Разработка горных пород и углей Исполнитель
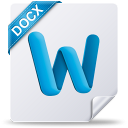
- Скачано: 24
- Размер: 2.25 Mb
- Разработка горных пород и углей начинается с их разрушения и может осуществляться следующими способами:
механическим, когда рабочие органы сосредоточенным силовым воздействием рабочего инструмента (как правило, клинообразной формы) непосредственно отделяют породу от массива. Энергоемкость способа (расход энергии на единицу объема разрушенной породы) в зависимости от крепости породы, типа, размеров и крупности рабочего органа составляет 0,72— 6,12МДж/м3;
{spoiler=Продолжать Читать}
гидравлическим, когда порода отделяется от массива напорной струей воды, подаваемой из гидромонитора, или когда порода со дна водоема вместе с водой всасывается земснарядом. Энергоемкость разрушения породы напорной струей составляет 1,44—14,4 МДж/м3, а при работе земснаряда она в 1,5—2 раза меньше (без учета транспортирования); взрывным, когда породы разрушаются под давлением газов, выделяемых при воспламенении взрывчатых веществ. Энергоемкость только бурения 1 м взрывной скважины составляет 14,4—36 МДж/м;
комбинированным способом разрушения, например, когда основное рыхление породы производится рыхлителем, а окончательное рыхление и захват разрушенной породы осуществляются механической лопатой, погрузчиком, скрепером, бульдозером или земснарядом.
Наибольшее распространение получил механический способ разрушения породы — до 85 % всего объема горных и земляных работ. Механический способ разрушения прочных пород при малой (до 5 м/с) скорости силового воздействия называется статическим, тогда как вибрационное, ударное, высокоскоростное и импульсное разрушения — динамическим.
- 3. Основными процессами открытых горных работ, на которых используются основные средства механизации, являются:
- подготовка пород к выемке;
- выемка и погрузка горной массы;
- транспортирование.
Основные машины обслуживающие эти процессы называются горными машинами. Теория горных машин и их конструкция являются предметом изучения в дисциплинах «Горные машины и комплексы» и «Горно-транспортные машины и комплексы». Бакалавр по направлению «Горная электромеханика» занимается эксплуатацией электромеханического оборудования горных машин. Знание основ взаимодействия машин объектами работы позволяет устранить не только возникшие неполадки, но и причины их вызывающие.
Основу горнодобывающей отрасли республики составляет разработка рудных месторождений, которые сложены скальными породами. Подготовка пород к выемке производится буровзрывным способом. Для бурения взрывных скважин диаметром 200 – 320мм используют в основном станки шарошечного бурения типа СБШ, и наиболее распространенной моделью является СБШ – 250МНА. Тенденция к увеличению диаметра скважин уменьшилась.
Буровзрывные работы (БВР) являются универсальным и практически единственным средством для подготовки пород к выемке. Этот способ останется доминирующим и в ближайшей перспективе.
Наиболее трудоемкая операция БВР – бурение. Применяются следующие виды бурения: шарошечное, вращательное, ударно-вращательное погружными пневмоударниками.
Перспективы развития буровой техники – в дальнейшем совершенствовании конструкций шарошечного бурового инструмента и во внедрении гидроударных бурильных машин.
В настоящее время на карьерах Узбекистана используется, и будет применяться цикличная технология (в сочетании с циклично-поточной). На выемочно-погрузочных работах используются главным образом экскаваторы – прямые мехлопаты типа ЭКГ с ковшом вместимостью 4,6 – 20м3 . На карьере Мурунтау применяются также гидравлические экскаваторы с большей вместимостью ковша.
Гидравлические экскаваторы имеют существенные преимущества по сравнению с карьерными. Они в 1,8 – 2,2 раза легче канатных машин и способны развивать усилия копания в 2,0 – 2,8 раза большие при меньших эксплуатационных затратах.
Особое место занимает класс так называемых выемочно-транспортирующих машин и в том числе одноковшовые фронтальные погрузчики. Современные пневмоколесные погрузчики – высокопроизводительная, маневренная, мобильная техника, которая способна обеспечить выемку, погрузку и транспортирование на уровне производительности экскаваторов при значительно меньшей стоимости и эксплуатационных затратах. Применение этой горной техники способствует также существенному повышению уровня полноты и качества выемки полезного ископаемого (в настоящее время потери составляют 4 -10 %, разубоживание – 6 – 20%, а в отдельных случаях и больше).
Для добычи угля на разрезе Ангренский в настоящее время применяется роторный экскаватор с малыми линейными размерами. Физико-механические свойства угля и вмещающих пород обуславливают применение для вскрытия пластов и на отвалах драглайнов с шагающим ходовым оборудованием и вместимостью ковша 10 – 14м3.
- 5. 6. Свойства пород изменяются в широких пределах, поэтому принято объединять породы в группы и категории с определенным диапазоном свойств и характеристик
Применительно к открытой разработке все горные породы подразделяют на группы: скальные и полускальные в естественном их состоянии; разрушенные (искусственно или естественно) скальные и полускальные; плотные, мягкие (связные) и сыпучие. Рассматривая горные породы как объект разработки, надо отметить следующие наиболее характерные их свойства.
Крепость — сопротивление горной породы общему разрушению. Предположив, что если одна горная порода крепче другой по буримости в f раз, то и по всем остальным механическим характеристикам (взрываемости, пределу прочности на сжатие и др.) она будет в f раз превосходить ее, проф. М. М. Протодьяконов составил шкалу крепости, разбив все горные породы на десять категорий с коэффициентами от f=20 и более для I категории до f = 0,3 для X категории.
Ориентировочно коэффициент крепости f равен 0,1 предела прочности горной породы при одноосном сжатии σсж (МПа)*.
Хотя шкала крепости проф. М. М. Протодьяконова получила широкое распространение в горном деле, она недостаточно полно отражает физико-механические свойства горных пород. Существуют также классификации горных пород, приспособленные для частных случаев ведения горных работ применительно к различным классам машин. Например, имеется классификация горных пород по буримости, определяющая скорость бурения в них скважины глубиной 1 м. Согласно этой классификации, породы делятся на одиннадцать категорий.
Твердость — способность породы оказывать сопротивление проникновению в нее другого, более твердого тела, не испытывающего при этом каких-либо остаточных деформаций. Твердость породы характеризуется сопротивлением ее поверхностного слоя воздействию внешней силы (например, бурового инструмента). Статическая твердость горных пород, получаемая в результате приложения статических сил, обычно на порядок выше, чем динамическая. Это учитывается при создании бурильных и других машин, использующих эффект ударного и вибрационного воздействий на породу.
Плотность γ (кг/м3 или т/м3) - отношение массы породы к ее объему при естественной влажности.
Связность определяется сцеплением отдельных частиц породы между собой и характеризует ее способность сопротивляться их разделению. От связности зависят прочность породы и ее сопротивление сдвигу, деформации и разрушению.
Гранулометрический состав — процентное содержание по массе частиц различной крупности (размера). В горной породе по крупности куска различают: валуны и камни (220 мм и более), гальку и щебень (20—200 мм), гравий (2— 20 мм) и песчаные фракции (до 2 мм).
Угол естественного откоса φ0 - угол у основания конуса, который образуется при отсыпке разрыхленной породы с некоторой высоты (табл. 1.1).
Величина угла φ0 зависит от категории, коэффициента внутреннего трения μ2, гранулометрического состава связности и влажности породы. Для несвязных пород угол естественного откоса равен углу внутреннего трения φ2.
- Разрушающий инструмент работает в тяжелых условиях, таких как:
- большие и переменные по характеру нагрузки;
- изменчивые свойства разрушаемых пород;
- повышенные температуры ( в крепких породах до 600°С).
При этом надзор за состоянием инструмента весьма затруднителен. Поэтому к буровому инструменту предъявляются следующие требования:
- эффективное разрушение горой породы с меньшими затратами и высокой производительностью;
- прочность и износостойкость, особенно армировки и рабочих кромок;
- соответствие формы, размеров и геометрических параметров свойствам разрушаемых пород, конструкции буровой машины и типу бурения;
- простое, надежное и жесткое крепление на штанге и в опорном узле машины;
- возможность быстрой замены при износе;
- удобство для ремонта, восстановления и заточки, а также невысокая стоимость изготовления и эксплуатации.
В связи с этим материалы, из которых изготовлены инструменты, должны отвечать требованиям: быть высокопрочными и достаточно вязкими, износостойкими, особенно в рабочей части; обладать высокой теплопроводностью и минимальным коэффициентом теплового линейного расширения; иметь широкий интервал ковки и хорошую закаливаемость, хорошую смачиваемость припоями.
