Особенности добычи строительных горных пород Исполнитель
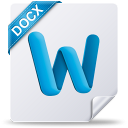
- Скачано: 33
- Размер: 495.1 Kb
Тема: Особенности добычи строительных горных пород
План:
- Технологические комплексы добычи и переработки песчано-гравийных пород.
- Технологические комплексы производства щебня.
- Технологические комплексы добычи природного камня.
Цель занятия – формировании в сознании студентов общих понятий о добыче строительных материалах, особенностях технологических комплексов песчанно-гравийных пород, щебня и природного камня.
{spoiler=Продолжать Читать}
Технологические комплексы добычи и переработки песчано-гравийных пород
Добыча песчано-гравийных пород и их переработка для получения гравия, щебня и песка, как правило, совмещены на одном предприятии — так же как добыча и переработка (обработка) большинства других строительных горных пород.
В общем случае производство продукции из строительных горных пород включает процессы: добывание этих пород, перемещение их в цеха переработки, переработка, складирование и последующая отгрузка готовой продукции потребителям.
При разработке песчано-гравийных пород возможные степень совмещения указанных процессов, место переработки породи состав комплексов оборудования зависят в основном от содержания и условий залегания в полезной толще крупнообломочного материала (валунов и др.) и глинистых пород, степени обводненности месторождения, видов готовой продукции и требований к ней, мощности и срока службы карьера, а также числа близрас-положенных карьеров.
Наиболее полное совмещение процессов добычи и переработки достигается при разработке сухих и частично обводненных месторождений добычными экскаваторами в комплексе с передвижными забойными перерабатывающими установками (агрегатами) (рис. 17.1,а) и при разработке полностью обводненных и подводных месторождений плавучими снарядами с добычным и перерабатывающим оборудованием (рис. 1.7.1, б). При отсутствии крупнообломочного материала (фракции +70 мм) для отделения песка и получения чистого гравия забойные агрегаты должны осуществлять грохочение с промывкой, а при наличии валунов — их дробление на щебень. Готовая продукция обычно отгружается в транспортные средства потребителей непосредственно или с промежуточным складированием на рабочей площадке, а отходы переработки (и песок при отсутствии потребителей) складируются в выработанном пространстве карьера.
Рис. 17.1. Основные технологические комплексы песчано-гравийных карьеров:
Э — экскаватор; П— погрузчик; А — автотранспорт; КЛ — конвейеры ленточные; ■ Б — баржа; ПС — плавучий снаряд; ПДСУ — передвижная или полустационарная дробильно-сортировочная установка; ДСЦ — дробильно-сортировочный цех; Ят — потребитель
При использовании полустационарных дробильно-сортиро-вочных установок для выпуска готовой продукции перемещение к ним горной массы из забоев осуществляется автотранспортом или непосредственно одноковшовыми погрузчиками (рис. 17.1, в).
Результатом переработки песчано-гравийных пород на передвижных и полустационарных дробильно-сортировочных установках (крупное дробление и отдельные стадии сортировки) чаще является промежуточный продукт. Дальнейшее перемещение его к основному дробильно-сортировочному цеху целесообразно осуществлять конвейерным транспортом (рис. 17.1,г, д).
В настоящее время комплексы с передвижными дробильно-сортировочными установками (ПДСУ) для выпуска готовой продукции применяются на карьерах малой мощности (100— 150 тыс. м3/год), в основном притрассовых. Недостаточно пока и применение передвижных и полустационарных дробильно-сортировочных установок для получения промпродукта. Вместе с тем перспективы применения таких установок, в первую очередь для получения промпродукта, связанные с внедрением передвижных дробильных агрегатов (с дробилками щековыми, молотковыми, вибрационного действия), велики и основаны на целесообразности расширения области применения конвейерного транспорта при разработке песчано-гравийных месторождений и уменьшения объемов перевозимых пород при складировании отходов в карьере.
Наиболее распространена в настоящее время при разработке сухих и частично обводненных песчано-гравийных месторождений технология с переработкой полезного ископаемого в стационарных дробильно-сортировочных цехах (ДСЦ). Расстояние транспортирования песчано-гравийной массы обычно не превышает 2,5 км, но может возрастать при обслуживании одним ДСЦ нескольких карьеров (участков). При большом содержании в песчано-гравийной массе валунных фракций обычно применяется автомобильный транспорт (иногда железнодорожный), а при отсутствии или небольшом содержании валунов на ряде карьеров используется конвейерный транспорт (рис. 17.1, е, ж).
Выемка и погрузка необводненных пород осуществляется в основном прямыми мехлопатами с ковшами вместимостью 1,25 м3 и более. На забойный конвейер порода поступает через бункер-питатель. При залегании отдельными прослоями крупнообломочного материала, глинистых пород или загрязненной илистыми и глинистыми частицами песчано-гравийной смеси производится их раздельная выемка, как и части песчаных пород при отсутствии потребителя; в последнем случае целесообразно применение также специального самоходного агрегата для отсева песка *. Экскаватором также выполняется сортировка негабаритных валунных фракций: при автотранспорте — по ширине приемного отверстия дробилки, при конвейерном транспорте — по ширине конвейерной ленты; в последнем случае для увеличения производительности экскаватора выделение негабаритных валунов возможно на грохоте бункера-питателя с последующей укладкой валунов в штабель и отгрузкой в средства автотранспорта.
