузы крупностью до 350 мм при углах наклона трассы до 25°.
Производительность конвейеров с рифлеными лентами нужно принимать на 30 – 40% ниже, чем для обычных ленточных конвейеров с одинаковой шириной и скоростью ленты при установке под углом
Достоинством конвейеров этого типа является возможность использования всех узлов (кроме ленты) от обычных ленточных конвейеров. К. недостаткам относят высокую жесткость ленты на изгиб, что позволяет использовать только однобарабанный привод с углом обхвата лентой приводного барабана 180°, а также трудности, связанные с очисткой ленты из-за рифов, что приводит к быстрой заштыбовке нижней ветви.
Ко второй группе относят конвейеры с лентой глубокой желобчатости (рис. 2). Конвейеры этого типа имеют горизонтальный или слабонаклонный загрузочный участок, на котором установлены обычные роликоопоры 1. На переходном участке угол наклона боковых роликов постепенно повышается, вследствие чего создается обжатие груза и увеличивается сила сцепления с лентой. Наибольшее обжатие достигается при применении гирляндных роликоопор 2. При подходе к разгрузочному концу лента переходит на участок с меньшим углом наклона и постепенно разворачивается. Конвейеры такого типа могут перемещать насыпные грузы крупностью до 300 мм при углах наклона до 25°. Для предотвращения скатывания отдельных кусков груза по открытой поверхности груз желательно примять на небольшой длине загрузочной части конвейера посредством короткой замкнутой ленты 3 (см. рис. 2).
Достоинствами конвейера с лентой глубокой желобчатости являются возможность унификации всех основных узлов с обычным ленточным конвейером, использование гладких конвейерных лент, применение многобарабанных приводов, а также простота очистки конвейерной ленты.
- Ленточный конвейер для крупнокусковых грузов
Ленточный конвейер для крупнокусковых грузов. Для перемещения насыпных грузов крупностью более 600 мм создан специальный конвейер на ходовых опорах (ленточно-тележечный), В ленточно-тележечном конвейере (рис. 4) приводное и натяжное устройства аналогичны тем, которые используют в обычных ленточных конвейерах. Отличие конвейера заключается в том, что основная часть грузовой ветви конвейерной ленты 1 поддерживается специальными ходовыми тележками 2, связанными между собой цепями 3 и движущимися по направляющим 4. Таким образом, груженая конвейерная лента, свободно лежащая на опорах, перемещается вместе с ними. Такое движение не вызывает шевеление груза на ленте, чем обеспечивается его устойчивость и снижение динамических нагрузок на ленту от действия крупных кусков. Опыт эксплуатации таких конвейеров на рудниках «Аксай» и «Джанатас» (ПО «Каратау»)
показал, что при ширине ленты 1200 и 1600 мм конвейер может перемещать грузы крупностью 1000 и 1500 мм.
- Рельсовый путь и его элементы.
Общие сведения
Карьерные железнодорожные пути принято разделять на постоянные и передвижные (временные).
К постоянным путям относят стационарные пути, пути выездных траншей, соединительные пути на поверхности карьера. Срок службы постоянных путей на одном месте, как правило, превышает два года.
К передвижным путям (со сроком службы на одном месте до двух лет) относят пути карьерных уступов, временные пути породных отвалов. Кроме того, по объему грузоперевозок и по допустимой скорости движения локомотивосоставов карьерные железнодорожные пути делятся на три категории.
Строение железнодорожных путей
Железнодорожный путь состоит из нижнего и верхнего строения. К нижнему строению относятся земляное полотно и искусственные сооружения, к верхнему – рельсы, скрепления, шпалы и балласт.
Земляное полотно – основание железнодорожного пути. Верхнюю плоскость земляного полотна, на которой размещается верхнее строение, называют основной площадкой. Ширину основной площадки принимают по специальным нормативам в зависимости от ширины колеи, числа путей, их прямолинейности и характеристики грунта, из которого сооружено земляное полотно.
Основные элементы железнодорожных путей
Рельсы служат для направления движения подвижного состава и распределения давления от колес на шпалы, балласт и нижнее строение. Поперечное сечение рельса представляет собой двутавр, хорошо сопротивляющийся вертикальным нагрузкам от колес. Верхнюю часть сечения рельса называют головной, среднюю – шейкой, а нижнюю – подошвой.
Расстояние между внутренними стенками головок рельсов железнодорожного пути называют колеей. На карьерах используют нормальную (1520 мм) и узкую (750 мм) колеи. Кроме того, на некоторых карьерах применяют нестандартную колею (900 или 1000 мм).
Рельсовые скрепления – промежуточные – применяют для соединения рельсов со шпалами, а стыковые – для соединения рельсов между собой.
Прочность прикрепления рельсов к шпалам имеет исключительное значение для передвижных путей, так как при их разборке на отдельные звенья, повторной укладке и сборке крепление ослабляется и прикрепители выдергиваются из шпал.