Легированные стали придают инструментам более высокую прочность и износостойкость. В целях повышения износостойкости бурового инструмента его рабочую часть армируют твердыми сплавами или алмазами. Инструмент, армированный алмазами применяют в основном в геологоразведочном бурении. Из твердых сплавов применяют металлокерамические твердые сплавы в виде пластин, штырей, электродов, трубчатозерновые и зерновые сплавы.
9. 10. В переводе с латинского перфоратор означает пробивать, прокалывать, пробуривать. На сегодняшний день к перфораторам относят бурильные машины для бурения шпуров и скважин в породах выше средней крепости ƒ>8 ударным, ударно-вращательным и вращательно-ударным способами.
По способу применения перфораторы можно подразделить на переносные, телескопные и колонковые (бурильные головки). Переносные перфораторы (более раннее название - ручные) в свою очередь по массе можно разделить на легкие - до 18 кг, средние - 18... 25 кг и тяжелые - более 25 кг. В горной промышленности в основном нашли применение средние и тяжелые переносные перфораторы, которые работают с пневмоподдержек или других установочно-подающих устройств. Без вспомогательных устройств переносными перфораторами можно бурить шнуры сверху вниз (при проходке стволов шахт).
Телескопные перфораторы предназначены для бурения восстающих шпуров снизу вверх при проходке восстающих выработок или шпуров под анкерную крепь. Подача перфоратора на забой осуществляется специальным податчиком (телескопом).
Колонковые перфораторы в том конструктивном исполнении, в котором они применялись ранее, а настоящее время не используются. Их заменили бурильные головки.
По роду используемой энергии перфораторы подразделяются на пневматические, гидравлические и электрические. Электрические перфораторы в горной промышленности пока не нашли применения.
По способу распределения энергоносителя перфораторы можно разделить на три группы: клапанные, золотниковые и бесклапанные, когда распределение энергоносителя производит сам поршень-ударник.
По конструкции механизма поворота бура перфораторы можно разделить на две группы: с автоматическим зависимым и независимым вращением буровой штанги.
По способу очистки шпура от бурового шлама различают перфораторы: с осевой или боковой промывкой шпура водой; с отсосом пыли и с продувкой шпура сжатым воздухом. Последний способ очистки шпура от буровой мелочи санитарными нормами запрещен к использованию в подземных условиях. Однако может быть применен в тех условиях, где невозможно использовать воду (в зоне вечной мерзлоты) или в конце бурения для очистки шпура от бурового шлама и более полного использования глубины шпура.
Переносные перфораторы
Рис 11. Перфоратор ПП63В
Воздухораспределительный механизм служит для подачи сжатого воздуха в правую или левую часть цилиндра. Если сжатый воздух поступает в левую часть цилиндра, то поршень-ударник, двигаясь слева направо, совершает рабочий ход, в конце которого шток поршня-ударника наносит удар по хвостовику бура.
11. 12. Характерными особенностями развития рудной базы являются ввод в действие и реконструкция мощных месторождений руд, разрабатываемых открытым и подземным способами. Разработка угля и нерудных полезных ископаемых также имеет большое значение в горнодобывающей отрасли Республики Узбекистан.
Бурильные машины классифицируются:
- по способу разрушения;
- по способу приложения силовой нагрузки к буровому инструменту;
- по способу удаления буровой мелочи от забоя скважины или шпура;
- по роду потребляемой энергии;
- по способу расположения скважин;
- по назначению.
Способы разрушения различают механические и физические. К физическим относятся термическое, взрывное, гидравлическое, электрогидравлическое, ультразвуковое и плазменное разрушение. К механическому бурению относятся шарошечное, вращательное, вращательно-ударное, ударно-вращательное и ударное бурение.
Вращательно-подающий патронного типа (рис-1) состоит из вращателя 1, закрепленного на платформе станка, гидропатрона 2 и гидроцилиндров подачи 3.
Двигатель М1 постоянного тока через двухскоростной редуктор, переключаемый рычагом 4, вращает полый шестигранный шпиндель 5, проходящий через ведущую шестерню 6, редуктора. Через внутреннее отверстие шпинделя проходит буровой став 7, который получает вращение от шпинделя через кулаки 8 гидропатрона 2. Патрон с помощью траверсы 9 и гидроцилиндров 3 перемещается на длину хода цилиндров (1,0 м) со скоростью до 1,5 м/мин, сообщая буровому ставу усилие подачи до 0,3 МН. Далее следует разжатые кулаков и подъем патрона в исходное положение. Полное погружение, например 8-метровой штанги, может быть осуществлено за семь перехватов става. Маневровые подъем и опускание става осуществляются канатом 10 реверсивной тормозной лебедки, состоящей из асинхронного электродвигателя М2, трехступенчатого редуктора 11, барабана 12, блока 13 вертлюга и системы 14—16 блоков, установленных на верхнем конце мачты.
Вращательно-подающий механизм шпиндельного типа с цепной подачей станка пневмоударного бурения (рис. 2):,
Вращение буровому стану 1 с пневмоударником 2 передается от двухскоростного асинхронного электродвигателя М1 через двухступенчатый планетарный редуктор 3. Конструктивное устройство последнего аналогично применяемому на станке СБУ-160. Подающий механизм обслуживает рабочие и маневровые операции и имеет две тяговые втулочно-роликовые цепи 4, концы которых крепятся к коромыслу вращателя. Привод цепи осуществляется звездочкой 6 от пневмодвигателя 6 (4,4 кВт; 2000 мин) через двухступенчатый редуктор, содержащий зубчатую 7 и глобоидную 8 передачи. Направляющие звездочки 9 установлены в верхней части мачты.
- Применение механизированных комплексов позволяет совмещать во времени все основные операции в лаве: выемку угля, его доставку, крепление призабойного пространства и управление кровлей.
Для определения целесообразности применения механизированного комплекса, необходимо учитывать следующие основные факторы: мощность пласта, его строение, физико-механические свойства угля, угол падения пласта, устойчивость кровли и несущую способность почвы. На основании этих факторов принимается решение о комплектующем оборудовании очистных комплексов.
Существуют три типа механизированных очистных комплексов для работы в пологих, наклонных и крутых пластах.
Современный очистной комплекс для работы длинными лавами в пологопадающих пластах любой мощности включает в себя (рис. 23.1): очистной комбайн 1 (или струг), доставочную машину 2, механизированную крепь 3, кабелеукладчик 4, гидрооборудование 5, крепь сопряжения лавы со штреками 6, маслостанцию типа СНУ для питания гидросистемы механизированной крепи 3, типовую оросительную систему (ТОС) с оросительной установкой типа НУМС и энергопоезд 7, состоящий из фидерного автомата и пускателей для дистанционного включения машин комплекса.
В зависимости от схемы работы очистной машины, став доставочной машины комплекса, роль которой выполняет скребковый конвейер 2, может изгибаться в плане и в вертикальной плоскости — при челноковой схеме работы, или только в вертикальной плоскости — при односторонней схеме работы комбайна, а также при работе со струговой установкой типа СН75.
Механизированные комплексы для работы в наклонных пластах (25÷35°), как правило, комплектуются из оборудования комплексов для работы в пологих пластах. Поэтому помимо уже перечисленных машин механизированный комплекс для выемки наклонных пластов включает предохранительную лебедку типа 1ЛГКН или 1ЛП, которая устанавливается на верхнем штреке и работает синхронно с подающей частью комбайна. При разрыве тяговой цепи комбайн удерживается от сползания вниз по лаве предохранительным канатом лебедки. Кроме того, между секциями механизированной крепи и конвейером
вводятся дополнительные связи для обеспечения устойчивости, управляемости и предохранения от сползания.
Комплексы для выемки наклонных пластов отличаются высокой универсальностью и сравнительно простым исполнением в отличие от комплексов для выемки крутых пластов.
При выемке крутопадающих пластов по простиранию наибольшая сложность заключается в удержании оборудования от сползания. Это обстоятельство обусловило конструктивные особенности машин комплекса для
крутых пластов и поэтому его оборудование не универсально в отличие от машин комплекса для работы на пологонаклонных пластах.
14.15. 16. 18. 19. Общие сведение Проходческие комбайны предназначены для механизации проведения горизонтальных и наклонных подготовительных выработок различного назначения на угольных и рудных шахтах. Они находят применение и при строительстве различных подземных сооружений (перегонных тоннелей метрополитенов, гидротехнических и коллекторных туннелей и т. д.). Применение проходческих комбайнов дает возможность совместить во времени основные технологические операции проходческого цикла: отделение горной породы от массива, ее погрузку в транспортные средства, а иногда и крепление выработанного пространства.