Частично обводненные песчано-гравийные породы при отсутствии водопонижения разрабатываются в основном драглайнами с укладкой в штабели для обезвоживания (до естественной влажности) и последующей погрузкой в средства автотранспорта (рис. 17.1, з) или на конвейер.
Возможно также применение приконвейерном транспорте обезвоживающих бункеров-питателей, а также обезвоживающее -транспортирующих конвейеров, имеющих выпуклую форму в поперечном сечении. Для увеличения коэффициента наполнения используются перфорированные.драглайновые ковши (пятистенные для увеличения высоты забоя).
Для разработки сухих и обводненных песчано-гравийных пород могут применяться также канатные скреперы и башенные экскаваторы.
Комплексы оборудования дробильно-сортировочных цехов включают щеко-вую (ЩКД) и конусные (КСД и КМД) дробилки, вибрационные и инерционные наклонные грохоты для предварительного и промежуточного разделения фракций, оборудование для промывки фракций перед и после грохочения, обезвоживания гравийных и песчаных фракций, классификации песков. Схемадробления при раздельном выпуске щебня и гравия трехста-дийная, а при совместном выпуске щебня и гравия — двустадийная.
Система разработки песчано-гравийных месторождений чаще продольная или поперечная однобортовая, иногда веерная.
Необводненная часть толщи песчано-гравийных пород часто разрабатывается одним уступом. При мощной толще сухих пород и применении конвейерного транспорта для обеспечения безопасности горных работ верхнюю часть высокого уступа (20 м и более) выполаживают до 35—40° с помощью вспомогательного драглайна со специальным рабочим органом, устанавливаемого на верхней площадке уступа (рис. 17.2).
При разработке частично обводненных песчано-гравийных пород добычной уступ обычно разделяется на два подуступа (сухой и частично обводненный), отрабатываемые различными выемочными машинами (см. рис. 17.1, з).Высота нижнего подуступа при выемке драглайном нижним черпанием полезного ископаемого из-под воды значительно меньше глубины черпания экскаватора вследствие обрушения подводной и надводной частей забоя и необходимости передвижки драглайна. Потери полезного ископаемого увеличиваются с уменьшением в нем содержания гравийных фракций.
Обводненные пойменные пёсчано-гравийные месторождений могут разрабатываться драглайнами после предварительного водопонижения с помощью дренажных траншей, что позволяет существенно увеличить высоту уступа (на величину понижения уровня грунтовых вод). Система разработки при этом обычно поперечная, а дренажные траншеи проводятся перпендикулярно разрезной траншее с попутной добычей полезного ископаемого. Разработка пойменных месторождений осуществляется в межпаводковый период года (8—10 месяцев). В паводковый период (с апреля по июль) обеспечение сырьем ДСЦ осуществляется из паводковых складов штабельного типа, сооружаемых на незатапливаемых участках поймы; вместимость складов принимается равной четырехмесячной производительности ДСЦ. Повышению эффективности разработки пойменных месторождений способствует улавливание (аккумуляция) наносов паводкового стока карьерными выработками с последующим использованием аккумулированных наносов в качестве сырья для ДСЦ. Эффективность наносоулавливания характеризуется коэффициентом аккумуляции, равному отношению аккумулированных наносов к первоначальному объему выработки; коэффициент аккумуляции возрастает с увеличением высоты и длины добычного уступа, а также при сглаживании русла реки перед и позади карьера и достигает 0,90—0,94.
Для экскаваторно-автомобильных добычных комплексов характерна отработка уступов сквозными продольными заходками — панелями или блоками неправильной формы: для усреднения качества песчано-гравийной смеси, при разработке отдельных островов поймы между водными протоками и т. д. При экскаваторно-конвейерных добычных комплексах уступ отрабатывается сквозными продольными, поперечными или тупиковыми продольными заходками. Тип применяемых заходок, а также их ширина и число заходок в панели при работе мехлопат и драглайнов зависит от наличия перегружателя, его длины, длины разгрузочного конвейера бункера-питателя и линейных параметров экскаваторов *. Ширина добычных панелей существенно увеличивается при использовании в качестве выемочно-погрузочного оборудования одноковшовых погрузчиков.
Ширина рабочих площадок добычных уступов определяется шириной панели и транспортной полосы, а также числом и размерами штабелей: для обезвоживания, готовой продукции, пром-продукта (с зазорами между штабелями).
Производительность комплексов добычного оборудования зависит во многом от содержания и размеров крупнообломочного материала, степени селекции и межзабойного усреднения песчано-гравийной смеси, степени обводненности месторождения. В благоприятных условиях производительность комплексов достигает 300— 400 тыс м3 на 1 м3 вместимости ковша экскаватора.
Комплексы с плавучими снарядами широко применяются для подводной добычи песчано-гравийных пород, чаще в руслах рек. Используются плавучие снаряды с ковшовой цепью, грейферным ковшом и земснаряды.
|
В ряде случаев на плавучих снарядах устанавливается перерабатывающее оборудование: виброгрохоты, корытные мойки, классификаторы, дробилки; отходы промывки складируются в выработанном пространстве акватории. Такие дражные комплексы с получением готовой продукции могут применяться при большой производительности предприятия. Чаще на плавучих снарядах устанавливают только грохоты (для отделения валунов, песка и валунов) или перерабатывающее оборудование отсутствует.