Стыковые скрепления, предназначенные для связи рельсов между собой, выполняют в виде накладок различного типа. На путях с нормальной колеей и рельсами тяжелого типа применяют двухголовые накладки 1 (рис. 3), обладающие большой жесткостью. Для скрепления накладок с рельсами применяют стыковые болты 2 с пружинящими шайбами, предотвращающими их самопроизвольное отвинчивание. При передвижке путей с использованием путепередвигательных машин накладки 3 выполняют с выемками в верхней части для пропуска роликов захватывающего устройства.
Шпалы предназначены для соединения рельсов в железнодорожный путь и передачи давления от подвижного состава через рельсы на балластный слой. Число шпал на 1 км пути устанавливается нормативами и зависит от нагрузки на оси подвижного состава, грузонапряженности, скорости движения и характера балластного слоя. Минимальное расстояние между соседними шпалами принимают 25 см, а на закруглениях и концах отдельных рельсов его уменьшают, так как эти участки испытывают повышенное давление.
Балласт. Рельсы, соединенные со шпалами при помощи скреплений, называют рельсошпальной решеткой, которая укладывается на балластный слой, являющийся упругим основанием, способствующим более равномерному распределению усилия на рельсы и смягчающим динамические нагрузки на земляное полотно. Кроме того, балластный слой, обладающий достаточной пористостью, способствует отводу поверхностных вод от рельсов и шпал и тем самым замедляет коррозию рельсов и гниение шпал.
Для балласта используют щебень крупностью 20 – 70 мм, гальку, гравий, крупнозернистый песок. Обычно щебень получают посредством дробления твердых вскрышных пород. На передвижных путях для балласта почти всегда используют пустые породы или отходы горного производства, если их свойства соответствуют требованиям, предъявляемым к балластировочным материалам.
34. Типы рудничных вагонеток
Шахтная вагонетка УВГ-1, 3 (рис. 4) емкостью 1,3 м3 имеет грузоподъемность 1 т. Сварной кузов вагонетки выполнен с полукруглым днищем из листовой стали толщиной 4 – 6 мм. Буфера вагонетки – разрезные кулачковые, сцепка – крюковая вращающаяся. К нижней части рамы заклепками крепятся кронштейны для установки полускатов. В средней части рамы прикреплен подвагонный упор для толкателя.
Вагонетка УВД-2,5 (рис. 5, а) разгружается через дно. Она имеет три откидных днища на поперечных шарнирах. Для двух днищ шарнирами служат оси полускатов, а третий шарнирно установлен на валике под торцовой стенкой вагонетки. В закрытом положении первое днище удерживается крючком, второе – загибом над шарниром первого днища, а третье – загибом второго днища. При движении вагонетки (рис. 6) над бункерной ямой 1 рычаг 3, находящийся на задней торцовой стенке, наезжает выступающим концом на установленную около путей профильную раму 2. Рычаг поднимается кверху и откидывает крючок. Днища 5 последовательно открываются и откидываются вниз, а уголь высыпается в бункер. Двигаясь дальше, вагонетка днищем наезжает на упор 4, расположенный между рельсами, который приподнимает и последовательно закрывает днища. Вагонетки, разгружающиеся через дно, не требуют сложного оборудования для разгрузки и специального обслуживающего персонала. Разгрузка происходит автоматически при медленном ходе вагонетки.
Недостатками таких вагонеток являются их большой мертвый вес сложность изготовления, возможность открывания днища в пути, необходимость подавать вагонетки к месту разгрузки всегда одной стороной. Кроме того, при движении вагонетки через зазоры между днищами и стенками возможно просыпание породной и угольной мелочи, которая сильно засоряет пути, а при влажных углях на днищах налипает слой грязи, который трудно удалить. Указанные недостатки снижают эксплуатационные качества таких вагонеток и поэтому они имеют ограниченное применение.
- Вагоны
При разработке месторождений открытым способом для перевозки полезного ископаемого, вскрышных пород и некоторых Вспомогательных насыпных грузов используют следующие типы вагонов: полувагоны (гондолы) – вагоны без крыши со сплошным днищем (рис. 2, а) или с открывающимися в днище люками (рис. 2, б), полувагоны с двухскатным днищем и открывающимися люками в нижней части боковых стенок (рис. 2, в), полувагоны с кузовом в виде бункера с наклонными стенками и открывающимися в нижней части люками (хопперы) (рис. 2, г), полувагоны с двухскатным днищем и поднимающимися стенками кузова (рис. 2, д) и полувагоны-самосвалы (думпкары) (рис. 2, е) с опрокидывающимися для разгрузки кузовом и откидывающимися или поднимающимися стенками.
Для перевозки оборудования и некоторых других вспомогательных грузов применяют также платформы и вагоны специального назначения.