Многолетняя практика эксплуатации проходческих комбайнов показывает, что с их применением существенно увеличивается скорость проходки выработок и производительность труда горнорабочих в сравнении с буровзрывной проходкой; упрощается организация труда; повышается безопасность труда; значительно облегчается труд проходчиков; улучшается устойчивость проведенных выработок, что снижает затраты на их поддержание; сокращает долю ручного труда по забутовке закрепленного пространства.
Все проходческие комбайны по общим признакам, определяющим область применения и технологическую схему работы, можно классифицировать:
-по области применения - для проведения вспомогательных и основных однопутевых и двухпутевых горных выработок по углю и смешанным забоям, для проведения основных и капитальных выработок по породе и нарезных выработок по углю (просеки, разрезные печи, ходки и т. п.);
Дополнительно проходческие комбайны можно классифицировать по конструкции его основных функциональных органов , габаритам, массе. Так, по массе стреловые комбайны в соответствии с ГОСТ 28599-90 делятся на четыре типоразмера:
I- до 13 т;
II- до 25 т;
III- до 48 т;
IV- до 75 т.
Независимо от области применения и конструктивного исполнения проходческие комбайны должны удовлетворять следующим техническим требованиям:
-устойчиво работать с заданной производительностью в требуемых горно-геологических условиях;
-в конструкции комбайна должна быть предусмотрена возможность установки дополнительного навесного оборудования для механизации трудоемких операций проходческого цикла (бурение шпуров и установка анкерной крепи, установка временной штучной крепи и пр.);
Рис . Проходческий комбайн 1ГПКС
Семейство унифицированных комбайнов 1 ГПКС состоит из базовой модели, которая предназначена для проведения горизонтальных и наклонных (±12°) выработок с погрузкой горной массы на конвейер. При погрузке горной массы в вагонетки базовая модель оснащается дополнительно ленточным перегружателем (модель 1ГПКС-01).
- В отличие от комбайновой выемки струги не режут, а строгают угольный пласт с открытой поверхности забоя. Для применения стругов необходимы благоприятные горно-геологические условия:
- сравнительно мягкий, трещиноватый уголь с сопротивляемостью резанию не более 180 кН/м;
- спокойное залегание пласта;
- устойчивые боковые породы;
- явно выраженная граница между угольным пластом и вмещающими породами с хорошим отделением верхней пачки пласта после подработки нижней пачки стругом;
- отсутствие твердых включений и др.
В таких условиях струговая выемка может оказаться более производительным способом добычи, чем комбайновая. Это подтверждается показателями работы струговых лав в ФРГ, Англии, Нидерландах, где струговая выемка получила широкое распространение благодаря хорошим горно-геологическим условиям. В СНГ пластов с вышеперечисленными свойствами сравнительно мало. Наибольшее распространение струговая выемка получила на шахтах производственного объединения «Ростовуголь».
Работы в области совершенствования струговых механизированных комплексов и агрегатов ведутся в направлении максимального увеличения их производительности за счет повышения энерговооруженности приводов (до 500 кВт и более), надежности и автоматизации всех производственных процессов в забое, расширения их области применения за счет работы в пластах с крепкими углями и возможности регулировки струга по высоте с целью одновременной обработки пласта на всю мощность.
Основные преимущества струговой выемки: возможность эффективной механизации выемки тонких пластов, простота конструкции, хорошее качество добываемого угля, малое пылеобразование, создание благоприятных условий для отработки пластов, опасных по газу, пыли и внезапным выбросам угля, отсутствие передачи электроэнергии по гибкому кабелю к движущейся машине, простая (рассредоточенная) схема организации работ в лаве.
К недостаткам струговой выемки относятся: ограниченная область применения по крепости угля и наличию в пластах крупных крепких включений колчедана, кварцита, породных прослойков; неудовлетворительная управляемость стругом по гипсометрии пласта, что в ряде случаев приводит к оставлению земника; большая ширина струговой дороги, что вызывает необходимость работы стругов в пластах с кровлями средней и выше средней устойчивости; низкий к.п.д. струговых установок из-за больших потерь на трение о почву и став забойного конвейера (η = 0,2÷0,3).
Струговой установкой принято называть комплект оборудования для узкозахватной выемки и доставки угля, состоящий из струга, верхнего и нижнего приводов с электродвигателями, скребкового передвижного забойного конвейера, системы гидравлических или пневматических цилиндров для передвижки конвейера.
Струг установки СН75
20.21. Крепление и управление кровлей — один из важных и трудоемких процессов угледобычи, составляющий 30 % от общих трудовых затрат в лаве. Для крепления и управления кровлей применяют крепь, которая разделяется по назначению на: призабойную и посадочную, основную и временную.
Призабойная крепь возводится в призабойном пространстве и предназначена для предотвращения обрушения в нем пород кровли. Крепление призабойного пространства осуществляется с помощью индивидуальной или механизированной крепи. Индивидуальная крепь включает стойку и верхняк. На первом этапе в качестве индивидуальной крепи использовалось дерево, которое применяется и до сих пор на некоторых шахтах при выемке крутых пластов. В дальнейшем деревянная крепь была заменена металлической индивидуальной крепью (рис. 17.1).
В середине 50-х годов прошлого века для крепления призабойного пространства начали применять гидрофицированные механизированные крепи, получившие на сегодняшний день широкое распространение при выемке пологих, наклонных и крутых пластов.
Посадочная крепь, как правило, применяется в лавах, в которых призабойное пространство крепится индивидуальной крепью, устанавливается на границе с погашаемым выработанным пространством и предназначается для управления обрушением (посадки) или плавным опусканием пород кровли.
Условно можно принять, что к основным крепям относятся индивидуальные и механизированные крепи, которые служат непосредственно для крепления призабойного пространства в лаве.
Рис. 17.1. Крепление лавы индивидуальной крепью при работе с широкозахватным (а) и узкозахватиым (б) комбайном:
1 — широкозахватный очистной комбайн; 2 — разборный конвейер; 3 — стойка деревянная; 4 — верхняк деревянный; 5 — комбайн узкозахватный; 6 — конвейер цельнопере-движной; 7 — верхняк шарнирный; 8 — стойка металлическая; 9 — посадочная крепь
Временная крепь, как правило, облегченного типа, применяется для временного и ускоренного закрепления обнаженного пространства пород кровли (например, при креплении ниш) с последующей заменой ее основной крепью.
Стойка является основным опорным элементом крепи и служит для поддержания рабочего пространства в лаве. Стойка работает в сочетании с деревянным или металлическим верхняком.
В основу классификации металлических стоек (рис. 17.2) положены принцип работы, рабочая характеристика и конструктивное исполнение их.
По принципу работы стойки разделяют на три группы: жесткие, стойки трения и гидравлические. Жесткие стойки в настоящее время не применяются.
Рабочая характеристика стойки является одним из важных факторов влияющих на состояние поддерживаемой кровли и показывает зависимость сопротивления от податливости. Рабочее сопротивление стойки может возрастать резко, плавно или оставаться постоянным.
22.23.24. Выемочно-транспортирующими машинами (ВТМ) называются такие машины, которые одновременно с отделением (или после отделения), горной породы от массива перемещают (транспортируют) ее, причем движение рабочего органа в этот период осуществляется перемещением всей машины, как правило, за счет развиваемого ею тягового усилия и реже — с помощью тягачей или толкателей.
Разработка пород выемочно-транспортирующими машинами осуществляется слоями толщиной от нескольких сантиметров (бульдозеры, скреперы, грейдеры, погрузчики и т. д.) до 2 м (рыхлители), что наилучшим образом отвечает условиям применения этих машин на карьерах со сложно структурными и многокомпонентными полезными ископаемыми.
ВТМ можно разделить на два основных типа: ножевые (бульдозеры, струги, грейдеры) и ковшовые (скреперы, погрузочные машины).
Бульдозерные отвалы, погрузочные оборудование и оборудование рыхлителей выполняются либо в виде навесного, либо полуприцепного оборудования к базовым гусеничным и колесным тягачам (тракторам).
Считается экономичным перемещать породу скреперами с гусеничными тягачами в пределах 300—900 м, а самоходными колесными скреперами — до 3—6 км. Бульдозерами же, при расположении отвала под углом 90° к оси движения, целесообразно перемещать породу на расстояние не более 150 м, так как при перемещении горной массы волоком часть ее теряется в результате высыпания по бокам отвала.