Плавучие снаряды с ковшовой цепью (часто это серийно изготавливаемые землечерпалки) имеют ковши вместимостью до 280 л, глубину разработки ниже уровня воды до 15 м, производительность до 300 м3/ч; папильонирование обычно канатное. Такие снаряды могут применяться для разработки валунистых песчано-гравийных пород.
Грейферные плавучие снаряды со стрелой (поворотной или подъемной) или передвижной тележкой (рис. 11.3) имеют ковш вместимостью 1—5 м3 и глубину черпания 30—40 м, определяемую канатоемкостью барабана. С увеличением глубины черпания от 10 до 20 и 30 м производительность грейферного снаряда уменьшается на 25 и 45%. Такие снаряды могут иметь два грейферных ковша для одновременного производства вскрышных и добычных работ. Целесообразны грейферные снаряды при разработке песчано-гравийных пород с высоким (30—70%) содержанием гравия.
Транспортирование песчано-гравийной массы или готовой продукции от плавучих снарядов осуществляется баржами, ленточными конвейерами или по пульповоду; последние монтируются на понтонах.
К параметрам разработок плавучими снарядами относятся мощность отрабатываемой подводной толщи (высота забоя), ширина забоев и заходок, длина фронта работ. Высота забоя определяется в основном глубиной черпания снаряда. Ширина забоя и возможное направление его подвигания зависят от вида транспорта, типа плавучего снаряда и глубины разработки. При землечерпалках и земснарядах ширина забоя (заходки) определяется так же, как для драг. Для грейферных снарядов при транспортировании горной массы на берег плавучим конвейером максимальная ширина заходки определяется суммированием длины плавучей бухты и расстояния между концами разгрузочного конвейера снаряда и грейферной стрелы; при переработке добытой массы на снаряде ширина заходки может быть в два раза больше. Размеры отрабатываемой площади зависят как от размеров залежи, так и от условий судоходства.
Сезонная производительность комплексов с плавучими снарядами достигает 500 тыс. м3 и более при коэффициенте использования во времени около 0,5. Лимитирующим в большинстве случаев является транспортное звено, особенно при использовании барж.
Технологические комплексы производства щебня
Процессы производства щебня составляют общий технологический процесс добычи полезного ископаемого в забоях, дробления, сортировки, обогащения, складирования и отгрузки готовой продукции потребителям. Комплексы включают оборудование всего технологического потока от забоев до складов готовой продукции. На формирование комплексов оборудования предприятий по производству щебня существенно влияют величина запасов месторождения, рельеф поверхности, трудность разработки пород и структура залежи, годовая производственная мощность карьера и требования к качеству продукции.
При небольших запасах, отрабатываемых карьерами малой мощности (до 200—400 тыс. м3/год) или временными карьерами (например, притрассовьши при производстве дорожно-строитель-ных материалов), комплексы могут включать передвижные дро-бильно-сортировочные установки (ПДСУ) и легкое маневренное малогабаритное добычное оборудование: легкие пневмоударные буровые станки, одноковшовые погрузчики, бульдозеры, экскаваторы с вместимостью ковша до 2—3 м3 и автосамосвалы грузоподъемностью 7, 12 и 27 т (рис. 11.4, а).
При запасах 10—25 млн. м3 и более 25 млн. м3 обычно строят карьеры соответственно средней (400—1000 тыс. м3/год) и большой (более 1 млн. м3/год) мощности с переработкой добываемого в карьере полезного ископаемого в стационарных дробильно-сортировочных цехах (ДСЦ) и на крупных дробильно-обогати-тельных фабриках (ДОФ). Выбор рационального добычного оборудования этих карьеров зависит в основном от их мощности, качества полезного ископаемого и расстояния его транспортирования к ДСЦ или ДОФ.
Наиболее качественный щебень получается из прочных изверженных пород (гранит, базальт и др.). Однако большая потребность в щебне для строительных и дорожных работ часто обусловливает необходимость использования для его производства различных осадочных пород (песчаников и карбонатных типа известняков и доломитов) месторождений, расположенных вблизи потребителей щебня.
Наиболее распространены в настоящее время на щебеночных карьерах (независимо от прочности и структуры разрабатываемых
Рис. 17.4. Основные технологические комплексы щебеночных карьеров:
СБУ, СВЯ/ — станки пневмоударного и шарошечного бурения; Р — рыхлитель; В — бульдозер; Я — погрузчик; Э — экскаватор; ЯД — передвижная дробилка; А — автомобильный транспорт; Ж.-Д. — железнодорожный транспорт; КЛ — конвейерный транспорт; ПДСУ — передвижная дробильно-сортировочная установка; ДСЦ — дробильно-сортировочный цех; ДОФ — дробильно-сортировочная фабрика
пород) комплексы оборудования ЭАР с использованием станков пневмоударного бурения, карьерно-строительных экскаваторов (Е 5s1,25 м3) и автосамосвалов грузоподъемностью 10—27 т (рис. 17.4, б). Такие комплексы в основном рациональны на карьерах средней мощности при разработке однородных пород, а также пород с горизонтальной слоистостью при мощности слоев не менее 4—5 м и расстоянии транспортирования к ДСЦ до 2,5— 3 км. При легковзрываемых породах в качестве выемочно-погру-зочных средств могут использоваться одноковшовые погрузчики, которые при расстоянии перемещения к ДСЦ или перегрузочному пункту не более 0,5—0,7 км могут работать и как выемочно-транспортирующие машины (рис. 11.4, б).