Основными параметрами вагонов являются: грузоподъемность G(т) – масса груза, которую можно разместить в вагоне; вместимость V (м3) – внутренний объем кузова; масса вагона т0(т); внутренние геометрические размеры кузова (м): длина l, ширина b, высота h;
- Локомотивы
На карьерах при перевозке горной массы железнодорожным транспортом используют следующие типы локомотивов: электровозы и тепловозы.
По условиям эксплуатации карьерные локомотивы должны удовлетворять следующим требованиям: преодолевать затяжные уклоны, проходить криволинейные участки железнодорожного пути с малыми радиусами (100 – 150 м), работать в любых климатических условиях, не зависеть от внешних источников подвода энергии на призабойных путях.
В наибольшей степени этим требованиям удовлетворяют электровозы, получившие широкое распространение на карьерном транспорте.
Электровозы бывают аккумуляторные и контактные. На карьерах, как правило, используют контактные электровозы постоянного и переменного тока.
Электровозы постоянного тока питаются от контактной сети постоянного тока напряжением 1500 или 3000 В, а электровозы переменного тока – от сети переменного тока напряжением 10000 В. Контактная сеть характеризуется большими потерями энергии, что приводит к снижению к. п. д. электровозного карьерного транспорта до 14%, в то время как к. п. д. самих электровозов составляет 86 – 88%.
Кроме того, наличие контактной сети на экскаваторных уступах и отвалах затрудняет производство буровзрывных и экскавационных работ, во время которых возникает опасность соприкосновения с контактной сетью ковша экскаватора, повреждения ее в момент взрыва или загрузки вагонов.
Некоторые операции по обслуживанию контактной сети связаны с большими затратами ручного труда.
Наиболее эффективны комбинированные контактно-аккумуляторные электровозы, для которых не требуется контактная сеть на экскаваторных уступах. Однако к настоящему времени не разработаны достаточно экономичные и дешевые аккумуляторы.
На карьерах нашей страны все большее распространение получают тяговые агрегаты, представляющие собой комбинацию из электровоза, дизель-генераторной секции и моторного вагона. При движении такого агрегата по постоянным путям он питается электроэнергией от контактной сети, а при движении по экскаваторному уступу питание тяговых двигателей осуществляется от дизель-генератора.
Электровозы. Основные параметры электровозов – масса, сцепной вес (вес локомотива, приходящийся на тяговые колеса), нагрузка на ось (вес локомотива, приходящийся на одну ось), мощность электродвигателей. Различают мощность часового режима, т. е. максимальную мощность, которую могут развивать электродвигатели, не перегреваясь в течение часа; мощность длительного режима, которую могут развивать двигатели длительное время без перегрева. Соответственно различают часовую и длительную силы тяги, часовую и длительную силу тока, часовую и длительную скорости.
Применение электровозов переменного тока более эффективно, чем электровозов постоянного тока, так как коэффициент сцепления электровозов переменного тока на 15 – 20% выше благодаря лучшему взаимодействию колесных тяговых пар с рельсами, соответственно больше и расчетная масса прицепной части состава на 15 – 20%, меньше потери в тяговой сети, поэтому выше к. п. д. транспортной системы в целом; в два раза меньше расход цветных металлов на контактную сеть. Кроме того, при использовании электровозов переменного тока можно увеличить расстояние между питающими подстанциями и сократить их число.
Вместе с тем стоимость электровозов переменного тока на 15 – 25% выше стоимости электровозов постоянного тока, перевод тяговой сети на переменный ток связан со значительными капитальными затратами, поэтому переходят и на питание постоянным током напряжением 3000 В, так как этот процесс требует меньших затрат.
Тепловозы. Тепловозом называют локомотив, оборудованный двигателем внутреннего сгорания. По типу трансмиссии, т. е. механизма передачи вращающего момента от двигателя к тяговым колесам, различают тепловозы с механической многоступенчатой передачей (мотовозы), гидромеханической и электромеханической передачами.
37.38.39.40. Характеристика и виды локомотивного транспорта
Рудничные локомотивы можно классифицировать по ряду основных признаков:
по роду энергии – электровозы (постоянного тока аккумуляторные и контактные, высокочастотные бесконтактные), дизелевозы и гировозы;
по способу питания – с автономным источником питания (аккумуляторные батареи, дизельный двигатель), с питанием от внешнего источника (через контактный провод или кабель), с комбинированным питанием (аккумуляторно-контактные или кабельно-контактные локомотивы);
по сцепному весу – легкие до 50 кН, средние от 50 до 100 кН и тяжелые свыше 100 кН;
по исполнению – нормального рудничного (РН), рудничного исполнения повышенной надежности (РП) и рудничного взрывобезопасного исполнения (РВ).