По сравнению с экскаваторами, используемыми в сочетании с соответствующим транспортом, ВТМ отличаются значительно меньшими металлоемкостью и энергоемкостью процесса. Так, на 1 т массы скрепера выработка в среднем составляет 2—5м3/ч (включая транспортирование и укладку породы); у бульдозеров этот показатель равен 4—6 м3/ч, у грейдеров и стругов — 10—12 м3/ч. Расход энергии на разработку 1 м3 породы у скреперов 2—2,5 кВт·ч при плече перевозки до 400 м. Удельная производительность на одного рабочего у мощных скреперов достигает 700 м3/ч. Себестоимость работ невысокая, иногда в 3-4 раза меньше стоимости работ, выполняемых экскаваторами в совокупности с автотранспортом.
Фронтальные погрузчики цикличного действия могут быть использованы на погрузке разрыхленных скальных пород в транспортные средства или для доставки пород самостоятельно. Благодаря высокой мобильности и маневренности погрузчики обеспечивают практически равную с экскаваторами производительность, приходящуюся на 1 м3 емкости ковша, при общей массе машины в 8—10 раз и стоимости в 3—4 раза меньших, чем у экскаваторов с такой же емкостью ковша.
Перспективы развития ВТМ заключаются в дальнейшем увеличении их производительности, прежде всего вследствие повышения мощности их двигателей, которая в ближайшие годы предположительно достигнет уровня 1100—2600 кВт (1500— 3000 л. с.), а также скоростей перемещения, которые в рабочих процессах уже сейчас у отдельных ВТМ достигают 10 км/ч, а при транспортировании — 90 км/ч.
При комплексном применении нескольких типов ВТМ могут быть выполнены почти все основные, а также многие вспомогательные работы на открытых горных разработках.
В качестве базовых тягачей для ВТМ используются гусеничные (табл. 13.1) и пневмоколесные (табл. 13.2) тягачи, которые в зависимости от мощности двигателя подразделяются на тягачи малой до 110 кВт (150 л. с.), средней 120-220 кВт (160-300 л. с.) и большой свыше 220 кВт (300 л. с.) мощности.
- Скрепер- представляет собой самоходную или буксируемую тележку с ковшом, имеющим нож по всей ширине передней кромки днища, с помощью которого отделяется слой породы. Ковш является рабочим органом скрепера.
Ковш врезается в массив под действием тягового и напорного усилий. Для лучшего наполнения он спереди снабжен заслонкой, которая может открываться на определенную величину, вследствие чего изменяется размер щели между режущей кромкой ковша и нижней кромкой заслонки. Величина щели в зависимости от толщины срезаемого слоя и физико-механических свойств породы регулируется системой управления. После заполнения ковша заслонка закрывается, а ковш переводится в транспортное положение.
По способу загрузки скреперы подразделяются на заполняемые за счет подбора грунта при реализации тягового усилия (загрузка тяговым усилием) и загружаемые с помощью шнекового или элеваторного устройства.
Для улучшения загрузки ковшей самоходных колесных скреперов используются бульдозеры-толкачи, помогающие осуществлять заполнение емкости на коротком пути, а также спаренные скреперы, работающие по методу «тяни-толкай». В последнем случае машины снабжаются дистанционно управляемым сцепным устройством. Скреперы стыкуются на ходу во время подхода к карьеру. Ведущая машина загружается первой, использую тяговую мощность своего двигателя и двигателя идущей машины, использующей роль толкача. Далее нагруженный передний скрепер выполняет роль тягача, помогая загрузиться идущему следом. Машины разъединяются на ходу и независимо друг от друга едут на разгрузку.
По способу разгрузки. Для скреперов применяются три основных способа разгрузки: свободный, полупринудительный и принудительный.
При свободном способе разгрузки порода может выгружаться вперед или назад. Для этого ковш с породой поворачивается вокруг точки, лежащей вблизи их центра тяжести. Этот способ наиболее прост и не требует применения дополнительных устройств, но пригоден только для работы в малосвязных нелипких породах, где не требуется достаточно точной регулировки толщины разгружаемого слоя (применяется для скреперов с ковшом малой емкости).
При полупринудительном способе порода выгружается поворотом днища или задней стенки вместе с днищем относительно боковых стенок и частично выталкивается. Недостатком способа является неполное опорожнение ковша, особенно при липких и увлажненных породах.
При принудительном способе заслонка ковша открывается, порода выталкивается вперед выдвижной задней стенкой, горизонтально перемещающейся на роликах в направляющих. Это самый надежный и один из наиболее распространенных способов обеспечивает полную разгрузку любых пород. Его недостатками являются большие усилия, необходимые для перемещения задней стенки с целью сдвига всей массы породы в ковше.
Нож ковша скрепера с элеваторной загрузкой при движении машины срезает стружку породы перемещаемую скребками элеватора, установленного на месте заслонки и заполняет ковш. Разгрузка ковша производится принудительно выдвигаемой задней стенкой через люк, открывающийся в днище одновременно с началом хода стенки вперед и обратным движением скребков. Скорость цепи элеватора - 0,3 – 0,5 м/с, а толщина стружки - до 150
. Схемы агрегатирования скреперов:
Наиболее тяжелыми условиями работы скреперов являются копание и движение на подъем. Для скреперов с ведомыми колесами на породах II—III категорий используются толкачи. Передача тягового усилия осуществляется более равномерно, если скрепер имеет ведущие колеса. Для передачи крутящего момента на колеса скрепера необходимо устанавливать дополнительный двигатель и самостоятельную трансмиссию. Управление двигателем осуществляется из кабины тягача.
- Ударные механизмы пневмоударников и перфораторов имеют одинаковый принцип действия и отличаются только размерами и конструкцией отдельных деталей.
Сущность работы пневмоударника и перфоратора заключается в том, что сжатый воздух с помощью воздухораспределительного устройства подается попеременно в правую или левую полость цилиндра ударного (или ударно-поворотного) механизма, обеспечивая для пневмоударника возвратно-поступательное, а для перфоратора и поворотное движение поршня-ударника.
Холостой ход поршня начинается под действием сжатого воздуха, поступающего через воздухораспределительное устройство по каналу в правую полость цилиндра. В крайней точке цилиндра поршень начнет открывать выхлопное отверстие передней правой полости цилиндра, соединяя ее с атмосферой. При этом давление в указанной полости резко падает, в то время как поршень продолжает перемещаться с нарастающей скоростью до максимальной величины. В конце холостого хода поршень перемещается по инерции с уменьшающейся скоростью движения, а давление снижается до близкого к атмосферному. В то же время левая полость цилиндра в начале холостого хода связана с атмосферой через выхлопное отверстие, и в ней давление первоначально удерживается на уровне атмосферного.
Когда выхлопное отверстие закрывается поршнем, воздух, находящийся в левой полости цилиндра, начинает сжиматься и происходит нарастание давления.
К концу холостого хода поршня на воздухораспределительное устройство с одной стороны действует повышенное давление, а с другой - полость цилиндра соединена с атмосферой. Клапан перемещается открывая путь сжатому воздуху в левую полость цилиндра. Однако поршень по инерции еще некоторое время продолжает холостой ход, сжимая воздух, а затем образовавшейся воздушной подушкой отбрасывается назад, начиная рабочий ход слева направо.
Во время рабочего хода поршень первоначально набирает скорость под действием сжатого воздуха. Перед окончанием рабочего хода поршень открывает выхлопное отверстие с одной стороны и закрывает отверстие с другой. При этом скорость движения поршня продолжает нарастать до максимальной величины, а давление в левой полости снижается, стремясь к атмосферному. В правой полости, которая была соединена с атмосферой, давление падает; к концу хода поршня воздух начинает снова сжиматься и давление возрастает. Под действием разности давлений в правой и левой полостях цилиндра клапан перебрасывается опять в крайнее левое положение, открывая для подачи сжатого воздуха канал. В то же время поршень наносит удар по хвостовику бурового инструмента, и начинается следующий холостой ход поршня.
Упрощенное описание в действительности более сложно протекающего процесса, хорошо объясняет физическую сущность работы перфоратора.
Воздухораспределительные устройства выполняются клапанными, золотниковыми и бесклапанными. В пневмоударниках и перфораторах наиболее распространено бесклапанное воздухораспределение, которое имеет малые движущиеся массы и поверхность трения и малую чувствительность к засорению. Золотниковое устройство более экономично по расходу сжатого воздуха, но более требовательно в эксплуатации. Бесклапанное воздухораспределение обеспечивается самим поршнем. Оно надежно в работе, но имеет меньшее наполнение полостей цилиндров сжатым воздухом, в связи с чем чаще применяется при малом ходе поршня и большой частоте ударов.