На мощных карьерах при валовой разработке пород рациональны комплексы ЭАР с шарошечными буровыми станками, мехлопатами карьерного типа (Е = 3,2ч-8 м3) и автосамосвалами грузоподъемностью от 27 до 75 т, а при больших расстояниях перемещения до ДОФ — комплексы с железнодорожным транспортом (рис. 17.4, г).
Комплексы с конвейерным или автомобильно-конвейерным транспортом целесообразны при валовой разработке неабразивных карбонатных пород, если позволяют существенно сократить расстояние перемещения полезного ископаемого до ДОФ (в основном на нагорных карьерах), увеличить производительность экскаваторов, сократить объем перемещаемой на ДОФ горной массы (до 20—30%) за счет оставления отходов (мелочи) в карьере и обеспечить непрерывность технологического процесса переработки (рис. 11.4, д, е).
Большинство месторождений карбонатных пород — сложно-структурные, представленные маломощными (0,5—1,5 м) горизонтальными и наклонными слоями пород различной прочности. При взрывании карбонатных пород на дробление происходит переизмельчение и перемешивание пород продуктивных слоев высокой прочности со слабыми и глинистыми прослоями, снижается также природная прочность карбонатных пород вследствие «пережога» их в зоне расположения заряда ВВ. В то же время технологические возможности механических методов переработки породы (дробления, сортировки) весьма ограничены. В результате при валовой подготовке тонкослоистых карбонатных пород взрыванием количество отходов на щебеночных карьерах достигает 40—50% и выпускается щебень преимущественно низкой прочности (марки 200, 300 иногда 400), несмотря на наличие в полезной толще до 25—30% пород, из которых может быть получен продукт более высоких марок. Раздельная выемка разнопрочных пород при валовой их подготовке, даже при взрывании в зажатой среде, обусловливает необходимость сложной экскаваторной сортировки, технически трудно достижима и практически возможна только при визуально различимых разнопрочных породах при мощности их слоев не менее 4—5 м.
Поэтому более рациональны безвзрывная раздельная подготовка карбонатных пород (Прдо 5—6) тонкими слоями выемки, а более прочных карбонатных пород (У7Р до 10) — комбинированным способом, при котором безвзрывному рыхлению предшествует предварительное ослабление массива взрывом на встряхивание (по расширенной сетке скважинных зарядов В В). Далее производится раздельная послойная выемка и отгрузка разрыхленных разнопрочных пород.
Комплексы добычного оборудования при раздельной разработке карбонатных пород включают: звено подготовки к выемке— навесные механические рыхлители (рис. 17.4, ж) или дополнительно буровые станки (рис. 11.4,з), звено выемки и погрузки —одноковшовые погрузчики (см. рис. 17.4, ж) или бульдозеры и экскаваторы (см. рис. 11.4, з), транспортное звено — чаще всего автосамосвалы.
В результате выделения прочных разностей пород непосредственно в забоях карьера при такой технологии повышается сортность щебня, увеличивается его выход, уменьшаются объемы транспортируемой для переработки горной массы и ее кусковатость, что позволяет в некоторых случаях отказаться от первичного (крупного) дробления в цехах переработки.
Комплексы оборудования переработки пород на щебень включают: щековые (реже конусные) дробилки (ЩКД и ККД), нор-мальноконусные (КОД) и короткоконусные (КМД) дробилки соответственно для крупного, среднего и мелкого трехстадийного дробления абразивных пород типа гранитов, базальтов и песчаников; такие же или дробилки ударного действия (молотковые и роторные) при неабразивных осадочных породах;
грохоты (инерционные и вибрационные) для предварительного грохочения перед отдельными стадиями дробления, отбора загрязняющей мелочи, сортировки рядового щебня (0—70 и 0— 40 мм) на товарные фракции с выделением фракции 0—5 мм, промывки и обезвоживания щебня;
спиральные или многокамерные гидравлические классификаторы при дешламации отходов дробления крупностью 0—5 мм с выделением и обезвоживанием песчаных фракций 0,15— 5 мм;
моечное оборудование (скрубберы, бичевые и корытные мойки) для промывки пород перед второй стадией дробления и перед сортировкой щебня на товарные фракции при наличии трудно-промывистой глины;
оборудование для обогащения методами отсадки или разделения в тяжелых суспензиях при переработке карбонатных пород с содержанием слабых разностей более 20%;
питатели (пластинчатые, вибрационные, качающиеся) для подачи горной массы в дробилки и равномерной загрузки остального оборудования.
Системы разработки при использовании комплексов с автотранспортом чаще всего продольные, поперечные или кольцевые. Выбор системы разработки зависит в основном от требуемой длины и возможной кривизны фронта работ, его положения относительно направления слоистости массива и потока подземных вод на обводненных месторождениях.
При валовой подготовке пород к выемке панели добычных уступов отрабатываются обычно продольными заходками по развалу взорванной породы-. Выемка производится торцовым илифронтальным забоем — по условиям усреднения или раздельной выемки.