Для транспортирования по главным откаточным выработкам применяют в основном электровозы, причем в угольных шахтах используют 70 % аккумуляторных и 30 % контактных электровозов, а в рудных шахтах – контактные. Высокочастотные бесконтактные электровозы и дизелевозы находятся на стадии внедрения. Гировозы применяют для транспортирования различных вспомогательных грузов в угольных сверхкатегорных шахтах, опасных по газу и пыли.
Комплекс откатки контактными электровозами (рис. 9) включает тяговую подстанцию с трансформатором 1 и преобразовательным агрегатом 2, контактный провод 3 с постоянным током напряжением 250 или 550 В, через токоприемник 4 поступающий к тяговым двигателям 5 электровоза. Обратный провод – рельсовый путь 6.
Комплекс откатки аккумуляторными электровозами включает зарядную подстанцию и зарядные столы для зарядки аккумуляторных батарей, которые устанавливаются на электровозе и питают его.
Контактные электровозы по сравнению с аккумуляторными проще по конструкции, более удобны и дешевле в эксплуатации, обеспечивают большую скорость движения и, следовательно, большую производительность. Ввиду искрообразования между контактным проводом и токоприемником, согласно ПБ контактные электровозы разрешается применять во всех выработках горизонтов шахт, не опасных по газу или пыли, и в шахтах I и II категорий по газу или опасных по пыли только по главным откаточным выработкам электровозами с двумя токоприемниками.
Электровозы включают в себя механическое и электрическое оборудование, которое в принципе выполнено одинаково на контактных и аккумуляторных электровозах. Отличие заключается в источнике питания и способе подвода энергии.
41.42.43.44.45. РАСЧЕТ ЭЛЕКТРОВОЗНОЙ ОТКАТКИ
Исходными данными для расчета электровозной откатки являются:
сменная производительность шахты;
количество выдаваемой пустой породы;
категория шахты по газу и пыли;
схема расположения и профиль подземных откаточных путей с указанием погрузочных пунктов и их сменной производительности;
средний (преобладающий) уклон откаточных путей по всей шахте;
длина откатки соответствующих участков;
ширина колеи;
грузоподъемность вагонеток;
число часов работы откатки в смену.
Порядок расчета. 1. Выбор типа электровоза. В зависимости от категории шахты, колеи откаточных путей, грузоподъемности шахтных вагонеток и длины откатки выбирается тип электровоза.
2. Определение расчетных параметров откатки.
а) Суммарная сменная добыча по всем откаточным участкам шахты Ас.ш = А1 + А2 +…+ Аn, т,
где А1, А 2 ,…Аn – сменная добыча первого, второго и т.д. откаточных участков, км.
б) Средневзвешенная длина откатки по шахте
где L1, L2 … Ln – длина первого, второго и т.д. откаточных участков, км.
в) продолжительность движения электровоза с груженым и порожним составом в течение одного рейса
мин,
где vx – средняя ходовая скорость движения поездов, м/с;
учитывается с поправочным коэффициентом 0,75 снижения длительной скорости vдл в период пуска и остановки электровоза и во время прохода им закруглений стрелок и подъемов.
г) Продолжительность одного рейса
мин,
где q - продолжительность маневров электровоза в околоствольном дворе и у выемочного участка за один рейс, мин.
д) Характеристика тягового режима
- Выбор величины состава поезда.
а) Максимально допустимый вес груженого поезда, исходя из условий сцепления при пуске груженого состава на преобладающем уклоне (среднем),
т,
где P – конструктивный вес электровоза, т; принимается равным сцепному весу Рс;
Qгр – полный вес груженого состава, т;
j - коэффициент сцепления колес электровоза с рельсами; принимается для мокрых рельсов 0,15, для сухих рельсов 0,2, при подсыпке песка 0,25;
Wгр – ходовое удельное сопротивление движению груженой вагонетки, кг/т;
iср – сопротивление от уклона равного сопротивления, кг/т; для вагонеток с роликоподшипниками примерно составляет 2% или 2 кг/т;
jо – пусковое ускорение; принимается 0,05 м/сек2.
46. 47. Автомобильные дороги
Схемы автотранспорта выбирают с учетом горно-технических условий, горно-геологических условий залегания месторождений, конфигурации и размеров карьера. При использовании автотранспорта связь рабочих горизонтов карьера с поверхностью осуществляется посредством прямых, спиральных, петлевых и комбинированных съездов.
Прямые съезды (рис. 1, а) используют при разработке пологих или наклонных пластов полезного ископаемого (в этом случае карьеры характеризуются значительной длиной при сравнительно небольшой глубине), а также на нагорных карьерах. При прямых съездах из-за небольшого числа поворота длина дорог, ведущих к нужной отметке в карьере, минимальна.
Спиральные съезды (рис. 1, б) применяют на карьерах большой глубины и с ограниченными размерами в плане. Так как спиральные съезды характеризуются большими радиусами кривых, возможно движение автомобилей со значительными скоростями.