- Экскаватором называется машины для зачерпывания (экскавации) горной массы, перемещения ее на относительно небольшие расстояния и погрузки на транспортные средства или отвал . Рабочий цикл одноковшового экскаватора складывается из четырех последовательных операций: наполнения ковша (черпания), перемещения его к месту разгрузки (транспортирования), разгрузки и перемещения порожнего ковша к месту зачерпывания для нового цикла. Поэтому одноковшовые экскаваторы - машины циклического действия. Многоковшовые экскаваторы у которых все элементы рабочего цикла осуществляются одновременно (совмещенно), являются машинами непрерывного действия.
Существующие типы экскаваторов классифицируются на: одноковшовые и
многоковшовые.
Одноковшовые экскаваторы в свою очередь различают :
- по типу рабочего оборудования:
прямая мех.лопата,
обратная мех.лопата,
драглайн ,
грейфер,
кран,
копер,
специальные типы рабочего оборудования;
-по типу ходового оборудования
гусеничные ,
шагающие,
пневмоколесные,
плавучие;
-по типу силового оборудования
электрические
дизельэлектрические
дизельгидравлические
электрогидравлические.
По типу и назначению одноковшовые экскаваторы различают:
- ЭО - строительные гусеничные и пневмоколесные экскаваторы Е = 0,16 ÷ 2,5 м3 (6 базовых моделей)
- ЭКСГ - карьерно-строительные гусеничные Е = 2,5 ÷ 8м3
( 5 базовых моделей)
- ЭКГ - карьерные гусеничные Е = 2,0÷20 м3 ( 6 базовых моделей)
- ЭВГ - вскрышные гусеничные Е = 15÷100 м3(4 базовые модели)
- ЭШ - шагающие (драглайны) Е = 4÷125 м3 (6 базовых моделей)
- ЭКСГ - Д - драглайны гусеничные Е < 6м3.
Базовые модели и модификации всех типов одноковшовых экскаваторов имеют сменные ковши для работы в породах различных категорий (по крепости).
Экскаватор состоит из следующих основных частей: рабочего оборудования (у одноковшовых экскаваторов оно же и транспортирующее), транспортирующего, механического, ходового, силового оборудования, механизмов управления, платформы с рамой, надстройки и кузова.
Карьерные экскаваторы предназначаются для выемки и погрузки тяжелых пород или полезного ископаемого в транспортные средства, находящиеся на одном уровне с экскаватором, или в отвал. Вскрышные лопаты и шагающие драглайны не имеют сменного оборудования и предназначены для разработки высоких забоев с перемещением горной породы в отвал или с погрузкой ее в транспортные средства. Драглайны - для разработки забоев, расположенных как ниже, так и выше горизонта установки экскаватора и перемещения породы в отвал, а также для переэкскавации отвалов.
Многоковшовые экскаваторы различают роторные и цепные.
Роторные экскаваторы различают по теоретической производительности :
- ЭР - карьерные роторные (5 базовых моделей) для вскрышных работ (Qт=630; 1250; 2500; 5000; 10000 м3/ч);
- ЭРП - модификация ЭР с повышенным усилием копания КF = 1,4МН/м2 той же производительности.
Эти экскаваторы предназначены для ведения добычных работ. Цепные экскаваторы поставлемые из Германии различают:
- ЕRS - на гусеничном ходу (22 типоразмера) с ковшом емкостью
250÷3150 л и Qт до 7800 м3/ч по рыхлой массе;
- ЕS - на рельсовом ходу ( 9 типоразмеров) с ковшом емкостью
900-4500л и Qт до 14500 м3/ч по рыхлой массе.
Кроме того, существующие одноковшовые и многоковшовые экскаваторы имеют более узкие классификации, отвечающие конкретной специфике конструкции.
Один из главных признаков различия одноковшовых экскаваторов, определяющих их назначение и область применения, является их оборудование (исполнительный механизм). В зависимости от назначения рабочее оборудование одноковшовых экскаваторов имеет различную конструкцию и кинематику. На универсальных экскаваторах могут применяться до десяти видов сменного рабочего оборудования. Однако экскаваторы, применяемые на открытых разработках, имеют, как правило, один основной вид специализированного рабочего оборудования.
32.33.34.35.36. Изучение конструктивные схемы одноковшовых экскаваторов
Конструктивной схемой, в отличие от кинематической, называется схематическое изображение всей машины или ее основных узлов с указанием их действительного взаимного расположения и кинематической связи.
Одним из главных признаков различия одноковшовых экскаваторов, определяющих их назначение и область применения, является рабочее оборудование (исполнительный механизм). В зависимости от назначения рабочее оборудование одноковшовых экскаваторов имеет различную конструкцию и кинематику. На универсальных экскаваторах могут применяться до десяти видов сменного рабочего оборудования. Однако экскаваторы, применяемые на открытых горных разработках, имеют, как правило, один основной вид специализированного рабочего оборудования.
Основные виды рабочего оборудования одноковшовых экскаваторов, применяемого на открытых работах,— прямая напорная лопата и драглайн; более ограниченно используются гидравлические прямые и обратные лопаты, ковшовые погрузчики, грейфер, струг и кран.
Выпускаются три вида рабочего оборудования прямой лопаты: напорная прямая с выдвижной рукоятью, напорная колено-рычажная и безнапорная. Напорная лопата имеет систему принудительной подачи рукояти и ковша в забой, действующую от какого-либо привода. У безнапорной лопаты подача ковша в забой осуществляется под действием сил тяжести ковша и рукояти со стрелой (применяется только на экскаваторах с небольшой емкостью ковша — до 2 м3 и здесь не рассматривается).
Прямая напорная лопата
Прямая напорная лопата с выдвижной рукоятью (рис. 1) состоит из: ковша 1, рукояти 2, удерживаемой седловым подшипником 3 и деталями напорного механизма. Стрела опирается на поворотную платформу с помощью пятового шарнира 4 и поддерживается с помощью подвески 5. Подъемный канат, от лебедки 04 проходит через головной блок 6 стрелы и в точке В с подвеской 7 ковша, образует подвижное звено.
В зависимости от системы напорного механизма и конструкции стрелы различают четыре основных типа прямой лопаты:
с.зубчато-реечным механизмом напора (рис. 1, а), расположенным на стреле 8 и передающим усилие на зубчатую рейку 9 рукояти через кремальерную шестерню 10 с осью вращения 02 и точки контакта ползунов седлового подшипника с рукоятью (точка А); с канатным механизмом напора (рис. 1, б) и стрелой, которую шарнир 02 делит на две части — верхнюю 5 и нижнюю 9, поддерживаемую подкосом 10. Напорная лебедка и располагается на платформе. Выдвижение и возврат рукояти производятся канатами 12 и 13, которые огибают центральные блоки 14, закрепленные на оси О2 и полублоки 15 и 16, закрепленные на рукояти; с канатным механизмом напора (рис. 1, в) и неразрезной стрелой 8. Седловои подшипник 3 и центральные блоки 14 укрепляются на оси O1 в стреле. Выдвижение и возврат рукояти осуществляются лебедкой 11 так же, как и на схеме, показанной на рис. 1, б; с канатным механизмом напора (рис. 1, г) и неразрезной двухбалочной стрелой 8. Седловои подшипник 3 установлен в шарнире стойки 9, не связанной со стрелой. Стойка поддерживается подкосом 10. Напорная лебедка 11 расположена в передней части платформы. Выдвижение и возврат рукояти осуществляются так же, как на схеме, показанной на (рис. 1, б).
Положение рукояти в седловом подшипнике позволяет ей вращаться вокруг оси О2 крепления седлового подшипника под действием усилия в подъемном канате, а также поступательно перемещаться в седловом подшипнике в результате действия напорного механизма и проворачиваться вокруг продольной оси. Таким образом, рукоять имеет три степени подвижности. Рабочие движения ковша во времени определяются сложением векторов перемещений, обеспечиваемых подъемным и напорным механизмами при вращательном движении барабанов лебедок напора и подъема.
Напорные прямые лопаты предназначены для разработки массивов, расположенных, как правило, выше уровня стояния машины, и способны осуществлять черпание ниже уровня стояния на незначительную глубину, достаточную только для самозаглубления машины при проходке траншей.