При раздельной разработке карбонатных равнопрочных пород осуществляются раздельные подготовка и выемка тонких (0,3— 0,5 м и более) горизонтальных или наклонных (до 25°) слоев (рис. 11.5, 11.6) в зависимости от направления слоистости массива. Заходки обычно продольные и по длине разделяются на рабочиеблоки, в пределах каждого из которых поочередно производятся взрывание пород на сотрясение (при Пр>5—6), механическое рыхление, выемка, погрузка (рис. 17.5, 17.6). Выемка горизонтальных слоев производится забоем-площадкой (рис. 17.5, б), а наклонных слоев — фронтальным (рис. 17.5, а, 17.6, а) или торцовым забоем.
Рис. 17.5. Варианты бульдозерно-экскаваторно-автомобильного технологического комплекса:
а, б— с рыхлением и выемкой соответственно наклонных и горизонтальных слоев
При использовании в* качестве выемочного и погрузочного оборудования соответственно бульдозеров и мехлопат после гыемки порода перемещается бульдозером в штабель, расположенный обычно на нижней площадке уступа. Высота и ширина штабеля зависят как от ширины панели и мощности слоя отдельно складируемых пород, так и от высотного положения слоя выемки относительно подошвы уступа.
Из штабеля производится погрузка горной массы экскаватором в транспортные средства (см. рис. 17.5). Бульдозерное и рыхлительное оборудование навешивается на одном тракторном тягаче, что позволяет попеременно выполнять процессы подготовки и выемки одним агрегатом, а промежуточное штабелирование горной массы обеспечивает достижение высокой технической и эксплуатационной производительности погрузочного экскаватора и требуемого качества полезного ископаемого.
При бульдозерной выемке забоем-площадкой в продольной заходке угол фронтального откоса уступа принимается, как и обычно, по условиям его устойчивости (см. рис. 17.5, б).
Рис. 17.6. Раздельная разработка карбонатных пород наклонными (а) и горизонтальными (б) тонкими слоями с использованием погрузчиков.
При выемке забоем-площадкой породы с помощью погрузчика фронтальный или торцовый откос уступа выполаживается (рис. 17.6, б), что позволяет использовать погрузчик и в качестве погрузочной машины. Наиболее эффективна работа погрузчиков фронтальным забоем (см. рис. 17.6, а), с выемкой и перемещением породы под уклон. Выемка торцовым забоем в продольных заходках, а также забоем-площадкой и продольным забоем в поперечных заходках,обусловливающая жесткую взаимосвязь подготовки, выемки и погрузки пород, рациональна в немногих случаях: при ограниченной длине карьера, складировании части пород в выработанном пространстве, для уменьшения угла откоса рабочего борта карьера.
Рассмотренная технология раздельной разработки возможна и для ряда сложноструктурных угольных месторождений с маломощными горизонтальными или пологими пластами.
Высокая производительность экскаватора, отсутствие траншейного вскрытия уступов, уменьшение ширины рабочих площадок и расстояний транспортирования горной массы достигаются при бульдозерной перевалке пород на нижние уступы. Горная масса (обычно взорванные породы) может переваливаться с одного или нескольких уступов на транспортный горизонт нижнего уступа, где она экскаватором отгружается в транспортные средства.
Рис. 17.7. Бульдозерно-автомобильный технологический комплекс:
/ — бульдозер; 2 — бункерный перегружатель
Такая бульдозерная перевалка применяется иногда на маломощных нагорных карьерах. Возможна также безэкскаваторная погрузка горной массы бульдозерами в автосамосвалы через бункерные перегружатели (рис. 17.7).
Высота добычного уступа при валовой выемке определяется мощностью однородных слоев или параметрами экскаватора. При раздельной выемке забоем-площадкой возможная высота уступа с нормальным фронтальным откосом зависит от устойчивости его и в скальных карбонатных породах может достигать 15—20 м и более. При выемке породы погрузчиком фронтальным забоем (наклонными слоями) или забоем-площадкой при выположенном откосе уступа с дальнейшей погрузкой породы в автосамосвалы рациональная высота уступа зависит от его угла откоса, а также мощности слоев выемки и составляет 5—10 м. При бульдозерной выемке наклонными слоями со штабелированием породы рациональная высота уступа должна обеспечить высокую производительность не только рыхлителя-бульдозера, но и экскаватора, и составляет 6—15 м; при этом высота штабеля изменяется от 3,5 до 5,0 м, а его ширина — от 6 до 9 м.
Ширина панели уступа Шппри валовой разработке определяется числом рядов взрывных скважин np (np = l-f-5). При разработке уступа наклонными слоями Шп — tили Ши= 2 t (t_ мощность слоя выемки). При разработке горизонтальными тонкими слоями величинаШаопределяет ' производительность рыхлителей — бульдозеров и погрузчиков; рациональная величина Шправна 20—35 м и 30—60 м при погрузке породы соответственно на уровне подошвы и рыхлимого слоя уступа.
Минимальная длина блока панели (экскаваторного блока) при валовой разработке с использованием комплекса оборудования ЭАР равна 70—100 м (см. раздел 15). При раздельной разработке длина блока панели (на один комплекс добычного оборудования) зависит от числа и длины рабочих блоков. Длина рабочего блока составляет 75—150 м. При использовании одноковшовых погрузчиков совмещаются рабочие блоки выемки и погрузки.
Ширина рабочих площадок уступов определяется суммой размеров составляющих ее полос и существенно увеличивается при раздельной разработке из-за большой ширины панелей уступа, выполаживания его откоса, размещения штабеля.