Петлевые съезды (рис. 1, в) используют в карьерах большой глубины, а также в карьерах, расположенных на склонах гор, так как в этом случае устройство прямых съездов невозможно из-за их недопустимо больших уклонов.
Комбинированные съезды (рис. 1, г) являются самыми распространенными, так как они наиболее приспособлены для разнообразных горно-технических и горно-геологических условий залегания месторождения.
Продольный профиль автодороги изображается в виде плавной кривой, состоящей из площадок горизонтальных участков, наклонных участков и кривых, соединяющих участии с различными уклонами. Руководящий уклон для современных карьерных автомобилей принимают от 70 до 100 - На затяжных уклонах (более 100 м) предусматривают участки длиной 50 – 60 м с уклоном не более 20 через каждые 500 – 600 м.
В зависимости от перевозимого груза автодороги на карьерах разделяют на производственные, по которым транспортируют вскрышные породы и полезное ископаемое, и хозяйственные, служащие для перевозки хозяйственных и вспомогательных грузов.
По сроку службы автодороги разделяют на постоянные и временные.
Производственные автодороги отличаются от хозяйственных значительно большими нагрузками на покрытие, постоянным интенсивным движением с меньшими скоростями движения.
Устройство автомобильных дорог.
Наиболее сложное устройство имеют постоянные карьерные дороги. Они состоят из земляного полотна с защитными устройствами и проезжей части, расположенной на верхней площадке земляного полотна (рис. 2). С обеих сторон дороги устраивают водоотводные кюветы и другие защитные устройства. Земляное полотно должно противостоять температурным колебаниям, атмосферным осадкам и быть устойчивым к нагрузкам от проходящих по проезжей части автомобилей.
Земляное полотно возводят из гравия или щебня. Оно включает в себя проезжую часть и две обочины (см. рис. 2). Наиболее интенсивное движение автомобилей происходит по проезжей части, а обочины служат для предохранения краев проезжей части от разрушения, складирования строительных материалов при ремонте дороги, для объезда и вынужденных остановок.
Земляное полотно выполняют в виде насыпей, выемок или нулевых мест. Крутизну откосов насыпей принимают от 34 до 18° при высоте до 1 м и 34° при высоте более 1 м.
48.49.50.51.52.53 Автосамосвалом называют автомобиль с усиленной грузовой платформой и кузовом, разгружающимся посредством опрокидывания назад или набок.
Автопоезд – автомобиль-тягач с одним полуприцепом или с одним или несколькими прицепами. Кузов прицепа или полуприцепа разгружается через дно, а также посредством опрокидывания назад или набок.
Условия эксплуатации карьерных автомобилей весьма тяжелые, поэтому к ним предъявляют ряд специфических требований. Карьерные автомобили должны обеспечивать минимальную продолжительность погрузки и разгрузки; обладать высокими маневренностью, устойчивостью и проходимостью при движении по дорогам низшего качества, высокой удельной мощностью и способностью преодолевать затяжные уклоны с необходимой скоростью. Кроме того, они должны иметь высокоэффективную тормозную систему, комфортные условия для работы водителя, выдерживать большие динамические нагрузки при погрузке экскаватором и при движении по неровным внутри-карьерным дорогам, должны быть легкоуправляемыми. Все эти требования обусловили рациональное конструктивное исполнение автосамосвалов.
В настоящее время основным типом карьерного автомобиля является двухосный самосвал с задней разгрузкой, так как он соответствует почти всем перечисленным выше требованиям. Если же необходима повышенная грузоподъемность, а другие требования менее значительны, то используют автопоезда.
К основным параметрам автосамосвалов относятся: грузоподъемность-максимальная масса груза, перевозимая автосамосвалом, вместимость кузова – максимальный полезный объем кузова, мощность двигателя, удельная мощность – мощность двигателя, отнесенная к 1 кг массы автосамосвала, мощность тяговых электродвигателей автосамосвалов с электромеханической трансмиссией, колесная формула – числовое выражение, показывающее общее число колес и число ведущих колес. Например, колесная формула 4X2 означает, что автосамосвал имеет четыре колеса, причем два из них ведущие.
Автосамосвал БеЛАЗ-549 отличается от предыдущих наличием электромеханической трансмиссии от дизеля к тяговым колесам, оборудованным электродвигателями. Автосамосвал БеЛАЗ-549 предназначен для работы в комплексе с экскаваторами ЭКГ-8 и ЭКГ-12,5.