Прямые коленно-рычажные напорные лопаты (рис. 2) имеют рукоять, кинематические не связанную со стрелой и перемещающуюся между стойками двухбалочной неразрезной стрелы. Такого рода лопаты наиболее распространены с двумя системами подачи: зубчато-реечной (рис. 2, а) и канатной (рис. 2, б).
Элементами рабочего оборудования лопаты являются ковш 1, рукоять 2, стрела 3 с головными блоками 4 и пятой 5, балансир 6, подвеска ковша 7, стреловой полиспаст 8, подъемный канат 9.
У коленно-рычажных лопат седловои подшипник а вынесен на двуногую стойку, а подача рукояти на забой осуществляется напорной балкой 10, перемещаемой посредством либо зубчато-реечной системы и (рис. 2, а), либо системы канатов 12 и 13 (рис. 2, б).
В кинематическом отношении неподвижным звеном исполнительного механизма экскаватора является поворотная платформа с двуногой стойкой и стрелой. Напорный механизм передает напорно-возвратное движение балке 10, шарнирно соединенной с балансиром 6. Рукоять и ковш образуют вращательные пары в шарнире D и в точке В. Ковш подвешивается к подъемному канату 9 через подвеску ковша 7. Колено-рычажный механизм воспроизводит движение прямой лопаты в результате вращательного движения кремальерной шестерни вокруг оси О2, а также барабанов лебедок относительно точек О4 и О3. Траектории копания определяются в результате сочетания поворотного относительно точки D и поступательного относительно седлового подшипника А движений напорной балки 10 рукояти. Прямая напорная лопата с рабочим оборудованием «Суперфронт» (рис. 3) имеет стрелу 22, на которой установлен нижний блок 2 канатного привода подъема рамы 6, образующий с верхним блоком 3 через уравнительный блок 5 полиспастную. систему. Два напорных гидравлических цилиндра 16 при выдвижении перемещают штангу 17 и мачту 20 относительно оси О4. Мачта напорным звеном 21 передает усилие на раму 6. Гидрофиксатор 9 через канат 11, профильный полу блок 13 и канат 12 удерживает ковш 8 от поворота по часовой стрелке
вокруг оси О2, укрепленной на рукояти 23 ковша. Возврат ковша в исходное положение осуществляется под действием сопротивления копанию или поворотом рамы 6 относительно оси О3 механизмом подъема или напора. Последние передают усилия через звено 7 и ковш поворачивается относительно оси О3 до полного выбирания слабины каната 14. Стрела 22 может подниматься и опускаться, поворачиваясь вокруг шарнира О4 за счет перемещения мачты 20. При разгрузке ковша его днище открывается с помощью пневмоцилиндров 24, установленных на задней стенке ковша. Таким образом, траектория рабочего движения образуется при сложном взаимодействии трех механизмов: подъема, напора и поворота ковша.
Гидравлическая прямая лопата с поворотным ковшом (рис. 4, а) имеет следующие элементы рабочего оборудования: стрелу 1, рукоять 2 и ковш 3, соответственно поворачивающиеся относительно шарниров О1, О2 и О3 с помощью гидравлических цилиндров подъема — опускания 4 стрелы, напора 5 рукояти и поворота 6 ковша. Гидроцилиндр 6 крепится к угловой тяге 7, соединенной шарниром с тягой 8 ковша. В кинематическом отношении неподвижным звеном исполнительного механизма экскаватора является поворотная платформа. Траектория копания образуется сочетанием перемещений основных элементов рабочего оборудования.
Гидравлическая прямая лопата может быть выполнена с ковшом, имеющим челюстной створ. В этом случае в задней стенке ковша устанавливаются дополнительные гидроцилиндры открывания ковша.
Гидравлическая обратная лопата (рис. 4, б) имеет стрелу 1 и рукоять 2, соединенные балкой 6, наклон которой по отношению к стреле фиксируется тягой 5. Поворот стрелы, рукояти и ковша в рабочем движении осуществляется соответственно вокруг осей O1, О2 и О3 гидроцилиндрами 4, 9 и 10. Тяги 7 и 8 служат для крепления ковша.
Обратная лопата может иметь неповоротный ковш. В этом случае отсутствует гидроцилиндр 10, а тяги 7 и 8 используются для крепления ковша к рукояти.
Гидравлический ковшовый погрузчик (рис. 4, в) имеет стрелу 1, рукоять 2 и ковш 3. Рабочие движения осуществляются их поворотом соответственно вокруг осей О,, О2 и О3 с помощью гидроцилиндров 4, 5 и 10. Тяги 6 и 9 образуют параллелограмную подвеску системы поворота ковша, что является характерной особенностью погрузчика. Тяги 7 и 8 используются для крепления ковша к рукояти.
Все перечисленные выше виды оборудования гидравлического экскаватора (прямая и обратная лопаты, погрузчик, а также грейфер, описываемый ниже) могут быть сменными и размещаться на одной базовой машине.
Экскаватор-драглайн
Драглайн (рис. 5, а) имеет: ковш 1 с упряжью, тяговый 2 и подъемный 3 канаты, стрелу 4 с направляющими 5, головными 6 блоками и пятой 7. Для перемещения ковша служат лебедки подъема и тяги. Угол наклона стрелы во время работы обычно не меняется и определяется длиной стрелового полиспаста 10.
Исполнительный механизм драглайна имеет два гибких звена-каната, связывающих ковш с ведущими звеньями механизма. Неподвижным звеном механизма драглайна является платформа экскаватора с двуногой стойкой и стрелой. Подъемный 8 и тяговый 9 барабаны лебедок образуют с неподвижными звеньями в точках О2, О3, O или О1 О3 и О4 вращательные пары. Механизм воспроизводит рабочие движения драглайна в результате перемещений подъемного и тягового канатов.
Рабочее оборудование приспособлено к разработке грунта преимущественно ниже уровня стояния, хотя вполне успешно может работать и выше этого уровня.
Грейфер
Исполнительный механизм грейфера (рис. 5, б) состоит из ковша 1, замыкающего 2 и поддерживающего 3 канатов, стрелы 4 с головными блоками 5 и 6. Стрела крепится в пяте 7 на платформе. Поддерживающий канат 3 прикрепляется к шарниру А, соединяющему тяги 8 ковша. Канат 2 служит для размыкания створок 9 ковша. Во время разгрузки под действием веса ковша и породы после ослабления замыкающего каната и передачи этих сил на поддерживающий канат средняя часть ковша опускается и створки расходятся. Неподвижным звеном исполнительного механизма является платформа экскаватора с двуногой стойкой. Механизм воспроизводит рабочее движение грейфера в результате действия поддерживающего 3 и замыкающего 2 канатов, сходящих соответственно с барабанов 10 и 11 лебедки. Рабочее оборудование грейфера предназначено для выемки породы со дна глубоких котлованов, водоемов, а также для погрузки сыпучих и мелкокусковых материалов.
Конструктивные схемы многоковшовых экскаваторов
Выемочно-погрузочные машины непрерывного действия — многоковшовые экскаваторы — различаются по типу рабочего органа и характеру перемещения его в пространстве.
По типу рабочего органа многоковшовые экскаваторы бывают: цепными; скребково-ковшовыми; роторными; фрезерно-ковшовыми; с безковшовым фрезерным рабочим органом.
По характеру движения рабочего органа:
экскаваторы продольного копания, у которых направление рабочего движения (ротора, цепи) совпадает с направлением их перемещения;
экскаваторы поперечного копания (обычно с неповоротной платформой), у которых направление рабочего движения (ротора, цепи, скребка) перпендикулярно направлению их перемещения;
экскаваторы радиального копания, у которых рабочий орган (ротор, ковшовая цепь) вместе с платформой поворачивается относительно базы машины. На открытых разработках применяются преимущественно роторные и цепные экскаваторы поперечного и радиального копания. Эти экскаваторы используются на однотипных работах большого объема, сосредоточенных в одном месте или на большом протяжении.
Экскаваторы продольного копания представлены группой траншейных, фрезерных и землеройных машин, предназначенных для строительства каналов. Эти машины относятся к строительным и в настоящем учебнике не рассматриваются.
Многоковшовый цепной экскаватор (рис. 1) зачерпывает горную массу ковшами 1, укрепленными на бесконечной цепи, двигающейся по ковшовой раме 2 и приводимой в движение приводной звездочкой 3. Двигаясь по забою снизу вверх, ковши заполняются горной породой и транспортируют ее по приемному желобу 4 к приводной звездочке, где они опрокидываются, и порода высыпается в бункер или на приемные промежуточные конвейеры, откуда она через погрузочные устройства поступает в вагоны или на конвейер.