Качественная комплектация добычного оборудования определяется соответствием его по параметрам и производительности. Рациональная грузоподъемность автосамосвалов при характерных для щебеночных и песчано-гравийных карьеров расстояниях транспортирования (1,5—2,5 км) составляет (по данным института ГипроНИИНеруд):
Вместимость ковша погрузочного оборудования, м3 |
1 |
1,25 |
2 |
3 |
Грузоподъемность автосамосвала, т |
5-7 |
7-11 |
11-17 |
17-27 |
Вместимость ковша погрузочного оборудования м3 |
4 |
5 |
6 |
8 |
Грузоподъемность автосамосвала, т |
27-30 |
27-40 |
27-50 |
40-50 |
Эксплуатационную производительность добычного комплекса оборудования могут лимитировать:
приемная способность разгрузочного пункта, т. е. производительность начального звена цеха переработки;
производительность транспортного звена (чаще при валовой разработке);
эффективная производительность экскаватора или его плановые простои — при раздельной выемке и усреднении полезного ископаемого;
эффективная производительность погрузчиков — при испол-зовании их в качестве выемочно-транспортирующих машин, а также при погрузке в автосамосвалы при большой ширине панели и высоте уступа;
эффективная производительность бульдозеров — при большой ширине панели и высоте уступа соответственно при выемке забоем-площадкой и фронтальным забоем.
Выбор типа комплекса добычного оборудования, его качественную и количественную комплектацию, как следует из предыдущего, целесообразно осуществлять с учетом не только выполнения требуемого объема добычи, но и качества породы.
Совершенствование технологических комплексов производства щебня осуществляется в направлениях расширения ассортимента и сортности выпускаемой продукции, увеличения выпуска щебня высших сортов, комплексного использования добываемого сырья и отсутствия отходов. В перспективе возможно получение качественно новой продукции из карбонатных пород в результате их первоначального измельчения и последующего создания строительных материалов с требуемыми физико-техническими и химическими свойствами.
Технологические комплексы добычи природного камня
Особенности разработки месторождений природного камня определяются необходимостью сохранения физико-технических характеристик, декоративных качеств, определенных размеров и формы камня (в том числе крупных блоков), учета закономерностей в изменении прочности и трещиноватости добываемого камня в разных направлениях, строгого соблюдения размеров и направления уступов, удаления и переработки значительных объемов попутной горной массы (бута, штыба, эрозированного камня) при относительно небольшой мощности карьеров по основной продукции. Коэффициент извлечения (выхода) готовой продукции (блоков или штучного камня) из добываемого полезного ископаемого равен 0,1—0,3 и 0,3—0,7 соответственно на карьерах облицовочного и стенового камня. Указанные положения определяют специфичность применяемх способов и средств подготовки, выемки и транспортирования полезного ископаемого *, а также особенности систем разработки и их параметров.
Вскрытие месторождений осуществляется чаще всего общими внешними траншеями; при использовании в качестве транспортных средств только деррик-кранов и кабельных кранов вскрытие месторождений облицовочного камня бестраншейное. Отвалы вскрышных пород, как правило, внешние. Выработанное пространство используется для складирования блоков или штучного камня, а также для размещения отходов, получаемых при выпиливании камня.
Для карьеров характерен большой объем горно-подготовительных работ, так как на каждом горизонте проводят основную и фланговую разрезные траншеи путем образования вертикальных продольных и поперечных пропилов камнерезными машинами и отбойки горной массы по горизонтальной плоскости буроклиновым способом. Минимальная ширина фланговых траншей в зависимости от типов машин составляет 3—5 м.
На месторождениях камня используют как сплошные, так и углубочные продольные и поперечные одно- и двухбортовые системы разработки с различным направлением выемки в профиле:
горизонтальнымислоями—на месторождениях значительных размеров в плане со спокойным равнинным рельефом поверхности и монолитным строением полезной толщи при использовании для подготовки пород к выемке канатных пил, дисковых, баровых, с алмазным кругом и кольцевой фрезой камнерезных машин;
наклоннымислоями— на месторождениях с преобладающим направлением трещиноватости или слоистости полезной толщи под углом до 25° при использовании буроклинового способа подготовки и специальных камнерезных машин;
крутымислоями— при направлении трещиноватости или слоистости полезной толщи под углом более 25° и использовании ченнелеров, буроклинового и термического способов подготовки;
комбинированные— при изменении характера и направления трещиноватости по глубине месторождения с использованием различных методов и средств проходки щели-вруба.
Двухбортовая система разработки крутыми слоями значительной мощности позволяет существенно уменьшить текущие объемы выемки скальных вскрышных пород, сопряженной с большими трудностями из-за нарушения сплошности полезной толщи при взрывании на дробление во вскрышной зоне. Под слоем понимается одновременно отрабатываемая часть месторождения между последовательными положениями контура карьера, которая включает вскрытые запасы камня, обеспечивающие производственную мощность карьера. Слой отрабатывается несколькими уступами (рис. 11.8). При разработке крутыми слоями сокращается также срок ввода карьера в эксплуатацию, увеличивается темп углубления горных работ, повышаются выход штучного камня (или блоков) и размеры блоков, упрощаются и удешевляются подъемно-транспортные операции при использовании кабельных кранов и дерриккранов
Рис. 17.8. Разработка месторождения природного камня крутыми слоями |
Добывание гранитных блоков обычно двухстадийное: от массива предварительно отделяются крупные блоки(монолиты), которые затем разделяются на товарные блоки. Ширина, высота и длина первоначального монолита определяются существующей системой трещин и направлениями облегченного раскола составляет 8—12 м, ширинакамня. Чаще всего длина монолита3—6 м, высота {2—5 м. Объем получаемых товарных блоков изменяется от 1 до 4 м3 и обычно зависит от мощности применяемых в карьере средств выемки, погрузки и транспортирования блоков.