Следующим типоразмером автосамосвалов серии БелАЗ является 110-тонный автосамосвал БелАЗ-7519, унифицированный сжимается при помощи поршня и воспламеняется от электрической искры. Необходимо отметить, что экономичность карбюраторного двигателя внутреннего сгорания зависит от степени сжатия горючей смеси, которая составляет 9 – 10. В дизельных двигателях внутреннего сгорания воспламенение смеси из воздуха и тяжелого топлива (солярового масла) происходит вследствие повышения температуры при сжатии. Топливо впрыскивается в рабочий цилиндр под давлением из форсунок. Степень сжатия рабочей смеси в дизельных двигателях принимают от 16 до 20. Дизельные двигатели обладают большей экономичностью, чем карбюраторные, так как расход топлива в них на 35 – 40% меньше на единицу мощности. Кроме того, для дизельных двигателей используют более дешевое топливо, поэтому, несмотря на более сложную конструкцию, они устанавливаются почти на всех карьерных автосамосвалах.
Двигатели. На карьерных отечественных автосамосвалах используют четырехтактные 6-, 8- и 12-цилиндровые двигатели с V-образным расположением рабочих цилиндров и с частотой вращения коленчатого вала 1500 – 2000 мин.
Дизельные двигатели состоят из остова, включающего в себя раму, блок цилиндров и масляный картер; шатунно-криво-шипного механизма, преобразующего возвратно-поступательное движение поршней во вращательное движение коленчатого вала; газораспределительного механизма, обеспечивающего впуск воздуха и выпуск выхлопных газов; топливной и регулировочной систем, необходимых для подвода топлива в цилиндры в определенные моменты и в строго определенном количестве в зависимости от того, какую мощность должен развивать в данный момент дизель.
Трансмиссиями карьерных автосамосвалов называют систему механизмов, служащих для передачи вращающего момента от коленчатого вала дизеля к ведущим колесам. На автосамосвалах применяют механические, гидромеханические и электрические трансмиссии.
Механическая трансмиссия (рис. 5) состоит из фрикционного механизма сцепления 1, шестеренчатой коробки передач 2, карданной 3 и главной 4 передач, дифференциального редуктора 5 и полуосей 6 с ведущими колесами. Из практики эксплуатации автосамосвалов и проведенных исследований установлено, что наибольшая эффективность достигается при использовании механических трансмиссий в самосвалах небольшой грузоподъемности (до 12 – 15 т). Этим типом трансмиссии оборудованы автосамосвалы КрАЗ. Основной недостаток механической трансмиссии – необходимость ручного переключения ступеней передач, поэтому экономичность работы автосамосвала и скорость его движения зависят от индивидуальных качеств водителя и его квалификации. Кроме того, сам процесс переключения может явиться причиной травматизма.
Гидромеханическая трансмиссия включает в себя: согласующий редуктор, соединенный с двигателем, гидротрансформатор (гидроредуктор), механическую коробку передач, карданный вал, задний мост, от которого вращающий момент передается на ведущие колеса. Гидромеханической трансмиссией оборудуют автосамосвалы грузоподъемностью от 15 до 60 т. Основной элемент гидромеханической трансмиссии – гидротрансформатор, служащий для автоматического и бесступенчатого изменения крутящего момента, передаваемого от дизеля на ведущие колеса.
На рис. 6 показан промежуточный карданный вал. Он состоит из эластичного и жесткого шарниров, соединенных скользящими фланцами. Эластичный шарнир включает в себя фланцы, соединенные между собой болтами через четыре обоймы. Каждая обойма состоит из двух чашек, внутри которых помещены резиновые втулки. Жесткий шарнир представляет собой конструкцию, состоящую из двух
эксплуатационный расчет автотранспорта
Эксплуатационная (сменная) производительность автосамосвала, т/см
где Тсм – продолжительность смены, ч;
Кв – коэффициент использования сменного времени, Кв = 0,8
Рабочий парк автосамосвалов
где Qсм— сменная производительность карьера, т/см;
f – коэффициент неравномерности сменного грузопотока f=1,15÷1,20.
54.55.56. Схемы и область применения.
В гидро- и пневмотранспортных установках дробленая горная масса перемещается по трубам рабочей средой – водой или воздухом. Перемещение горной массы в гидротранспортных установках осуществляется за счет разностей уровней (самотечное транспортирование) или под действием избыточного давления, а в пневмотранспортных – за счет разности давлений воздушного потока в загрузочном и разгрузочном пунктах трубопровода.
По принципу действия различают гидротранспортные установки безнапорные самотечные, в которых пульпа (смесь частиц горной массы и воды) перемещается по желобам (рис. 2, а) или по трубам (рис. 2, б), и напорные, в которых пульпа перемещается искусственным напором, создаваемым пульпона-сосом (рис. 2, в), или горную массу отдельно загружают в трубопровод питателем, а воду в трубопровод подают под давлением насосом (рис. 2, г). Особой разновидностью гидротранспортных установок являются гидроэлеваторы и эрлифты. Принцип действия гидроэлеватора (рис. 2, д) заключается в том, что в его насадку подают под давлением воду, которая входит из насадки с большой скоростью, благодаря чему в камере гидроэлеватора создается вакуум, и пульпа через патрубок засасывается в камеру и под напором струи перемещается в трубопровод.