Исполнительный орган при отделении стружки от массива движется в горизонтальной и вертикальной плоскостях (рис. 1, а). Основным рабочим движением является прямолинейное движение ковша в плоскости рисунка, определяемое скоростями резания vр и поперечной подачи ковшовой рамы vx (или транспортной скоростью экскаватора, если он работает поперечным черпанием).
Цепные экскаваторы поперечного черпания различают по следующим основным признакам: взаимному расположению экскаватора и забоя; конструкции рабочего оборудования; способу подачи рабочего оборудования в забой; конструкции разгрузочных устройств; способу связи рабочего оборудования с ходовой тележкой; по типу ходового оборудования.
Роторный экскаватор
Роторный экскаватор (рис. 4) представляет собой самоходную машину непрерывного действия, экскавирующую горную породу ковшами, укрепленными на роторном колесе, и предназначенную для одновременной разработки и транспортирования вскрышных пород или полезного ископаемого.
В отличие от цепного экскаватора транспортирование породы после разгрузки ее из ковшей ротора осуществляется ленточным конвейером, расположенным на стреле.
Исполнительный орган — роторное колесо (ротор) осуществляет движение в горизонтальной и вертикальной плоскостях. Основными рабочими движениями являются вращательное ротора в вертикальной плоскости и поворотное стрелы с ротором на платформе в горизонтальной плоскости. Траектория перемещения ковша определяется скоростями резания fp(wp) и подачи v3.
Роторные экскаваторы радиального и поперечного копания различают по технологическим и компоновочным признакам.
- Бульдозеры
Отечественные бульдозеры серийно выпускаются на базе гусеничных тракторов тяговых классов 30, 100, 150 и 250 кН и на базе колесных тягачей — классов 9, 14 и 50 кН. Ведется подготовка к производству бульдозеров на базе параметрического ряда перспективных гусеничных тракторов классов 40, 60, 100, 150, 250, 350 и 500 кН (ТП-4, Т-130, Т-220, Т-330 и T-500), (рис. 1), а также на базе перспективных колесных тракторов Т-80, Т-136 и колесных тягачей мощностью до 1200 л. с. (табл. 1 и 2).
Наиболее распространенными машинами являются бульдозеры с неповоротным отвалом на гусеничных тракторах класса 30 кН (Т-74 и ДТ-75) и 100 кН (Т-100 М), а также на колесном тракторе класса 14 кН (МТЗ-52). С поворотным отвалом наиболее распространены бульдозеры, агрегатируемые с тракторами класса 100 кН.
Бульдозер 41-В фирмы «Фиат-Эллис» с неповоротным отвалом и трехстоечным рыхлителем (рис. 1) на тракторе мощностью 524 л. с. класса 800 кН и массой 47 т эксплуатируется на ряде отечественных горных предприятий.
На базовом тракторе 1, снабженном гидросистемой, с помощью опорных шарниров установлен отвал 2 с козырьком 3, ножами 4 и толкающей рамой (брусьями) 5. Верхняя часть отвала соединена с толкающими брусьями упорами 6, обеспечивающими возможность поперечного перекоса отвала и изменения его угла резания в пределах ±5°. На задней части ходовой рамы устанавливается трехстоечный рыхлитель 7 на параллелограммной подвеске 8. Подъем и опускание отвала и рыхлителя осуществляются гидроцилиндрами 9.
У бульдозеров с поворотным отвалом последний крепится к универсальной раме, выполняющей функцию толкающих брусьев, в трех точках — в центре отвала через шаровое гнездо 8 (см. рис. 1) и с помощью двух пар соединительных тяг. Перестановкой положения точек крепления тяг на универсальной раме осуществляется поворот отвала.
Некоторое количество бульдозеров с канатным управлением еще эксплуатируется в условиях низких температур. Подъем отвала у таких бульдозеров осуществляется с помощью канатно-полиспастной системы, неподвижные блоки которой крепятся на раме передней части радиатора, а подвижные — на задней стенке отвала. Канат подъемной лебедки, расположенной сзади трактора и приводимой от вала отбора мощности подводится к полиспасту по защитной трубе и через систему блоков. Опускание и врезание отвала в породу происходят только под действием силы его тяжести, что является одним из существенных недостатков бульдозеров с канатным управлением. Перспективные бульдозеры будут выпускаться с гидравлическим управлением отвала.
Рыхлители
Рыхлитель представляет собой прицепное или навесное оборудование к трактору, которое может разрушать горную породу, отделяя ее от массива в виде крупных глыб или кусков. Рыхлители, как правило, применяются для рыхления пород, которые не могут быть эффективно и экономично разрушены экскаваторами, бульдозерами, скреперами. К таким породам относятся осадочные — песчаник, глинистый сланец, известняки, доломит, мергель, а также выветренные скальные вулканического происхождения. Стоимость разрушения известняков и песчаников рыхлителем зачастую в два-три раза ниже, чем при применении буровзрывного способа разрушения. Мрамор, гнейс, кварцит и другие породы метаморфического происхождения хорошо разрушаются рыхлителем при наличии трещин или слоистой структуры. Повышенная влажность горных пород также облегчает процесс разрушения. Применение рыхлителей для работы на скальных породах вулканического происхождения, таких как гранит и базальт, нецелесообразно.
Навесные рыхлители по сравнению с прицепными более распространены, так как обладают лучшими маневренностью, устойчивостью и, кроме того, позволяют использовать часть веса тягача для внедрения рабочего органа. Рыхлители должны устанавливаться на тракторах мощностью не менее 200 л. с, имеющих достаточно жесткую подвеску опорных роликов гусеничного хода.
Скреперы
По емкости ковша скреперы подразделяются на скреперы малой емкости —до 4 м3; средней —4—12 м3 и большой емкости — 12—45 м3 и более.
Прицепные скреперы, обычно двухосные, применяются чаще с гусеничными тягачами. Полуприцепные скреперы, как правило, используются с одноосными тягачами и редко с двухосными колесными или гусеничными тягачами.
Полуприцепные скреперы с одноосными тягачами являются в настоящее время наиболее маневренными и быстроходными землеройно-транспортными машинами. Однако основным их недостатком является то, что на ведущую ось тягача передается не более 52% силы тяжести груженой машины. Еще в меньшей степени используется тяговое усилие у двухосных колесных тягачей, у которых на ведущую ось передается только 37—38% силы тяжести груженой машины.
Самоходные скреперы в сравнении с прицепными и полуприцепными скреперами при одинаковой общей массе имеют большие сцепной вес, а также мощность, маневренность и быстроходность. Однако у скреперов с одноосными тягачами в отдельных случаях величина сцепного веса оказывается недостаточной для реализации тягового усилия двигателя, поэтому предпринимаются попытки создания самоходных скреперов по типу, показанному на рис. 4, е. Для увеличения тягового усилия и сцепного веса устанавливается либо второй двигатель на задней оси скрепера (одноосный тягач находится впереди), либо один двигатель с дизель-электрической передачей на обе оси скрепера. В этих случаях сцепной вес агрегата равен весу всей машины. Но даже при одной ведущей задней оси сцепной вес таких машин может быть доведен до 75% их веса. Наиболее совершенным конструктивным решением скрепера можно считать дизель-электрический скрепер с индивидуальным приводом на все колеса-(мотор-колеса, см. рис.2).
Самоходные скреперы. Самоходный скрепер Д-357М (рис. 4) агрегатирован с одноосным тягачом 1 с помощью
седельно-сцепного устройства 2, обеспечивающего свободу их поворота относительно друг друга в вертикальной плоскости при неровностях пути и в горизонтальной плоскости при повороте машины. Разворот тягача осуществляется с помощью двух горизонтальных гидроцилиндров 3. Подъем (опускание) ковша 4 осуществляется гидроцилиндрами 5 относительно рамы 6. Передняя заслонка 7 ковша перемещается гидроцилиндрами 8 относительно шарнира 9 рамы ковша. Последний имеет подвижную заднюю стенку 10.
Самоходный скрепер оборудован гидравлической системой Управления и снабжен пневматическими тормозами на всех четырех колесах.
Одноковшовые погрузчики
В последние годы одноковшовые фронтальные погрузчики благодаря своей универсальности находят все более широкое применение. Они используются для работ в породах I—III категорий для рытья траншей, планировочных и рыхлительных работ, погрузки в транспортные средства предварительно разрыхленных скальных пород, а также как самостоятельные транспортные средства для перемещения пород от забоя до погрузочного пункта.