Отделение монолитов от массива осуществляется буроклино-вым, буровзрывным, газоструйным или комбинированным (например, газоструйным и буровзрывным) способами. При буровзрывном способе монолит обуривают шпурами на глубину до горизонтальной трещины при расстоянии между шпурами 0,8— 1 м. В качестве ВВ используют черный (дымный) порох или (реже) относительно более безопасные порохолодобные аммиачно-сели-тренные ВВ. Разделка монолита на кондиционные блоки осуществляется буроклиновым способом.
Добывание мраморных блоков чаще одностадийное с отделением.непосредственно от массива кондиционных блоков при помощи* камнерезных машин (около 75% общего объема добычи). В основном применяется камнерезная машина CM-177A.
При разработке месторождений со сложным строением мраморной толщи (развитая трещиноватость, тонко- и грубосланцева-тая текстура, наличие породных прослоев и твердых включений и т. д.), а также при высокой прочности мрамора (асж> 13- 10 Па)
в основном применяется одно- или двухстадийная добыча с буроклиновым способом подготовки. Получают распространение закладные клинья с гидравлическим приводом, канатные пилы, ударно-врубовые машины (ченнелеры), камнерезные машины с алмазным инструментом и тонкими барами с твердосплавными резцами, электросверла и др.
Добывание стенового камня в основном одностадийное. Для подготовки камня к выемке применяются камнерезные машины
Рис. 17.9. Схемы вырезки стенового камня:
а_ низкоуступная захватная; б — высокоуступная столбовая; в — высокоуступная захватная вертикальными заходками; г — высокоуступная двухстадийная фронтальная; д — низкоуступная столбовая; е — высокоуступная захватная сплошная; ж — высокоуступная захватная; з — высокоуступная двухстадийная диагональная
с дисковыми пилами, цепными барами и кольцевыми фрезами.
Схемы вырезки стенового камня различаются (табл. 17.1, рис. 17.9) по числу одновременно разрабатываемых уступов (одно-уступные и многоуступные), их высоте (низкоуступные и высокоуступные), организации вырезки и последовательности получения готовой продукции. При низкоуступных схемах высота уступа составляет 0,41 м, что равно двойной высоте стандартных стеновых камней (с учетом толщины пропила).
Таблица 17.1
Класс схем |
Группа |
Схема |
Высота уступа, м |
Описание схемы |
Условия применения |
Многоус-тупная |
Низкоуступная |
Захватная (НЗ) |
0,41 |
Длина поперечных пропилов определяется габаритами машины; горизонтальные и затыловочные пропилы осуществляются параллельно фронту работ |
Небольшая мощность вскрышных пород; малая мощность полезного ископаемого (1—1,5 м); раздельная выемка по высоте; предел прочности камня на сжатие свыше 15-Ю6 Па |
Одноуступ-ная |
Низкоуступная |
Столбовая (нст) |
0,41 |
Поперечные пропилы производятся на любую заданную длину |
Весьма малая мощность вскрышных пород (до 1—1,5 м); горизонтальный или слабонаклонный пласт; форма карьерного поля приближается к квадрату; большой коэффициент выхода готовой продукции (0,6—0,75) |
Высокоуступная |
Столбовая (вст) |
До 1,2 |
То же, но при добыче крупных блоков |
|
|
Одноуступ-ная и многоуступная |
Высокоуступная |
Захватная сплошная (ВЗС) |
До 3 |
Горизонтальные и затыловочные пропилы производятся по всей высоте уступа |
Мощность полезного ископаемого более 2 м; предел прочности камня на сжатие до 15-10° Па; производственная мощность карьера не менее 80—100 тыс. М3/год; длина фронта работ 600—700 м; средняя трещи-новатость пласта |
То же |
0,86—2,0 |
То же, но при добыче крупных блоков |
Мощность полезного ископаемого более 2 м; предел прочности камня на сжатие 3,5 ■ 106—4 ■ 107 Па; производственная мощность карьера не менее 35—50 тыс. м3/год; длина фронта работ 200—600 м; малая трещино-ватость пласта |
Захватная горизонтальными заходками (ВЗГ) |
До 3 |
Горизонтальные и затыловочные пропилы производятся последовательными заходками по высоте уступа |
Карьеры малой и средней производственной мощности (10— 50 тыс. м3/год); предел прочности камня на сжатие до 3,5 • 106—5 ■ 106 Па; доработка уступов, разрабатывавшихся ранее другими машинами |
Захватная вертикальными заходками (ВЗВ) |
До 3 |
Продольные пропилы осуществляются последовательно по высоте, затыловочные пропилы производятся заходками по вертикали |
В основном при проведении фланговых разрезных траншей или.доработке уступов |
Двухстадийная фронтальная (ВДФ) |
До 3 |
То же, что для ВЗС, но добываются блоки-заготовки, подлежащие вторичной переработке |
Для получения продукции с минимальными допусками или архитектурно-строительных изделий, а также, при явно выраженной горизонтальной трещиноватости |
Двухстадийная диагональная (ВДД) |
До 3 |
То же, что для ВЗС, но режущий орган располагается под углом 45° к фронту; исключаются фланговые траншеи |