В эрлифте (рис. 2, е) движение частиц горной массы происходит в результате подачи в трубопровод сжатого воздуха и пульпы, образующих аэрированную пульпу высотой Н, вес которой меньше веса столба пульпы высотой h.
Гидротранспортными установками можно перемещать дробленую горную массу, частицы которой не размокают и не прилипают к стенкам трубопровода.
Гидротранспортные установки применяются на угольных шахтах с гидродобычей для транспортирования угля по всем выработкам от забоя до поверхности, на поверхности для транспортирования угля, реже – руды от места добычи до потребителя на расстояние до нескольких десятков и даже сотен километров, а также для транспортирования породы в отвал и закладочных материалов в выработанное пространство.
Производительность самотечных гидротранспортных установок достигает 600 т/ч, а напорных – 1600÷2000 т/ч.
Гидроэлеваторы применяют при небольших грузопотоках и расстояниях транспортирования, например, для уборки породы от проходческих комбайнов, чистки зумпфов и т. д. Эрлифты редко используют для подъема из шахты измельченной горной массы.
Пневмотранспортные установки нагнетательного типа иногда применяют для подъема из шахты угольной мелочи и подачи сухих закладочных материалов в выработанное пространство. Наибольшее распространение на рудных шахтах получают самотечно-пневматические установки для транспортирования твердеющей закладки, применение которой позволяет сократить потери и разубоживание ценных руд, заменить рудные целики искусственными, сохранить ненарушенной земную поверхность.
Производительность напорных пневмотранспортных установок до 500 т/ч, длина 700 – 800 м. Самотечно-пневматические установки обеспечивают производительность по закладочной смеси до 180 – 200 м3/ч при дальности транспортирования до 2000 – 2500 м.
Оборудование гидро- и пневмотранспортных установок.
В оборудование гидротранспортных установок входят желоба, трубопроводы, пульпонасосы (углесосы) и питатели.
Для самотечных установок применяют желоба прямоугольного или полукруглого сечения, изготовленные из листовой стали и укладываемые внахлестку с уклоном 0,03 – 0,08.
Для напорных гидротранспортных установок применяют трубопроводы диаметром до 600 мм, собираемые из отдельных отрезков труб длиной 2 – 6 м, которые между собою соединяются с помощью быстроразъемных или фланцевых соединений. С целью увеличения срока службы внутреннюю поверхность труб упрочняют закалкой или армируют износостойким материалом, например базальтом.
Для пуска, остановки и регулирования гидротранспорта трубопроводы оборудуют задвижками и вентилями.
Пульпонасосы представляют собой центробежные насосы с большими пропускными отверстиями для прохода кусков горной массы крупностью до 100 мм. Производительность отдельных пульпонасосов 1400 – 1600 м3/ч.
В установках с вводом горной массы в трубопровод (рис. 2, г) применяют питатели непрерывного и цикличного действия, например камерные, работа которых основана на принципе обмена объема напорной воды на равный объем горной массы.
В оборудование пневмотранспортных установок входят трубопроводы, компрессоры или воздуходувки, питатели (закладочные машины).
Для трубопровода применяют стальные, реже чугунные и полиэтиленовые трубы диаметром 50 – 250 мм. Внутреннюю поверхность труб футеруют каменным литьем, а поворотных колен – твердым сплавом.
В пневмотранспортных установках с давлением воздуха в магистрали до 0,3 МПа применяют воздуходувки, а с давлением 0,3 – 0,7 МПа – компрессоры.
Питатели или закладочные машины, используемые для загрузки трубопроводов закладочным материалом, изготавливают двухкамерными цикличного действия производительностью 100 – 120 м3/ч и барабанного типа непрерывного действия производительностью до 160 м3/ч. Дальность транспортирования с применением пневматических закладочных машин достигает 1500 – 1700 м, максимальная крупность транспортируемого материала 70 – 80 мм.
57.58.59.60. Общие сведения
На поверхности шахты около ствола располагается комплекс технических сооружений и зданий, приемных, транспортирующих, погрузочных и складских устройств, которые называются технологическим или производственным комплексом шахты. Технологический комплекс предназначен для приема полезного ископаемого из шахты, его дальнейшей переработки и погрузки в железнодорожные вагоны, а также для приема из шахты пустой породы и транспортировки ее в отвалы. На поверхности шахты располагаются здания вентиляторов, калориферов, компрессорной подстанции, котельной, механических мастерских, складов для хранения оборудования и материалов, административно-бытовой комбинат и лесной склад. План расположения на поверхности зданий, сооружений, складов, подъездных железнодорожных путей узкой и широкой, колеи, автодорог и т. д. называется генеральным планом шахты.