Несмотря на большое разнообразие моделей погрузчиков, они сходны между собой по компоновке, конструкции, принципу действия. Выпускаются они с ковшами емкостью 0,5— 20 м3. Управление рабочим оборудованием — гидравлическое. Фронтальные погрузчики разгружают ковш вперед при его опрокидывании или опускании. Погрузчики с разгрузкой ковша через себя выполняются чаще всего на гусеничном ходу, с ковшом емкостью не более 4 м3, дизельным или дизель-гидравлическим приводом, гидравлическим или, реже, канатно-блочным управлением.
Погрузчики с боковой разгрузкой ковша по конструкции аналогичны фронтальным погрузчикам, однако шарнирное соединение ковша со стрелой у первых позволяет производить разгрузку как в левую, так и в правую стороны от погрузчика. Широкого распространения эти погрузчики ввиду сложности конструкции и низкой надежности не получили.
В СНГ пневмоколесные погрузчики создаются в основном на базе специальных гусеничных или колесных самоходных шасси или колесных тягачей с двумя ведущими мостами.
Колесный фронтальный погрузчик ТО-13 с основным ковшом емкостью 6 м3 (рис. 5) монтируется на пневмоколесном тягаче типа «Зауралец 2-400» с двумя жестко подвешенными ведущими мостами и шарнирно сочлененной рамой. Навесное оборудование погрузчика устанавливается на заднем мосту. На передней полураме расположен дизельный двигатель мощностью до 375 л. с. В сменное рабочее оборудование погрузчика входят ковши номинальной, увеличенной и уменьшенной емкости, челюстной захват, рыхлитель, крюковая подвеска и отвал планировщика. Погрузчик может быть переоборудован в бульдозер путем установки на специальную раму неповоротного отвала.
38. 39. Разрушение горной породы водой производится двумя способами: размывом напорной струей или размывом самотечным потоком, поступающим к всасывающей трубе землесоса.
При первом способе работ вода насосом по водоводу подается к гидромонитору, из насадки которого под давлением и со скоростью 30 - 50 м/с направляется на забой и разрушает его.
Размытая порода вместе с водой образует гидросмесь, которая называется пульпой. Она характеризуется консистенцией, под которой понимают соотношение твердой и жидкой фаз в пульпе (Т:Ж). Различают объемную консистенцию и массовую. Первая определяется отношением объема породы с естественной пористостью к объему воды, а вторая - соотношением масс породы и воды.
Образовавшаяся пульпа стекает по почве к зумпфу, откуда засасывается землесосом и по трубам перекачивается к месту укладки (гидроотвалу), где она отстаивается. При отстаивании порода отделяется от воды и остается в отвале, а осветленная вода через водосборный колодец по канаве попадает к насосной станции для повторного использования или сбрасывания в естественный водоисточник. Для самотечного движения пульпы от забоя до зумпфа подошве уступа придается уклон, вследствие чего часть породы остается неразмытой, образуя недомыв. Последний убирается бульдозерами или экскаваторами, укладывающими породу в отвал, смываемый струей гидромонитора в зумпф.
Интенсивность размыва характеризуется объемом горной породы, размываемой 1 м' воды. Увеличение высоты уступа до определенного предела увеличивает интенсивность размыва. Она также возрастает с увеличением расхода воды, уменьшением расстояния от гидромонитора до забоя и повышением компактности струи.. Повышение удельного давления струи гидромонитора целесообразно только до определенного оптимального предела.
Классификация гидромониторов. По своим конструктивным особенностям гидромониторы классифицируются по следующим признакам:
способу управления - с ручным и дистанционным управлением;
способу передвижки - несамоходные (передвигаемые вручную, тракторами, лебедками и другими способами) и самоходные;
рабочему расстоянию - дальнего и ближнего боя;
рабочему давлению - с низким (до 1,2 МПа) и с высоким (более 1,2 МПа).
Наиболее широкое распространение на карьерах имеют несамоходные гидромониторы дальнего боя с ручным управлением. Самоходные гидромониторы и гидромониторы с дистанционным управлением, очевидно, в будущем найдут повсеместное применение в гидромеханизации, однако в настоящее время они еще находятся в стадии освоения.
Гидромониторы с ручным управлением должны быть безопасными в эксплуатации, легко управляемыми усилием одного человека. Их конструкции должны обеспечивать минимальные потери давления воды, компактность вылетающей из гидромонитора струи и сохранение ее на пути до забоя, а также иметь небольшую массу, быть надежными и ремонтопригодными в эксплуатации.
Рис. 25.1 Гидромониторная установка ГУЦ -6 с дистанционным электрогидравлическим управлением.
Гидромонитор ГМЦ-250М имеет каретку с гидравлическими зажимами, конструкция которых обеспечивает поворот ствола в горизонтальной плоскости на любой угол. Управление поворотом ствола производится непосредственно с пульта, устанавливаемого на расстоянии до 30 м. Электропривод системы, насос и маслобак устанавливаются непосредственно у гидромонитора на специальном патрубке, соединенном с нижним коленом.
Исполнительные механизмы системы управления (гидроцилиндры) соединяются с насосом и маслобаком резиновыми маслостойкими рукавами и образуют замкнутую электрогидравлическую систему (рис. 25.2), изолированную от внешней среды.
Лебедка поворота служит также для поддержания непрерывного контакта всасывающего устройства с породным массивом и создания необходимого давления.
Рис. 25.3. Схема плавучего землесосного снаряда:
1—рыхлитель; 2—рама рыхлителя; 3 —полиспаст подвески раиы рыхлителя; 4 — укосина; 5 — подвеска укосины; 6 — двигатель рыхлителя; 7 — всасывающий патрубок; 8 — грунтовый насос; 9 — двигатель грунтового насоса; 10 — напорный пульпопровод; 11— свайный аппарат; 12 — сваеподъемная лебедка; 13 —лебедка поворота; 14 — лебедка подъема рамы рыхлителя; 15 —якорный канат
Грунтозаборные устройства обеспечивают рыхление пород, смешивают их с водой и передают для гидротранспортирования. Классификация грунтозаборных устройств земснарядов приведена на рис.25.4.
Для механического разрушения породы служит рыхлитель. Рыхлители на земснарядах применяются гидравлические и механические. Гидравлический рыхлитель состоит из нескольких небольших насадок, расположенных около всаса. Вода, выходящая под давлением из насадки, разрушает породу, которая затем засасывается землесосом. Давление воды у насадок при подводной разработке должно быть на 0,1 -0,15 МПа выше, чем при надводной разработке.
- Специальные насосы. К специальным насосам относятся насосы для транспортирования смеси твердого материала и воды — углесосы и шламовые насосы, предназначенные для гидроподъема угля из шахт при гидравлическом способе его добычи, транспортирования гидравлической закладки выработанного пространства, откачки неосветленных шахтных вод» очистки зумпфов и водосборников от шлама, транспортирования гидросмесей на обогатительных фабриках т. п.
- Углесосы позволяют транспортировать угольную гидросмесь при отношении твердых материалов крупностью до 100 мм к жидкому по массе не более 1 : 5.
Основные типы углесосов 10У4, 12У10, 14У7 и 12УВ6 (первая цифра — диаметр всасывающего патрубка, мм, уменьшенный в 25 раз; буква У — углесос; буква В — высоконапорный; последняя цифра — коэффициент удельной быстроходности, уменьшенный в 10 раз и округленный). Углесос 12УВ6 представляет собой двухступенчатый спиральный насос с горизонтальным разъёмом: остальные типы углесосов — одноступенчатые насосы, характеризующиеся рядом конструктивных особенностей, связанных с транспортированием частиц и кусков угля. В частности, их рабочие колеса выполнены с широкими проходными каналами и минимальным числом рабочих лопаток.
Центробежные шламовые насосы представляют собой одноступенчатые насосы консольного типа с закрытыми (6Ш8 и 8Ш8) и открытыми рабочими колесами (ВШН-150, ШН-200-1, ШН-150-1).
Насосы типа ШН перекачивают шламовые воды с содержанием твердых частиц до 50% при максимальном диаметре этих частиц до 20 мм.
Углесосы и шламовые насосы имеют проточную часть, элементы которой изготовляются из материалов, особо устойчивых к гидроабразивному износу; в их конструкциях предусматриваются сменные детали; частота вращения рабочего колеса обычно принимается ниже, чем у насосов для воды, и т. п. К. п. д. специальных насосов ниже и составляет для углесосов 0,53—0,68.
{/spoilers}