|
В зависимости от организации вырезки стандартных стеновых камней или блоков схемы могут быть захватные и столбовые. При захватных схемах длина поперечного пропила ограничивается конструктивными размерами камнерезной машины (машины СМ-89А и СМ-518). При столбовых схемах камнерезная машина нарезает поперечные пропилы большой длины, передвигаясь по кровле разрабатываемого слоя. При захватной сплошной схеме вырезки камня одна камнерезная машина или агрегат, состоящий из нескольких машин, за один проход вдоль подготовленногоуступа, когда нарезаны поперечные пропилы, подготавливает камень к выемке. Фронтальная и диагональная схемы аналогичны высокоуступной захватной сплошной схеме. По направлению движения рабочего органа машин в забое схемы подразделяются на два типа: горизонтальными заходками, вертикальными заходками. Выемке, погрузке и перемещению подлежат: товарные блоки или штучный камень — на перегрузочный пункт промплощадки карьера или в камнераспиловочный цех; некондиционные блоки, бутовый камень, щебень, штыб — на дробильно-сортировочную фабрику, потребителям или на склад. Стреловые самоходные краны (с вылетом стрелы до 30 м и грузоподъемной силой до 200 кН) в комплексе с автотранспортом целесообразно использовать на карьерах глубиной до 20—25 м. На более глубоких карьерах для механизации процессов выемки, погрузки и перемещения рациональны деррик-краны (мачтово-стреловые) со стрелой длиной до 40 м и грузоподъемной силой до 250 кН — при ширине рабочей зоны в пределах двух радиусов действия кранов, а также кабельные краны. Для перемещения некондиционных блоков, бута, щебня и штыба целесообразно использование одноковшовых погрузчиков.
Параметры систем разработки определяются в зависимости от горно-геологических условий, конструктивных параметров камнерезных машин и других факторов. Высота уступа на карьерах стенового камня составляет 0,41—3 м. На карьерах облицовочного мрамора при использовании камнерезных машин с кольцевой фрезой или с алмазными отрезными кругами высота уступа не превышает 1 м. При двухстадийной добыче блоков облицовочного камня (гранита, мрамора, известняка) высота уступа определяется в основном расположением горизонтальных трещин отдельности и может достигать 5 м и более.
Минимальная ширина рабочих площадок уступов для камнерезных машин КМ-ЗА, КМГ-2, КМАЗ-188 составляет 6 м, для СМ-89А, СМ-177А, СМ-580А — 9 м, для СМ-518 — 10 м, для СМ-824 — 12 м. Ширина рабочих и нерабочих площадок уступов и подуступов зависит как от типов применяемого горного и транспортного оборудования, так и от вида продукции. Добываемые на карьерах стеновые штучные камни и блоки должны быть выдержаны на площадках для удаления влаги. Продолжительность выдержки устанавливается по технологическим картам месторождений и практически составляет 5—20 дней. Высота штабеля для штучных стеновых камней составляет 1,8 м и для крупных стеновых блоков — 2,5 м, а ширина штабеля зависит от производственной мощности карьера.
Рациональная длина фронта работ определяется экономическими и технологическими факторами, а также физико-техническими свойствами камня. На практике длина фронта работ составляет: 150—300 м для машин СМ-89А, 700—800 м для СМ-824, 100—200 м для СМ-177А и 200—300 м для СМ-580А.
Структура комплексов оборудования чаще разветвленная или параллельная. Взаимодействие между звеньями подготовки и выемки осуществляется через склад, при двухстадийной подготовке — также через склад между стадиями. Лимитировать эксплуатационную производительность комплекса может эффективная производительность звеньев подготовки к выемке, погрузки или транспорта *.
В связи с взаимодействием через склад эксплуатационная производительность средств механизации подготовки камня к выемке может рассчитываться независимо от последующих процессов. Рабочее время камнерезных машин в течение смены достигает 80%, а число рабочих смен за год — 70% времени работы карьера.
Рекомендуемая литература по разделу:
- Анистратов Ю. И. Технология открытой добычи руд редких и радиоактивных металлов. – М., Недра, 1988.
- Горная энциклопедия в 5-ти томах. М., Советская энциклопедия, 1986.
- Мельников Н. В. Краткий справочник по открытым горным работам. М., «Недра», 1974. 424 с.
- Ржевский В. В. Открытые горные работы. Часть 1. – М., Недра, 1985.
- Ржевский В. В. Процессы открытых горных работ. М., «Недра», 1978. 542 с.
- Симкин Б. А. Технология и процессы открытых горных работ. М., «Недра», 1970. 215 с.
- Томаков П. И., Манкевич В. В. Открытая разработка угольных и рудных месторождений. М., Изд. МГГУ, 1995. 611 с.
- Технология открытой разработки месторождений полезных ископаемых, ч. I. Под общей ред. М. Г. Новожилова. М., «Недра», 1971. 635 с.
{/spoilers}