Генеральный план поверхности
Генеральный план поверхности угольной шахты годовой производительности 900 тыс. т. в год коксующихся углей без обогатительной фабрики показан на рис. 1. Уголь и порода выдаются по одному стволу с помощью соответственно двухскипового и односкипового (скип и противовес) подъема. По клетевому стволу производится спуск вспомогательных материалов, спуск и подъем людей.
B настоящее время ' на шахтах применяются четыре схемы технологических комплексов:
- технологические комплексы, где не предусматривается переработка и обогащение полезного ископаемого, и оно отгружается потребителю рядовым. Такие комплексы отличаются наибольшей простотой;
- технологические комплексы, где производится рассортировка без обогащения полезного ископаемого. В этом случае в цепи аппаратов добавляются дробилки, грохоты, конвейеры, а погрузочные бункера разделяются на ячейки, число которых должно соответствовать числу сортов полезного ископаемого, отгружаемого потребителю;
- технологические комплексы без сортировки, где полезное ископаемое только обогащается. В этом случае поверхностный комплекс включает также обогатительную фабрику;
- технологический комплекс, который предусматривает сортировку и обогащение полезного ископаемого. В этом случае схема получается наиболее сложной.
Приемные устройства на поверхности
При вертикальном стволе приемные устройства на поверхности зависят от применяемых подъемных сосудов и разделяются на два различных типа: устройства, применяемые при скиповом подъеме и в опрокидных клетях, и устройства при подъеме в обыкновенных клетях. В первом случае выдаваемое полезное ископаемое разгружается в приемный бункер, который выполняет роль аккумулятора полезного ископаемого и обеспечивает непрерывную подачу груза на последующие транспортные устройства. Число и емкость приемных бункеров зависят от схемы технологического комплекса и выдаваемых сортов полезного ископаемого. Подъем груза в обыкновенных клетях на главных стволах применяется в настоящее время только на старых шахтах. На новых шахтах такой подъем используется только как вспомогательный для выдачи породы, спуска в шахту материалов и оборудования, а также для подъема и спуска людей.
В зависимости от характера движения вагонеток на приемной площадке различают кольцевую самокатную и тупиковую схемы. Кольцевая самокатная схема, при которой вагонетки с грузом, выданные на поверхность, выталкиваются из клети, следуют по откаточным путям к опрокидывателю, разгружаются и по кольцу возвращаются с обратной стороны клети к стволу. По пути движения в течение одного цикла обмена вагонетка обрабатывается 10 – 15 механизмами. На рис. 2 показана схема автоматизированной круговой откатки вагонеток в надшахтном здании шахты. Основными достоинствами кольцевой откатки являются большая пропускная способность и наличие резервных путей для накапливания вагонеток. Тупиковые схемы откатки отличаются от кольцевой тем, что изменение направления движения порожних вагонеток для их возврата в клеть происходит не по закруглениям, а с помощью тупиковых стрелочных переводов, размещенных в конце надшахтного здания. Тупиковая откатка (рис. 3) по сравнению с кольцевой является более компактной, и при ее применении требуются меньшие размеры надшахтных зданий. Однако пропускная способность при такой схеме мала Комплексы для обмена вагонеток, применяемые на поверхности шахт, работают следующим образом. Поднятая из шахты вагонетка с породой (см. рис. 3) выталкивается из клети порожней вагонеткой с помощью цепного толкателя 1 нижнего действия. До прибытия клети порожняя вагонетка удерживается перед клетью стопорами 2. Груженая вагонетка по закруглению направляется к путевому тормозу 3, установленному перед круговым опрокидывателем 4. Расторможенная вагонетка по самокатному уклону закатывается в опрокидыватель, разгружается и направляется на задерживающие стопоры 6 цепного компенсатора высоты 7. Перед компенсатором установлен ловитель 5 грузового типа, который предотвращает откатывание вагонетки к опрокидывателю. С компенсатора высоты вагонетка по самокатному уклону скатывается до задерживающих стопоров 8. В зависимости от того, в какую клеть будет направлена вагонетка, устанавливаются в соответствующее положение стрелочные переводы 9 и 10, затем открываются задерживающие стопоры 8 и вагонетка движется к путевым тормозам 11. Здесь вагонетка останавливается и автоматически направляется до путевых задерживающих стопоров 2, установленных перед клетью. С приходом клети процесс обмена повторяется. Подача леса и других материалов к клети производится с помощью вертикальных лесоподъемников 13 и 14. Вагонетка с лесного склада шахты доставляется к лесоподъемнику, поднимается на верхнюю приемную площадку, а затем через стрелочные переводы направляется к стволу. Подача порожних вагонеток на лесной склад производится от задерживающего стопора 8 через стрелочный перевод 15 к путевому тормозу 12, установленному перед порожняковым лесоподъемником.
{/spoilers}